Shenzhen EMAR Precision Technology Co., Ltd. hija manifattur magħruf sew li jispeċjalizza fl-ipproċessar estern ta’ għodod tal-magni CNC ta’ preċiżjoni għolja. Għandu aktar minn 100 tip ta’ tagħmir tal-makkinarju CNC ta’ preċiżjoni. Illum, a ħna nħarsu lejn il-gwida tal-proċess ta’ tħaddim għall-manifatturi tal-makkinarju CNC. Dan huwa ta’ benefiċċju kbir għall-istandardizzazzjoni tal-proċess ta’ tħaddim u l-manutenzjoni tal-għodod tal-magni CNC minn persunal tekniku, inkluż is-sigurtà tal-produzzjoni, l-ista

1[UNK] Wara li l-għodda tal-magna tkun imħaddma, għandhom jittieħdu l-prekawzjonijiet li ġejjin:
1. Wara li l-għodda tal-magna tkun attivata, għandha l-ewwel tiċċekkja jekk is-swiċċijiet u l-buttuni kollha humiex normali u flessibbli, jekk hemmx sitwazzjonijiet anormali jew storbji anormali fl-għodda tal-magna;
2. Iċċekkja jekk il-vultaġġ, il-pressjoni taż-żejt u l-kejl tal-pressjoni tal-arja humiex f’kundizzjoni normali. Jekk ikun hemm partijiet lubrikati manwalment, għandha ssir l-ewwel lubrikazzjoni manwali;
3. Wara li l-għodda tal-magna tkun mixgħula, kull koordinata għandha tiġi rritornata manwalment għall-punt ta’ referenza. Jekk assi jkun diġà fil-pożizzjoni żero qabel ma jerġa’ lura għall-punt ta’ referenza, għandha titmexxa għal pożizzjoni 100 mm ’il bogħod mill-oriġini qabel ma jerġa’ lura manwalment għall-punt ta’ referenza. F’din il-pożizzjoni, l-għodda tal-magna għandha tkun ikkontrollata biex tiċċaqlaq fid-direzzjoni negattiva tal-linja biex terġa’ lura għall-punt ta
4. Meta jsir skambju ta’ rotazzjoni fuq il-mejda tax-xogħol, jiżgura li ma jkun hemm l-ebda fdal fuq il-mejda, kopertura protettiva, jew ferrovija gwida;
5. Wara li jiddaħħal il-programm NC, għandu jkun ipproqrat bir-reqqa u żgurat li jkun ħieles mill-iżbalji, inklużi struzzjonijiet, kodiċijiet, valuri, indirizzi, punti deċimali, sinjali u kontrolli tas-sintaks;
6. Jinstallaw it-twaħħil skont ir-rekwiżiti fl-ispeċifikazzjonijiet tal-proċess;
7. tkejjel u jikkalkula b’mod preċiż is-sistema ta’ koordinati tal-biċċa tax-xogħol, u jivverifika u jivverifika r-riżultati miksuba;
8. Daħħal is-sistema tal-koordinati tal-biċċa tax-xogħol fil-paġna tal-offset u ċċekkja bir-reqqa l-koordinati, il-valuri tal-koordinati, is-sinjali u l-punti deċimali;
9. Wara li tiddaħħal il-paġna ta’ kumpens għall-valuri ta’ kumpens tal-għodda bħat-tul u r-raġġ, jeħtieġ li jiġi ċċekkjat u vverifikat bir-reqqa n-numru ta’ kumpens tal-għodda, il-valur ta’ kumpens, il-punt deċimali, sinjali pożittivi u negattivi, eċċ;
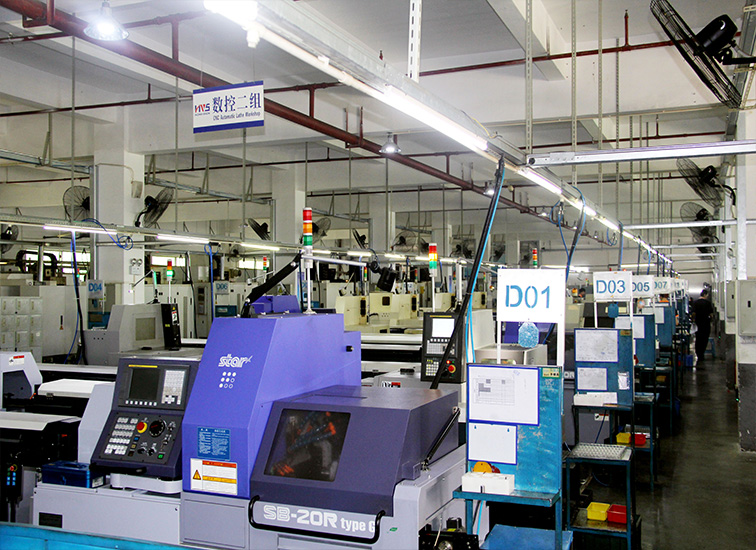
2[UNK] Matul l-ipproċessar tal-biċċiet tax-xogħol, għandhom jittieħdu l-prekawzjonijiet li ġejjin:
1. Meta jsir ipproċessar ta’ formazzjoni ta’ biċċa tax-xogħol ta’ preċiżjoni għolja, għandu jintuża mikrometru biex jinstab l-għodda fuq l-ispindula, sabiex l-iskadenza statika tagħha tkun ikkontrollata fi ħdan 3um. Jekk ikun meħtieġ, is-sistema li żżomm l-għodda trid tiġi installati mill-ġdid jew sostitwita;
2. Jekk tkun parti li tkun qed tiġi pproċessata għall-ewwel darba jew parti li tkun qed tiġi pproċessata ripetutament perjodikament, jeħtieġ li kull għodda u programm finali jiġu ċċekkjati u vverifikati skont ir-rekwiżiti tal-proċess, il-programm u l-karta ta’ a ġġustament tal-għodda fuq id-disinn qabel l-ipproċessar. Speċjalment għall-partijiet fejn il-kumpens tat-tul tal-għodda u l-kumpens tan-nofs dijametru huma inklużi fil-programm, il-qtugħ tal-prova għandu
3. Meta jsir qtugħ ta’ prova b’segment wieħed, is-swiċċ tal-multiplikatur tal-metall għandu jiġi ssettjat fuq ger aktar baxx, pereżempju;
4. Meta tintuża għall-ewwel darba, jeħtieġ li jiġi vverifikat jekk it-tul attwali tiegħu jaqbilx mal-valur ta’ kumpens mogħti;
5. Waqt l-eżekuzzjoni tal-programm, huwa importanti li tiffoka fuq l-osservazzjoni tal-kontenut tal-wiri fuq is-sistema CNC;
6. Displej tal-koordinati, li jista’ jifhem il-pożizzjoni attwali tal-pad tal-moviment tal-għodda fis-sistema tal-koordinati tal-magna u s-sistema tal-koordinati tal-biċċa tax-xogħol, jifhem l-ammont ta’ moviment f’din it-taqsima tal-programm, u kemm jifdal il-moviment disponibbli;
7. L-wiri tar-reġistri u tar-reġistri ta’ riżerva jippermettik li tara l-istatus tas-segment tal-programm ta’ eżekuzzjoni u wkoll il-kontenut tas-segment tal-programm li jmiss;
8. L-wiri tal-programm ewlieni u s-subroutines jistgħu jiżvelaw il-kontenut speċifiku tas-segment tal-programm ta’ eżekuzzjoni;
9. Skrin tal-wiri tad-djalogu, li jista’ jifhem il-veloċità kurrenti tat-tħaddim tal-għodda tal-magna, l-għalf kurrenti tat-tqattigħ tal-għaġla għal kull rivoluzzjoni, ir-rata kurrenti tat-tqattigħ tal-għalf, it-tagħbija kurrenti tat-tqattigħ tal-għaġla, u t-tagħbija tal-assi tal-mogħdija. L-għalf tat-tqattigħ tal-għaġla
10. Matul il-proċess ta’ qtugħ tal-prova, meta l-għodda tilħaq fond ta’ 30 sa 50 mm fuq il-wiċċ intern tal-biċċa tax-xogħol, għandu jiġi vverifikat li l-valuri tal-koordinati li jifdal tal-assi tal-koordinati huma konsistenti mal-valuri tal-koordinati tal-assi X u Y u l-immaġni filwaqt li tinżamm rata baxxa ta’ alimentazzjoni;
11. Għal xi għodod speċjali ta’ qtugħ li jeħtieġu qtugħ tal-prova, jiġi adottat approċċ progressiv biex jippermetti li d-dejta tal-funzjoni ta’ kumpens tar-raġġ tal-għodda tiġi a ġġustata minn kbira għal żgħira, b’kull qtugħ u modifika tal-prova;
12. Matul il-proċess tal-qtugħ u l-makkinarju tal-prova, wara li l-għodda u l-għodod awżiljarji jiġu sostitwiti, jeħtieġ li t-tul tal-għodda jerġa’ jitkejjel u jiġi modifikat il-valur tal-kumpens tal-għodda u n-numru tal-kumpens tal-għodda;
13. Meta jiġu rkuprati programmi, għandha tingħata attenzjoni jekk il-pożizzjoni indikata mill-kursur hijiex raġonevoli u preċiża, u jekk il-koordinati tad-direzzjoni tal-moviment tal-għodda u tal-għodda tal-magna humiex korretti għandhom jiġu osservati;
14. Wara l-modifika tal-programm, jeħtieġ li jiġu kkalkulati u vverifikati bir-reqqa l-partijiet modifikati;
15. Meta jkun qed jitħaddem l-għalf manwali u l-għalf manwali kontinwu, jeħtieġ li jiġi vverifikat jekk il-pożizzjonijiet magħżula ta’ diversi swiċċijiet humiex korretti, jiġu ċċarati d-direzzjonijiet pożittivi u negattivi, jiġu identifikati l-buttuni u r-rata tal-veloċit à u l-impuls tal-għalf issettjati, u mbagħad isir it-tħaddim;
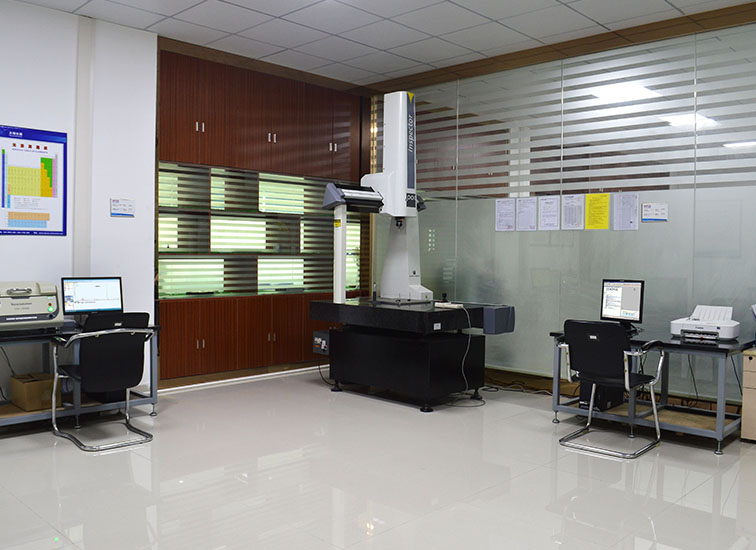
3[UNK] Wara li l-partijiet jiġu pproċessati, għandhom jittieħdu l-prekawzjonijiet li ġejjin:
1. Wara li l-lott kollu tal-partijiet jiġi pproċessat, in-numru tal-għodda u l-valur tal-kumpens tal-għodda għandhom jiġu ċċekkjati sabiex jiġi żgurat li l-valur tal-kumpens tal-għodda u n-numru tal-għodda fil-programm, il-paġna offset, il-karta tal-aġġustament, u l-karta tal-proċess ikunu eżattament l-istess. Meta l-għodda tiġi użata mill-ġdid, għandha tiġi allinjata mill-ġdid fuq il-predefinitur tal
2. Iċċarġja l-għodod mill-librerija tal-għodod, naddaf u nnumerahom skont il-kard jew il-programm ta’ a ġġustament, u taħżen id-diski, l-għodod u l-kards tal-ipproċessar bħala sett;
3. Wara li jinħattu l-fittings, xi fittings għandhom jiġu rreġistrati għall-pożizzjoni u l-orjentazzjoni tal-installazzjoni tagħhom, u wara r-reġistrazzjoni, għandhom jiġu arkivjati;
4. Waqqaf kull assi ta’ koordinati fil-pożizzjoni tan-nofs;
5. Jekk għandek bżonn tagħlaq f’dan il-ħin, tista’ tagħfas il-buttuna ta’ skonnettjar tal-enerġija fuq il-pannell tal-operazzjoni, u mbagħad stenna għal mument biex tippermetti li ż-żejt tat-tkessiħ tal-ispindula fl-ispindula jgħaddi parzjalment lura qabel ma tintefa’ awtomatikament;
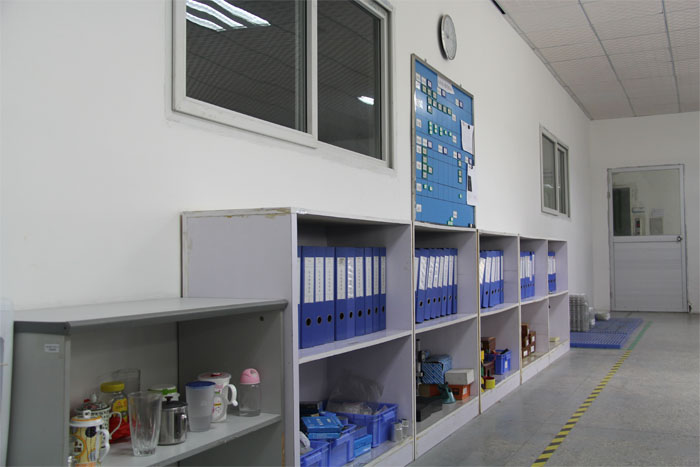
Dan ta’ hawn fuq huwa spjegazzjoni dettaljata tal-manwal tal-proċess ta’ tħaddim għall-manifatturi tal-makkinarju CNC. Nittamaw li dan jista’ jkun ta’ għajnuna għalik. Familjarizza ruħek mal-manwal tal-operazzjoni u tmexxi l-manwal tal-operazzjoni, u segwih strettament biex tiżgura s-sigurtà manwali tal-operaturi tal-makkinarju, kif ukoll il-kwalità tal-ipproċessar tal-prodott u l-ħajja tas-servizz tal-għodod tal-makkinarju. Għalhekk, huwa meħtieġ