Numerical control lathe is a high-precision and high-efficiency machine automated tool. The use of numerical control lathe can improve processing efficiency and create more value. The emergence of numerical control lathe has enabled enterprises to rid of old processing technology. The processing technology of numerical control lathe is similar to that of ordinary lathe. However, since numerical control lathe is a one-time clamping and continuous automatic processing to complete all turning processes, the following aspects should be noted.
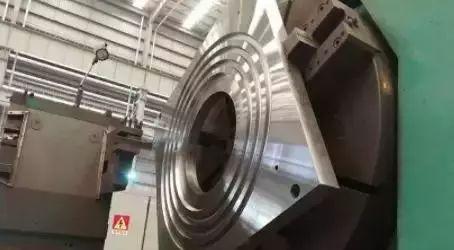
Reasonably choose cutting parameters
For efficient metal cutting, the material being machined, cutting tools, and cutting conditions are the three major elements. Haec tempus processionis, vita instrumentorum et qualitatem processionis determinant. Metodo processionis economically effectus rationale opus concidi conditionibus esse oportet.
Tres elementa conditionum secendi: velocitatem secendi, velocitatem pascuae, et profunditate profunditatem directo detrimentur instrumentum. Cum crescere velocitatis, temperatura extinguentis crescet, resultat in mechanica, chemical et thermal vestimenta. Increasing cutting speed by 20% reduces tool life by half.
Relatio inter conditiones pascuae et instrumentum germinatur in minimo intervalo. But with a large feed rate, the cutting temperature rises, and there is significant wear later on. Minus effectus est super instrumentum succidentium quam velocitatem succidentium. Quando effectus profunditates secendi in instrumentis secendi non est tam significatior quam velocitatem et fertilitatem, in micro profunditate secendi, materiae concidit difficile layer producit, quod etiam vitae instrumenti influent.
Users need to choose the cutting speed based on the material being processed, hardness, cutting state, material type, feed rate, cutting depth, etc.
Seleccio optimis conditionium processionis super haec factores est. Regular et stabile vestimenta et lacrima vitae perficiendi est condicio ideale.
However, in practical operations, the choice of tool life is related to tool wear, changes in machined dimensions, surface quality, cutting noise, machining heat, and other factors. When determining the processing conditions, it is necessary to conduct research based on the actual situation. Difficile machinae materiae, sicut stainless steel et calore resistentes alloys, coolantes aut blades cum bona rigiditate utilisar potest.
Quomodo tres elementos procedentis procedentis determinare
Quomodo haec tres elementos recte elegere constituit principibus metallicis, et principibus principibus principibus haec tres elementorum elegere sunt:
(1) Velocitate secendi (velocitas lineae, velocitas circumferentiae) V (m/min)
To select the spindle revolutions per minute, it is necessary to know how much cutting line speed V should be taken. The choice of V depends on the tool material, workpiece material, processing conditions, etc.
Materiale instrumenti:
Hard alloy, V can achieve a high value, generally above 100 meters per minute, and technical parameters are usually provided when purchasing blades:
Quot lineae velocitates elegere potest quando materiales processare. High speed steel: V can only be obtained at a relatively low level, generally not exceeding 70 meters per minute, and in most cases below 20-30 meters per minute.
Materium laborpiece:
Alta fortitudo minima V valor Ferrum mitte, cum minimo valore V, utilizatur ad succidendum vasa difficile in velocitate 70-80 metrorum per minutam; Low carbon steel can have a V value of over 100 meters per minute, while non-ferrous metals can have a higher V value (100-200 meters per minute). Stella et steel a incantata inferiora V valor habere debet.
Conditiones procedentes:
Difficile machina, inferior V valor accipite; Precision machining, with a higher V value. The rigidity system of machines tools, workpieces, and cutting tools is poor, and V is taken as low. If the CNC program uses S as the spindle speed per minute, then S (spindle speed per minute) should be calculated based on the workpiece diameter and cutting line speed V, where S=V (cutting line speed) * 1000/(3.1416 * workpiece diameter). If the CNC program uses a constant line speed, S can directly use the cutting line speed V (meters/minute)
(2) Feed rate (feed rate)
F prima depends on the surface roughness requirements of the workpiece processing. When precision machining, the surface requirements are high, and the cutting amount should be small: 0.06~0.12mm/spindle per revolution. Quando machina difficile, maior erit. It depends mainly on the strength of the tool, which can generally be above 0.3. When the main rake angle of the tool is large, the strength of the tool is poor, and the feed rate cannot be too large. In addition, the power of the machine tool and the rigidity of the workpiece and cutting tool should also be considered. Programma CNC duas unidades fertilis temporis utilizat: mm/min et mm/spindle per revolutionem. Unidades supra utilizatae sunt omnes mm/spindle per revolutionem. Si mm/min utilizatur, formula ad convertendum potest: fertilis per minutam=fertilis per revolutionem * revolutiones spindle per minutam
(3) Cutting depth (cutting depth)
When precision machining, it is generally advisable to take a radius value of 0.5 or less. During rough machining, it is determined based on the condition of the workpiece, tool, and machine tool. Generally, small lathes (with a maximum machining diameter of 400mm or less) are used to turn 45 # steel in a normalized state, and the depth of the radial cutting tool is generally not more than 5mm. In addition, it should be noted that if the spindle speed of the lathe adopts ordinary variable speed regulation, when the spindle speed is very low per minute (below 100-200 revolutions per minute), the motor output power will significantly decrease, and the cutting depth and feed rate can only be achieved very little in this time.
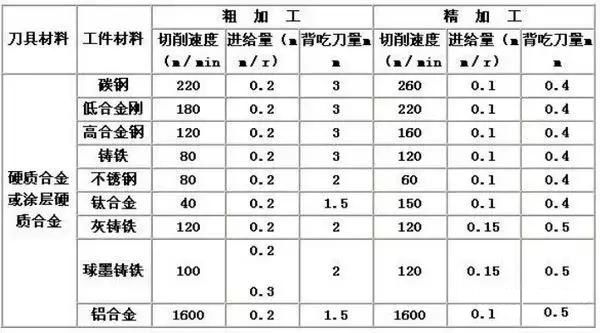
Selection Reasonable of cutting tools
When rough turning, it is necessary to choose cutting tools with high strength and good durability to meet the requirements of large back cutting and large feed rate during rough turning.
When precision machining, it is necessary to choose tools with high precision and good durability to ensure the required machining accuracy.
To reduce tool changing time and facilitate tool alignment, machines clamped knives and machines clamped blades should be used as much as possible.
Reasonabile elige fixturas
1. Proicite universas fixturas utilisere ad clampsimos opus et evadere specializatus fixturas;
2. Aligne optimis positionis parterum ut errores positionis reducant.
Determine route processionis
Lingua machinae referit ad trajectorium motionis et direction instrumenti relative to the part during the CNC Machining process.
1. It should be able to ensure the machining accuracy and surface roughness requirements;
2. Rutus processionis quam maxime possibile breviabitur ut instrumentum vacuum tempore redderet.
The relationship between processing route and machining allowance
Nunc, absente amplius utilizationem CNC lathi, excessive allowance in vacuum, sublime allowance continentem latus pellium fabricatum aut proiectum, generale ad processandum in latus ordinaris. Si opus est CNC lathe ad machinas utilizati, attention ad flexibiliam agentiam programmae considerare debet.
Puncti clavi instantiae fixturae
Currente, connexio inter hydraulicam et hydraulicam clampingom cylindrum accipit a virga pulla. Clave puncti hydraulicam clampingom sunt sicut sequentes: primum, utilis manum ut auferat nudum in cylindro hydraulicam, auferat tubam pullam, et extractat ab exterior finem spindle. Tad, utilis manum ut auferat pulchram fixing pulchram ut auferat pulchram pulchram.