Aluminium precisie onderdelen en producten zijn populair om hun lichtgewicht en prachtige verschijning, en worden veel gebruikt in de industrie en dagelijkse behoeften. Met de voortdurende vooruitgang van technologie wordt de vraag van mensen naar productdiversiteit steeds sterker. Daarom worden de procesvereisten voor aluminiumlegeringsproducten steeds hoger, en de marktvraag neemt ook toe. Om te voldoen aan de vraag van mensen naar diversiteit en hoge kwaliteit van aluminiumlegering shell producten, hebben aluminiumlegering CNC bewerkingsfabrikanten de procestechnieken en problemen samengevat die moeten worden opgemerkt bij aluminium CNC bewerking.
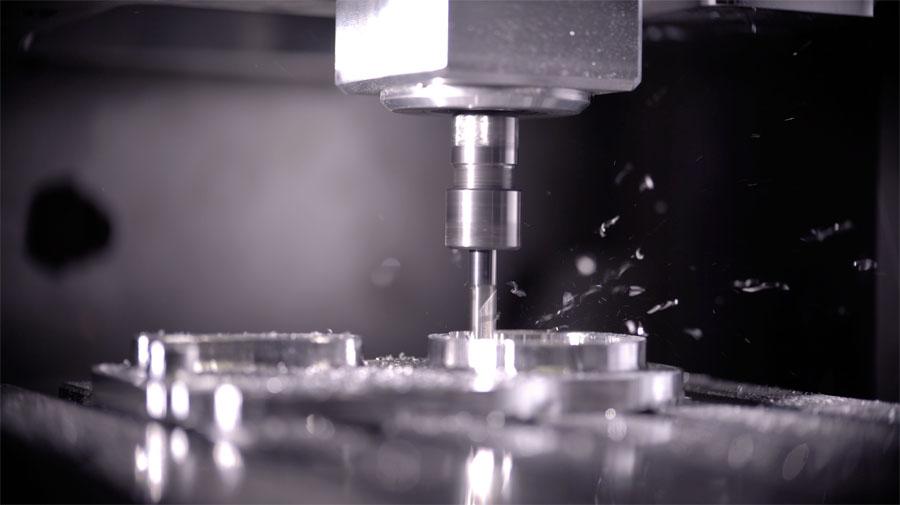
1. Kies de juiste verwerkingsmethode
Numerieke controle snijden is een gestroomlijnde snijmethode en een algemeen gebruikt proces voor precisiebewerking van aluminiummaterialen. Ik gebruik een eindfrees met multidirectioneel snijvermogen, spiraalsnijinterpolatie en contoursnijinterpolatie. Bewerk minder gaten met minder gereedschap.
2. Baleindmolens kunnen in combinatie met spiraalvormige interpolatie worden gebruikt om taps toelopende gaten continu te verwerken.
Voor boring en afschuining kunnen kogeleindfrezen en spiraalvormige interpolatieboren worden gebruikt. Eindfrezen kunnen worden gebruikt in combinatie met contoursnijinterpolatie voor semi-precisiebewerking van gaten en precisiebewerking van onderdelen. De eindmolen die wordt gebruikt voor draadbewerking kan in combinatie met spiraalinterpolatie worden gebruikt om verschillende draadgaten te bewerken.
Efficiënte aluminiumlegeringsprecisieonderdelen kunnen worden bewerkt in precisiegaten van verschillende grootte met behulp van gereedschapsinterpolatie. De belasting op elke tand is relatief licht, vooral bij gebruik van hogesnelheidsfreesmachines. Daarom kan dezelfde gecoate harde legering eindmolen worden gebruikt voor hoge snelheid en hoge precisie boren van verschillende bewerkingsmaterialen.
3. Kies de juiste snijhoeveelheid
Personeel kan kiezen welke snijsnelheid te gebruiken op basis van het te bewerken materiaal, hardheid, snijomstandigheden, materiaaltype en snijdiepte. Deze voorwaarden zijn noodzakelijk om machineslijtage effectief te verminderen.
4. Kies geschikte gereedschappen.
Hark hoek: De juiste hark hoek moet worden geselecteerd met behoud van de randsterkte. Één kant kan scherpe snijkanten slijpen om snijvervorming te verminderen, spaanafvoer soepeler te maken en snijweerstand en hitte te verlagen. Gebruik geen gereedschap met negatieve fronthoeken.
Achterhoek: De grootte van de achterhoek beïnvloedt direct de slijtage van het achterhoekoppervlak en de kwaliteit van het bewerkte oppervlak. De snijdikte is een belangrijk criterium voor de keuze van de achterhoek. Bij ruwe bewerking is de toevoersnelheid groot, is de snijbelasting hoog en is de warmtegeneratie groot, dus het is vereist dat het gereedschap goede warmteafvoeromstandigheden heeft. Daarom moet een kleinere achterhoek worden gekozen. Bij precisiebewerking met een freesmachine is het noodzakelijk om de snijrand te slijpen om wrijving tussen het achtersnijoppervlak en het bewerkingsoppervlak te verminderen en elastische vervorming te minimaliseren. Daarom moet een grotere achterhoek worden gekozen.
Spiraalhoek: De spiraalhoek moet zo groot mogelijk worden geselecteerd om de freesmachine glad te maken en de spanning op de freesmachine te verminderen.
Aanpak hoek: Het correct verminderen van de naderingshoek kan de warmtedissipatievoorwaarden effectief verbeteren en de gemiddelde temperatuur van het behandelingsgebied verlagen.
Verminder het aantal frezen tanden en vergroot de ruimte voor spanverwijdering.
Vanwege de hoge plasticiteit van aluminiumlegeringsmaterialen, is er significante snijvervorming tijdens de verwerking, resulterend in een grote spaanruimte De onderste straal van de spaangroef moet groot zijn, en het aantal tanden op de frees moet klein zijn. Bijvoorbeeld, frezen met een diameter van minder dan 20mm gebruiken 2-tanden, maar frezen met een diameter van 30~60mm zijn het beste uitgerust met 3-tanden om vervorming van dunne onderdelen van aluminiumlegering te voorkomen als gevolg van spanblokkade.
Fijn slijpende tanden: De ruwheidswaarde van de tandrand zou minder moeten zijn dan Ra=0.4um. Voordat u een nieuw mes gebruikt, moeten de voor- en achterkant licht gepolijst worden met een fijne oliesteen om bramen of lichte breuken te verwijderen die tijdens het slijpen achterblijven. Op deze manier kan niet alleen snijwarmte worden verminderd, maar snijvervorming is ook relatief klein.
Strikte controle over gereedschapsslijtage normen. Naarmate het gereedschap slijt, neemt de oppervlakteruwheidswaarde van het werkstuk toe, stijgt de snijtemperatuur en neemt de vervorming van het werkstuk toe. Daarom, naast het selecteren van gereedschapsmaterialen met goede slijtvastheid, moet de slijtagenorm 0.2mm niet overschrijden. Anders is het gemakkelijk om puintumoren te ontwikkelen. Bij het snijden, zou de temperatuur van het werkstuk over het algemeen 100 ℃ niet moeten overschrijden om vervorming te voorkomen.
5. Kies een redelijke inrichting.
De onderdelen moeten volledig voldoen aan de behoeften van de machine om onnodige positioneringsfouten te verminderen, en speciale spangereedschappen moeten worden geselecteerd.
6. Bepaal een redelijke verwerkingsroute.
Probeer de verwerkingsroute zo kort mogelijk te houden om machineslijtage te verminderen.
Bij het snijden met hoge snelheid is de machinale toelage groot en het snijden is intermitterend, dus trillingen zullen worden gegenereerd tijdens het frezen, die de bewerkingsnauwkeurigheid en oppervlakteruwheid beïnvloeden. Daarom kan CNC high-speed snijden over het algemeen worden onderverdeeld in ruwe bewerking semi precisiebewerking, hoekreiniging, precisiebewerking en andere processen.
Voor onderdelen die hoge precisie vereisen, kan secundaire semi-finishing nodig zijn voordat precisiebewerking plaatsvindt. Na ruwe bewerking worden de onderdelen natuurlijk gekoeld om de interne spanning die wordt gegenereerd door ruwe bewerking te elimineren en vervorming te verminderen. De resterende toelage na ruwe bewerking zou groter moeten zijn dan de vervormingshoeveelheid (gewoonlijk 1-2mm). Tijdens het precisiebewerkingsproces moet het precisiebewerkte oppervlak van het onderdeel uniforme bewerkingstoleranties handhaven. 0.2-0.5mm is meestal goed. Dit houdt het gereedschap stabiel tijdens het bewerkingsproces en vermindert snijvervorming aanzienlijk. Krijg een goede oppervlakteverwerkingskwaliteit om productnauwkeurigheid te verzekeren.