W mgnieniu oka obsługuję tokarkę CNC od dziesięciu lat i zdobyłem pewne umiejętności obróbki i doświadczenie w zakresie tokarek CNC. Chciałbym wymienić się pomysłami z kolegami. Ze względu na częste wymiany obrabianych części i ograniczone warunki fabryczne, od ostatniej dekady sami programujemy, sprawdzamy narzędzia, debugowanie i kończymy obróbkę części. Podsumowując, nasze umiejętności operacyjne można podzielić na następujące punkty. (Autor/Li Neng)
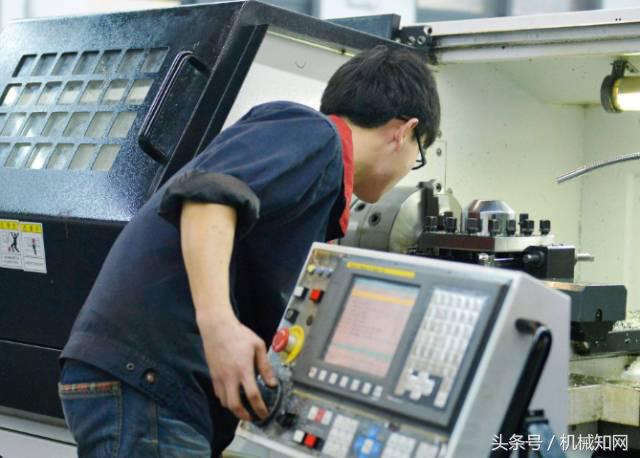
Umiejętności programowania: Ze względu na wysokie wymagania precyzyjne naszej fabryki dla przetworzonych produktów, podczas programowania należy wziąć pod uwagę następujące czynniki:
1. Sekwencja przetwarzania części:
Najpierw wiercić, a następnie spłaszczyć koniec (ma to zapobiec skurczu materiału podczas wiercenia);
Najpierw surowy samochód, a następnie dobry samochód (ma to zapewnić dokładność części);
Najpierw obrób te o większych tolerancjach, a następnie te o mniejszych tolerancjach (gwarantuje to, że powierzchnia o małej tolerancji nie jest zarysowana i zapobiega deformacji części).
2. Wybierz rozsądną prędkość, szybkość posuwu i głębokość cięcia w oparciu o twardość materiału:
1) Wybierz materiały ze stali węglowej o dużej prędkości, dużej szybkości posuwu i dużej głębokości cięcia. Na przykład: 1Gr11, wybierz S1600, F0.2 i głębokość cięcia 2mm;
2) Wybierz niską prędkość, niską szybkość posuwu i małą głębokość cięcia dla twardych stopów. Na przykład: GH4033, wybierz S800, F0.08 i głębokość cięcia 0,5mm;
3) Stop tytanu powinien być wybierany z niską prędkością, dużą szybkością posuwu i małą głębokością cięcia. Na przykład w przypadku Ti6 wybierz S400, F0.2 i głębokość cięcia 0,3mm. Biorąc na przykład obróbkę pewnej części: materiałem jest K414, który jest bardzo twardym materiałem. Po wielu testach został ostatecznie wybrany jako S360, F0.1 i głębokość cięcia 0.2, aby wyprodukować kwalifikowaną część.
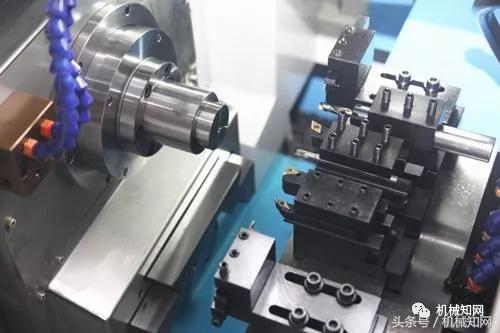
2,2Technika wyrównania noża jest podzielona na instrument wyrównywania noża i bezpośrednie wyrównanie noża. Większość tokarek w naszej fabryce nie posiada urządzenia do wyrównywania narzędzi i wymaga bezpośredniego wyrównywania narzędzi.Poniższe techniki wyrównywania narzędzi odnoszą się do bezpośredniego wyrównywania narzędzi.
Najpierw wybierz środek prawej powierzchni końcowej części jako punkt wyrównania narzędzia i ustaw go jako punkt zerowy. Po powrocie obrabiarki do początku, każde narzędzie, które musi być użyte, jest wyrównane ze środkiem prawej powierzchni końcowej części jako punkt zerowy; Gdy narzędzie wejdzie w kontakt z prawą powierzchnią końcową, wprowadź Z0 i kliknij przycisk pomiarowy. Wartość kompensacji narzędzia automatycznie rejestruje wartość mierzoną, wskazując, że oś Z jest prawidłowo wyrównana. Oś X służy do cięcia próbnego, a przy użyciu narzędzia do regulacji zewnętrznego koła części, wejść x20 w celu zmierzenia wartości zewnętrznego koła regulowanej części (np. x wynosi 20mm). Kliknij przycisk pomiarowy, a wartość kompensacji automatycznie rejestruje zmierzoną wartość. Ta metoda wyrównania narzędzi, nawet jeśli obrabiarka jest wyłączona, nie zmieni wartości wyrównania po włączeniu i ponownym uruchomieniu. Jest odpowiednia do dużej i długoterminowej produkcji tej samej części, podczas której tokarka nie musi być ponownie ustawiana.
3,3Umiejętności debugowania: Po programowaniu i wyrównaniu narzędzia, części muszą być przetestowane i debugowane. Aby zapobiec błędom w wyrównaniu programu i narzędzia, które mogą powodować wypadki kolizyjne, powinniśmy najpierw wykonać obróbkę symulacji pustego skoku. W systemie współrzędnych obrabiarki narzędzie powinno być przesunięte w prawo o 2-3 razy całkowitej długości części jako całości; Następnie rozpocznij symulację obróbki. Po zakończeniu obróbki symulacyjnej, potwierdź, że program i wyrównanie narzędzi są prawidłowe, a następnie rozpocznij obróbkę części. Po obróbce pierwszego elementu części, samodzielnie sprawdź i potwierdź, że jest kwalifikowany, a następnie znajdź dedykowanego inspektora, aby go sprawdzić. Tylko po potwierdzeniu, że jest on kwalifikowany, można zakończyć debugowanie.
4,8Po zakończeniu pierwszego elementu cięcia próbnego, przetworzone części muszą być produkowane masowo. Jednak kwalifikacja pierwszego elementu nie oznacza, że cała partia części będzie kwalifikowana, ponieważ podczas obróbki różne materiały przetwarzania powodują zużycie narzędzi. Miękkie materiały obróbki mają mniejsze zużycie narzędzi, podczas gdy twarde materiały obróbki mają szybsze zużycie narzędzi. Dlatego, podczas przetwarzania, konieczne jest przeprowadzanie częstych kontroli i terminowe zwiększenie lub zmniejszenie wartości kompensaczenia lub zmniejszenia wartości kompensacji narzędzi zapewnienia kwalifikacji.
Biorąc na przykład określoną część, materiałem obróbki jest K414, z całkowitą długością obróbki 180mm. Ze względu na niezwykle twardy materiał zużycie narzędzia jest bardzo szybkie podczas obróbki. Od punktu początkowego do punktu końcowego, niewielkie odchylenie 10-20mm będzie generowane z powodu zużycia narzędzia. Dlatego musimy ręcznie dodać niewielkie odchylenie 10-20mm w programie, aby zapewnić kwalifikację części.
Krótko mówiąc, podstawową zasadą obróbki jest najpierw szorstka maszyna, usunięcie nadmiaru materiału z obrabianego przedmiotu, a następnie precyzyjna maszyna; Należy unikać wibracji podczas przetwarzania; Istnieje wiele powodów, aby uniknąć drgań spowodowanych odkształceniem termicznym podczas obróbki przedmiotu, które mogą być spowodowane nadmiernym obciążeniem; Może to być rezonans między obrabiarką a przedmiotem obrabianym lub niewystarczająca sztywność obrabiarki lub może być spowodowana pasywacją narzędzia. Możemy zmniejszyć drgania za pomocą następujących metod:; Zmniejsz boczną szybkość posuwu i głębokość obróbki, sprawdź, czy mocowanie przedmiotu obrabianego jest bezpieczne, zwiększ prędkość narzędzia, co może zmniejszyć rezonans poprzez obniżenie prędkości. Dodatkowo sprawdź, czy konieczne jest wymiana narzędzia na nowe.
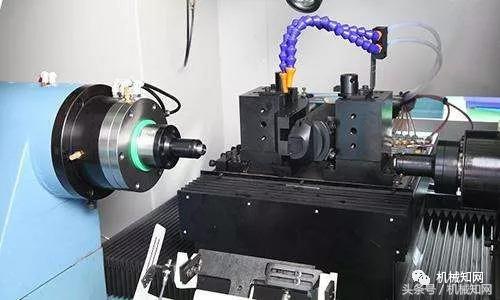
5,Doświadczenie zapobiegania kolizjom między obrabiarkami znacznie niszczy dokładność obrabiarek, a wpływ różni się dla różnych rodzajów obrabiarek. Ogólnie rzecz biorąc, ma większy wpływ na obrabiarki o słabej sztywności. Tak długo, jak operator jest ostrożny i opanuje pewne metody antykolizyjne, kolizje można całkowicie zapobiec i uniknąć.
Główna przyczyna kolizji:
Jednym z nich jest błąd wejściowy średnicy i długości narzędzia tnącego;
Po drugie, występują błędy w wprowadzaniu wymiarów i innych powiązanych z nimi wymiarów geometrycznych przedmiotu obrabianego, a także błędy w początkowym pozycjonowaniu obrabianego przedmiotu;
Po trzecie, system współrzędnych obrabianego przedmiotu obrabianego obrabiarki jest ustawiony nieprawidłowo lub punkt zerowy obrabiarki jest resetowany podczas procesu obróbki, co powoduje zmiany. Kolizje obrabiarek występują najczęściej podczas szybkiego ruchu obrabiarki, a zagrożenia takich kolizji są również największe, których należy absolutnie unikać.
Operatorzy powinni więc zwrócić szczególną uwagę na początkowy etap wykonywania programu i wymiany narzędzia. Jeśli program jest nieprawidłowo edytowany lub średnica i długość narzędzia zostały nieprawidłowo wprowadzone, prawdopodobnie wystąpią kolizje. Na końcowym etapie programu, jeśli sekwencja działania cofania osi CNC jest nieprawidłowa, mogą również wystąpić kolizje.
Aby uniknąć wyżej wymienionych kolizji, operator powinien w pełni wykorzystać funkcje swoich rysów twarzy podczas obsługi obrabiarki, obserwować, czy występują jakiekolwiek nieprawidłowe ruchy, iskry, hałas, nieprawidłowe dźwięki, wibracje lub spalone zapachy. W przypadku stwierdzenia nieprawidłowej sytuacji program należy natychmiast zatrzymać.Obrabiarka może kontynuować pracę dopiero po rozwiązaniu problemu z łóżkiem.
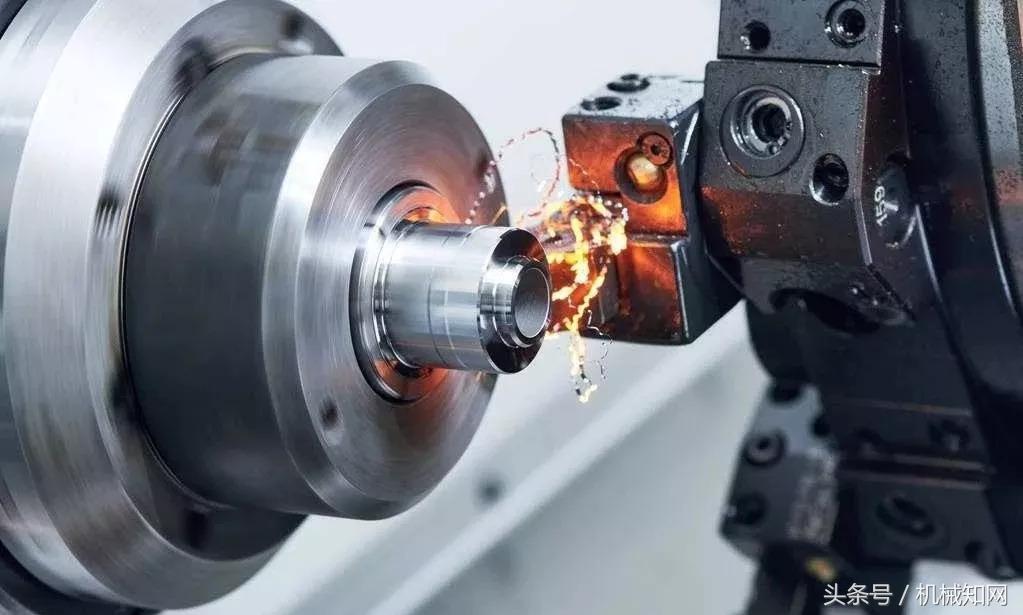
Krótko mówiąc, opanowanie umiejętności obsługi obrabiarek CNC jest procesem stopniowym i nie może być osiągnięte z dnia na dzień. Opiera się on na opanowaniu podstawowej obsługi obrabiarek, podstawowej wiedzy z zakresu obróbki mechanicznej oraz podstawowej wiedzy programowania. Umiejętności obsługi obrabiarek CNC nie są stałe, wymagają od operatora pełnego wykorzystania wyobraźni i praktycznych zdolności w organicznej kombinacji, która jest innowacyjną pracą.