Bahagian dan produk ketepatan aluminum adalah populer untuk berat ringan dan penampilan indah, dan digunakan secara luas dalam industri dan keperluan sehari-hari. Dengan kemajuan teknologi terus menerus, permintaan orang untuk pelbagai produk semakin kuat. Oleh itu, keperluan proses untuk produk selai aluminium semakin tinggi, dan permintaan pasar juga meningkat. Untuk memenuhi permintaan orang untuk kebanyakan dan kualiti tinggi produk shell aluminum legum, penghasil legum aluminum CNC telah ringkasan teknik proses dan isu yang perlu dicatat dalam mesin aluminum CNC.
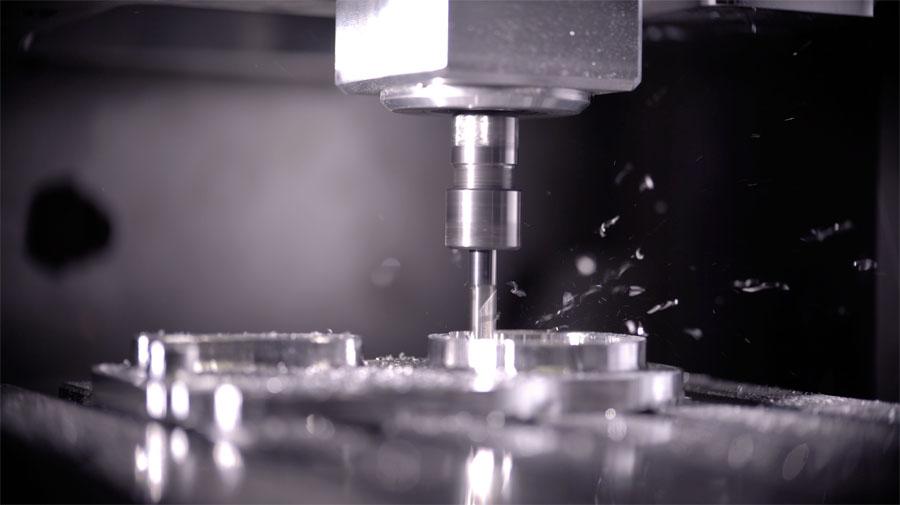
1. Pilih kaedah pemprosesan yang sesuai
Pemotongan kawalan numerik adalah kaedah pemotongan yang disegerakan dan proses yang biasa digunakan untuk mesinan ketepatan bahan aluminum. Saya menggunakan kilang akhir dengan kemampuan memotong berbilang arah, interpolasi memotong spiral, dan interpolasi memotong kontor. Proses lebih sedikit lubang dengan lebih sedikit alat.
2. Mills akhir bola boleh digunakan bersama dengan interpolasi spiral untuk proses terus-menerus lubang yang ditetapkan.
Mills akhir bola dan latihan interpolasi spiral boleh digunakan untuk membosankan dan mengganggu. Mills akhir boleh digunakan bersama dengan interpolasi potongan kontor untuk mesinan setengah ketepatan lubang dan mesinan ketepatan bahagian. Mill akhir yang digunakan untuk mesin benang boleh digunakan bersama dengan interpolasi spiral ke lubang benang berbeza mesin.
Bahagian ketepatan sidang aluminium yang efisien boleh dibuat dalam lubang ketepatan berbeza saiz menggunakan interpolasi alat. Muatan pada setiap gigi adalah relatif ringan, terutama apabila menggunakan mesin pemotong kelajuan tinggi. Oleh itu, kilang akhir legasi keras yang sama boleh digunakan untuk pengeboran kelajuan tinggi dan ketepatan tinggi berbagai bahan mesin.
3. Pilih jumlah potongan yang sesuai
Staf boleh memilih kelajuan memotong yang digunakan berdasarkan bahan yang sedang diproses, kesukaran, syarat memotong, jenis bahan, dan kedalaman memotong. Keadaan ini diperlukan untuk mengurangi pakaian mesin dan air mata.
4. Pilih alat yang sesuai.
Sudut rak: Sudut rak yang betul patut dipilih semasa mengekalkan kekuatan pinggir. Satu sisi boleh menggiling pinggir potongan tajam untuk mengurangi deformasi potongan, membuat pemindahan cip lebih lembut, dan mengurangi penentangan potongan dan panas. Jangan guna alat dengan sudut depan negatif.
Sudut belakang: Saiz sudut belakang secara langsung mempengaruhi pakaian permukaan sudut belakang dan kualiti permukaan mesin. Ketempatan potongan adalah kriteria penting untuk memilih sudut belakang. Apabila mesin kasar, kadar makan besar, muatan potong tinggi, dan generasi panas besar, jadi diperlukan bahawa alat mempunyai keadaan penyebaran panas yang baik. Oleh itu, sudut belakang yang lebih kecil perlu dipilih. Apabila mesin penentuan tepat dengan mesin pemilihan, perlu menggiling pinggir potong untuk mengurangi ketekan antara permukaan potong belakang dan permukaan mesin, dan untuk mengurangi deformasi elastik. Oleh itu, sudut belakang yang lebih besar perlu dipilih.
Sudut spiral: Sudut spiral patut dipilih sebanyak yang mungkin untuk membuat mesin pemilihan licin dan mengurangkan tekanan pada mesin pemilihan.
Sudut pendekatan: Mengurangi sudut pendekatan dengan betul boleh meningkatkan keadaan penyebaran panas secara efektif dan menurunkan suhu rata-rata kawasan rawatan.
Kurangkan bilangan gigi pembeluh dan meningkatkan ruang untuk pembuangan cip.
Kerana plasticiti tinggi bahan-bahan selai aluminium, terdapat deformasi pemotongan yang signifikan semasa pemprosesan, yang mengakibatkan ruang cip besar. Radius bawah penutup cip perlu besar, dan bilangan gigi pada pemotong pemotong perlu kecil. Contohnya, pemotong mili dengan diameter kurang dari 20 mm menggunakan 2 gigi, tetapi pemotong mili dengan diameter 30~60 mm yang terbaik dilengkapi dengan 3 gigi untuk mencegah deformasi bahagian legu aluminium tipis disebabkan blok cip.
Gigi melting halus: Nilai kasar pinggir gigi sepatutnya kurang dari Ra=0.4um. Sebelum menggunakan pisau baru, hadapan dan belakangnya seharusnya bersinar ringan dengan batu minyak halus untuk menghapuskan mana-mana burrs atau serrations ringan yang ditinggalkan di belakang semasa menggali. Dengan cara ini, tidak hanya boleh memotong panas dikurangi, tetapi memotong deformasi juga relatif kecil.
Alat kawal ketat memakai standar. Sebagai alat keluar, nilai kelabuan permukaan bahagian kerja meningkat, suhu memotong meningkat, dan deformasi bahagian kerja meningkat. Oleh itu, selain memilih bahan alat dengan perlahan pakaian yang baik, piawai pakaian tidak patut melebihi 0.2 mm. Jika tidak, mudah untuk mengembangkan tumor sampah. Apabila memotong, suhu bahagian kerja secara umum tidak sepatutnya melebihi 100 [UNK] untuk mencegah deformasi.
5. Pilih perbaikan yang masuk akal.
Bahagian mesti memenuhi keperluan mesin untuk mengurangi ralat posisi yang tidak diperlukan, dan alat tekanan istimewa patut dipilih.
6. Tentukan laluan pemprosesan yang masuk akal.
Cuba menjaga laluan pemprosesan yang singkat mungkin untuk mengurangi pakaian mesin dan air mata.
Dalam pemotongan kelajuan tinggi, pembagian mesin adalah besar dan pemotongan adalah intermittent, jadi getaran akan dijana semasa pembagian, mempengaruhi ketepatan mesin dan kasar permukaan. Oleh itu, pemotongan kelajuan tinggi CNC secara umum boleh dibahagi menjadi mesinan setengah ketepatan mesinan kasar, pembersihan sudut, mesinan ketepatan dan proses lain.
Untuk bahagian yang memerlukan ketepatan tinggi, semi selesaian sekunder mungkin diperlukan sebelum mesinan ketepatan. Selepas mesinan kasar, bahagian-bahagian secara alami dibekukan untuk menghapuskan tekanan dalaman yang dijana oleh mesinan kasar dan mengurangkan deformasi. Akaun yang tersisa selepas mesinan kasar sepatutnya lebih besar daripada jumlah deformasi (biasanya 1-2 mm). Semasa proses mesinan ketepatan, permukaan mesinan ketepatan bahagian seharusnya menjaga toleransi mesinan seragam. 0.2-0.5 mm biasanya bagus. Ini menjaga alat stabil semasa proses mesinan dan mengurangkan pencegahan pemotongan secara signifikan. Mendapatkan kualiti pemprosesan permukaan yang baik untuk memastikan ketepatan produk.