Because most domestic stamping mold manufacturing enterprises are small and medium-sized enterprises, and a suitable portion of these enterprises are still in the traditional workshop style production management stage, they often neglect the stability of molds, resulting in long mold development cycles and high production costs, which severely restrict the pace of enterprise development.
Ut cognoscitur, materiae metallici, quae in stampionis mollis utili sunt, multas varietates includent, et necessitates et electiones criteria materiae eorum etiam differunt a causa diversorum effectorum partium in molda. Pro hoc, quomodo elegere fabrica rationale facta est unum de optimis operibus in fabricatione.
In practical operation, mold designers tend to select mold materials based on personal experience, which often leads to unstable mold forming due to improper material selection of mold parts in stamping. It is worth noting that during the stamping process, each type of stamping sheet has its own chemical composition, mechanical function, and characteristic values closely related to stamping function. The instability of stamping material function, fluctuations in stamping material thickness, and changes in stamping material not only directly affect the accuracy and quality of stamping processing, but may also lead to damage to stamping molds.
In solvit problemam stabilitatis molae, necesse est stricto controlare ex sequentibus aspectis:
1. In process planning stage, by analyzing the product, potential defects that may occur during production can be predicted, and then a stable production process plan can be developed;
2. Implement standardization of production processes and production techniques;
3. Establite datum bāzes et continua summarize et optimizate illud; Using CAE analysis software system, obtain the optimal solution plan.
This article is from EMAR Mold Co., Ltd. For more EMAR related information, please click on www.sjt-ic.com,
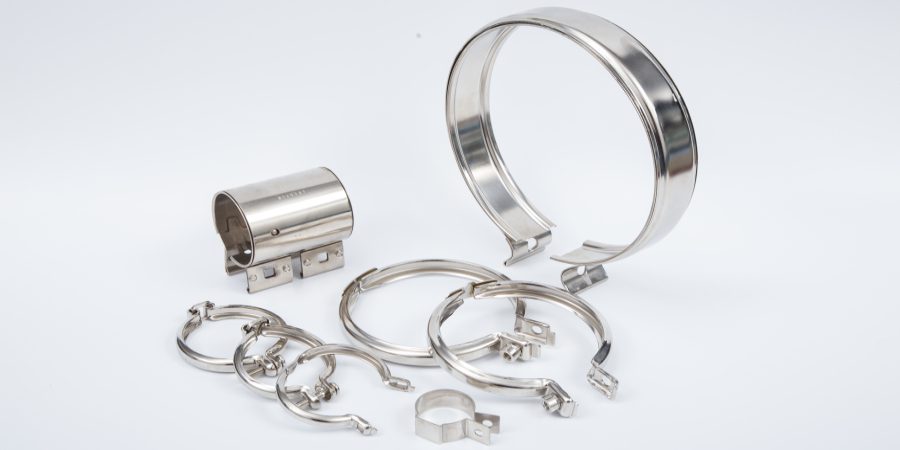