Introduction to G32 machining end face threads:
Overview: The end face threads are mostly rectangular threads, and the self centering chuck (disc thread) of the lathe uses this structure. Hic typus threadis non habet speciosam annotationem codicem, saepe annotationem textum.
Figure 2-8 is a schematic diagram of the end face thread
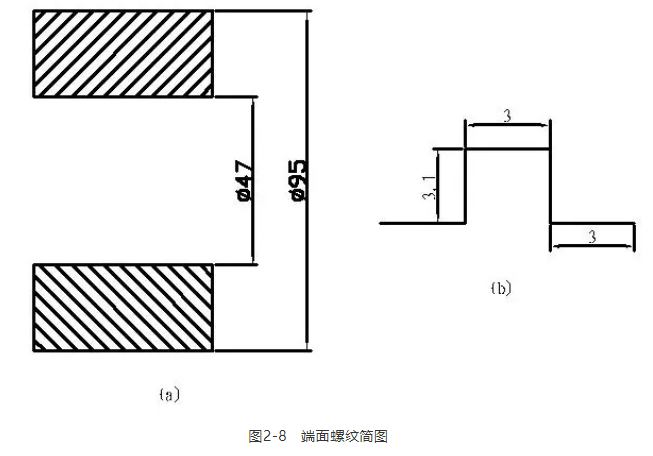
Figure (a) is a schematic diagram of the overall structure of the end face thread, while Figure (b) is a partial enlarged view of the end face thread. It is specified that when the thread depth is less than 5mm, an additional 0.1mm needs to be added.
Determination of end face thread rotation direction:
In the case of the main spindle turning forward, turning from the outside to the inside belongs to right-handed (clockwise), and vice versa is left-handed thread (counterclockwise).
Format instruktionis: G32 X-F_ (X est coordinatus puncti concidi, F est plumbus radii)
Program statement (only the threaded section of the end face)
G99 M3 S500 T0202; (Slot cutter B=3mm)
G0 X100 M8;
Z-0.5;
G32 X40 F3.0;
G0 Z3;
X100;
Z-0.7;
G32 X40. (Considering blade width diagram 2-9) F3.0;
G0 Z3;
X100;
Z-1.0;
G32 X40 F3.0;
G0 Z3;
X100;
Z-1.5;
G32 X40 F3.0;
G0 Z3;
X100;
Z-2.0;
G32 X40 F3.0;
G0 Z3;
X100;
Z-2.5;
G32 X40 F3.0;
G0 Z3;
X100;
Z-3.1;
G32 X40 F3.0;
G0 Z90;
M5;
M30;
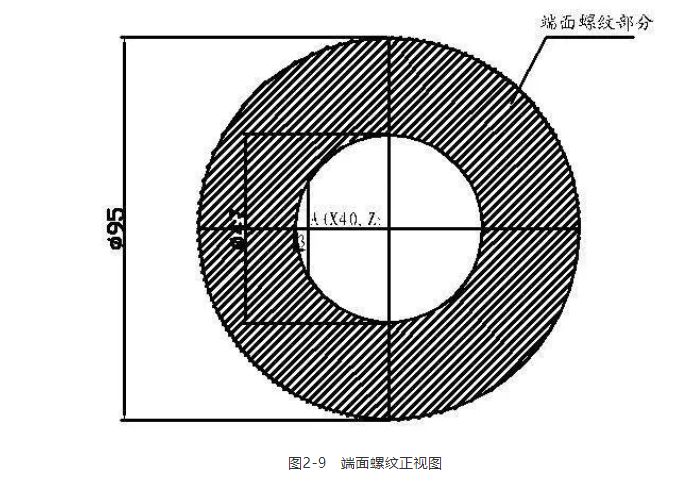
Note: Positioning should be consistent these times.
●9313;Introduction to Variable Pitch Thread Processing
Some domestic CNC systems, such as Guangzhou CNC (GSK), use G32 instructions when machining variable pitch threads. As shown in Figures 2-10:
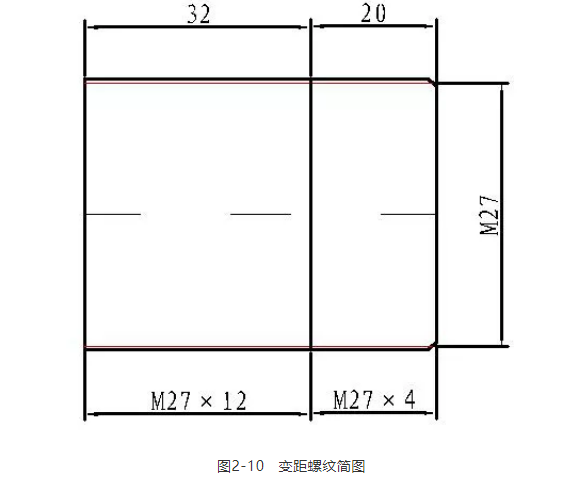
Figure 2-10 Schematic diagram of variable pitch thread
Calcula numerica:
The tooth height (diameter value) of M274 is 1.34=5.2mm;
Altitudo dentis (valor diameter is) M2712 1,312=15,6mm est;
Altitudo dentis minima altitudo dentis fundata est:
So the minor diameter is 27-5.2=21.8mm.
Quando variabile radices in pitch conversa, velocitas spindle per maxima radicem determinata est (P=12).
Program statement (only threaded section)
G99 M3 S200 T0202;
G0 X30;
Z3;
X26;
G32 Z-20 F4.0;
G32 Z-56 F12;
G0 X30;
Z3;
X25.6;
G32 Z-20 F4.0;
G32 Z-56 F12;
;
G32 X30;
Z3;
X21.8;
G32 Z-20 F4;
G32 Z-56 F12;
G0 X30;
Z90;
M5;
M30;
The so-called variable pitch thread refers to a specified reference pitch value F starting from the thread cut in, and then generating a pitch difference K (increase or decrease) every other pitch
In quibus sistemis CNC importatis, sicut FANUC, est instruktio particula G34 ad machinandum variabilis pitch threads.
Formatus instruktionis: G34 X_Z_F_K_;
Inter eos X et Z sunt positiones finis virgae, F est plumbus in longo oriente axis a principio puncto, K est incrementa et diminutio plumaris per rotationem spinalae, et in latione K valoris est 0,0001-500,000mm, sicut in sequente figura monstrata est.
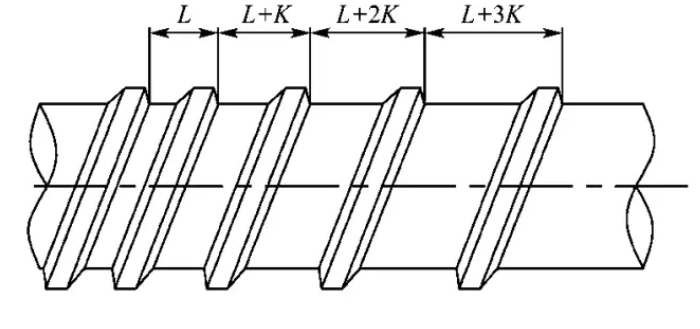
Exemplo, prima plumbus quinque mm est, prima incrementa 1mm est, longitudo fila 50mm est, et programma G34 Z-50 est F5. K1.
●931414Processingof multi thread threads
Multi line threads are generally used for transmission and are straight threads. CNC Machining of multi line threads can be done by calling subroutines using G92. Imported machine tools also support G32 instructions for machining multi line threads, and G76 instructions can also be used for machining multi line threads (as discussed later).
G92 calls subroutines to process multi thread machining as shown in Figure 2-11.
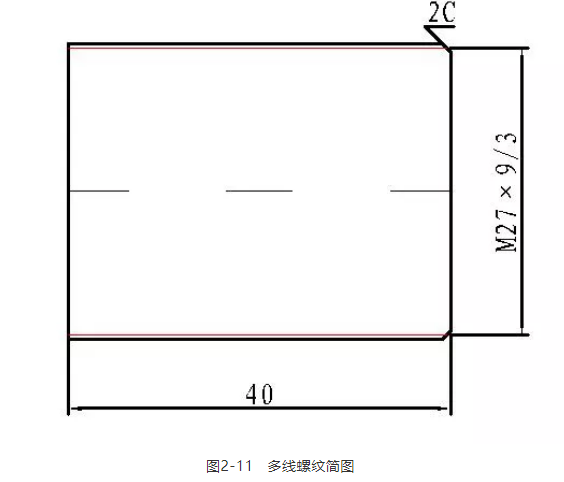
The meaning indicated in the figure: M279/3
Inter eos M27 est nominal is diametrus, 9 est lignum plumbum, et 3 est hydrium.
Because: lead=number of pitch lines, therefore: this is a three wire thread.
Calcula numerica:
Diametrus maximus=27-0.133=26.61mm;
Minimum diameter=27-1.33=23.1mm;
Program statement (only threaded section)
Subprogram (O0046)
G92 X26 Z-40 F9;
X25.7;
X25.4;
X25.2;
X25.0;
;
X23.1;
M99;
principal program
G99 M3 S700 T0202;
G0 X30 M8;
Z3;
M98 P0046;
G0 X30;
Z6;
M98 P0046;
G0 X30;
Z9;
M98 P0046;
G0 Z90;
M5;
M30;
Z3. Z6. Z9. Increase one pitch per position (P=3)
Some systems also support G32 machining of variable pitch threads
Instructione formata: G32 X_Z_F_Q_;
Ubi X et Z sunt positiones finis virgae F est plumbum virgae et Q est angulum initii virgae. Incremente est 0.001, decimalum punctum non potest specificare; If processing double thread and the corresponding displacement is 180, specify Q180000
Anglo initio Q non est valor modal a et per singulos vices indicabitur, alioquin systema nullum esse considerabit
Multi thread machining is effective for G32, G34, G92 and G76 instructions.
●9315Processingof trapezoidal threads
On CNC lathes, G76 thread cutting cycle instructions can be used to machine trapezoidal threads using methods such as oblique and staggered cutting, but there are certain technical difficulties. Therefore, based on long-term practical experience, a set of precise calculations of programming data using a series of empirical formulas has been developed. By using thread cutting instructions G32 and calling subroutines, and cleverly setting machining methods in the subroutines, qualified trapezoidal threads can be safely and reliably processed.
Analisi programationum et machinationum:
(1) When grinding the blade, pay attention to ensuring that the cutting edge of the turning tool is consistent with the dent shape angle, and the width of the cutting edge must be less than the width of the groove bottom.
(2) Try to make the gap between the dents during the turning process enough large to ensure smooth chip removal with a single cutting edge of the turning tool. Consolitabilis est trapezoidal thread groove bottom width of 1.7mm with a pitch of 5mm and a sharpened blade tip of 1.2-1.4mm. Excessive blade tip can cause the gap between the blade tip and the tooth side to be too small, making it difficult to remove debris and prone to cutting; A too small tool tip can cause a decrease in the rigidity of the tool tip, which can easily cause vibration and result in poor machining surface roughness, making it difficult to control accuracy.
(3) Attention ad positionem instrumenti conversionis antequam virgam convertere. Distancia a summitate instrumenti ad summitatem dentium maior est quam altitudo dentium. Si minus est altitudo dentium, causabit friction inter summitatem instrumenti et summitatem dentium ferentium in post ferentiam, resultans in solitudinem.
(4) Subroutines disveloppate et vocate, quae unum subroutinum aut multi subroutinum utilizat.
1. Calculation of programming data
(1) Posicionis punctus X vacuum=nominal is diameteris+(0.5P+ac) 2+1, ubi P est pitch, ac est clarens finis dentis, et altitudo dentis 0.5P+ac. Elegite valorem interrumpuae dentis basis super granditudinem puncti, sicut in mensa infra monstrata est.

(2) First cutting point X value, X=nominal diameter - average deviation of upper and lower parts -0.2
(3) Minus diameter=nominal diameter - (0.5P+ac) 2
(4) Processing addend=(X-value of the first cutting point - minor diameter)/X-direction feed amount (diameter value)+1
(5) U=X valor vacuum puncti positionis - X valor primi puncti cutionis.
2. Cutting route: Generally, the left and right cutting method is used to process trapezoidal threads, and those with small pitches can be divided into coarse turning, semi precision turning, and precision turning; qui habent hydrias magnas dividentur in circuitum tunicam semi tunicam conversum semi pretium conversum et pretium conversum Using the left and right cutting method, when calling the subroutine once, the turning tool enters a cutting depth and moves one gap to the right after turning one tool to the left, and then turns another tool. When calling the subroutine again, the turning tool enters another cutting depth and moves one gap to the right after turning one tool to the left, and then turns another tool until it is completed.
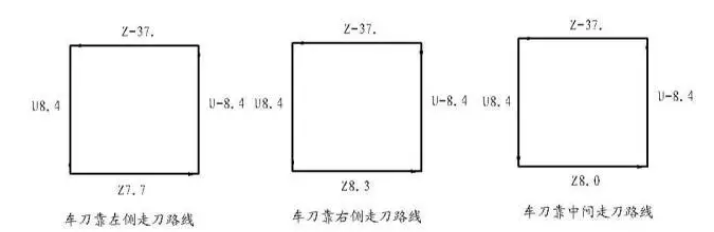
[Exemplo trapezoidal thread machining] As shown in the figure below, it is a trapezoidal thread machining part.
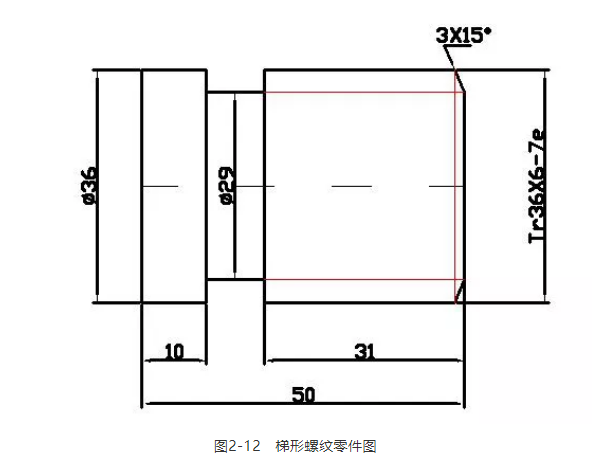
3. Calculation of data for machining trapezoidal threads
(1) Rough positioning point X value
X=nominal diameter+(0.5P+ac) 2+1=36+(0.56+0.5) 2+1=44
(2) Check the table to determine the upper and lower deviation values of the nominal diameter: the upper deviation is 0, the lower deviation is -0.375, and the average value is -0.2. The X value of the first cutting point is 36-0.2-0.2=35.6
(3) Minus diameter=nominal diameter - (0.5P+ac) 2=36- (0.56+0.5) 2=29.
(4) Processing addend=(X-value of the first cutting point - minor diameter)/X-direction feed amount (diameter value)+1=(35.9-29)/0.1+1=67
(5) U=difficile positioning point X value - First cutting point X value=44-35.6=8.4
4. Calculate the size of the trapezoidal thread and check the table to determine its tolerance
Diametrus magnus D=36
Secundo mensam, tolerantia d determinata est quasi d-0.5p=36-3=33, ita d=33
Tooth height h=0.5p+ac=3.5
Minus diameter d=d, medium -2h=29
Crown width f=0.336p=2.196
Tooth base width w=0.366p 0.536a=2.196-0.268=1.928
Based on experience, it is reasonable to use a trapezoidal thread with a tool tip width of f=1.5mm.
Using a 3.1mm measuring rod to measure the middle diameter, the measurement dimension M=d+4.864d-1.866p=36.88, and the tolerance (0-0.355) is determined based on the middle diameter tolerance zone, resulting in M=36.525-36.88
5. Programmas CNC scribe
G99 M3 S300 T0101;
G0 X44 Z8; (44 est valor X vacuum puncti positionis)
M8;
M98 P470002; (47 is the number of rough machining tools)
M98 P200003; (20 is the number of precision machining tools)
M9;
G0 X100 Z100;
M30
Scribe subroutines machinaturae difficile
O0002
G0 U-8.4; (8.4 est valor U)
G32 Z-37 F6;
G0 U8.4;
Z7.7;
U-8.4;
G32 Z-37 F6;
G0 U8.4;
Z8.3;
U-8.4;
G32 U0 Z-37 F6;
G0 U8.3;
Z8;
M99;
Writing precision machining programs
O0003;
G0 U-8.4;
G32 Z-37 F6;
G0 U8.4;
Z7.9;
U-8.4;
G32 U0 Z-37 F6;
G0 U8.4;
Z8.1;
U-8.4;
G32 U0 Z-37 F6;
G0 U8.3;
Z8;
M99;
The above mentioned workpiece can also be programmed using G92 subroutines.
principal program
Exactly!
G00 X44 Z6; (Thread cutter rapidly reaches diameter) Φ 44mm End Face Outer 3mm)
M98 P60002; (Coarse car calls O0002 subroutine 6 times)
M98 P80003; (Yarım ciddi araba O0003 subroutine 8 kere çağırır)
M98 P80004; (Semi precision car calls the main program O0004 subroutine 8 times)
M98 P80005; (Fine car calls O0005 subroutine 8 times)
G0 X100 Z100; (Thread cutter cito ad initium programae redit)
Exactly!
O0002 (subroutine automobilis difficile)
G00 U-0.5; (Hard turning with each feed depth)
M98 P0006; (Calling the basic subroutine O0006)
M99; (Subroutina finit et redit ad principem programam)
O0003; (Semi robustum raedam subroutinum)
G00 U-0.3; (Semi rough turning with each feed depth)
M98 P0006; (Calling the basic subroutine O0006)
M99; (Subroutina finit et redit ad principem programam)
O0004; (Semi precision car subroutine)
G0 U-0.15; (Semi precision turning with each feed depth)
M98 P0006; (Calling the basic subroutine O0006)
M99; (Subroutina finit et redit ad principem programam)
O0005 (subroutine automobilis precisius)
G0 U-0.05; (Precision turning with each feed depth)
M98 P0006; (Calling the basic subroutine O0006)
M99; (Subroutina finit et redit ad principem programam)
O0006 (Basic subroutine)
G92 U-8 Z-37 F6; (Turning the left side of the thread)
G00 W0.43; (The threaded knife quickly moves 0.43mm to reach the side of the right tooth)
G92 U-8 Z-37 F6; (Turning the right side of the thread)
G0 W-0.43; (Move -0.43mm to return to the axial position on the left side of the thread)
M99; (Subroutina finit et redit ad principem programam)
Can we give it some attention before we leave? Update UG programming videos cotidie.
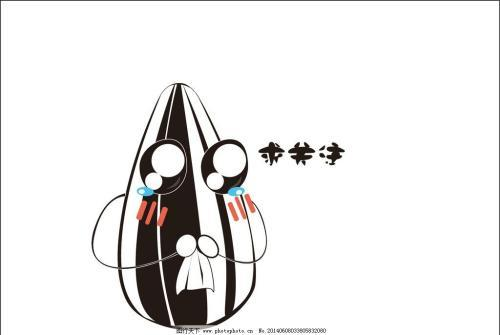