Many of our aluminum profiles require post-processing after extrusion production because they need to be assembled for special use scenarios. Some assembly precision is very high, so it is necessary to reduce the amount of processing deformation. There are many reasons for the deformation of aluminum alloy profiles during precision processing, which are related to materials, part shapes, production and manufacturing standards, etc. There are mainly multiple levels of deformation: deformation caused by thermal stress on the embryo, deformation caused by cutting force and cutting heat, and deformation caused by clamping force.
Processing technology countermeasures to reduce processing deformation
1. Reduce the thermal stress of the billet
Using natural or artificial aging and vibration solutions can partially remove the thermal stress of the blank. Preprocessio est etiam technica praecepta et fessima procedura. For hard and coarse heavy hair blanks due to their large capacity, there is also significant deformation after processing. Si non necessaria partes vacuum ante processantur et capacitatem singulae partee diminuetur, non solum potest deformationem processationis sequentis fluctus procedentis dimittere, sed etiam aliquid stressum thermalem postquam ante processatur et relinquetur tempus.
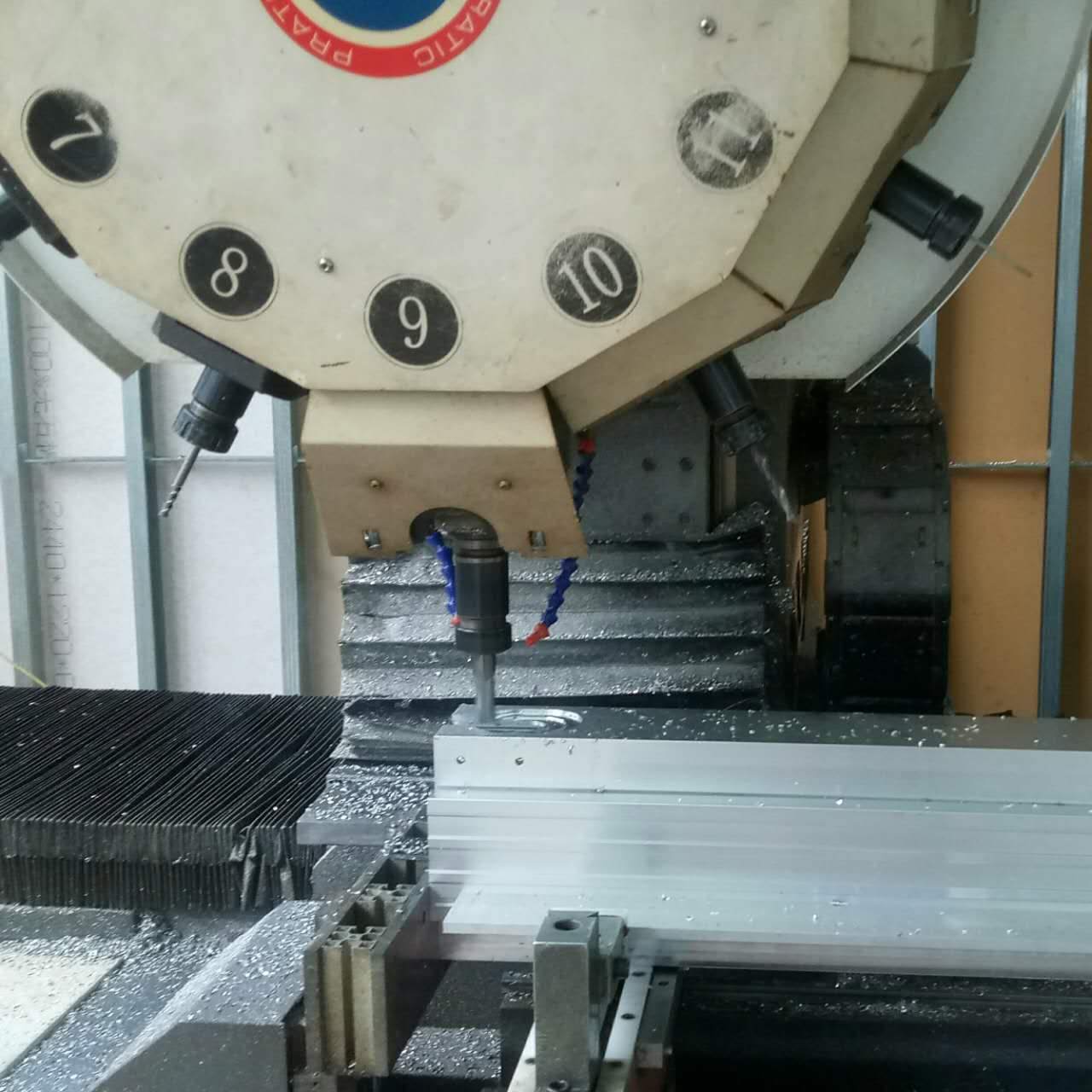
2. Improver the cutting ability of cutting tools
The raw materials and geometric parameters of cutting tools have a significant impact on cutting force and cutting heat. Proper selection of cutting tools is particularly important for reducing deformation during precision machining of aluminum alloy parts.
(1) Effectively select the main parameters of tool geometry.
●9312;Fore angle: Under the standard of maintaining the compressive strength of the cutting edge, the front angle should be moderately selected to be larger. On the one hand, it can polish the sharp cutting edge, and on the other hand, it can reduce cutting deformation, make the milling surface complete, and thus reduce cutting force and cutting temperature. Noli instrumenta negativa de angulo rake utilizat.
:: 9313; Angulus exterior: Dimensio anguli exterioris habet significativum impactum ad damnum exterioris cutationis et processationis. Carmen est criterium clave ut sequeretur angulum retrorsum. Durante calore militiae, propter altam velocitatem cutationis, gravitatem cargam cutationis, et altam valorem caloris, opus est ponare bonam standard pro dissipatione caloris caloris pipes caloris instrumenti cutationis. Pro hoc, minor angulum retrorsum elegere debet. Quando precision militiae est, necesse est ut angulus acus esset, ut dimitteret frictionem inter exteriorem segregationem et superficiem machinatum, dimittere deformationem ductilem, et idcirco exteriorem angulum ut maiorem esset.
●9314;Spiral angle: In order to ensure stable cutting and reduce cutting force, the spiral angle should be selected as large as possible.
●9315;Main inclination angle: Moderately reducing the main inclination angle can improve the heat dissipation standard of the heat pipe and reduce the average temperature in the precision processing area of the aluminum profile.
(2) Improver tool construction.
:: 9312;Reduce numerum dentium in instrumento cutationis et cresce spatiorem in compartmento chip. Pro substantiam deformationem plasticae materiae morientibus et deformationem in processione sequentem est spatio magna intra gazofilacium chipi necesse est. Pro hoc radius inferioris gazofilacionis chipi magnus esse debet et numerum dentium in instrumento succidentis relative parvus esse.
●9313;Fine sharpening technique for dentes. Valor superficie anguli lateralis sequentis inferior quam Ra=0.4um. Before applying a new culter, a fine grinding stone should be used to gently grind the side blade twice in front and behind to remove any remaining burns and slight serrated marks from the sharpening technique dentes. Non solum calorem reducere potest sed et deformationem reducere relative parvo est.
●9314;Strictly control the damage specifications of cutting tools. Postquam instrumentum detrahitur, verum laboris difficile crescit, temperatura concidit, et deformatio laboris consequente crescit. Therefore, in addition to using wear-resistant tool raw materials, the tool damage specification should not exceed 0.3mm, otherwise it is very easy to cause chip deposits. In cutatione temperatura opus non est necesse superire 100 °C ut deformationem non evaderet.
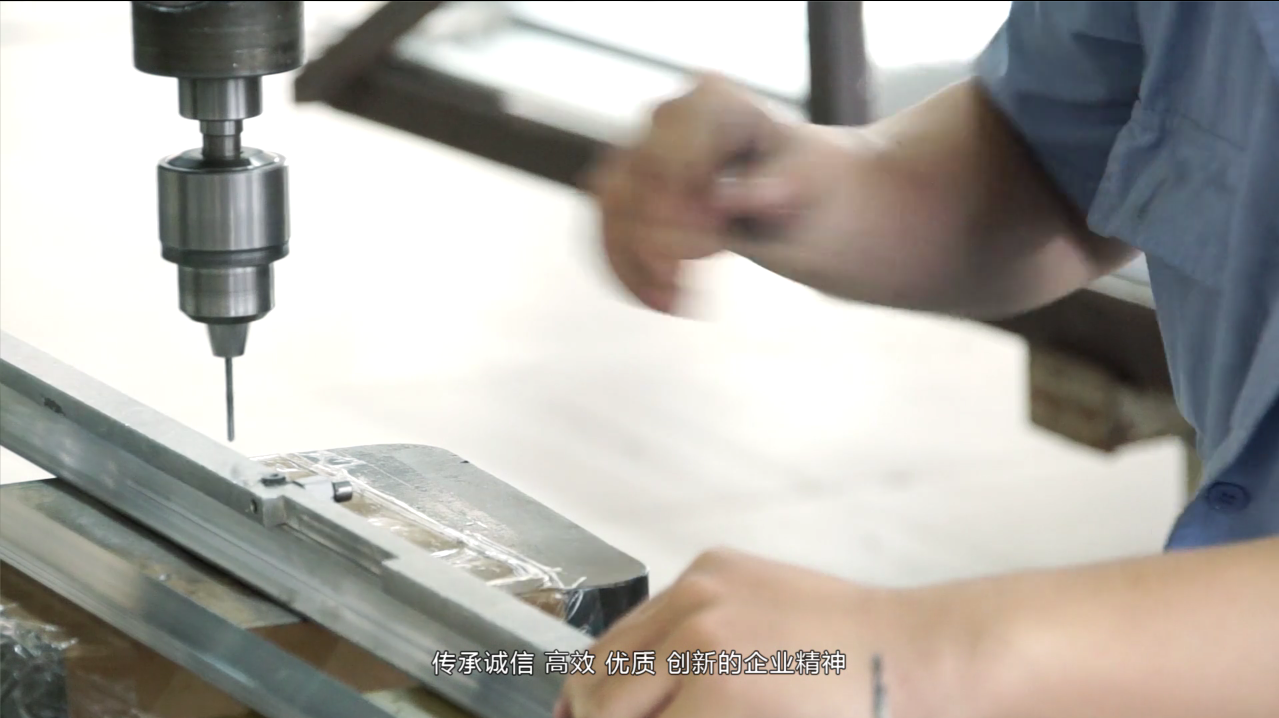
3. Improve the clamping method of workpieces
For thick walled die-casting works with weak strength, the following clamping methods can be used to reduce deformation:
* 9312; For thick walled shaft sleeve parts, if a three jaw self assured hydraulic chuck or elastic chuck is used to clamp from the axial direction, once it loosens after processing, the aluminum profile workpiece will inevitably deform. At this point, a radial interior hole clamping method with good strength should be used. Using the internal threads of the component for precise positioning, create a thread shaft neck with external threads and insert it in the internal threads of the component. Secure the inner hole with a rear cover plate and back tight it with a screw cap. Cum circulus exterius processatur, deformationem clampire potest et precision machinae satisfactoris attingere.
* 9313; When processing thick walled metal sheet workpieces, it is best to use a vacuum suction cup to obtain evenly distributed clamping force, and then use a small amount of cutting to process, which can effectively avoid workpiece deformation.
In addition, the sealing method can also be applied. To improve the processing stiffness of thick walled aluminum profile works pieces, materials can be added inside the workpiece to reduce deformation during clamping and cutting processes. Exemplo, per effundendum solutionem ureae quae continet 3% ad 6% nitrate potassium in opus fabricationis et processantur, opus aluminium profilium in aqua aut ethanol dissolvere et effundere potest.
4. Scientific arrangement of process flow
Durante velocitatem secessionis, propter magnam processationem capacitatem et intermittentiam secessionem, totum proceduram secessionis normale vibrationem causat, quod precision et difficilitatem processationis profilorum aluminium peribit. Therefore, the entire process of high-speed cutting and machining of CNC machines can generally be divided into rough machining, semi precision machining, surface milling, precision machining and other process flows. For parts with high precision requirements, sometimes it is necessary to perform secondary semi precision machining before proceeding with precision machining. After hard machining, the parts can naturally cool, remove the thermal stress caused by difficult machining, and reduce deformation. The remaining capacity after rough machining should exceed the deformation amount, usually 1-3mm. When precision machining aluminum profiles, it is necessary to maintain a uniform machining capacity on the surface, generally between 0.2-0.5 millimeters, to ensure that the cutting tool is in a stable state throughout the machining process, greatly reducing cutting deformation and obtaining excellent surface machining quality, ensuring the precision of the product.
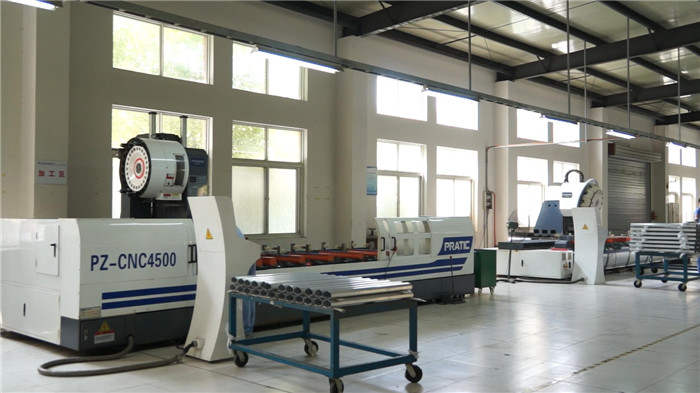
Practical methods for reducing machining deformation
Partibus ex aluminium alloy raw materialibus deformantur in to to processamento, et in addition to the reasons mentioned above, the operating steps are also crucial during the operation process.
1. In partes with large processing capacity, to achieve good heat pipe dissipation standards throughout the processing process and prevent heat concentration, symmetrical processing should be selected during processing. Si est plate a 90 mm densa quae processura est usque ad 60mm, et altera later subito secundum milling una latere, placitum quinque mm post processionem ad definitionem partitionem in una parte pertransibit. If continuous symmetrical machining is chosen, each side is machined twice to the final specification, ensuring a flatness of 0.2mm.
2. Si plura mold a concave sunt in profilo alloy aluminium, non est adequa sequentiale processionem methodos concave sequentiae ferentem post alterum dum processionem, quod facile ad unequam subterrandum partium et deformationem ducere potest. Select multiple layers for processing, with each layer being processed as much as possible to cover all the concave molds, and then processing the next layer to ensure even support of the parts and reduce deformation.
3. Reduce fortitudinem cutationis et calorem cutationis, mutantes utilitatem cutationis. Inter tres elementos utilis succidentis, quanta instrumenti retrorsum succidentis significat influentiam super succidentiam fortitudinis. Si fortitudo processionis magna est et fortitudo unius pascuae alta est, non solum causabit deformationem parterum, sed etiam continuabit detrahere fortitudinem spinae latae et reddere resistentiam ferentium succidentium. Si summa pascuae et cultris redacta fuerit, significa implevetur ad productivitatem. However, high speed cutting is commonly used in CNC machines, which can overcome this difficulty. In addition to reducing the amount of backstep and cutting, if the cutting speed is relatively increased and the speed ratio of the CNC lathe is increased, the cutting force can be reduced, and the machining efficiency can be ensured.
4. Attention should also be paid to the cutting sequence. Hard machining focuses on improving processing efficiency and pursuing a perfect cutting rate per unit time. Generally, reverse milling can be used. Remove unnecessary raw materials from the surface of the hair germ in the shortest and least amount of time, and generate the geometric contour required for precision machining. Focus machinae precision super altam precision et altam qualitatem est, et consilium est eligere milling surfaces. A causa gradual is dimisionis debilitatis dentium a magno usque a nulo in millionibus sequentibus, nivel machinae difficionis nimis diminuit, et nivel deformationis partium etiam diminuit.
5. Thick walled works pieces are inevitably deformed during machining due to clamping, even during precision machining. In order to minimize the deformation of the workpiece, the clamping piece can be loosened before the aluminum profile is finished to the final specifications, allowing the workpiece to be repaired to its original appearance at will. Then, it can be lightly clamped to the standard of being able to hold the workpiece firmly (completely by touch), so as to achieve the desired processing effect. In summario, punctus clampionis fortitudinis preferit super superficiem clampionis, et fortitudo clampionis in directo bonae robustitatis operis. Under the premium of ensuring that the workpiece does not loose, the lower the clamping force, the better.
6. When machining aluminum alloy parts with a concave die, it is not necessary to let the turning tool insert into the parts immediately like a Fried Dough Twists drill when machining the concave die as far as possible, resulting in insufficient space in the turning tool chip chamber, unsmooth milling surface, and bad conditions such as overheating, swelling, tool collapse, and tool breakage of the parts. First, add a Fried Dough Twists drill with the same specification or one size larger than the turning tool to drill the tool hole, and then use the turning tool to cut. Alternatively, the spiral cutting program can be produced using CAM software.