Wysokiej klasy obrabiarki CNC
Te sześć słów zawiera trzy warstwy koncepcji, przyjrzyjmy się bliżej każdej warstwie.
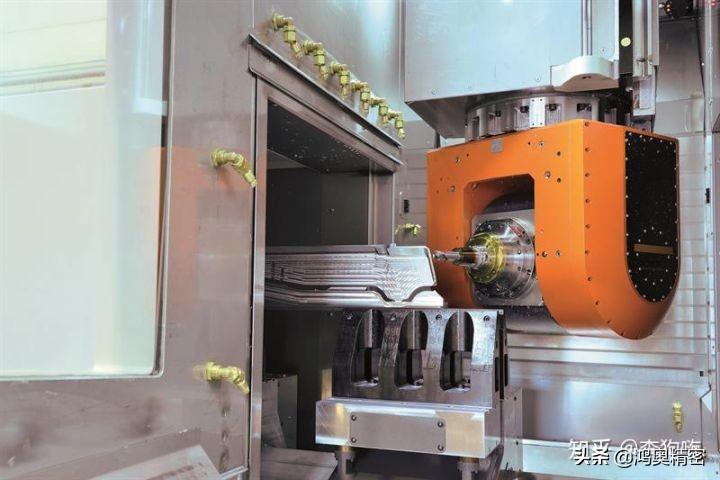
Pięcioosiowa frezarka CNC Handtmann PBZ HD
Po pierwsze, czym jest "obrabiarka"?
W wąskim znaczeniu, "obrabiarka" zwykle odnosi się do "obrabiarki cięcia" (w wąskim znaczeniu jest to dlatego, że istnieją również obrabiarki do produkcji dodatkowej, takie jak druk 3D lub inne specjalne obrabiarki), które wykorzystują metody cięcia do przetwarzania przedmiotów obrabianych na części maszyny. To znaczy, że obrabiarki są maszyny, które produkują maszyny, więc są również znane jako "maszyny robocze". W języku japońskim, są one nazywane "maszyny robocze" (くきききい), a w języku angielskim, są one nazywane "obrabiarki".
Pierwszą prawdziwą obrabiarką była właściwie wiertarka, wynaleziona przez brytyjskiego przemysłowca Johna Wilkinsona w latach 1775. Pierwotną motywacją do wynalezienia tej wiertarki było rozwiązanie praktycznego problemu produkcji precyzyjnych luf armatnych w tamtym czasie w wojsku.
Obróbka wiercenia to proces cięcia, który wykorzystuje narzędzia tnące do powiększenia średnicy wewnętrznej otworów lub innych okrągłych konturów na obracających się elementach obrabianych. Odpowiada ono toczeniu, czyli procesowi cięcia, który wykorzystuje narzędzie do zmniejszenia średnicy zewnętrznej obrabianego przedmiotu lub do kształtowania powierzchni końcowej. [2]
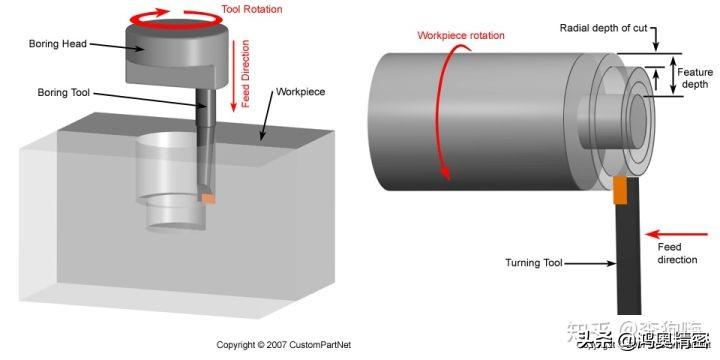
Procesy wiercenia (w lewo) i toczenia (w prawo)
47-letni Wilkinson, po ciągłych staraniach w fabryce ojca, w końcu stworzył tę nową maszynę, która potrafi produkować lufy armatne z rzadką precyzją. Zasada działania polega na obracaniu stałego wału narzędzia wiercenia przez koło wodne i pchnięciu go względem cylindrycznego przedmiotu obrabianego. Stały wał narzędzia wiercenia przechodzi przez cylindrę i jest wspierany na obu końcach. Ze względu na względne ruchy między narzędziem a przedmiotem obrabianym materiał jest wywierceny do wysoce precyzyjnego otworu cylindrycznego.
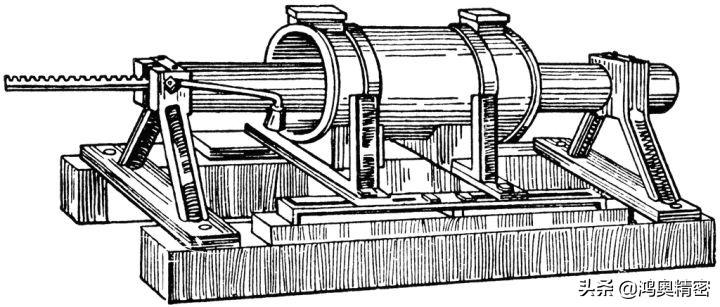
Schemat pierwszej wiertarki
A wiertarka została później używana do obróbki cylindrów silników parowych. Powodem jest to, że po wynalezieniu silnika parowego James Watt bardzo trudno było mu produkować cylindry silnika parowego za pomocą metod kucia, a ze względu na niską dokładność produkcji i poważny wyciek powietrza z cylindrów, produkcja i poprawa wydajności silnika parowego były ograniczone. [3] Po przyjęciu tej wiertarki można produkować wysoce precyzyjne cylindry ponad 50-calowe, znacznie poprawiając jakość przetwarzania i wydajność produkcji cylindrów silników parowych, a tym samym osiągając ogromny sukces.
Następnie, aby sprostać potrzebom różnych technik obróbki, pojawiły się różne rodzaje obrabiarek, takich jak tokarki, frezarki, hobarki, szlifierki, wiercerki itp. [4]
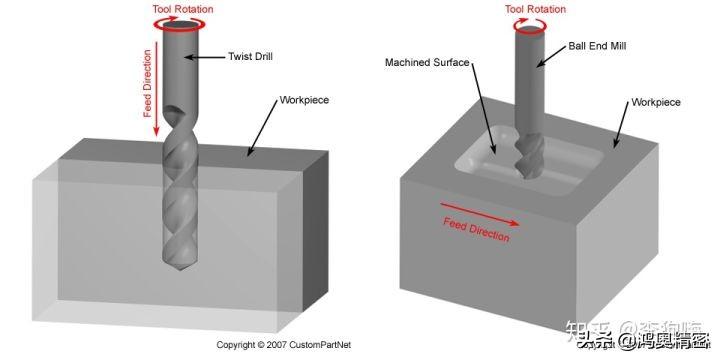
Procesy wiercenia (po lewej) i frezowania (po prawej)
Więc czym jest "obrabiarka CNC"?
Pierwszy komputer elektroniczny urodził się w lutym 14,1946 na Uniwersytecie Pensylwanii w Stanach Zjednoczonych. Początkową motywacją jego rozwoju było wyprodukowanie "elektronicznego" urządzenia obliczeniowego, które w kontekście II wojny światowej zastąpiło przekaźniki rurami elektronicznymi na żądanie wojska USA, w celu obliczenia trajektorii pocisków.
Sześć lat później, w latach 1952, Parsons współpracował z Massachusetts Institute of Technology (MIT), aby opracować pierwszą obrabiarkę sterowania numerycznego (NC), znaną również jako "obrabiarkę cyfrową") poprzez połączenie systemu sterowania numerycznego opartego na komputerach elektronicznych z frezarką z Cincinnati. Od tego czasu tradycyjne obrabiarki uległy zmianie jakościowej, oznaczając początek ery CNC dla obrabiarek. [5]
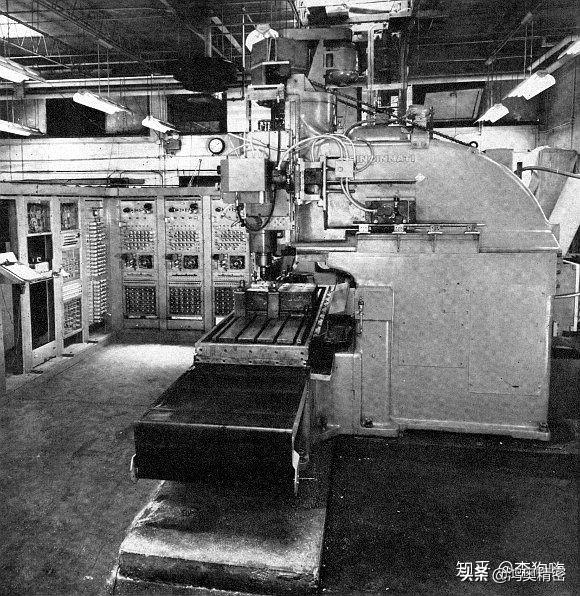
Pierwsza obrabiarka CNC (frezarka)
Sześć lat później, w latach 1958, MIT współpracowało z wieloma firmami pod sponsorem wojska USA w celu opracowania APT (Automatic Programming Tools), wysokiego poziomu języka programowania komputerowego używanego do generowania instrukcji pracy dla obrabiarek CNC. Najczęstszą metodą obecnie jest użycie instrukcji formatu RS-274, powszechnie określanych jako "kod G". [7]
Wraz z ciągłym rozwojem technologii komputerowej mikroprocesory zostały zastosowane do sterowania cyfrowego, znacznie ulepszając ich funkcje.Ten rodzaj systemu nazywa się Computer Digital Control (CNC), Computer Numerical Control), Obrabiarka, która stosuje ten system, jest również znana jako obrabiarka CNC, która jest sterowaną komputerowo obrabiarką numeryczną, lub po prostu określana jako "obrabiarka CNC".
Technologia sterowania numerycznego w obrabiarkach CNC to metoda techniczna, która wykorzystuje sygnały cyfrowe do sterowania ruchem i procesem obróbki obrabiarki. Obrabiarka CNC to obrabiarka, która wykorzystuje technologię CNC lub jest wyposażona w system CNC. Piąty Komitet Techniczny Międzynarodowej Federacji Przetwarzania Informacji (IFIP) definiuje obrabiarkę CNC jako obrabiarkę wyposażoną w system sterowania programem. Ten system sterowania może logicznie przetwarzać programy z kodami sterującymi lub innymi instrukcjami symbolicznymi, dekodować je, reprezentować zakodowanymi numerami i wprowadzać je do systemu CNC za pośrednictwem nośników informacji. Po obliczeniach i przetwarzaniu różne sygnały sterujące są wysyłane przez urządzenie CNC w celu kontrolowania działania obrabiarki, a części są automatycznie przetwarzane zgodnie z wymaganiami.
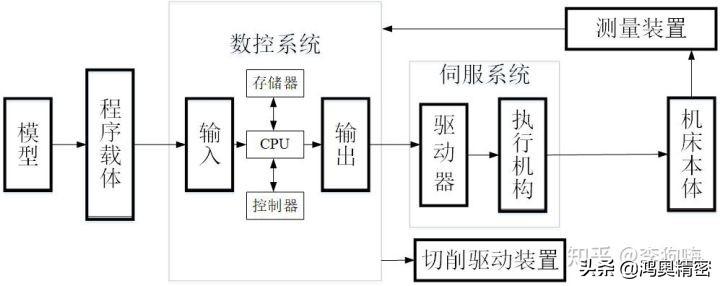
Proces obróbki obrabiarek CNC
Obróbka obrabiarek CNC dzieli współrzędne ruchu narzędzia i przedmiotu obrabianego na niektóre minimalne jednostki, a mianowicie minimalne przesunięcie. System CNC przesuwa współrzędne kilkoma minimalnymi przesunięciami zgodnie z wymaganiami programu części (tj. kontroluje trajektorię ruchu narzędzia), osiągając w ten sposób ruch względny między narzędziem a przedmiotem obrabianym oraz zakończenie obróbki części.
Ruch względny narzędzia wzdłuż każdej osi współrzędnych mierzony jest w jednostkach ekwiwalentu impulsu (mm/puls). Gdy ścieżka cięcia jest linią prostą lub łukiem, urządzenie CNC wykonuje "zagęszczenie punktów danych" między wartościami współrzędnych początkowych i końcowych segmentu linii lub łuku, oblicza serię wartości współrzędnych punktów pośrednich, a następnie wysyła impulsy do każdej współrzędnej zgodnie z wartościami współrzędnych punktów pośrednich, aby zapewnić przetwarzanie pożądanej linii prostej lub konturu łuku.
Gęstość punktów danych przeprowadzana przez urządzenia CNC nazywa się interpolacją, a generalnie urządzenia CNC pełnią funkcję interpolacji podstawowych (takich jak funkcje liniowe i okrągłe). W rzeczywistości obróbka każdej części krzywej L na obrabiarce CNC jest przybliżona przez podstawowe funkcje matematyczne, które może obsługiwać urządzenie CNC, takie jak linie, łuki itp. Oczywiście błąd przybliżenia musi spełniać wymagania rysunku części.
W porównaniu z tradycyjnymi obrabiarkami, obrabiarki CNC mają następujące zalety:
Wysoka dokładność przetwarzania i stabilna jakość. Dla każdego impulsu wyjściowego przez system CNC przesunięcie ruchomych części obrabiarki jest nazywane odpowiednikiem impulsu.Odpowiednik impulsu obrabiarek CNC wynosi ogólnie 0.001mm, a precyzyjne obrabiarki CNC mogą osiągnąć 0.0001mm, o znacznie wyższej rozdzielczości ruchu niż zwykłe obrabiarki. Ponadto obrabiarki CNC posiadają urządzenia do wykrywania położenia, które mogą dostarczyć informacji zwrotnej do systemu CNC o rzeczywistym przemieszczeniu ruchomych części lub kącie śruby i serwosilnika i to zrekompensować. Dlatego można osiągnąć większą dokładność obróbki niż sama obrabiarka. Jakość części przetwarzanych przez obrabiarki CNC jest gwarantowana przez obrabiarkę i nie ma wpływu na błędy operacyjne, więc spójność rozmiaru tej samej partii części jest dobra, a jakość jest stabilna. Zdolność do obróbki złożonych części, które są trudne lub niemożliwe do obróbki przy użyciu zwykłych obrabiarek. Na przykład obrabiarki CNC, które wykorzystują połączenie dwuosiowe lub więcej niż dwuosiowe, mogą przetwarzać zakrzywione części obrotowe ciała, części krzywkowe i różne złożone zakrzywione przestrzenne części z zakrzywionym generatorem. Wysoka wydajność produkcji. Prędkość wrzeciona i zakres posuwu obrabiarek CNC są większe niż zwykłe obrabiarki, a dobra sztywność konstrukcyjna pozwala obrabiarkom CNC korzystać z dużych ilości cięcia, skutecznie oszczędzając czas manewrowania. Do obróbki niektórych złożonych części, jeśli stosuje się centrum obróbcze CNC z automatycznym urządzeniem do wymiany narzędzi, może to osiągnąć ciągłą obróbkę wielu procesów pod jednym zaciskaniem, skrócić czas obrotu półproduktów i znacznie poprawić wydajność. Silna zdolność adaptacyjna do przeprojektowania produktów. Po zmodyfikowanej konstrukcji obrabianych części konieczne jest tylko zmiana programu obróbki części i dostosowanie parametrów narzędzia na obrabiarce CNC, aby osiągnąć obróbkę zmodyfikowanych części, znacznie zmniejszając cykl przygotowania produkcji. Dlatego obrabiarki CNC mogą szybko przejść z obróbki jednego rodzaju części do obróbki innej zmodyfikowanej konstrukcji części, co zapewnia dużą wygodę w przetwarzaniu pojedynczych i małych serii nowych produktów próbnych i częstych aktualizacji struktury produktu. Korzystne dla rozwoju technologii produkcji w kierunku kompleksowej automatyki. Obrabiarki CNC są podstawowym wyposażeniem do automatyki obróbki mechanicznej. Zintegrowane systemy automatyki, takie jak FMC (Flexible Machine Center), FMS (Flexible Manufacturing System), CIMS (Computer Integrated Manufacturing System), itp., zbudowane na obrabiarkach CNC, umożliwiają integrację, inteligencję i automatyzację produkcji mechanicznej. Dzieje się tak dlatego, że system sterowania obrabiarek CNC przyjmuje informacje cyfrowe i standaryzowane wejście kodu oraz ma interfejsy komunikacyjne, co ułatwia osiągnięcie komunikacji danych między obrabiarkami CNC.Jest najbardziej odpowiedni do łączenia komputerów w celu utworzenia przemysłowej sieci sterowania, realizacji obliczeń, zarządzania i sterowania zautomatyzowanymi procesami produkcyjnymi. Silna funkcja monitorowania i zdolność do diagnozowania usterek. System CNC nie tylko kontroluje ruch obrabiarki, ale także zapewnia kompleksowy monitoring obrabiarki. Na przykład wczesne ostrzeganie i diagnozowanie usterek można przeprowadzić dla niektórych czynników, które powodują usterki, znacznie poprawiając wydajność konserwacji. Zmniejszyć intensywność pracy pracowników i poprawić warunki pracy. Wreszcie, czym jest "wysokiej klasy obrabiarka CNC"?
Definicja "high-end" lub "high-end" obrabiarek CNC: obrabiarki CNC z funkcjami takimi jak szybka, precyzja, inteligencja, kompozyt, połączenie wieloosiowe, komunikacja sieciowa itp. Jego rozwój symbolizuje, że obecny przemysł produkcji obrabiarek w kraju zajmuje zaawansowany etap w rozwoju światowego przemysłu obrabiarek. Dlatego na arenie międzynarodowej wysokiej klasy technologie obrabiarek, takie jak pięcioosiowe obrabiarki CNC są uważane za ważny symbol uprzemysłowienia kraju. [10]
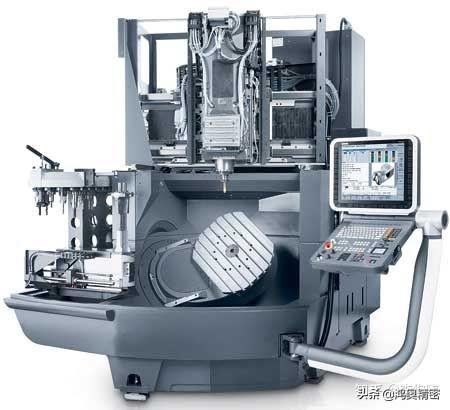
Centrum obróbki pięcioosiowej DMG
Obrabiarki CNC można podzielić na trzy poziomy w zależności od ich poziomu funkcjonalnego: niski, średni i wysoki. Ta metoda klasyfikacji jest szeroko stosowana w Chinach. Granice pomiędzy niską, średnią i wysoką klasyfikacją są względne, a standardy klasyfikacji różnią się w różnych okresach. W zależności od aktualnego poziomu rozwoju można ją ogólnie odróżnić od następujących aspektów (oczywiście klasyfikacja ta nie może obejmować wszystkich wskaźników):
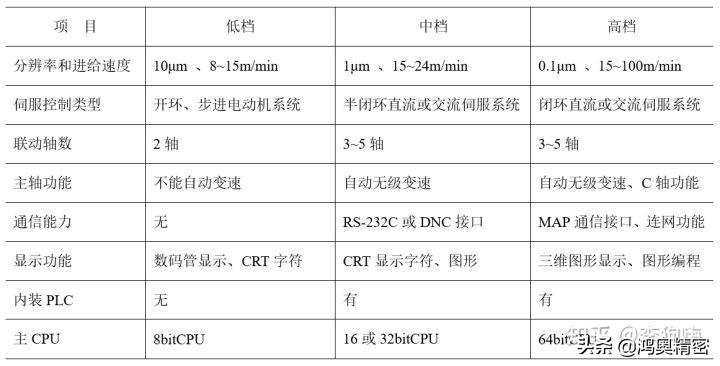
Porównanie wysokiej, średniej i niskiej klasy obrabiarek CNC
Wraz z rozwojem zaawansowanej technologii produkcji nowoczesne obrabiarki CNC są wymagane do rozwoju w kierunku wysokiej prędkości, wysokiej precyzji, wysokiej niezawodności, inteligencji i bardziej kompletnych funkcji.