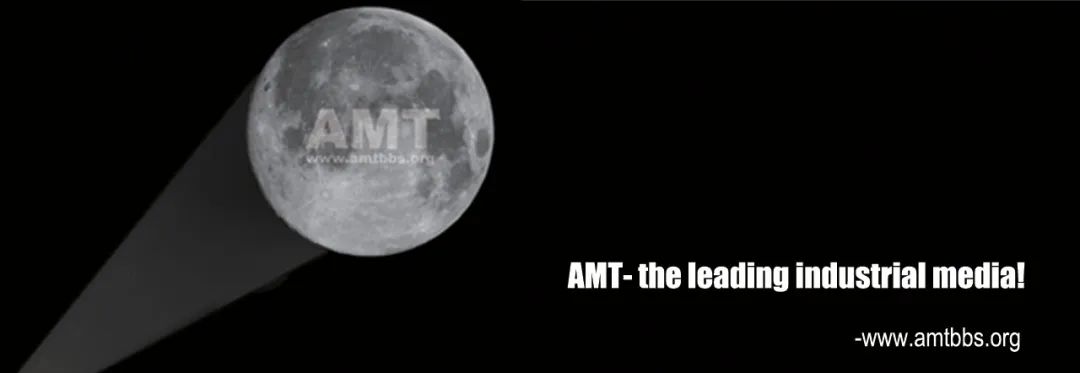
CNC milling significantly improves cutting efficiency and tool life
The significant progress made in improving metal cutting efficiency is the result of joint efforts of tools manufacturers, machine tools manufacturers and software developers. Insertio milling (Z-axis milling) bona exemplum machinae est. Inter insertionem militiam, instrumentum rotationis directo in laborem secundum orientem Z axis retractit instrumentum supra longe axis Z. Unc, horizontale secundum orientem X axis aut Y axis in longitudinem certam distantiam movet, et verticale succident, quæ superlapit cum priora parte succidentia, ut plus materia operantium succidet. Insertio milling multa beneficia habet. Especially in long overhanging machining (such as milling deep mold cavities), the traditional flat milling method (i.e. milling from one side of the workpiece to the other) has to reduce the cutting speed in order to minimize the lateral force that can cause chatter. During insertion milling, the cutting force is directly transmitted to the machine spindle and worktable, thus achieving a much higher metal removal rate than traditional milling methods. According to AMT Software Company, the Prospector CAM software package developed by the company includes the insertion milling function. Compared with traditional flat rough milling using button shaped milling cutters, the metal removal rate of insertion milling processing can be improved by at least 50%. Due to its ability to minimize the lateral load on machine tool components, slot milling can be used for old-fashioned or lightweight machine tools with insufficient rigidity to improve productivity. John Ross, the marketing manager of Doushan Machine Tool Company, agrees with the statement that slot milling can reduce the cutting force acting on low performance machine tools, but he adds that in new machine tools with structural design that is conducive to slot milling processing, the advantages of this process can be maximized. He pointed out that due to the direct transmission of milling cutting force into the machine tool spindle and worktable, various problems caused by weak workpiece clamping can be minimized to the greatest extent. Bill Fiorenza, Product Manager of Ingersoll Tool Company's Mold Production Line, stated that insert milling helps reduce cutting heat entering the tool and workpiece. He said, "During insertion milling, there is not much heat entering the workpiece because the cutting tool rotates a fast speed to cut in and out the workpiece. Only a small portion of the workpiece with a moving step makes contact with the tool." This feature is particularly useful when cutting difficult to machines materials such as stainless steel, high-temperature alloys, and titanium alloys. Fiorenza explicata est dum insertione et milling demonstratione, "Usually, temperatura cipsi metallorum altissima est, et etiam paniculum sandwichom in pila cipsis coquere potes. Sed, cum impleta est insertio et milling processus, statim manum tuam super pecus laboris possis ponere et sentere frigidorem ad touch." Reductione caloris caloris non solum vitam instrumentorum extendere potest, sed etiam deformationem opus minimere potest.
【 Worth a try 】 Insertion milling can greatly accelerate the production rhythm of high-end and complex components. Gary Meyers, milling product manager at Seco Tool Company, stated that "the most commonly used are as of insert milling technology are mold manufacturing and aviation industry, as the types of parts in these industries are very suitable for insert milling." Mold manufacturers need to mill various complex shapes on the overall workpiece to form mold cavities, and many aviation parts are also processed from whole blanks. He said, "The cutting amount of these workpieces is astonishing, and in some cases, it is necessary to cut 50% -60% or even more of the workpiece material from the blank." Kenyon Whetsell, Product Manager of DP Technology, the developer of ESPRIT CAM software, pointed out that in addition to manufacturers of complex parts, general-purpose machining workshops can also benefit from the application of insert milling technology. Metal processing WeChat, content is good and worth following. He said, "Some workshops are still using 2.5-axis machining technology, which has outdated machine s, poor rigidity, and insufficient clamping force of fixtures. However, they still hope to improve productivity.Is crucial, et traditional milling strategies can generate chatter and vibration, shortening tool life. Kenner recently rebuilt its Z-axis milling cutter sales platform to meet the growing demand of users." The request for. "Tempus probavit, quod volumen venditorum Z-axis milling cuttorum semper crescit, cum tempus annorum crescere 40%."
The design characteristics of milling cutters: Tool manufacturers have developed various milling cutters that can fully leverage the advantages of milling technology. Meyers de Shangao Tools dixerunt quod fortitudo talium instrumentorum in principio directo translata est ad axim Z. Forma geometrica insertionis calcatoris milling similis est ei 90 umeris quadratis calcatoris. Differentia est in deviatione principis anguli flammae de aeroplano verticale a paucis gradibus, quæ 87 est pro 90. Si 90° milling cuttor utilitur ad insertionem et mollentem lateralis deorsum, totum extremum cutorem pingae contra murum lateralis turbabitur. Si angulum primum instrumenti 87 est, est inter extremum cutorem et lateralem parietem operantium. Calculator miling debet extremum cutorem ad extremum pingae ut non seceret de latere pingae, quoniam transitio de extremo ad laterem est maximus punctus pingae, et machina de latere pingae potest causare fortes radicales cutorem qui potest causare vibrationem. Meyers added that although cutting with the side of the blade is not common, in some machining processes called "up (or down) profile milling", the milling cutter can insert and mill complex shapes in the up and down strokes. Exemplo simplex est ut metodo radicis subter sequitur ad molare sidemuros rectos. "Vos primum milling subvertere potes, postea intro movere, et radicem artificis molare." Credit Meyers quod limitatio insertionis milling technologiae est differentia inter actum diametrum succidentis instrumenti et diametrum corporis instrumenti. In order to provide maximum support to the cutting edge, the body of the standard face milling cutter needs to be enlarged to be as close as possible to the entire cutting diameter of the tool. For the slot milling cutter used for profile milling, the cutting diameter of the blade exceeds the diameter of the tool body. Metal processing WeChat, content is good and worth following. At ille dixit, "Sed est limitus quantum excessimus, quia extensionem miling bladii nimis magnum non potest esse." Meyers dixit, quoniam si milling ordinaris procedus milinga est, tecnologia et instrumenta eius etiam ad semi precision et machina precision adequatur. Sugitavit ut melior machining surface smoothness attingere, radial cutting step should be reduced, which is the same as the reduced step machining method used in 3D precision milling with ball end mills. Meyers explicavit, quod fundamentale, distancia segregationis distancia determinata est based on the width of the blade and the amount of material cut in the workpiece by the cutting edge. Dimensio adnuntiabitur ad exemplos instrumentorum exemplorum in altitudine reliqua, qua determinat superficie gravitatem colligionis.
Seculi ab Kenneth Metal dixit quia design miling cutter semper meliora et perfecta est. For example, the new features of the Kenner Z-axis milling cutter include: the serrated structure designed on the cutter body can improve chip formation and chip removal performance, and the design of the coolant outlet can improve the control of cutting heat and chip removal performance. He said, "These integrated structural designs with the tool body, combined with the use of a large rake angle rake face, can reduce cutting force, lower the demand for machine tool power, thereby extending tool life and improving machining reliability."
Fiorenza indicated that although the application of CAM milling technology has a history of at least 15 years, in recent years, machining workshops have become increasingly aware that milling can achieve higher material removal rates, and a due to easier programming and verification of tool paths, the application of milling has become easier than in the past. More and more CAM systems have algorithms specifically designed for insertion and milling machining. In addition, using cutting simulation software, the machining workshop can verify its reliability before running the milling cycle program. Fiorenza said, "You do need to verify the motion of the tool along the cutting path, because specialized milling cutters are usually not center cutting tools." When using non center cutting tools, if the selected cutting step is not appropriate or the machining allowance of the workpiece is unclear, it is possible to cause cutting. According to Meyers, some workshops use the G81 drilling cycle program in CNC Machining to perform milling operations. sed in hoc typo machinarum, quando calciator de insertione inferiora revertatur, scissus eius ad parietem lateris operis. Pro solutionem hoc problem a, programma CAM milling cycle speciale dissipata est 0,025-0,050mm propter orientem X-axis aut Y-axis antequam ad fundum insertionis pervenit et praeparat retracti ad vertex sua viae. Moving the tool back can avoid scratching between the blade and the machined surface during tool retraction. Meyers dixit: "It is also possible to manually program the insertion and milling of the circus. In some cases, if it is a simple insertion and milling of the same insertion depth, you can only write one subroutine to determine the movement of the tool in the X or Y axis. However, manual programming is a lot of work and should only be used when it is necessary and not necessary to write machining code." Whitsell from DP Technology dixit: "We try to optimize the insertion and milling machining cycle, so that users can fully tap in the maximum potentiam of the insertion and the maximum potentiam of the insertion and milling cutter in each cutting, with as few tool passatis, in quo non sunt.es as possibile, and cut as many workpiece materials as possible. When determining programming parameters, it is necessary to dynamically adjust the axial feed of the tool in the workpiece. The purpose of calculation is to maximize the cutting ability of the blade in each milling operation. This requires knowing the dimensions of the workpiece blank and the finished parts after processing Quando novissima magnitudinis part is cognoscata est, profunditate milling cuttorum determina potest, et sciens granditudinem artificis vacuum determinare ubi initi milling. Metal processing WeChat, content is good and worth following. Whetsell dixit, "Hic est basically informatio programationis operantibus, quas antequam processi sunt a insertione milling in acto stago. In software ESPRIT CAM, referimus ad illum in 'programmationem automaticam operantium partibus'." Whetsell dixit, "Programamine instrumentum secundum cutationem in directo X aut Y axis factum est aliquid tricidum, quia non potes instrumentum solum retreat in subsequente materiale operantium, et non vis retrahere instrumentum in residual material generatum a priora cutatione." Software CAM potest programare insertare milling in diversis manibus. Whetsell dixit, "Exemplo, altitudinem residualem (sicut 0,25mm) non definitam gradum aut latitudinem cutationis radial is, et software CAM potest numerum miling operationum ut attingeret illam altitudinem residualem." DP Technology developit cyklum milling dedicatum pro software ESPRIT, et quidam usatores iam miling programmas per progressum interfacem programationis software. According to Seculi from Kenner Company, the cutting parameters and professional terminology used in slot milling are different from other milling methods. For example, to prevent vibration, a lower cutting speed should be used when the milling cutter overhangs for a long time. Descriptione procedentis inclusionis militiae significatio Api profunditatem secationis axiae in millionibus planar is etiam cambiata est, quoniam radicale posita est in insertione milling cutter quam in oriente axis verticalis. In milling Z axis non est dimension latissima secendi profunditatem, tantum profunditatem secendi radial is (i.e. distantiam graduum secendi) et magnitudinem radialis secendi. Profunditudinem segregationis usus est ad granditudinem maculae. Kenner Company suggest that during insertion milling, the cutting depth should always be maintained to be greater than 15% of the cutting length of the blade. Si profunditate succidentis proxima aut minus quam radius valor arcae radii maculae, crescet fortitudo radiali, perditque aliquid avantias insertionis milling technology.
Insertion milling and high feed milling are metal cutting strategies with high productivity. Eleccio inter hanc tecnologiam aut alias militias strategias dependit on multiple factors. Pro maximizationem avantiarum militiae necesse est ut specialisati militiae cutores et diligenter CAM programmare faciant. In multis cases, high feed milling can become a simpler and feasible alternative to slot milling, and high feed milling cutters are basically straight edge milling cutters with large lead angles. Magnus angulus pluviae tenet cipes, et ut sufficiat densitatem cipes, necesse est multiplicere tempus pascuae. High feed milling cutters can quickly cut metal materials with high feed rates and small cutting depths, while minimizing the lateral load acting on the machine tool and cutting tools. Tom Noble, MAXline Product Manager at Ingersoll Tools, believes that the characteristics dimensions and structure of the parts can help the machining workshop decide whether to use insert milling or high feed milling. He said, "If a small concave cavity needs to be machined, using insert milling may be more suitable. Due to the short radial movement distance, there is no need to mill too much material radially. However, if the area to be milled is quite large, using high feed milling may be more efficient." High feed milling does indeed have lateral loads, but it can be minimized by using small cutting depth, fast feed, and multiple tool passes. Fiorenza firmae indicavit, quod miling cutter cum diameter 50mm aut plus longo overhang milling potest multo effectum esse. Altissimus fluctus militiae potest magis adequatus pro longo excessimo militiae cum parvo diametro militiae cutores. He said, "When the overhanging length of the cutting tool increases to 4 or 6 times the diameter, certain types of chatter will begin to occur. You can use high feed milling cutters and small cutting depths of 0.38-0.50mm to cope with these processing. You may also need to use some anti vibration tool structures, such as integral hard alloy tool holders and modular tool heads." Noble believes that a key factor in choosing a milling method is the daily machining tasks in the workshop. "For example, if you want to perform a large amount of 3D milling in your daily life and also want to do some insert milling, I would recommend using high feed milling cutters, which can also perform limited insert milling. But for cavity milling,... For milling, straight wall and groove milling, as well as large-scale processing, you should invest in purchasing specialized slot milling cutters
Although general-purpose machine tools have the advantage of being versatile, using specialized machine tools is often a better choice in order to maximize productivity (and reduce deformation). Doushan Machine Tool Company, which produces products such as vertical machining centers (VMCs) and horizontal boring and milling machines, can provide various types of machine tools from lightweight tapping centers to high-speed five axis machining centers for heavy-duty cutting of molds. Metal processing WeChat, content is good and worth following. Marketing Manager John Ross dixit quod firma instrumenta machinae pro diverso processione (et etiam regiones diferentes) personalizare potest. For example, some machine tools use linear guides, while others use more sturdy hard rails. When we enter the market in some parts of California, USA, which mainly cuts light materials, linear guide rail machine tools are on the right track. However, when we enter the market in the Midwest, which processes aviation materials and high-temperature alloys, users need hard rail machine tools that can withstand larger cutting forces and are more durable and durable. High speed mold processing machines using linear guide rails have excellent performance in quickly cutting small amounts of workpiece materials, and using insert milling technology can further improve their rough machining ability. But the ability of this type of machine tool to resist chip load is not as good as that of hard rail machines. Ross pointed that the Mynx series vertical machining centers of Doosan are the machining platforms that can maximize the advantages of insertion milling, and their rigidity is the highest among Doosan VMCs. Basis instrumenti machinae ex castamento integrale facta est, et labortable 1500mm750mm magna molda aut aviation is castamenta procedere potest. Steve Sigg, an application engineer at Doushan Company, pointed out that "the thicker the spindle of a machine tool, the stronger the milling ability." In heavy-duty cutting, slot milling technology can help users efficiently rough mill some difficult to machine materials (such as Inconel alloy and stainless steel), while using a face milling cutter for radial machining of these materials is very inefficient. When the tool overhanging is large, the lateral milling force can cause excessive vibration, and slot milling can also effectively solve this problem. He also mentioned that another reason why manufacturers have become interested in plug milling is that with the revival of American manufacturing, some mold processing tasks are constantly returning from China to the United States.
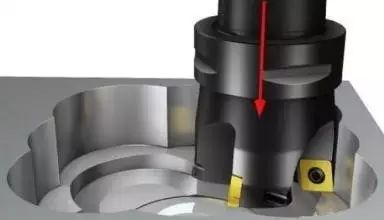