Technologie van de plaatverwerking: Volgens de basisverwerkingsmethoden van plaatmetalen delen, met inbegrip van snijden, buigen, uitrekken, vormen, en lassen. Technologie van de plaatverwerking: Volgens de basisverwerkingsmethoden van plaatmetalen delen, met inbegrip van snijden, buigen, uitrekken, vormen, en lassen.
Snijden: Snijden kan worden onderverdeeld in algemene ponsen, numerieke ponsen, knippen van de machine, lasersnijden, en wind snijden volgens verschillende verwerkingsmethoden.Vanwege verschillende verwerkingsmethoden, varieert de verwerkingstechnologie van snijden ook. De belangrijkste snijmethoden voor plaatbewerking zijn ponsen en lasersnijden. Bij het buigen van materialen wordt de buitenste laag uitgerekt terwijl de binnenste laag wordt samengeperst in het afgeronde hoekgebied. Wanneer de dikte van het materiaal constant is, hoe kleiner de binnenste r, hoe ernstiger de uitrekking en compressie van het materiaal; Wanneer de trekspanning op de buitenste filet de uiteindelijke sterkte van het materiaal overschrijdt, zullen scheuren en breuken optreden. Daarom moet het structurele ontwerp van gebogen delen overmatig kleine buigende filet radii vermijden.
Uitrekken: De filetradius tussen de bodem van het uitrekkende deel en de rechte muur moet groter zijn dan de plaatdikte, d.w.z. r1t. Om het uitrekkingsproces gladder te maken, wordt r1=(3-5) t over het algemeen genomen, en de maximale filetradius moet minder dan of gelijk zijn aan 8-maal de plaatdikte, d.w.z. r18t. De dikte van het uitgerekte materiaal zal veranderen als gevolg van de verschillende niveaus van spanning toegepast op verschillende locaties. Over het algemeen behoudt het bodemcentrum zijn oorspronkelijke graad, het materiaal bij de afgeronde hoeken van de bodem wordt dunner, het materiaal bij de flens aan de bovenkant wordt dikker en het materiaal bij de afgeronde hoeken rond het rechthoekige stretchende deel wordt dikker.
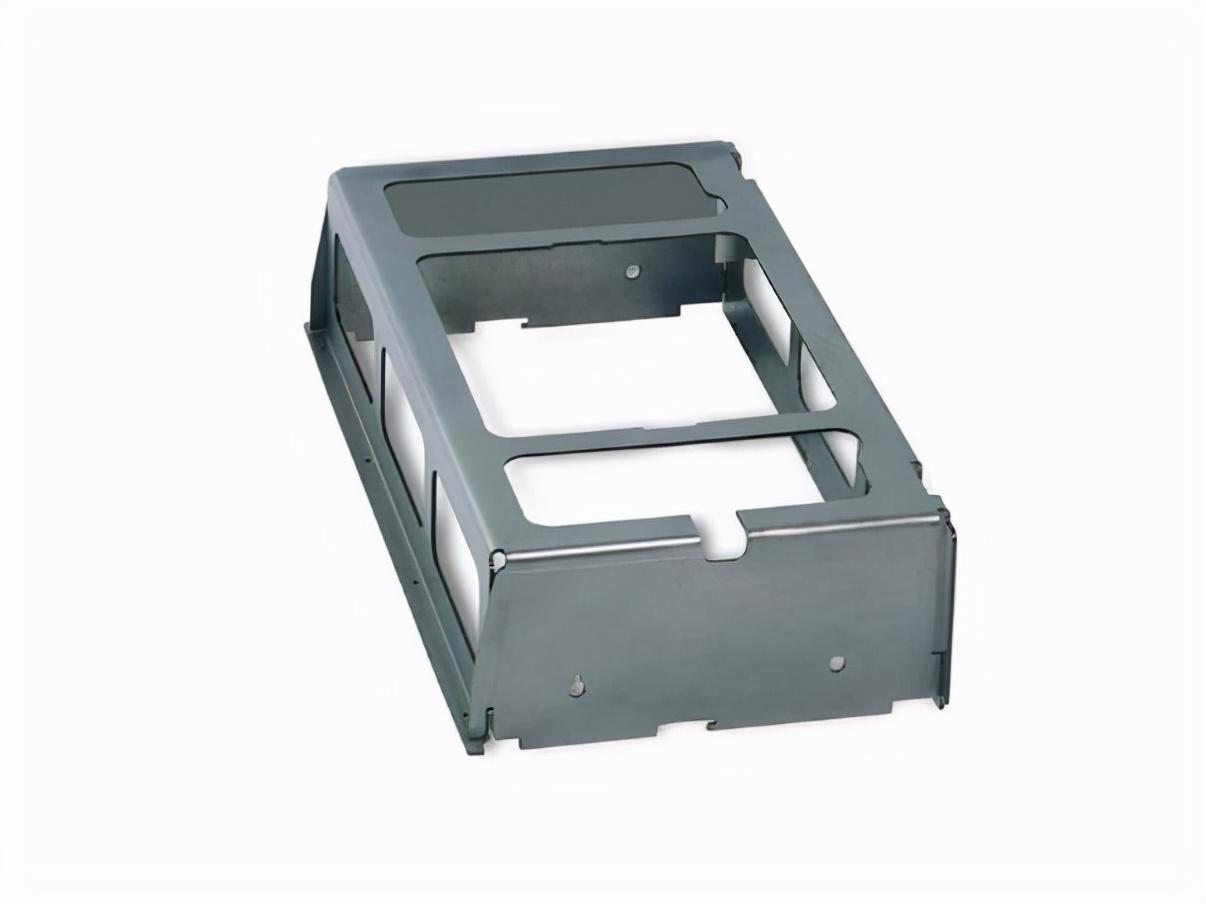
Vormen: Het drukken van ribben op plaatvormige metalen delen helpt om structurele stijfheid te verhogen.Luizers worden meestal gebruikt op verschillende afdekkingen of behuizingen voor ventilatie en warmteafvoer. De vormmethode is om het materiaal te snijden met een rand van de convexe vorm, terwijl de rest van de convexe vorm tegelijkertijd rekt en vervormt het materiaal om een golvende vorm te vormen met één rand open.
Lassen: De lasmethoden omvatten hoofdzakelijk booglassen, slakkenlassen, gaslassen, plasmabooglassen, fusielassen, druklassen en solderen.Het lassen van plaatmetaalproducten omvat hoofdzakelijk booglassen en gaslassen. Het booglassen heeft flexibiliteit, manoeuvreerbaarheid, en brede toepasbaarheid, en kan voor alle positielassen worden gebruikt; De gebruikte apparatuur heeft de voordelen van eenvoud, goede duurzaamheid en lage onderhoudskosten. Maar de arbeidsintensiteit is hoog en de kwaliteit is niet stabiel genoeg, wat afhankelijk is van het niveau van de operator. De vlamtemperatuur en eigenschappen van gaslassen voor koolstofstaal, laaggelegeerd staal, roestvrij staal en non-ferro legeringen zoals koper en aluminium die geschikt zijn voor lassen met een diameter van 3mm of meer kunnen worden aangepast. De warmtebron van het booglassen heeft een bredere hittebeïnvloede zone, en de hitte is niet zo geconcentreerd als de boog, resulterend in lage productiviteit. Het wordt gebruikt voor het lassen van dunwandige structuren en kleine onderdelen. De acceptatienormen voor gelast staal, gietijzer, aluminium en koperplaatchassis kunnen worden geïnspecteerd en geaccepteerd in de productiefabriek of de door partij A aangewezen productleveringslocatie. De resultaten moeten consistent zijn en de uiteindelijke resultaten moeten gebaseerd zijn op de eindbestemming.
Aanvaardingscriteria:
De vlakheid van de bodem en andere zijden van de doos is 1mm.
2. De verticaliteit van de voor- en achterhoogten of links en rechts van het dooslichaam ten opzichte van het bodemoppervlak is 1mm.
3. De parallelliteit tussen de boven- en bodemoppervlakken van het paneel is 0.5mm, en de loodrecht tussen de zij- en bodemoppervlakken is 0.5mm.
Nadat het paneel in de doos is geïnstalleerd, moet het verticaal en rechtop zijn, met een loodrecht van 0.5mm tussen zijn kant en de bodem van de doos, en een parallelliteit van 0.5mm tussen de bodem en de bodem van de doos.
5. Bij het installeren van het plug-in frame van de printplaat of het chassis, is het noodzakelijk om een armatuur te gebruiken om de printplaat of het chassis voor montage te simuleren Het armatuur moet soepel worden ingevoegd en verwijderd van de plug-in doos, en na in de plug-in doos te worden geplaatst, moet het veilig worden bevestigd zonder te drijven of los te maken. Hard aangesloten connectoren moeten nauwkeurig worden uitgelijnd en zonder abnormale obstructie worden geplaatst en verwijderd.