Reducing deformation measures during machining of parts is a comprehensive process that requires consideration of multiple aspects such as material, machining methods, fixture design, cutting parameters, etc. Here are some specific measures: First, optimize the manufacturing process of the blank to reduce internal stress: The blank will generate internal stress during the manufacturing process, which may cause deformation of the parts in subsequent processing. Per naturam senectionem, artificiam senectionem, aut vibrationem trationem, insidium interius vacuum partially eliminabitur, ut reducat deformationem in processione. 2. Choose appropriate cutting parameters and tool cutting parameters: cutting speed, feed rate, cutting depth, and other parameters need to be reasonably selected according to the material, shape, and processing requirements of the parts. Exemplo, reductione mensurae segregationis potest diminuere fortitudinem segregationis, sed etiam potest diminuere productionem efficientiam. In machinatione CNC, possibile est conservare machinationem efficientiam, reducing cutting forces by increasing the machine speed and feed rate. Tool selection: The material and geometric parameters of the tool have a significant impact on cutting force and cutting heat. Reasonable selection of tool geometry parameters, such as rake angle, rake angle, helix angle, and lead angle, can grind sharp edges and reduce cutting deformation. In addition, improving the tool structure, such as reducing the number of milling cutter teeth, increasing the chip space, and refining the grinding teeth, can also reduce cutting heat and cutting deformation. 3 , Reasonable selection of clamping method and clamping force fixture design: The design and selection of fixtures have a significant impact on the deformation of parts during machining. Reasonable fixture design can ensure the stability of parts during processing and reduce the impact of clamping force on part deformation. For thin-walled parts with poor rigidity, axial end face compression or fixtures such as vacuum suction cups can be used to obtain uniformly distributed clamping force. Clamping force control: The clamping force should be as small as possible while ensuring that the work piece is not loose. Excessive clamping force can cause deformation of the parts. In addition, the clamping force should be applied as much as possible on the supporting surface and in the direction of good rigidity of the workpiece. 4 , Reasonably arrange the processing sequence and cutting parameters: A reasonable processing sequence can reduce the internal stress of parts and lower the risk of deformation. Exemplo, machina difficile primum exercere potest, secundum machina precision ut dimitteret effectum succidentis fortitudinis et calore ex parte seceret. Büyük makinelerin allowansı olan parçaları, simetrik makineler, ısı konsantrasyonu nedeniyle deformasyonu önlemek için kullanılmalı. Cuting parameters: During the cutting process, cutting force and cutting heat are reduced by changing the cutting parameters. In machinationibus CNC, hoc objectio accipere potest a reductione summae retrorsum, crescere tempus fertilis, et velocitatem machinae crescere. 5 , Real time monitoring and adjustment of machining process monitoring: Real time monitoring is carried out during the machining process to detect and correct deformations in a timely manner. In monitoring parametros such as cutting force and cutting temperature, it is possible to determine whether the parts have undergone deformation and take corresponding measures for adjustment. 6 , Other measures to improve workpiece clamping methods: For parts with poor rigidity such as thin-walled workpieces, filling methods can be used to increase process rigidity and reduce deformation during clamping and cutting processes. Surface treatment: Through surface treatment processes such as anodization, the surface characteristics of the parts can be further improved or altered, enhancing their rigidity and resistance to deformation.
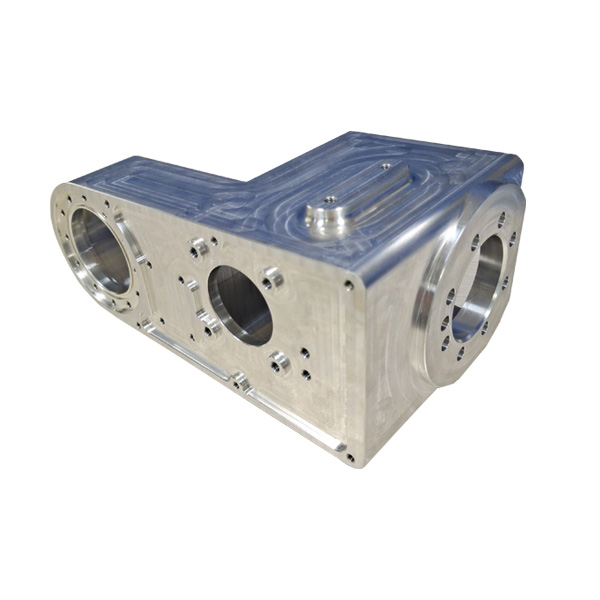