Selectarea sculelor și sculelor de tăiere este unul dintre conținutul important al tehnologiei de Prelucrare CNC, care afectează nu numai eficiența prelucrării mașinii unelte, ci și calitatea prelucrării. În comparație cu metodele tradiționale de prelucrare, prelucrarea CNC are cerințe mai mari pentru scule și scule de tăiere. Nu numai că necesită precizie ridicată, rigiditate bună și durabilitate, dar necesită, de asemenea, dimensiuni stabile și instalare și reglare convenabilă.
Materiale de prelucrare CNC 1. oțel de mare viteză
Oțel de mare viteză, cunoscut și sub numele de oțel frontal sau oțel alb. Este un oțel aliat care conține elemente, cum ar fi tungsten (W), molibden (Mo), crom (Cr), vanadiu (V), cobalt (Co), etc Este împărțit în două serii majore de tungsten și molibden și este un material de unelte tradiționale. Duritatea sa la temperatura camerei este de 62-65HRC, iar duritatea sa termică poate fi crescută la 500-600 ℃. După stingere, deformarea este mică, ușor de ascuțit și poate fi forjată și tăiată. Acesta poate fi utilizat nu numai pentru fabricarea burghiului și a mașinilor de frezat, ci și pentru fabricarea uneltelor complexe de tăiere, cum ar fi mașinile de frezat și mașinile de frezat. Cu toate acestea, datorită vitezei sale de tăiere admisibile scăzute (50m/min), este utilizat în principal pentru prelucrarea la viteze scăzute pe mașini CNC. Oțelul obișnuit de mare viteză este reprezentat de W18Cr4V.
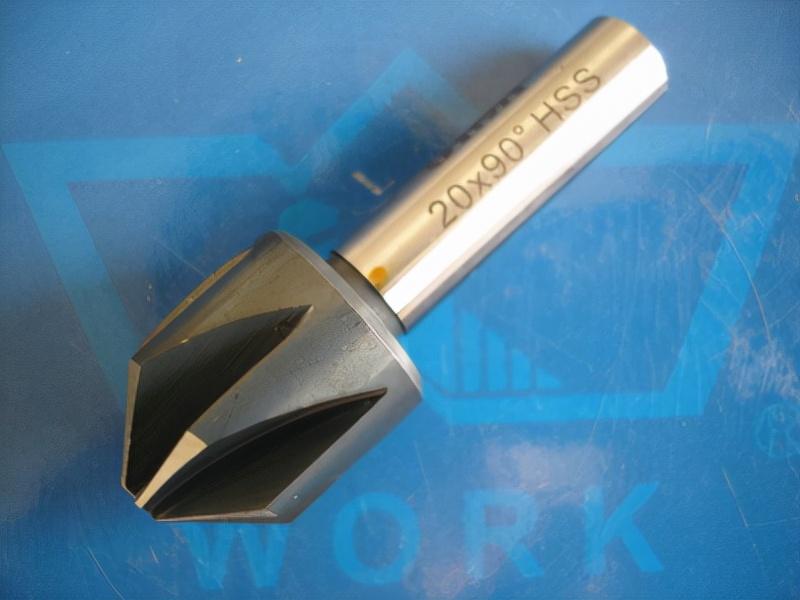
2. Aliaj dur
Aliajul dur este un produs metalurgic al pulberii fabricat din carburi (WC, TiC, TaC, NbC, etc.) cu duritate ridicată și punct de topire, folosind Co, Mo, Ni ca lianți. Duritatea temperaturii sale poate ajunge la 74-82HRC și poate rezista la temperaturi ridicate variind de la 800 ℃ la 1000 ℃. Datorită costului său scăzut de producție, poate prezenta performanțe excelente de tăiere la viteză medie (150m / min) și tăiere cu alimentare ridicată, făcându-l cel mai utilizat material de scule în prelucrarea CNC. Dar rezistența la impact și rezistența la îndoire sunt mult mai mici decât cele ale oțelului de mare viteză, deci rareori este transformată în unelte de tăiere integrale. În utilizarea practică, blocurile de tăiere din aliaj dur sunt, în general, fixate pe corpul de tăiere prin sudare sau prindere mecanică. Aliajele dure utilizate în mod obișnuit includ aliaje de tungsten cobalt (YG) (YG8, YG6, YG3), aliaje de tungsten titan (YT) (YT5, YT15, YT30) și aliaje de tungsten titan tantal (niobiu) (YW) (YW1, YW2).
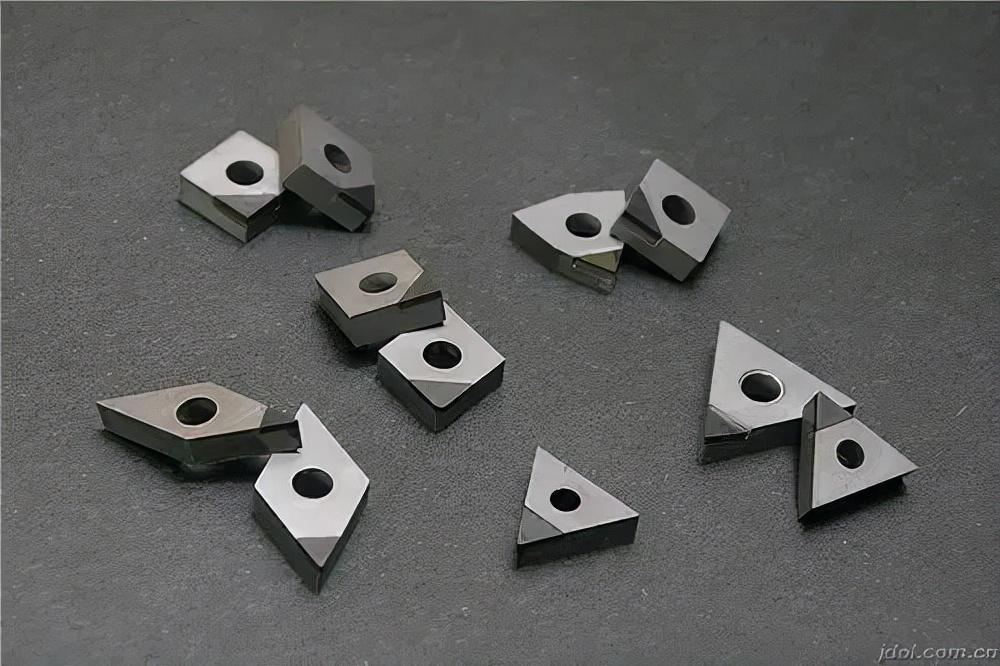
3. Aliaj dur acoperit
Uneltele din aliaj dur acoperite sunt realizate prin acoperirea unuia sau mai multor straturi de TiN rezistente la uzură, TiCN, TiAlN și Al2O3 pe unelte din aliaj dur cu rezistență bună. Grosimea acoperirii variază de la 2 µm la 18 µm. Acoperirile au de obicei două funcții: pe de o parte, ele au un coeficient de conductivitate termică mult mai mic decât substratul uneltei și materialul piesei de prelucrat, slăbind efectul termic al substratului uneltei; Pe de altă parte, poate îmbunătăți eficient frecarea și aderența în timpul procesului de tăiere, reducând generarea de căldură de tăiere. TiN are caracteristici de frecare scăzute, care pot reduce pierderea țesutului de acoperire. TiCN poate reduce uzura suprafeței de tăiere din spate. Acoperirea TiCN are o duritate mai mare. Acoperirea Al2O3 are un efect excelent de izolare termică. În comparație cu sculele de tăiere din aliaj dur, sculele de tăiere din aliaj dur acoperite s-au îmbunătățit semnificativ în ceea ce privește rezistența, duritatea și rezistența la uzură. Pentru tăierea pieselor de prelucrat cu o duritate de 45-55 HRC, aliajele dure acoperite cu costuri reduse pot obține tăiere de mare viteză. În ultimii ani, unii producători s-au bazat pe îmbunătățirea materialelor de acoperire și proporțiilor, ceea ce a îmbunătățit considerabil proprietățile instrumentelor de tăiere acoperite.
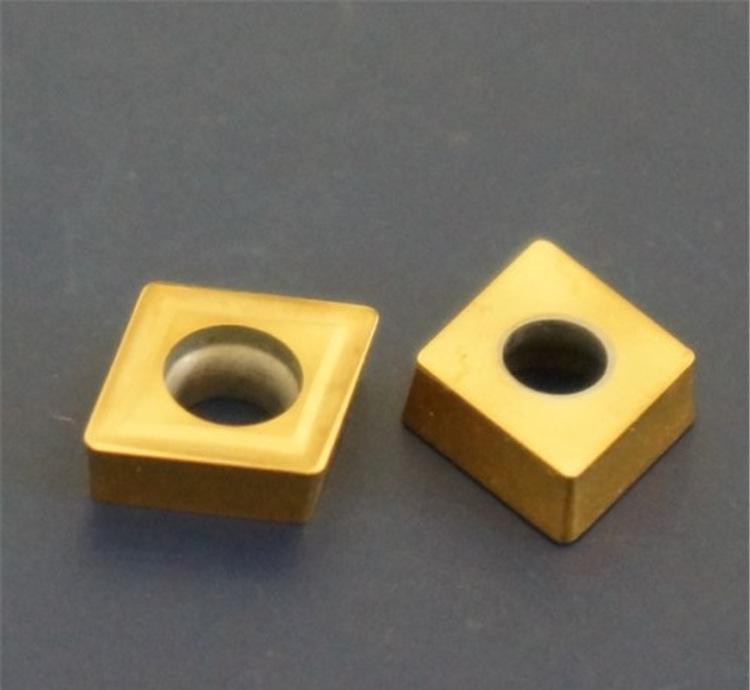
4. Materiale ceramice
Ceramica este unul dintre materialele uneltelor de tăiere care s-a dezvoltat rapid și a devenit din ce în ce mai utilizat pe scară largă în ultimii 20 de ani. În viitorul apropiat, ceramica poate duce la o a treia revoluție în prelucrarea de tăiere, după oțel de mare viteză și aliaje dure.
Uneltele de tăiere ceramică au avantaje, cum ar fi duritate ridicată (91-95HRA), rezistență ridicată (rezistență la îndoire de 750MPa ~ 1000MPa), rezistență bună la uzură, stabilitate chimică bună, rezistență bună la adeziv, coeficient de frecare scăzut și costuri scăzute. Nu numai că, sculele de tăiere ceramică au, de asemenea, duritate la temperaturi ridicate, atingând 80HRA la 1200 ℃. Când sunt utilizate în mod normal, uneltele de tăiere ceramică au o durată de viață extrem de lungă, iar viteza de tăiere poate fi crescută de 2-5 ori în comparație cu uneltele de tăiere din aliaj dur. Acestea sunt deosebit de potrivite pentru prelucrarea materialelor de înaltă duritate, prelucrarea de precizie și prelucrarea de mare viteză. Acestea pot prelucra diferite tipuri de oțel călit și fontă călită cu o duritate de până la 60HRC. Utilizate frecvent includ ceramica pe bază de aluminiu, ceramica pe bază de nitrură de siliciu și ceramica metalică. Uneltele de tăiere ceramică pe bază de aluminiu au o întărire termică mai mare decât aliajele dure. În condiții de tăiere de mare viteză, muchia de tăiere, în general, nu suferă deformare plastică, dar rezistența și rezistența sa sunt mai mici. În plus față de duritatea termică ridicată, ceramica pe bază de nitrură de siliciu, de asemenea, au o rezistență bună. În comparație cu ceramica pe bază de oxid de siliciu, dezavantajul său este că este predispusă la difuzie la temperaturi ridicate în timpul prelucrării oțelului, ceea ce intensifică uzura sculelor. Uneltele ceramice pe bază de nitrură de siliciu sunt utilizate în principal pentru strunjirea intermitentă și frezarea fontei gri. Metalul Cermet este un material de scule pe bază de carburi, similar aliajelor dure, dar cu afinitate mai mică, frecare bună și rezistență mai bună la uzură. Acesta poate rezista la temperaturi mai ridicate de tăiere decât aliajele dure convenționale, dar nu are rezistența la impact, duritatea în timpul prelucrării grele și rezistența la viteze mici și rate ridicate de alimentare a aliajelor dure. În ultimii ani, prin cercetarea extinsă, îmbunătățirea și adoptarea de noi procese de fabricație, rezistența la îndoire și rezistența materialelor ceramice au fost mult îmbunătățite. De exemplu, noua ceramică metalică NX2525 dezvoltată de Mitsubishi Metal Company în Japonia și seria CT de lame metalice ceramice și seria de lame metalice ceramice acoperite dezvoltată de Sandvik Company în Suedia au o rezistență semnificativ mai mare la îndoire și rezistență la uzură decât ceramica metalică obișnuită, extinzând considerabil gama de aplicații a materialelor ceramice.
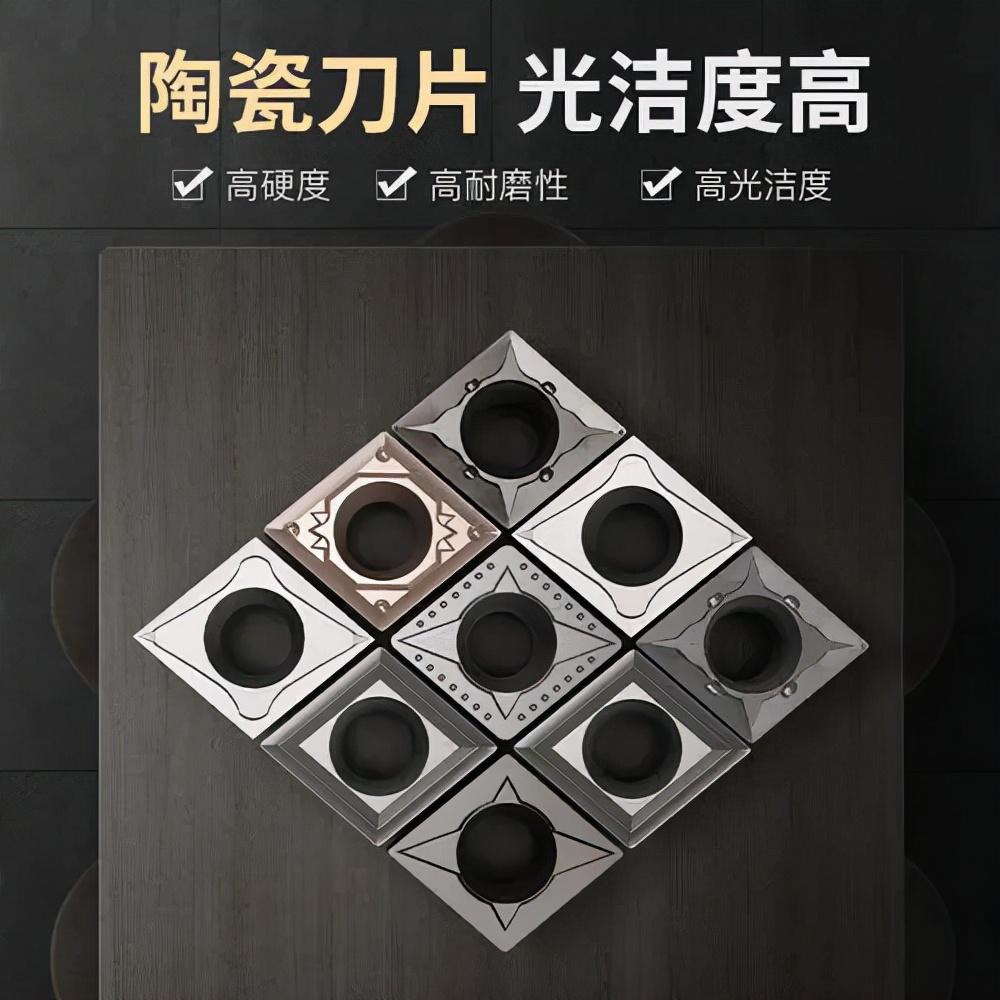
5. Nitrură cubică de bor (CBN)
CBN este un material de înaltă duritate sintetizat artificial, cu o duritate de până la 7300-9000HV. Duritatea și rezistența la uzură sunt doar a doua decât diamantul, și are duritate excelentă la temperaturi ridicate. În comparație cu uneltele de tăiere ceramică, rezistența la căldură și stabilitatea chimică sunt ușor mai rele, dar rezistența la impact și performanța anti-zdrobire sunt mai bune.
Este utilizat pe scară largă pentru tăierea oțelului călit (peste 50HRC), fontă gri perlit, fontă răcită și aliaje la temperaturi ridicate. În comparație cu uneltele de tăiere din aliaj dur, viteza sa de tăiere poate fi crescută cu un ordin de mărime. Uneltele de tăiere PCBN (nitrură de bor cubică policristalină) cu conținut ridicat de CBN au duritate ridicată, rezistență bună la uzură, rezistență ridicată la compresie și rezistență la impact bună. Cu toate acestea, dezavantajele lor sunt stabilitatea termică slabă și inerția chimică scăzută, ceea ce le face potrivite pentru tăierea aliajelor rezistente la căldură, fontă și metale sinterizate pe bază de fier. Conținutul de particule CBN în uneltele compozite de tăiere PCBN este relativ scăzut, iar ceramica este folosită ca lianți, rezultând o duritate mai mică. Cu toate acestea, acest lucru compensează stabilitatea termică slabă și inerța chimică scăzută a PCBN cu conținut ridicat de CBN, ceea ce îl face potrivit pentru tăierea oțelului călit. În domeniul de aplicare al tăierii fontei gri și oțelului stins, sunt disponibile unelte de tăiere ceramică și unelte de tăiere CBN pentru selectarea simultană. Atunci când tăierea uscată a oțelului călit, costul utilizării ceramicii Al2O3 este mai mic decât cel al materialelor PCBN, deoarece sculele de tăiere ceramică au o bună stabilitate termică și chimică, dar nu sunt la fel de dure și dure ca sculele de tăiere PCBN. Uneltele ceramice de tăiat sunt o alegere mai bună atunci când tăiați piese de prelucrat cu o duritate sub 60HRC și rate mici de alimentare. Sculele de tăiere PCBN sunt potrivite pentru situațiile în care duritatea piesei de prelucrat este mai mare de 60HRC, în special pentru prelucrarea automată și de înaltă precizie.
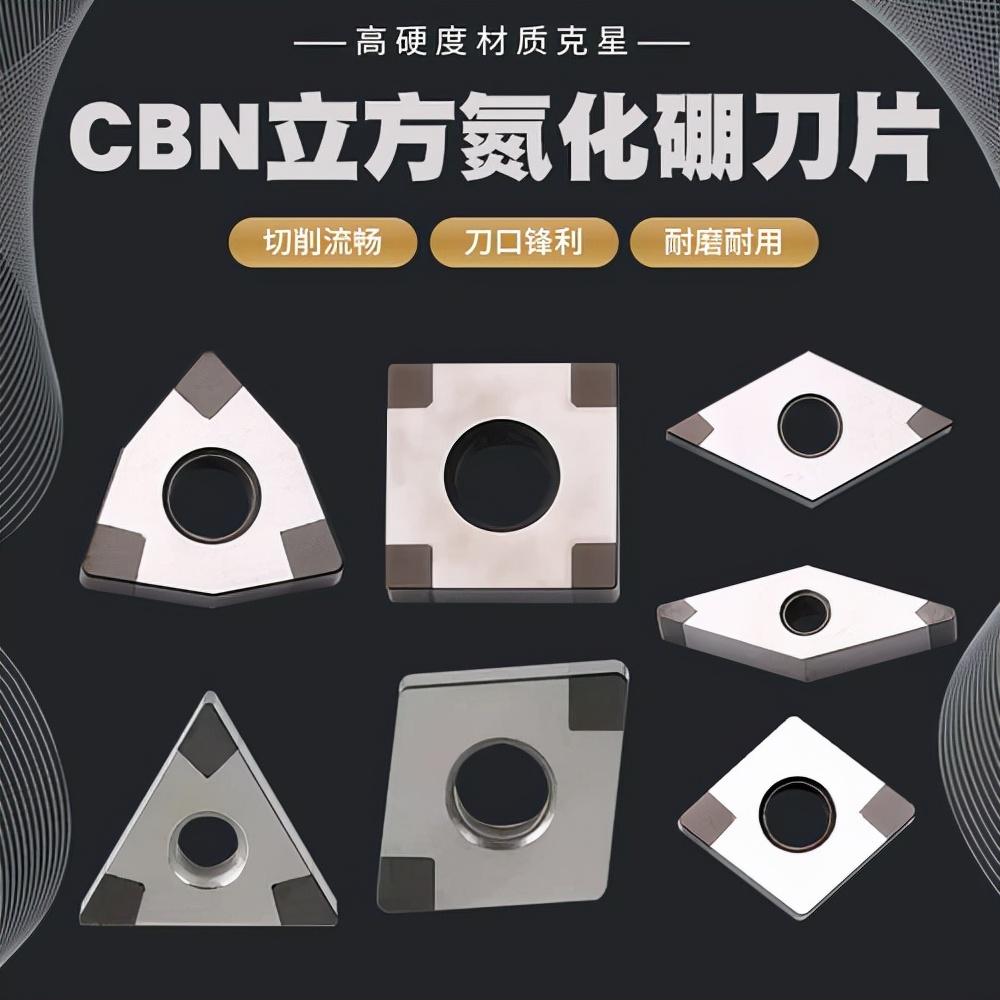
6. Diamant policristalin (PCD)
Fiind cel mai dur material pentru unelte de tăiere, PCD are o duritate de până la 10000HV și cea mai bună rezistență la uzură. Acesta poate prelucra materiale metalice neferoase moi cu viteză mare (1000m/min) și precizie. Cu toate acestea, este sensibil la impact, ușor de rupt și are o afinitate puternică pentru fierul din metale feroase, care poate declanșa cu ușurință reacții chimice. În general, poate fi folosit doar pentru prelucrarea pieselor neferoase, cum ar fi metalele neferoase și aliajele lor, fibrele de sticlă, ceramica inginerie și aliajele dure, care sunt materiale extrem de dure.
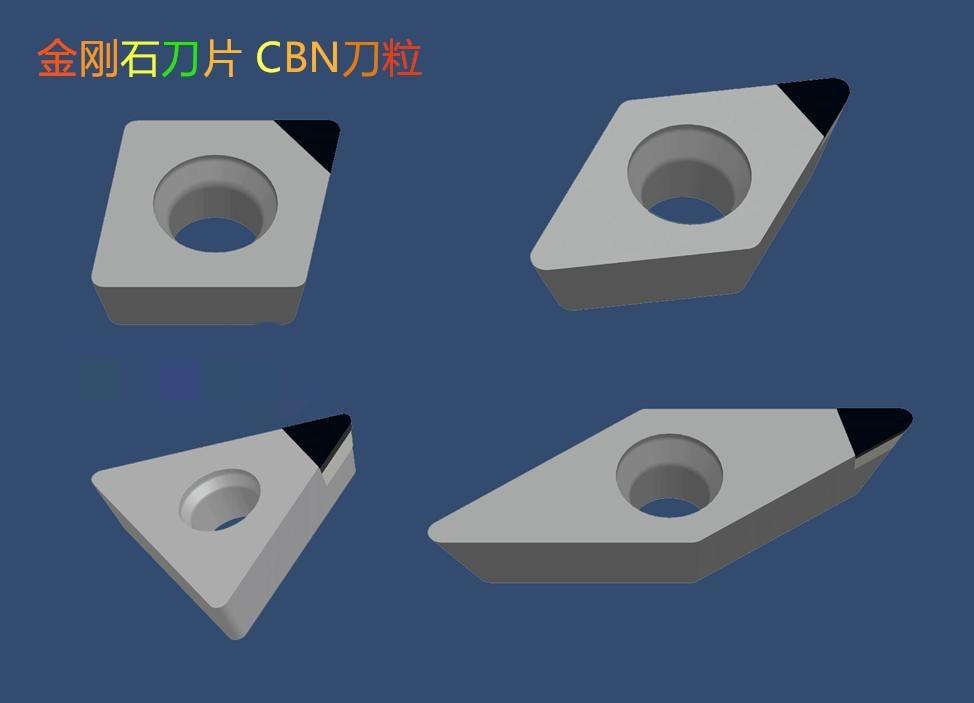