Dalam sekejap mata, saya telah beroperasi laphe CNC selama sepuluh tahun dan telah mengumpulkan beberapa kemahiran mesin dan pengalaman dalam lapis CNC. Sebab penggantian biasa bahagian mesin dan keadaan kilang terbatas, kami telah memprogram, memeriksa alat, menyahpepijat, dan menyelesaikan mesin bahagian kita sendiri selama dekad terakhir. dalam ringkasan, kemahiran operasi kita boleh dibahagi ke titik berikut. (Penulis/Li Neng)
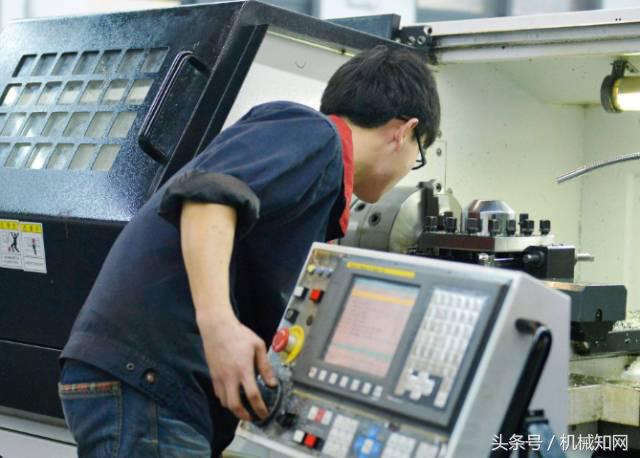
1[UNK] Kemampuan pemrograman: Kerana keperluan ketepatan tinggi kilang kita untuk produk diproses, faktor berikut perlu dianggap apabila pemrograman:
1. Proses urutan bahagian:
Latihan dahulu dan lepaskan hujung (ini untuk mencegah pengurangan bahan semasa latihan);
Pertama kereta kasar, kemudian kereta yang baik (ini untuk memastikan keperluan bahagian);
Pertama proses yang mempunyai toleransi yang lebih besar, dan kemudian proses yang mempunyai toleransi yang lebih kecil (ini memastikan permukaan saiz toleransi yang kecil tidak dicakar dan mencegah deformasi bahagian).
2. Pilih kelajuan yang masuk akal, kadar sumber, dan kedalaman potongan berdasarkan kesukaran bahan:
1) Pilih bahan besi karbon dengan kelajuan tinggi, kadar sumber tinggi, dan kedalaman potongan besar. Contohnya: 1Gr11, pilih S1600, F0.2, dan kedalaman potongan 2mm;
2) Pilih kelajuan rendah, kadar sumber rendah, dan kedalaman potongan kecil untuk ikatan keras. Contohnya: GH4033, pilih S800, F0.08, dan kedalaman potongan 0.5 mm;
3) Liu titanium patut dipilih dengan kelajuan rendah, kadar sumber tinggi, dan kedalaman potongan kecil. Contohnya, untuk Ti6, pilih S400, F0.2, dan kedalaman potongan 0.3 mm. Mengambil pemprosesan bahagian tertentu sebagai contoh: bahan adalah K414, bahan yang sangat sukar. Selepas ujian berbilang, ia akhirnya dipilih sebagai S360, F0. 1, dan kedalaman potongan 0. 2 untuk menghasilkan bahagian yang berkualifikasi.
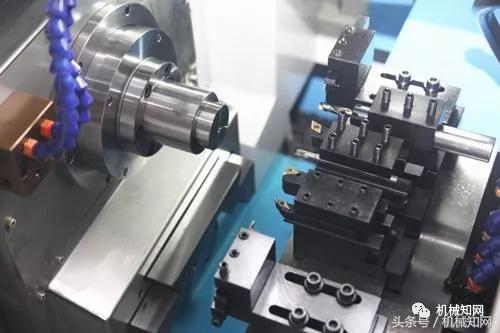
2[UNK] Teknik penyesuaian pisau dibahagi menjadi alat penyesuaian pisau dan penyesuaian pisau langsung. Kebanyakan kunci di kilang kita tidak mempunyai peranti penyesuaian alat dan memerlukan penyesuaian alat langsung. Teknik penyesuaian alat berikut rujuk kepada penyesuaian alat langsung.
Pertama, pilih tengah muka hujung kanan bahagian sebagai titik penyesuaian alat dan tetapkannya sebagai titik sifar. Selepas alat mesin kembali ke asal, setiap alat yang perlu digunakan disesuaikan dengan tengah muka hujung kanan bahagian sebagai titik sifar; Apabila alat masuk ke dalam kenalan dengan muka hujung kanan, input Z0 dan klik pada butang pengukuran. Nilai pembayaran alat akan secara automatik rekod nilai diukur, menunjukkan paksi Z dijajarkan dengan betul. Paksi X adalah untuk memotong ujian, dan apabila menggunakan alat untuk mengatur bulatan luar bahagian, input x20 untuk mengukur nilai bulatan luar bahagian yang dijajarkan (seperti x ialah 20mm). Klik pada butang pengukuran, dan nilai pembayaran akan secara automatik rekod nilai diukur. Pada titik ini paksi X juga dijajarkan dengan betul; Kaedah penyesuaian alat ini, walaupun alat mesin dimatikan, tidak akan mengubah nilai penyesuaian selepas kuasa menyala dan dimulakan semula. Ia sesuai untuk produksi skala besar dan jangka panjang bahagian yang sama, semasa lathe tidak perlu disesuaikan semula.
3[UNK] Kemampuan penyahpepijatan: Selepas pemrograman dan menyesuaikan alat, bahagian perlu diuji dan nyahpepijat. Untuk mencegah ralat dalam program dan penyesuaian alat, yang mungkin menyebabkan kemalangan bertentangan, kita patut buat mesin simulasi lejang kosong. Dalam sistem koordinat alat mesin, alat patut dipindahkan ke kanan dengan 2- 3 kali panjang keseluruhan bahagian; Kemudian mulakan simulasi mesinan. Selepas mesinan simulasi selesai, sahkan bahawa program dan alat penyesuaian adalah betul, dan kemudian mulakan mesinan bahagian-bahagian. Selepas bahagian pertama adalah mesinan, periksa sendiri dan sahkan bahawa ia adalah berkwalifikasi, dan kemudian cari inspektor dedikasi untuk periksanya. Hanya selepas inspektor dedikasi sahkan bahawa ia berkwalifikasi boleh penyahpepijatan selesai.
4[UNK] Selepas potongan percubaan pertama selesai, bahagian-bahagian yang diproses perlu dihasilkan massa. Namun, kualifikasi bahagian pertama tidak bermaksud bahawa seluruh batch bahagian akan kualifikasi, kerana semasa pemroses, bahan-bahan pemroses berbeza akan menyebabkan pakaian alat. Bahan-bahan pemroses lembut mempunyai lebih sedikit pakaian alat, sementara bahan-bahan pemroses keras mempunyai pakaian alat yang lebih cepat. Oleh itu, semasa pemroses, perlu melakukan pemeriksaan sering dan meningkat tepat masa atau mengurangi nilai kompensasi alat untuk memastikan kua
Mengambil sebahagian tertentu sebagai contoh, bahan pemprosesan adalah K414, dengan panjang pemprosesan keseluruhan 180mm. Sebab bahan yang sangat sukar, pakaian alat sangat cepat semasa pemprosesan. Dari titik permulaan hingga titik akhir, pelbagai pelbagai 10- 20 mm akan dijana kerana pakaian alat. Oleh itu, kita mesti menambah pelbagai pelbagai pelbagai 10- 20 mm dalam program untuk memastikan kualifikasi bahagian.
Secara singkat, prinsip asas pemprosesan adalah untuk pertama mesin kasar, menghapuskan bahan berlebihan dari bahagian kerja, dan kemudian mesin ketepatan; Vibrati patut dihindari semasa pemprosesan; Terdapat banyak sebab untuk mengelakkan getaran disebabkan deformasi panas semasa pemprosesan kertas kerja, yang mungkin disebabkan muatan berlebihan; Ia mungkin resonansi antara alat mesin dan potong kerja, atau tidak cukup ketat alat mesin, atau ia mungkin disebabkan oleh pasif alat. Kita boleh mengurangkan getaran dengan kaedah berikut:; Kurangkan kadar sumber sisi dan kedalaman mesinan, periksa sama ada penyekatan bahagian kerja selamat, meningkatkan kelajuan alat, yang boleh mengurangkan resonansi dengan mengurangkan kelajuan. Tambahan, periksa sama ada perlu untuk menggantikan alat dengan yang baru.
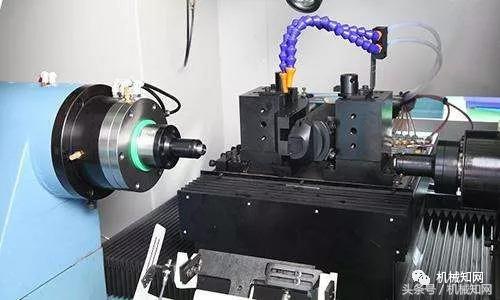
5[UNK] Pengalaman mencegah bertentangan antara alat mesin merusak kelakaran alat mesin, dan kesan berbeza untuk jenis lain alat mesin. Secara umum, ia mempunyai kesan yang lebih besar pada alat mesin dengan ketat lemah. Sehingga operator berhati-hati dan menguasai kaedah tertentu anti-raksasa, raksasa boleh dihindari dan dihindari.
Alasan utama untuk kejadian:
Satu adalah ralat input bagi diameter dan panjang alat potong;
Kedua, terdapat ralat dalam memasukkan dimensi dan dimensi geometrik lain yang berkaitan dengan bahagian kerja, serta ralat dalam posisi awal bahagian kerja;
Ketiga, sistem koordinat bahagian kerja alat mesin ditetapkan dengan salah, atau titik sifar alat mesin ditetapkan semula semasa proses mesin, yang mengakibatkan perubahan. Kolision alat mesin kebanyakan berlaku semasa pergerakan cepat alat mesin, dan bahaya dari raksasa tersebut juga yang terbesar, yang patut dihindari.
Jadi operator patut beri perhatian istimewa kepada tahap awal pelaksanaan program dan penggantian alat. Jika program disunting dengan salah atau diameter dan panjang alat dimasukkan dengan salah, kelalaian mungkin berlaku. Pada tahap akhir program, jika jujukan tindakan pulih paksi CNC tidak betul, bertentangan juga boleh berlaku.
Untuk mengelakkan kejadian yang disebut di atas, operator patut gunakan sepenuhnya fungsi ciri-ciri wajah mereka semasa mengendalikan alat mesin, perhatikan sama ada ada ada pergerakan yang tidak normal, cermin, bunyi, bunyi yang tidak normal, getaran, atau bau terbakar. Jika mana-mana situasi tidak normal ditemui, program patut dihentikan segera. Alat mesin hanya boleh terus berfungsi selepas masalah katil diselesaikan.
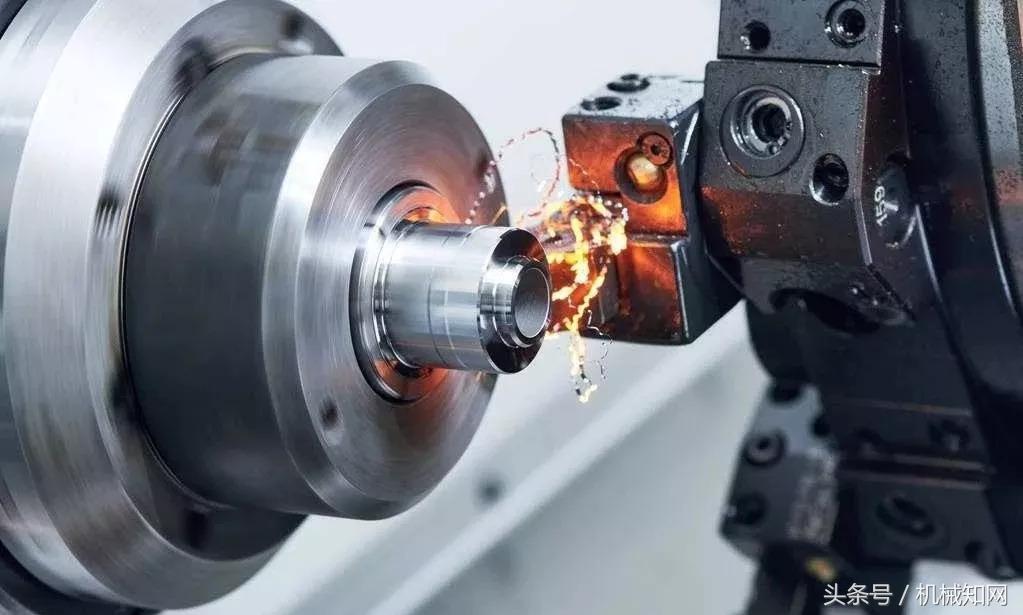
Secara singkat, menguasai kemampuan operasi alat mesin CNC adalah proses perlahan-lahan dan tidak boleh dicapai dalam semalam. Ia berdasarkan menguasai operasi dasar alat mesin, pengetahuan dasar pemprosesan mekanik, dan pengetahuan pemrograman dasar. Kemampuan operasi alat mesin CNC tidak diselesaikan, mereka memerlukan operator untuk menggunakan imajinasi dan kemampuan tangan mereka secara penuh dalam kombinasi organik, yang merupakan kerja inovatif.