Într-o clipită din ochi, operez un strung CNC timp de zece ani și am acumulat unele abilități de prelucrare și experiență în strunguri CNC. Aș dori să schimb idei cu colegii mei. Datorită înlocuirii frecvente a pieselor prelucrate și condițiilor limitate ale fabricii, am programat, verificăm sculele, depanam și finalizăm noi înșine prelucrarea pieselor. Pe scurt, abilitățile noastre operaționale pot fi împărțite în următoarele puncte. (Autor/Li Neng)
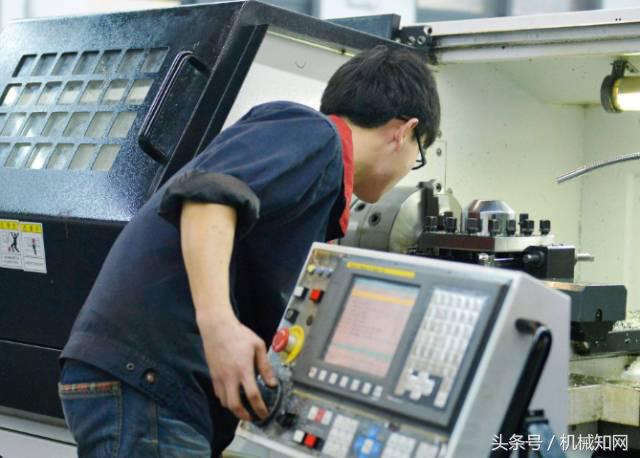
1,Abilități de programare: Datorită cerințelor de înaltă precizie ale fabricii noastre pentru produsele prelucrate, următorii factori trebuie să fie luați în considerare atunci când programați:
(1) Secvenţa de prelucrare a pieselor:
Găuriți mai întâi și apoi aplatizați capătul (acest lucru este pentru a preveni contracția materialului în timpul găuririi);
Mai întâi mașina dură, apoi mașina fină (acest lucru este pentru a asigura precizia pieselor);
Mai întâi procesați cele cu toleranțe mai mari, apoi procesați cele cu toleranțe mai mici (acest lucru asigură că suprafața dimensiunii mici de toleranță nu este zgâriată și previne deformarea pieselor).
2. Alegeți o viteză rezonabilă, rata de alimentare și adâncimea de tăiere pe baza durității materialului:
1) Alegeți materiale din oțel carbon cu viteză mare, rată ridicată de alimentare și adâncime mare de tăiere. De exemplu: 1Gr11, selectați S1600, F0.2 și o adâncime de tăiere de 2mm;
2) Alegeți viteză scăzută, viteză scăzută de alimentare și adâncime mică de tăiere pentru aliaje dure. De exemplu: GH4033, selectați S800, F0.08 și o adâncime de tăiere de 0,5 mm;
3) Aliajul de titan trebuie selectat cu viteză scăzută, viteză ridicată de alimentare și adâncime mică de tăiere. De exemplu, pentru Ti6, selectați S400, F0.2 și o adâncime de tăiere de 0,3 mm. Luând ca exemplu prelucrarea unei anumite piese: materialul este K414, care este un material foarte dur. După mai multe teste, a fost selectat în cele din urmă ca S360, F0.1, și o adâncime de tăiere de 0,2 pentru a produce o piesă calificată.
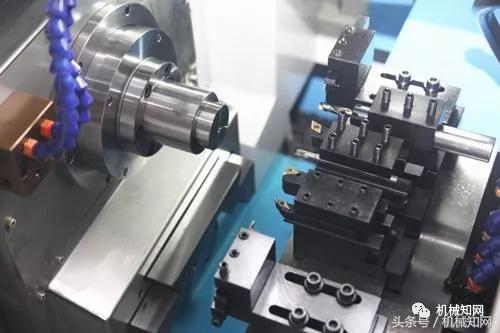
2,Tehnica de aliniere a cuțitului este împărțită în instrument de aliniere a cuțitului și aliniere directă a cuțitului. Majoritatea strungurilor din fabrica noastră nu au dispozitiv de aliniere a sculelor și necesită aliniere directă a sculelor. Următoarele tehnici de aliniere a sculelor se referă la alinierea directă a sculelor.
În primul rând, selectați centrul feței capătului drept al piesei ca punct de aliniere a uneltei și setați-l ca punct zero. După ce mașina unelte revine la originea, fiecare unealtă care trebuie utilizată este aliniată cu centrul feței capătului drept al piesei ca punct zero; Atunci când unealta intră în contact cu fața de capăt dreaptă, introduceți Z0 și faceți clic pe butonul de măsurare. Valoarea de compensare a uneltei va înregistra automat valoarea măsurată, indicând faptul că axa Z este aliniată corect. Axa X este pentru tăiere de încercare, iar atunci când utilizați unealta pentru a regla cercul exterior al piesei, introduceți x20 pentru a măsura valoarea cercului exterior al piesei care este reglată (cum ar fi x fiind 20mm). Faceți clic pe butonul de măsurare, iar valoarea de compensare va înregistra automat valoarea măsurată. În acest punct, axa X este, de asemenea, aliniată corect; Această metodă de aliniere a sculelor, chiar dacă mașina uneltei este oprită, nu va schimba valoarea de aliniere după pornire și repornire. Este potrivită pentru producția pe scară largă și pe termen lung a aceleiași piese, în timpul căreia strungul nu trebuie să fie re-aliniat.
3,depanare abilități: După programarea și alinierea uneltei, piesele trebuie să fie testate și depanate. În scopul de a preveni erorile în programul și alinierea uneltei, care poate provoca accidente de coliziune, ar trebui mai întâi să efectueze simularea cursei goale prelucrare. În sistemul de coordonate al mașinii unelte, scula ar trebui să fie mutată la dreapta de 2-3 ori lungimea totală a piesei în ansamblu; Apoi începeți simularea prelucrării. După terminarea prelucrării simulate, confirmați că programul și alinierea sculei sunt corecte și apoi începeți prelucrarea pieselor. După prelucrarea primei piese a piesei este prelucrată, verificați singur și confirmați că este calificată, apoi găsiți un inspector dedicat pentru a o inspecta. Numai după ce inspectorul dedicat confirmă că este calificat poate fi finalizată depanarea.
4,După ce prima piesă de tăiere de probă este finalizată, piesele prelucrate trebuie să fie produse în masă. Cu toate acestea, calificarea primei piese nu înseamnă că întregul lot de piese va fi calificat, deoarece în timpul prelucrării, diferite materiale de prelucrare vor cauza uzură scula. Materialele moi de prelucrare au mai puțină uzură scula, în timp ce materialele dure de prelucrare au uzură mai rapidă scula. Prin urmare, în timpul prelucrării, este necesar să efectueze inspecții frecvente și creșterea sau scăderea valorii de compensare a sculei pentru a asigura calificarea pieselor.
Luând o anumită parte ca exemplu, materialul de prelucrare este K414, cu o lungime totală de prelucrare de 180mm. Datorită materialului extrem de dur, uzura uneltei este foarte rapidă în timpul prelucrării. De la punctul de pornire până la punctul final, se va genera o ușoară abatere de 10-20mm din cauza uzurii uneltei. Prin urmare, trebuie să adăugăm manual o ușoară abatere de 10-20mm în program pentru a asigura calificarea piesei.
Pe scurt, principiul de bază al prelucrării este mai întâi mașina dură, eliminarea excesului de material din piesa de prelucrat și apoi mașina de precizie; Vibrațiile trebuie evitate în timpul prelucrării; Există multe motive pentru a evita vibrațiile cauzate de deformarea termică în timpul prelucrării pieselor de prelucrat, care pot fi datorate sarcinii excesive; Poate fi rezonanță între mașina unealtă și piesa de prelucrat, sau rigiditate insuficientă a mașinii unelte sau poate fi cauzată de pasivarea uneltei. Putem reduce vibrațiile prin următoarele metode:; Reduceți viteza de alimentare laterală și adâncimea de prelucrare, verificați dacă prinderea piesei de prelucrat este sigură, creșteți viteza sculei, ceea ce poate reduce rezonanța prin scăderea vitezei. În plus, verificați dacă este necesar să înlocuiți scula cu una nouă.
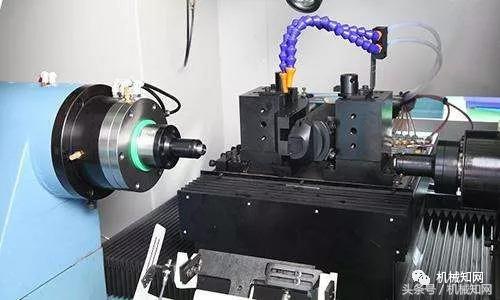
5,Experiența de prevenire a coliziunilor dintre mașini-unelte dăunează foarte mult precizia mașinilor-unelte, iar impactul variază pentru diferite tipuri de mașini-unelte. În general vorbind, are un impact mai mare asupra mașinilor-unelte cu rigiditate slabă. Astfel, pentru strungurile CNC de înaltă precizie, coliziunile trebuie eliminate absolut. Atâta timp cât operatorul este atent și stăpânește anumite metode anti-coliziune, coliziunile pot fi prevenite și evitate complet.
Principalul motiv al coliziunilor:
Una este eroarea de intrare a diametrului și lungimii uneltei de tăiere;
În al doilea rând, există erori în introducerea dimensiunilor și a altor dimensiuni geometrice conexe ale piesei de prelucrat, precum și erori în poziționarea inițială a piesei de prelucrat;
În al treilea rând, sistemul de coordonare a piesei de prelucrat al mașinii-unelte este setat incorect sau punctul zero al mașinii-unelte este resetat în timpul procesului de prelucrare, rezultând modificări. Coliziunile mașinii-unelte apar în principal în timpul mișcării rapide a mașinii-unelte, iar pericolele unor astfel de coliziuni sunt, de asemenea, cele mai mari, care ar trebui absolut evitate.
Astfel, operatorii trebuie să acorde o atenție deosebită etapei inițiale de execuție a programului și de înlocuire a uneltei. Dacă programul este editat incorect sau diametrul și lungimea uneltei sunt introduse incorect, este posibil să apară coliziuni. În etapa finală a programului, dacă secvența acțiunii de retragere a axei CNC este incorectă, pot apărea și coliziuni.
Pentru a evita coliziunile menționate mai sus, operatorul trebuie să utilizeze pe deplin funcțiile caracteristicilor faciale ale acestora atunci când operează mașina uneltei, să observe dacă există mișcări anormale, scântei, zgomot, sunete anormale, vibrații sau mirosuri arse. Dacă se constată vreo situaţie anormală, programul trebuie oprit imediat. Maşina uneltei poate continua să funcţioneze numai după rezolvarea problemei patului.
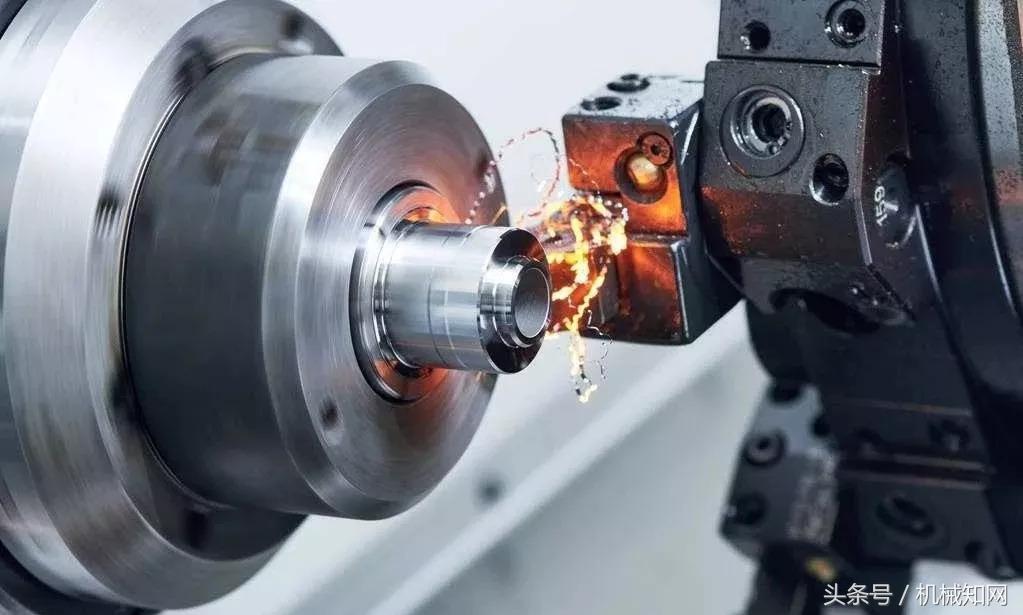
Pe scurt, stăpânirea abilităților de operare ale mașinilor-unelte CNC este un proces treptat și nu poate fi realizată peste noapte. Se bazează pe stăpânirea funcționării de bază a mașinilor-unelte, cunoștințele fundamentale ale prelucrării mecanice și cunoștințele de bază de programare. Abilitățile de operare ale mașinilor-unelte CNC nu sunt fixe, ele necesită operatorului să-și utilizeze pe deplin imaginația și abilitățile hands-on într-o combinație organică, care este o muncă inovatoare.