We all talk about CNC Machining and have been pursuing the machining techniques of CNC machines. In my opinion, the so-called techniques mainly focus on two aspects: machining efficiency and machining stability, both of which are closely related to the output value that CNC machines bring to machining manufacturers.
1. Improver the processing efficiency of the walking machine:
a. Quando finis in spina prima finitur, duae spinae inter se proximae sunt, et melior erit splendor superficie. Quanto minor summa parterum, melior est.
b. Prius cutationis, alta productivitate reversa machina utilizatur ad finem gradum processationis exterior diametro operantis, et simul cutatio beneficium est ad reducendum vibration is.
c. Finally, the CNC core machine mainly completes the final precision machining on the secondary spindle. This process of the core machine belongs to inner diameter machining, but it can also be outer diameter machining
2. Increase the stability of the machining process of the walking machine
a. Generally, in the application of radial machining, it is necessary to perform internal turning and drilling on the main spindle, and use the support effect of the guide sleeve on the bar material to improve the stability of radial machining.
c. Quando iterum opus est milling, finis facies milling preferitur. In addition, the power and stability of the rotating shaft of the walking machine are limited, so the smaller cutting force of the walking machine, the better. Walking machine end face milling can meet this requirement.
Shenzhen EMAR Precision Technology has nearly 20 imported CNC lathe machines from Japan, mainly from brands such as Nomura, Star, and Tianjin. In fact, CNC lathe machines are a type of CNC lathe, fully known as the walking type CNC lathe, which can also be called a spindle box mobile CNC lathe, an economical turning milling composite machine tool, or a longitudinal cutting lathe. Compared with conventional CNC lathes, its advantages mainly lie in the machining process. It can complete machining processes such as turning, milling, drilling, tapping, boring, and gong in one clamping, and is commonly used in the field of high-precision CNC machining.
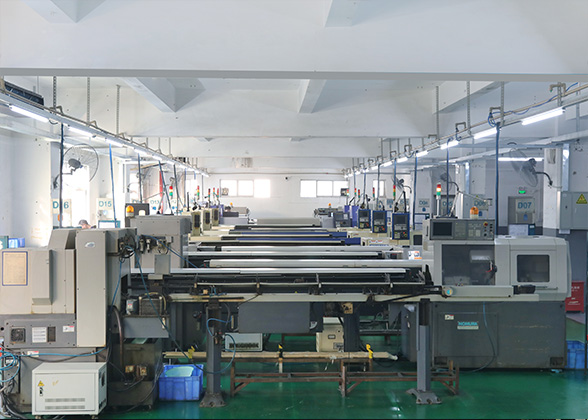