The editor will organize many practical knowledge methods and hot news for everyone. Please pay more attention and there will be better content presented to you.
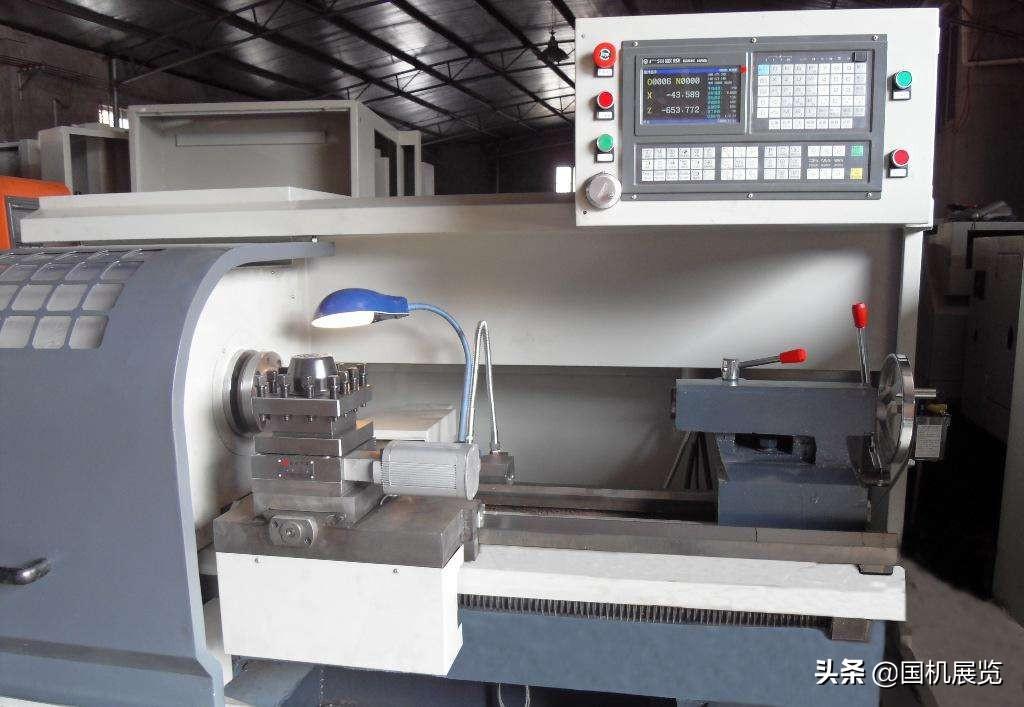
On a CNC lathe, four standard threads can be machined: metric, inch, modulus, and radial. Regardless of which type of thread is machined, a strict motion relationship must be maintained between the lathe spindle and the tool: that is, for every rotation of the spindle (i.e., one rotation of the workpiece), the tool should move uniformly by one lead distance (of the workpiece). Analizante virgas ordinaris, volumus intellegere nostrum eorum ut melius processamus illos.
1 , Dimensional analysis of ordinary threads
The machining of ordinary threads by CNC lathes requires a series of dimensions, and the size calculation and analysis required for ordinary thread machining mainly include the following two aspects:
1. Diameter of workpiece before threading processing
Considering the expansion of the thread profile during thread machining, the diameter of the workpiece before thread machining is d/d-0.1p, which is the reduction of the thread pitch by 0.1 from the larger diameter of the thread. Generally, based on the material's deformation ability, the smaller diameter is taken as 0.1 to 0.5 compared to the larger diameter of the thread.
2. Thread machining feed rate
Quantitate insertion is lignorum est diameter subter lignorum, quod est novissima positio cutoris lignorum.
Diametrus lignis est: magnus diameter -2 times altitudo dentis; Altitudo tres=0.54p (p est pitch)
The feed rate for thread machining should be continuously reduced, and the specific feed rate should be selected based on the tool and working material.
2,Assembly and alignment of ordinary thread cutting tools
Si instrumentum succidentis nimis altum aut nimis altum aut nimis altum est, quando succidentis attinget quaecum profundum, facie retrorsum instrumenti succidentis presset contra laborem, crescere frictionem et etiam crescere laborem, causa phenomenum morientium instrumenti; Si chip nimis humilis est, difficile est discargere chips. Directio radiolis instrumenti conversionis est in medio laboris. In addition, the clearance between the transverse screw and the nut is too large, causing the cutting depth to automatically increase, thereby lifting the workpiece and causing tool biting. At this point, the height of the turning tool should be adjusted in a timely manner to ensure that its tip is at the same height as the axis of the workpiece (the tool can be aligned with the tip of the tailstock). During rough and semi precision machining, the position of the tool tip is about 1% d higher than the center of the workpiece (d represents the diameter of the workpiece being machined).
Laborem firme clamabitur non potest, et rigiditate eius non potest resistere fortitudinem cutationis durante conversationis, resultat in excessive deflectione et mutare altitudinem centri inter instrumentum cutationis et opera (opera est elevata), causantem subito crescere in profunditate et interfectione instrumentorum. In hoc tempore, opus clamabitur firme, et lapides caulstockis potest ad crescere rigiditatem opus.
The methods for aligning ordinary threads include trial cutting and automatic alignment with a tool alignment device. The tool can be directly used for trial cutting alignment, or the workpiece zero point can be set with the G50 and the workpiece zero point can be set with the workpiece movement for alignment. Praecepta ad alignationem instrumentorum in machinationibus ligaminis non sunt altissima, sublime in z-direction ubi non sunt constraintiones strictae ad alignationem instrumentorum, quae iuxta praecepta programationis.
3,Programming and machining of ordinary threads
In current CNC lathes, there are generally three machining methods for thread cutting: g32 straight cutting method, g92 straight cutting method, and g76 oblique cutting method. Due to different cutting methods and programming methods, machining errors are also different. Operationes nostras diligenter analisare debemus et quaeremus ut partes altas precisiis producemus.
1. Metodo directo secendi G32 habet fortitudinem et difficultatem secendi a causa simultanee operatione utraque laterum secendi. Utraque latera secendi sunt in concidione. Cum sagittere tres in maximo hydria propter maximum profunditatem sagittationis caligine celerior est, resultit errores in diametro caligini ligni. However, its machining precision is relatively high, so it is generally used for small pitch thread machining. Due his tool movement and cutting being completed through programming, the machining program is relatively long; Pro facile folio folii, necesse est mensurare frequenter in processione.
2. The g92 direct cutting method simplifies programming and improves efficiency compared to the g32 instruction.
3. The G76 oblique cutting method, due to its single-sided edge machining, is prone to damage and wear of the machining blade, resulting in uneven threaded surfaces and changes in the tool tip angle, leading to poor tooth profile accuracy. However, due to its single side blade operation, the tool load is relatively small, the removal of chip is easy, and the cutting depth is decreasing. Therefore, this processing method is generally suitable for machining large pitch threads. Pro facile subtractione chipa et bona conditiones processionis bladiis, hoc methodo machinationis convenientior est in situationibus ubi alta precisa thread is non est requisita. Cum alta precision threads processerint, duas sectiones utilizatur ad consummationem machinarum, primum modo machinarum G76 ad conversionem durum, et tunc modo machinarum G32 ad finem conversionem utilizatur. Sed gravis est notare quod principium instrumenti sectionis accusatum esse, alioquin facile est errores facere et causare partes colligi.
4. After the completion of thread processing, the quality of the thread can be judged by observing the thread profile and taking timely measures. When the thread crest is not pointed, increasing the cutting amount of the knife will actually increase the diameter of the thread, which depends on the plasticity of the material. When the crest has been sharpened, increasing the cutting amount of the knife will proportionally reduce the diameter. Based on this characteristic, the cutting amount of the thread should be treated correctly to prevent scrap.
4,Inspection of ordinary threads
For general threads, thread ring gauges or plug gauges are used for measurement. quando mensus est ligna exteriora si ligna transiens per finem Gaudium anuli rotatur in pretio et Fine to End "; Si gaudium anuli introire non potest indicat quoniam lignum processum complicit necessitatibus, alioquin non est qualificatum. Metientibus ferris interioris, utilizat gaudium et mensuram per semel methodo. In addition to measuring with thread ring gauges or plug gauges, other measuring tools can also be used for measurement. Use a thread micrometer to measure the thread pitch diameter, use a tooth thickness vernier caliper to measure the trapezoidal thread pitch diameter, tooth thickness, and worm gear pitch diameter, and use a measuring needle to measure the thread pitch diameter according to the three needle measurement method.