Struktura stampionis precisiorum directo precisium et qualitatem stampionis precisiorum parterum influent. Como portator importante in manu frigido stampionis, stampionis particula multo commune habent. And it is precisely because of its own characteristics that we need to consider a scientific and reasonable perspective when planning stamping dies.
Good mold planning can improve mold lifespan, durability, production power, reduce production costs, and ensure product quality. So what should we pay attention to when planning molds?
1. In mold planning, the selection of mold materials, heat treatment and surface treatment, especially for metal deep drawn parts.
2. Material strip planning is an analysis of the product forming process, which basically determines whether the stamping die is successful.
Prius plantatione structurae materiae, necesse est intellegere necessitates servitutis parterum, inclusione function is materiae, punching tonnage, punching table top, SPM (punching per minuta), feeding direction, feeding altitudo, mold thickness requirements, material utilisation rate, and mold service life. When planning the material strip, CAE analysis should be conducted simultaneously, with the primary consideration being the thinning rate of the material, and more communication with the customer is necessary.
3. Quando testatur molam, oportet lentem claudere molam superiorem. Quando est processus extensionis, oportet fusionem utilizat ut menseret densitatem position is materiae. Postquam gapus inter positiones materiae densitatem materiae attinget, proba molam iterum. Angulus succintionis primum alignetur. Uter, quaeso, insertiones movabiles in catena de tiraculo ut adjustet altitudinem eius. References hole and reference surface must be stamped with the mold before placing the product on the measuring tool for measurement, or sending it to CMM for 3D presentation.
4. Dan rufus bene conformetur, alioquin productus stabilis erit et non potest postea modificationem et iudicium facere, et partis granditudo non potest requirere. For parts with many bends, the bending should be adjusted step by step according to the process when adjusting the mold.
6. When adjusting the forming viewpoint, it is possible to reduce the R angle during bending or move the line reference to achieve the goal of reaching the forming viewpoint.
7. When adjusting the mold, most people use shims to adjust the inequality of the molded male or move the molded male part back and forth left and right. The shims are usually made of stainless steel hard sheets.
8. Concerni terminum succidentium cogitationis cogitationis, opus est sequere post molationem, et positiones speciosas in transverso succidentibus impleretur.
9. Concerni multis positiones referentiae foedus singulorum punctionis elige ut non efficiat accuracionem post gradum per gradum punctionem et succidentem.
10. Regarding product rupture, various methods such as adding packaging, extruding materials, increasing the forming area of the sheet rod, and opening holes can be adopted during early stretching. CAE analysis should be conducted before mold modification.
This article is from EMAR Mold Co., Ltd. For more EMAR related information, please click on www.sjt-ic.com,
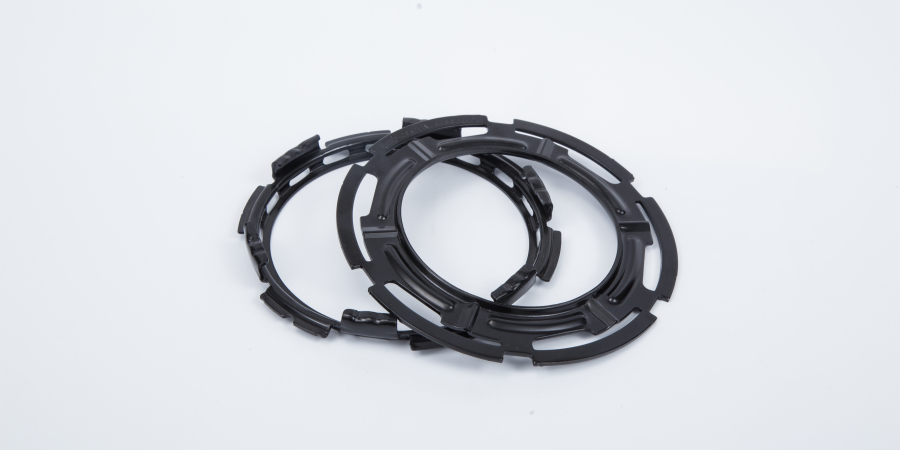