실제 생산에서 금속 스탬핑 부품은 주름, 쌓기, 목 수축, 스프링백, 고르지 못한 트리밍, 탄, 파쇄 및 슬립 라인 등 다양한 단점을 나타내는 경우가 많습니다. 부품 쌓기 결함으로 인해 부품이 폐기될 수 있습니다. 쌓기 영역의 제품 기능 계획으로 인해 스탬핑 중에 재료가 간단하게 축적됩니다. 재료 활동이 원활하지 않으면 쌓기 문제가 발생합니다.
다이 블랭크 홀더 힘으로 인한 플레이트 적층이 너무 작고, 시트 재료 활동의 도면 과정이 너무 빠르며, 시트의 크기가 너무 짧으며, 적층 재료의 원인이 되는 기타 요인은 금속 스탬핑 부품의 품질에 영향을 미칠 뿐만 아니라 생산 및 가공에도 제약을 가합니다. 동시에 금형에 특정 손상을 입혀 금형의 사용 수명을 단축시킵니다. 따라서 적층 재료의 원인을 분석한 후 자세히 처리할 필요가 있습니다.
1. 공작기계 마스터 실린더와 블랭크 홀더 힘이 좋지 않고 성형 압력이 너무 낮으며 CAE 기준 압력 값에 도달하지 않습니다. 성형 압력 처리를 조정할 필요가 있습니다.
2. 시트의 크기가 너무 짧고, 성형 중 재료 활동이 너무 빠르며, 도면 늑골은 효과가 없습니다. 처리 방법은 재료의 크기를 늘려야 합니다. 000 @ 000 3. 프레스 표면이 제자리에 없고, 내부 링이 너무 느슨하고, 외부 링이 너무 빡빡합니다. 프레스 표면의 내부 링을 압축하기 위해 프레스 표면을 다시 접지해야 하며, 연구 속도를 높이기 위해 표면을 다시 접지해야 합니다.
4. 도면 늑골의 높이가 너무 낮고 판금 성형 과정에서 도면 늑골의 효과가 없어 재료 활동이 너무 빠릅니다. 디버깅을 위해 용접을 수리하고 도면 늑골을 늘려야 합니다.
5. 공정 설계가 불합리하고 CAE 이론 분석 과정에서 적층 경향이 있으며 조치가 취해지지 않아 적층 생산이 심하고 처리 방법이 금형 프로필의 공정 모양을 변경합니다.
6. 다이 이젝터 로드의 높이가 일정하지 않고, 빈 홀더 링의 접촉 블록이 고르지 않으며, 다시 스탬핑하는 과정에서 빈 홀더 링의 손이 고르지 않으면 플레이트가 구겨지고 쌓입니다. 다이를 설치하기 전에 매우 일관된 이젝터 로드를 사용하면 금속 스탬핑 부품이 구겨지고 쌓이는 것을 방지할 수 있습니다.
이 기사는 EMAR Mold Co., Ltd.의 기사입니다. 자세한 EMAR 관련 정보는 다음을 클릭하십시오www.sjt-ic.com,
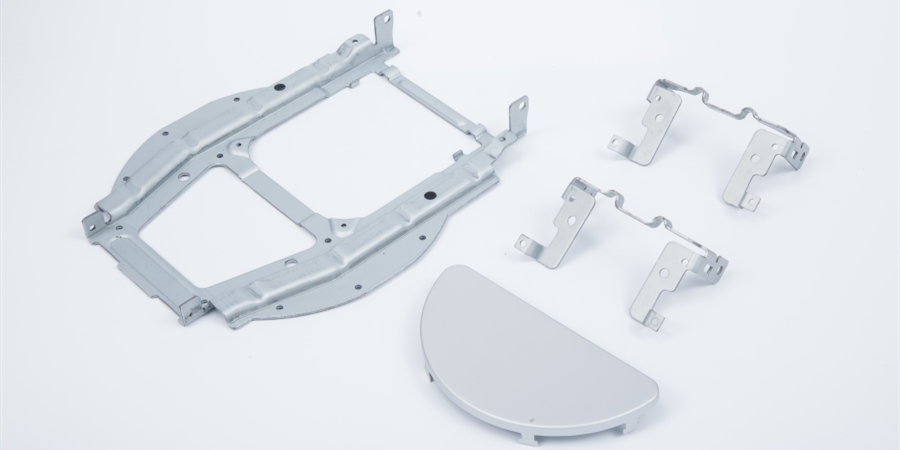