Num piscar de olhos, opero um torno CNC há dez anos e acumulei algumas habilidades de usinagem e experiência em torno CNC. Gostaria de trocar ideias com meus colegas. Devido à substituição frequente de peças usinadas e condições de fábrica limitadas, temos vindo a programar, verificar ferramentas, depurar e concluir a usinagem de peças por nós mesmos na última década. Em resumo, nossas habilidades operacionais podem ser divididas nos seguintes pontos. (Autor/Li Neng)
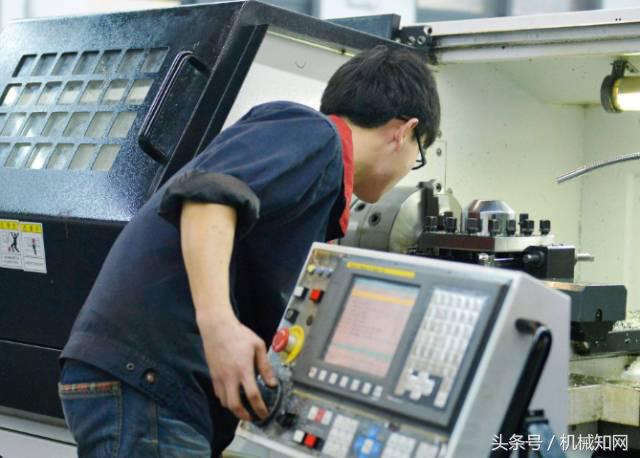
1,Habilidades de programação: Devido aos requisitos de alta precisão de nossa fábrica para produtos processados, os seguintes fatores precisam ser considerados ao programar:
1. Sequência de processamento das peças:
Perfure primeiro e depois achate a extremidade (isto é para evitar o encolhimento do material durante a perfuração);
Primeiro carro áspero, depois carro fino (isto é para garantir a precisão das peças);
Primeiro processe aqueles com tolerâncias maiores e, em seguida, processe aqueles com tolerâncias menores (isso garante que a superfície do tamanho de tolerância pequeno não é arranhada e impede a deformação da peça).
2. escolha uma velocidade razoável, taxa de alimentação, e profundidade de corte com base na dureza do material:
1) Escolha materiais de aço carbono com alta velocidade, alta taxa de alimentação e grande profundidade de corte. Por exemplo: 1Gr11, selecione S1600, F0.2, e uma profundidade de corte de 2mm;
2) Escolha baixa velocidade, baixa taxa de alimentação, e pequena profundidade de corte para ligas duras. Por exemplo: GH4033, selecione S800, F0,08 e uma profundidade de corte de 0,5mm;
3) A liga de titânio deve ser selecionada com baixa velocidade, alta taxa de alimentação e pequena profundidade de corte. Por exemplo, para Ti6, selecione S400, F0.2 e uma profundidade de corte de 0,3 mm. Tomando como exemplo o processamento de uma determinada peça: o material é K414, que é um material muito duro. Após vários testes, foi finalmente selecionado como S360, F0.1, e uma profundidade de corte de 0,2 para produzir uma peça qualificada.
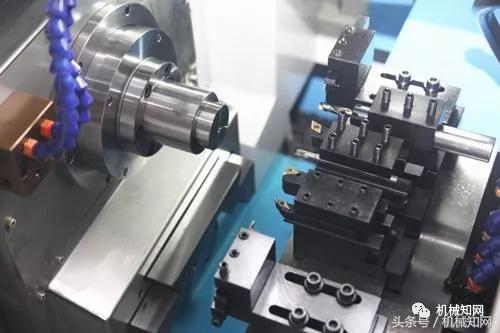
2,A técnica de alinhamento da faca é dividida em instrumento de alinhamento da faca e alinhamento direto da faca. A maioria dos tornos em nossa fábrica não tem um dispositivo de alinhamento de ferramentas e requer alinhamento direto de ferramentas.As seguintes técnicas de alinhamento de ferramentas referem-se ao alinhamento direto de ferramentas.
Primeiro, selecione o centro da face da extremidade direita da peça como o ponto de alinhamento da ferramenta e defina-o como o ponto zero. Depois que a máquina-ferramenta retornar à origem, cada ferramenta que precisa ser usada é alinhada com o centro da face da extremidade direita da peça como o ponto zero; Quando a ferramenta entrar em contato com a face da extremidade direita, insira Z0 e clique no botão de medição. O valor de compensação da ferramenta registrará automaticamente o valor medido, indicando que o eixo Z está alinhado corretamente. O eixo X é para corte experimental, e ao usar a ferramenta para ajustar o círculo externo da peça, insira x20 para medir o valor do círculo externo da peça sendo ajustada (como x sendo 20mm). Clique no botão de medição, e o valor de compensação gravará automaticamente o valor medido. Neste ponto, o eixo X também está alinhado corretamente; Este método de alinhamento da ferramenta, mesmo que a máquina-ferramenta esteja desligada, não alterará o valor de alinhamento após ligar e reiniciar. É adequado para a produção em larga escala e a longo prazo da mesma peça, durante a qual o torno não precisa ser re-alinhado.
3,Habilidades de depuração: Depois de programar e alinhar a ferramenta, as peças precisam ser testadas e depuradas. A fim de evitar erros no programa e alinhamento da ferramenta, que podem causar acidentes de colisão, devemos primeiro executar usinagem de simulação de curso vazio. No sistema de coordenadas da máquina-ferramenta, a ferramenta deve ser deslocada para a direita por 2-3 vezes o comprimento total da peça como um todo; Depois que a usinagem de simulação estiver concluída, confirme que o alinhamento do programa e da ferramenta estão corretos e comece a usinar as peças. Depois que a primeira peça da peça for usinada, verifique e confirme se ela está qualificada e, em seguida, encontre um inspetor dedicado para inspecioná-la. Somente depois que o inspetor dedicado confirmar que ela está qualificada pode a depuração ser concluída.
4,Depois que a primeira peça de corte experimental é concluída, as peças processadas precisam ser produzidas em massa. No entanto, a qualificação da primeira peça não significa que todo o lote de peças será qualificado, porque durante o processamento, diferentes materiais de processamento causarão desgaste da ferramenta. Materiais de processamento macio têm menos desgaste da ferramenta, enquanto materiais de processamento duro têm desgaste mais rápido da ferramenta. Portanto, durante o processamento, é necessário realizar inspeções frequentes e aumentar ou diminuir oportunamente o valor de compensação da ferramenta para garantir a qualificação das peças.
Tomando uma determinada parte como exemplo, o material de processamento é K414, com um comprimento total de processamento de 180mm. Devido ao material extremamente duro, o desgaste da ferramenta é muito rápido durante o processamento. Do ponto de partida ao ponto final, um ligeiro desvio de 10-20mm será gerado devido ao desgaste da ferramenta. Portanto, devemos adicionar manualmente um ligeiro desvio de 10-20mm no programa para garantir a qualificação da peça.
Em suma, o princípio básico de processamento é primeiro a máquina áspera, remover o excesso de material da peça de trabalho e, em seguida, a máquina de precisão; A vibração deve ser evitada durante o processamento; Há muitas razões para evitar a vibração causada pela deformação térmica durante o processamento da peça de trabalho, que pode ser devido à carga excessiva; Pode ser ressonância entre a máquina-ferramenta e a peça de trabalho, ou rigidez insuficiente da máquina-ferramenta, ou pode ser causada por passivação da ferramenta. Podemos reduzir a vibração pelos seguintes métodos:; Reduza a taxa de alimentação lateral e a profundidade de usinagem, verifique se o aperto da peça está seguro, aumente a velocidade da ferramenta, o que pode reduzir a ressonância reduzindo a velocidade. Além disso, verifique se é necessário substituir a ferramenta por uma nova.
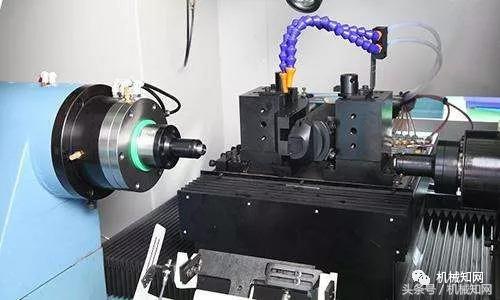
5,A experiência de evitar colisões entre máquinas-ferramentas danifica grandemente a precisão das máquinas-ferramentas, eo impacto varia para diferentes tipos de máquinas-ferramentas. De um modo geral, tem um impacto maior nas máquinas-ferramentas com rigidez fraca. Assim, para tornos CNC de alta precisão, as colisões devem ser absolutamente eliminadas. Desde que o operador seja cuidadoso e domine certos métodos anticolisão, as colisões podem ser completamente evitadas e evitadas.
A principal razão das colisões:
Um é o erro de entrada do diâmetro e comprimento da ferramenta de corte;
Em segundo lugar, há erros na introdução das dimensões e outras dimensões geométricas relacionadas da peça de trabalho, bem como erros no posicionamento inicial da peça de trabalho;
Em terceiro lugar, o sistema de coordenadas da peça de trabalho da máquina-ferramenta é ajustado incorretamente, ou o ponto zero da máquina-ferramenta é redefinido durante o processo de usinagem, resultando em mudanças. As colisões da máquina-ferramenta ocorrem principalmente durante o movimento rápido da máquina-ferramenta, e os riscos de tais colisões também são os maiores, o que deve ser absolutamente evitado.
Portanto, os operadores devem prestar especial atenção ao estágio inicial de execução do programa e substituição da ferramenta. Se o programa for editado incorretamente ou o diâmetro e comprimento da ferramenta forem inseridos incorretamente, é provável que ocorram colisões. No estágio final do programa, se a sequência da ação de retração do eixo CNC estiver incorreta, também podem ocorrer colisões.
Para evitar as colisões acima mencionadas, o operador deve utilizar plenamente as funções de suas características faciais ao operar a máquina-ferramenta, observar se há movimentos anormais, faíscas, ruídos, sons anormais, vibrações ou odores queimados. Se alguma situação anormal for encontrada, o programa deve ser interrompido imediatamente. A máquina-ferramenta só pode continuar a funcionar após o problema da cama é resolvido.
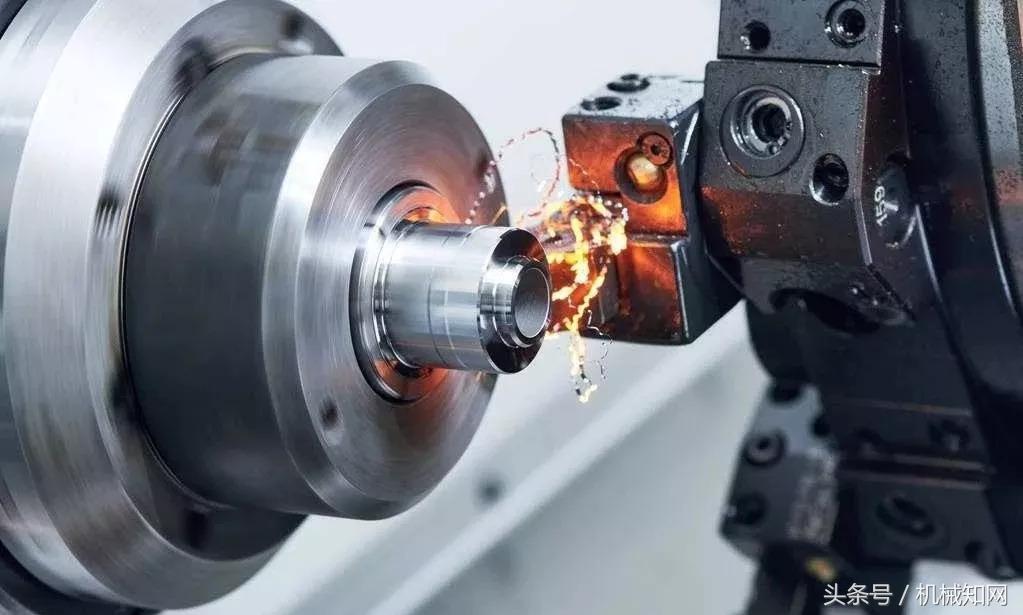
Em suma, dominar as habilidades de operação das máquinas-ferramentas CNC é um processo gradual e não pode ser alcançado durante a noite. Baseia-se no domínio da operação básica de máquinas-ferramentas, no conhecimento fundamental do processamento mecânico e no conhecimento básico da programação. As habilidades de operação das máquinas-ferramentas CNC não são fixas, elas exigem que o operador utilize plenamente sua imaginação e habilidade prática em uma combinação orgânica, que é um trabalho inovador.