Hodie cum vobis principes factores cogitare quando quinque axis machining center elegerit, ut industria industria leading Makino quinque axis machining center in exemplum. I will provide you with a detailed list of those who don't know
01
Struktura praesentiam instrumentorum determinat
There are various structures of five axis machining centers, and the structural design of the machine tool determines the performance of the equipment, including rigidity, machining accuracy, stability, operability, and so on.
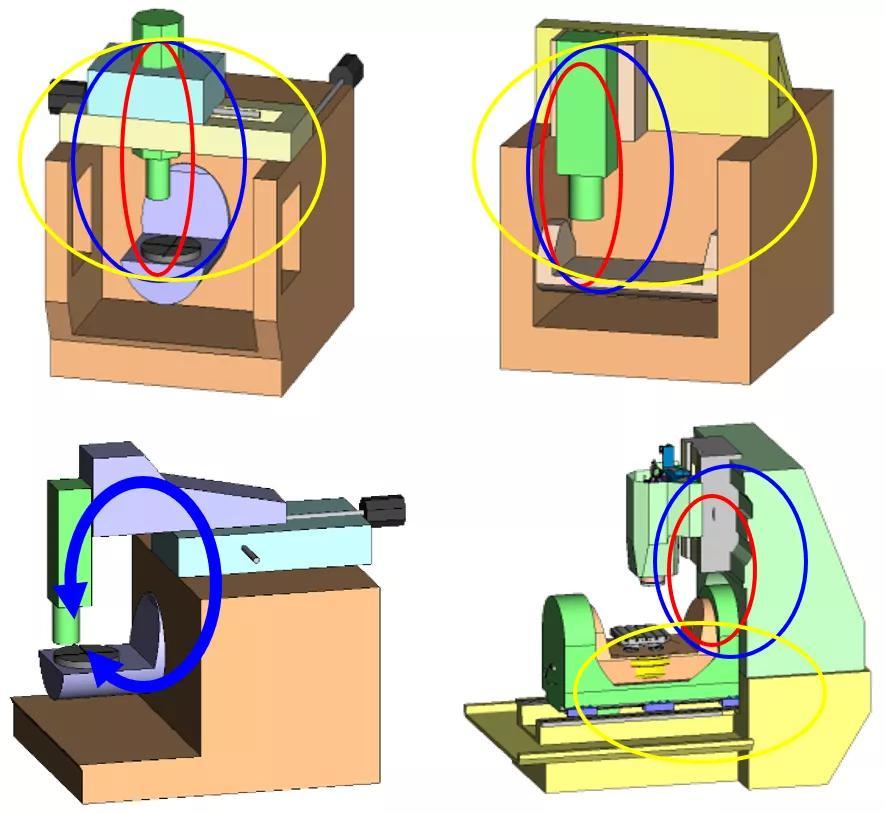
Sequentes aspecti prima considerentur:
1) Assis linearis non merget neque superimposit cum movetur
2) Equipment with short cutting circuits has good rigidity
3) Is the tilting rotation axis a DD motor
4) Is it 5-axis linkage
paper size
Makino's D200Z/D800Z/a500Z series five axis machining center adopts a "Z" - shaped high rigidity worktable structure, as shown in the figure below. The worktable does not require support at both ends, with large diameter inclined bearings and a workpiece center of gravity B within A. Comparatus cum universa structura universa suporta traditionis, quanta bending d valde parva est et brachium fortis L breviae est.
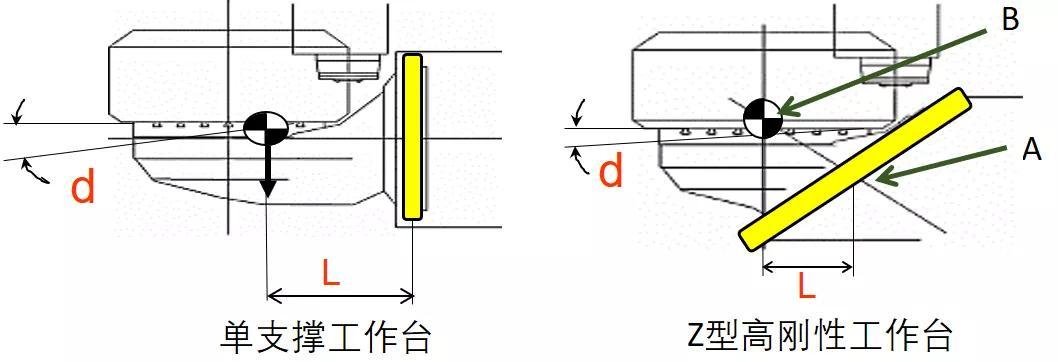
This inclined axis structure can achieve high-precision machining comparable to 3-axis machining centers. Etiam quando componentes gravissimas carganda et rotata sunt, deflectio arboris ad minimum potest controlli. In ipso tempore, portantes altas rigiditates et motores directos ferent alta precision et flata rotatione cum minima vibratione. In addition, it has excellent spatial proximity.
02
Assis rotationis precisa
The machining accuracy of machine tools is directly affected by the accuracy of the rotating axis. To understand the actual impact of tilted rotating axis accuracy on machining accuracy, use the Makino D800Z machine tool.
1= 60′
1′= 60″
1=3600″
Minima resolucio axis B/C instrumenti D800Z est 0,0001 gradus, quod est 0,36 inches, et precisa positionis 3 inches. Pro sequente diagramma calculi scire possumus errorem accuracionis resultentem.
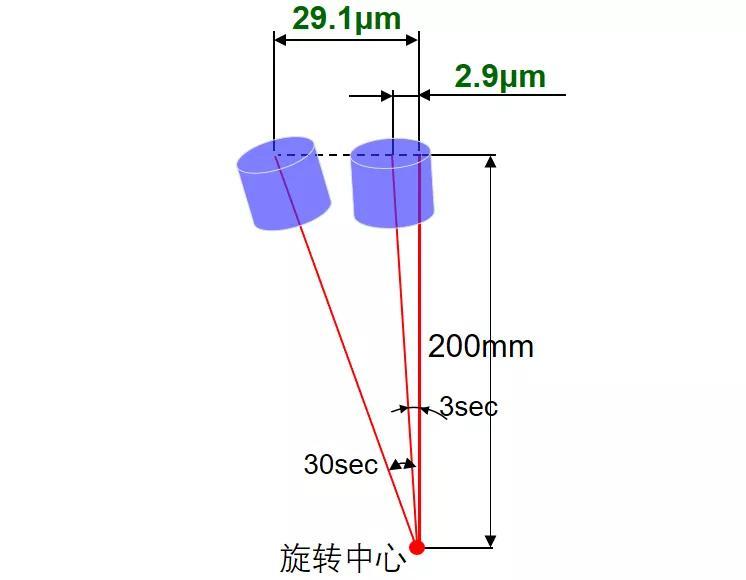
03
Interference collision avoidance
Interference et avoidance collision is problemas importantes sunt in machinationibus 5 axis. In addition to using computer-based software for interference inspection, Makino's 5-axis machining center is equipped with online real-time simulation CSG function, which can prevent interference even in manual mode.
The online real-time simulation CSG function can check for possible tooling errors or tool length setting errors before processing, in order to minimize emergency stops during operation. Inter operatio, basit super data pre calibratis et adjustatis, sed et coordinatis, valores offset et et alias informationes positivas legitas ex dispositivo controlli CNC, possibilia interferencee predicta est. Quando instrumentum machinae cessat exercere, ecran status in tempore rex monstrabitur, et partibus interferentiae predictus et direction moventis axis confirmabitur.
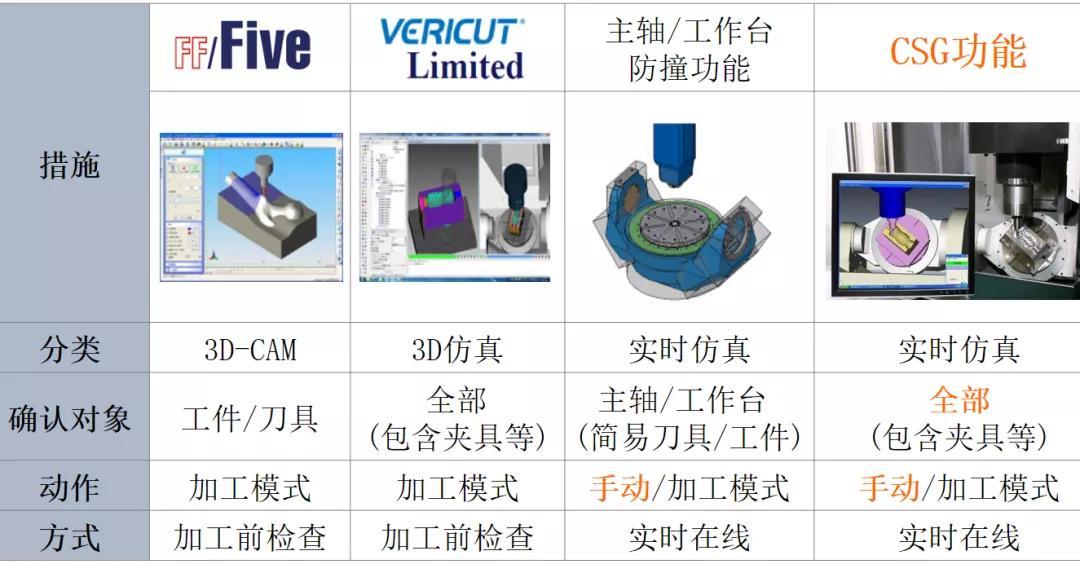
04
Rotation center correction
The change in rotation center caused by environmental and temperature changes can affect the precision of five axis machining. It should be able to automatically calibrate through the probe, verify the machining accuracy of 3-axis/indexing/5-axis machining, and ensure that the tool error is less than or equal to; 4 μ m.
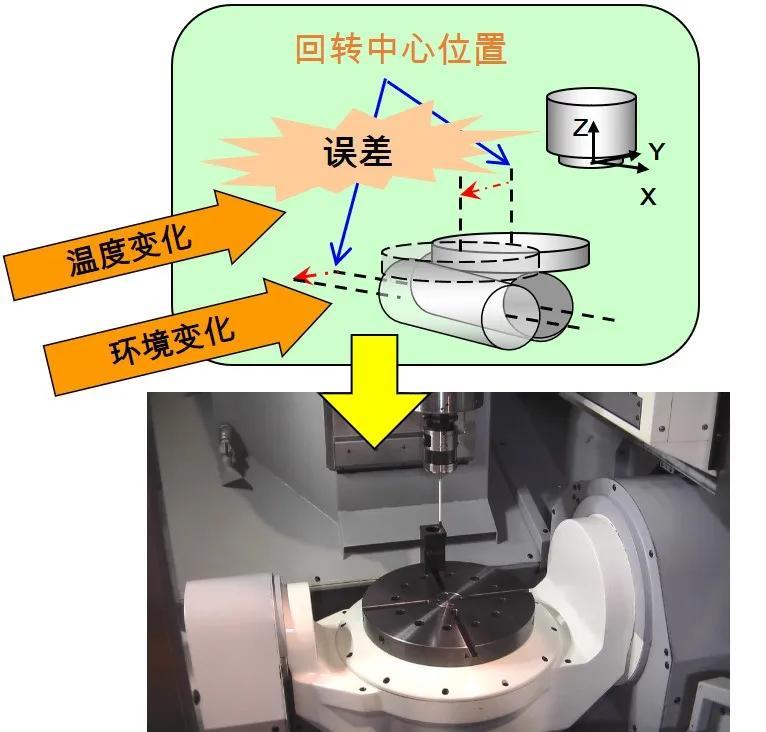
Automatically calibrate the 5-axis rotation center using a probe
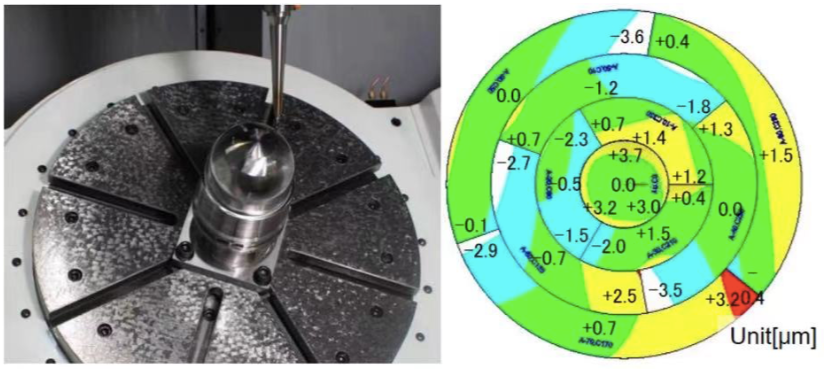
3-axis/indexing/5-axis machining accuracy verification machining
05
Precisis ligaminis
Linkage accuracy of a five axis machining center is a reflection of the results of multiple factors. Taking Makino D200Z as an example, provide processing cases to provide reference to linkage accuracy.
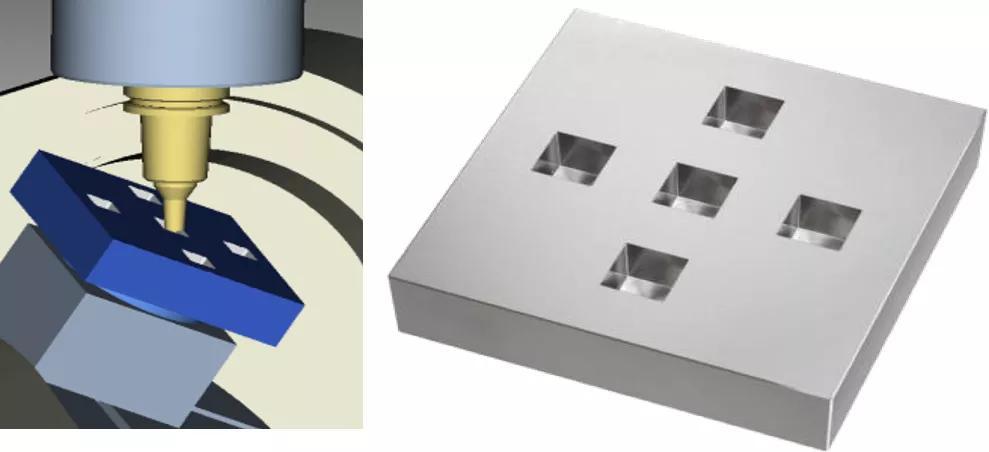
Processing equipment: D200Z
CAM:FFCAM
Workpiece material: NAK80 (40HRC)
Workpiece size: 140x140x35mm
Cavitate Mold: Clear angle R0.22mm, depth 20mm
Processing time: 1H35min/pocket
Cutting tools: 7 pairs and 6 types
Precisio Linkage: Position accuracy 2 μ m, shape accuracy 3 μ m
06
Processo suportus
Procedus machinationis quinque machinationis centri axis determinat an exercitus equipationis maximisatur. Exemplo, non regular instrumenta cutationis utilizat machinationis effectivitatem significantem meliora potest.
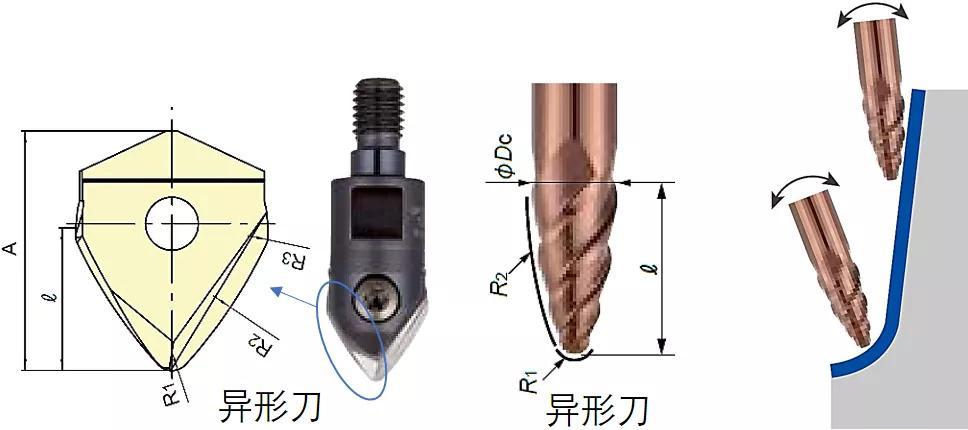
Processing case: Efficiency increased a 6 times!
Material: YXR33 (58HRC)
Forma et dimension: as shown in the figure below, depth 30mm, draft angle 2, clearance angle R3mm
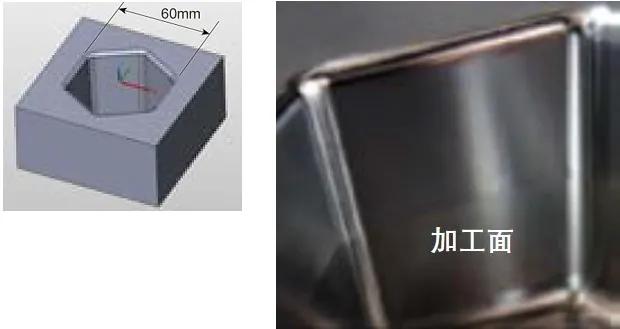
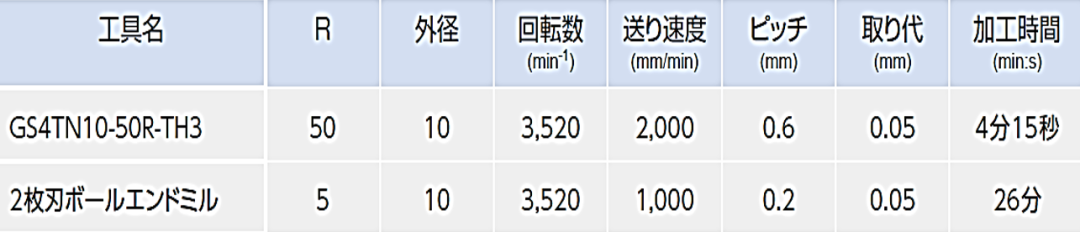
Okay, that's all for the editor to share here! Some students say that even after reading an article, they still can't understand it, just like watching TV. Learning UG programming well is actually very simple, as long as you learn systematically from experienced people, communicate more with friends, colleagues, and classmates. Quanto difficilior laboras. Felix! Move everyone's little finger to forward to your own circle of friends to benefit more partners