Presisjonsstyrkemetallprosessen er en prosessemetode som brukes til å produsere nøyaktige deler og komponenter, vanligvis funnet i industrier som luftrom, elektronikk, kommunikasjon, medisinsk utstyr, etc. I praktisk operasjon kan imidlertid forekomme noen problemer. Denne artikkelen vil presentere noen felles problemer og gi løsninger.
Problem 1: Dimensjonsavvik overskrider krav
I prosessen av presisjonsstyrkemetallprosessen kan dimensjonelle avvik overstige kundekontroller, noe som kan føre til at komponenter ikke virker riktig eller dårlig som passer med andre deler.
Oppløsning:
1. Forsiktig analyser og evaluerer nøyaktigheten for å sikre at det møter kravene.
2. Konsentrer simulering og tester før prosessen oppdager og korrigerer dimensjonale avvik.
3. Innenfor strengte kvalitetskontrollprosesser, inkludert virketidskontroll og tester under prosessen.
4. Jobb nøye med kunder, klarlagte størrelsekrever og justere og forbedre prosesseteknologi på en tidsnok måte.
Spørsmål 2: Material deformasjon eller ruptur
Under lakettmetallprosessen kan materialet forverre eller bryte seg, noe som fører til en reduksjon i kvaliteten av det ferdige produktet eller til og med forårsake det ubrukelig.
Oppløsning:
1. Velg passende materiale, inkludert deres hardhet, styrke, hardhet og andre egenskaper.
2. Tidligere materialebehandling, som stresselindring, bør utføres før behandlingen reduseres risikoen for deformasjon og frakturen av materialet.
3. Optimiser prosesseteknologien ved å adoptere egne metoder og sekvenser for å slå, bøye og andre prosesser for å redusere materiell stress og deformasjon.
4. Økning av moldstøtte eller justering av mold design for å øke materiell støtte og stabilitet.
5. Kondukt produksjon av studien før prosessen for å oppdage og korrigere materiell deformasjon eller knekkeproblemer.
Problem 3: Stakkars overflatekvalitet
Kravene av overflatekvaliteten for nøyaktighetshettmetall-behandlingen er høye, og dersom de nødvendige indikasjonene som flatne og rødme mislykkes å møte forventninger, vil det påvirke utseendet og performansen av produktet.
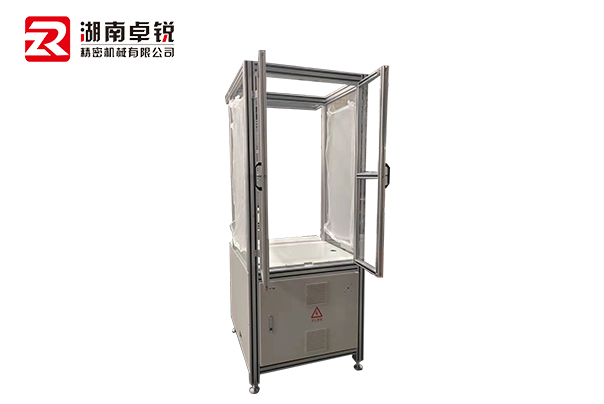
Oppløsning:
1. Velg egnet prosesseteknikk og parametre, slik som punchrensering for å slå maskiner, støttemetoder for bendingsprosesser, etc. for å sikre at overflateskader ikke for årsakes under prosessen.
2. Tidligere overflatebehandling som polishing, grinding etc. bør utføres før behandlingen forbedres overflatekvalitet.
3. Forsterk vedlikeholdet av behandlingsutstyr og kuttstyr for å sikre deres gode tilstand og unngå å kløe eller skade materiale overflaten.
4. Rens avfallsmaterier på en tidsnok måte under prosessen for å unngå forurensning eller skraping av materiale overflaten.
5. Velg egne testmetoder, slik som optiske inspeksjonsinstrumenter, laserskanning, etc. for å utføre kvalitetsforsikring på prosesserte produkter for å sikre at overflatekvaliteten møter kravene.
Problem 4: High laboratoriekostnader
Presisjon av rulleblad krever vanligvis flere prosesser, og hver prosess krever tid og arbeidskostning.
Oppløsning:
1. Gjennomsnittlig planlegging og organisering av prosedyrer og minimalisere redundante prosedyrer og gjentatte operasjoner så mye som mulig.
2. Velg avansert processing og automatisjonsutstyr for å forbedre prosessens effekt og kvalitet.
Tre. Tog og forbedre ansattes evner og styrke og enhancement av arbeidernes operative effekt.
4. Kommunisere og samarbeid med kunder for å minimalisere unødvendige behandlingskrav og redusere produktet kompleksitet.
Finn egnet leverandører og partnere til å redusere prosessekostnadene samtidig.
Gjennom de ovennevnte oppløsningene kan vanlige problemer med nøyaktighetshettmetallprosessen behandles effektivt, forbedre produktkvalitet og prosesseeffekt. Forskjellige industrier og produkter kan også ha spesifikke problemer og oppløsninger som krever målbare justeringer og forbedringer basert på virkelige situasjoner.