Quomodo sequentem fokus determinare quando machinam laser sequentem est? Shenyang laser cutting manufacturer explicat tibi:
1. Cutting focus on the surface of the workpiece: This method is also known as zero focal length and is commonly used for cutting workpieces such as SPC, SPH, SS41, etc. When using, the focus of the cutting machine is selected to be close to the surface of the workpiece. In this mode, the smoothness of the upper and lower surfaces of the workpiece is different. Generally speaking, the cutting surface close to the focus is relatively smooth, while the lower surface far away from the cutting focus appears rough. Hoc modus iuxta praecepta procedentis superioris et inferioris superioris in aplicationibus praecepticis determinabitur.
2. Cutting focus inside the workpiece: This method is also known as positive focal length. When the work you need to cut is stainless steel or aluminum plate steel, the commonly used cutting point is inside the workpiece. Sed unus defectus huius method on is est quod a principe concussionis, amplitudia concussionis relativamente maior est quam punctus concussionis super superficiem opus. In eadem tempore, modus haec maximus fluxum aeris concussionis requirit, temperatura sufficiens, et tempus paululum concussionis et perforationis. So when you choose stainless steel or aluminum as the main material for the work piece, choose materials with high difficulty.
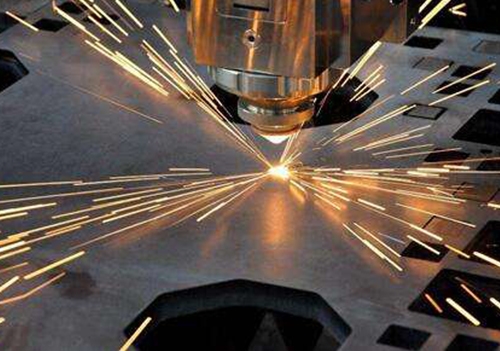
3. Cutting focus on the workpiece: This method is also known as negative focal length, because the cutting point of the laser cutting machine is not located on the surface or inside of the cutting material, but is positioned above the cutting material. Haec methodo prima est ut materiae cum alta densitate seceret. Reage quare haec methodo posit focus supra succidentam materiae est in principio, quia vasae plateae magnae latitudinem succidentae requirunt, alioquin oxygenum, extractam a nozzle, non sufficit, resultat in diminutionem temperaturae succidentis.
Prima advantage laser cutationis machinae est quod densitas energiae ligni laser alta est, sic diameter focal pulchritudinis est tam parvus quam posibilis ad producendum angulos cutos. Because the smaller the focal depth of the focusing lens, the smaller the diameter of the focal spot. For high-quality cutting, the effective focal depth is also related to the lens diameter and the material being cut. Pro hoc, constituere positionem foederis relative to the surface of the material being cut is crucial.
Contenium artificis ab internet est. Si quaestiones habes, contacta me ut deleam illum!