Strungul de control numeric este o mașină unealtă automatizată de înaltă precizie și de înaltă eficiență. Utilizarea strungului de control numeric poate îmbunătăți eficiența procesării și poate crea mai multă valoare. Apariția strungului de control numeric a permis întreprinderilor să scape de tehnologia de prelucrare învechită. Tehnologia de prelucrare a strungului de control numeric este similară cu cea a strungului obișnuit. Cu toate acestea, deoarece strungul de control numeric este o prindere unică și prelucrare automată continuă pentru a finaliza toate procesele de strunjire, trebuie remarcate următoarele aspecte.
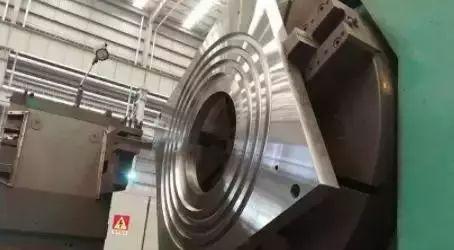
Alegeți în mod rezonabil parametrii de tăiere
Pentru tăierea eficientă a metalelor, materialul prelucrat, sculele de tăiere și condițiile de tăiere sunt cele trei elemente majore. Acestea determină timpul de prelucrare, durata de viață a sculelor și calitatea prelucrării. Metoda de prelucrare eficientă din punct de vedere economic trebuie să fie o alegere rezonabilă a condițiilor de tăiere.
Cele trei elemente ale condițiilor de tăiere: viteza de tăiere, rata de alimentare și adâncimea de tăiere cauzează în mod direct deteriorarea sculei. Odată cu creșterea vitezei de tăiere, temperatura marginii de tăiere va crește, rezultând uzură mecanică, chimică și termică. Creșterea vitezei de tăiere cu 20% va reduce durata de viață a sculelor cu jumătate.
Relația dintre condițiile de alimentare și uzura uneltelor apare într-un interval foarte mic. Dar cu o rată mare de alimentare, temperatura de tăiere crește și există uzură semnificativă mai târziu. Are un impact mai mic asupra uneltei de tăiere decât viteza de tăiere. Deși impactul adâncimii de tăiere asupra sculelor de tăiere nu este la fel de semnificativ ca viteza de tăiere și viteza de alimentare, în tăierea micro adâncime, materialul tăiat produce un strat călit, care afectează, de asemenea, durata de viață a sculei.
Utilizatorii trebuie să aleagă viteza de tăiere în funcție de materialul prelucrat, duritatea, starea de tăiere, tipul materialului, rata de alimentare, adâncimea de tăiere etc.
Selectarea celor mai potrivite condiții de prelucrare se bazează pe acești factori. Uzura regulată și stabilă pentru a obține durata de viață este condiția ideală.
Cu toate acestea, în operațiunile practice, alegerea duratei de viață a sculei este legată de uzura sculei, modificările dimensiunilor prelucrate, calitatea suprafeței, zgomotul de tăiere, căldura prelucrării și alți factori. Atunci când se stabilesc condițiile de prelucrare, este necesar să se efectueze cercetări bazate pe situația reală. Pentru materiale dificil de prelucrat, cum ar fi oțelul inoxidabil și aliajele rezistente la căldură, se pot utiliza lichizi de răcire sau lame cu rigiditate bună.
Cum se determină cele trei elemente ale prelucrării de tăiere
Cum să selectați corect aceste trei elemente este un conținut major al cursului privind principiile de tăiere a metalelor, iar principiile de bază pentru selectarea acestor trei elemente sunt:
(1) Viteza de tăiere (viteza liniei, viteza circumferențială) V (m/min)
Pentru a selecta rotațiile axului pe minut, este necesar să știți mai întâi cât de mult trebuie luată viteza liniei de tăiere V. Alegerea V depinde de materialul sculei, materialul piesei de prelucrat, condițiile de prelucrare etc.
Material unelte:
Aliaj dur, V poate atinge o valoare ridicată, în general peste 100 de metri pe minut, iar parametrii tehnici sunt de obicei furnizați la achiziționarea lamelor:
Câte viteze de linie pot fi selectate atunci când prelucrează ce materiale. Oțel de mare viteză: V poate fi obținut numai la un nivel relativ scăzut, în general nu depășește 70 de metri pe minut și, în cele mai multe cazuri, sub 20-30 de metri pe minut.
Materialul piesei de lucru:
Duritate ridicată, valoare V scăzută; fonta, cu o valoare de V scăzută, poate fi utilizată pentru scule de tăiere din aliaj dur la o viteză de 70-80 metri pe minut; Oțelul cu emisii reduse de carbon poate avea o valoare V de peste 100 de metri pe minut, în timp ce metalele neferoase pot avea o valoare V mai mare (100-200 de metri pe minut). Oțelul și oțelul inoxidabil ar trebui să aibă o valoare V mai mică.
Condiții de prelucrare:
Prelucrare dură, luați o valoare V mai mică; Prelucrare de precizie, cu o valoare V mai mare. Sistemul de rigiditate al mașinilor-unelte, pieselor de prelucrat și sculelor de tăiere este slab, iar V este luat la fel de scăzut. Dacă programul CNC utilizează S ca viteză a arborelui pe minut, atunci S (viteza arborelui pe minut) trebuie calculată pe baza diametrului piesei de prelucrat și a vitezei liniei de tăiere V, unde S=V (viteza liniei de tăiere) * 1000/(3.1416 * diametrul piesei de prelucrat). Dacă programul CNC utilizează o viteză constantă a liniei, S poate utiliza direct viteza liniei de tăiere V (metri/minut)
(2) Rata furajelor (rata furajelor)
F depinde în principal de cerințele de rugozitate a suprafeței prelucrării pieselor de prelucrat. Când prelucrarea de precizie, cerințele de suprafață sunt ridicate, iar cantitatea de tăiere ar trebui să fie mică: 0,06 ~ 0,12 mm / ax pe rotație. Când prelucrarea dură, poate fi mai mare. Depinde în principal de rezistența uneltei, care poate fi în general peste 0,3. Când unghiul principal de greblă al uneltei este mare, rezistența uneltei este slabă, iar rata de alimentare nu poate fi prea mare. În plus, trebuie luate în considerare și puterea mașinii uneltei și rigiditatea piesei de prelucrat și a uneltei de tăiere. Programul CNC utilizează două unități de viteză de alimentare: mm/min și mm/ax pe rotație. Unitățile utilizate mai sus sunt toate mm/ax pe rotație. Dacă se utilizează mm/min, formula poate fi utilizată pentru a-l converti: viteză de alimentare pe minut = viteză de alimentare pe rotație * rotații ale ax pe minut
(3) Adâncime de tăiere (adâncime de tăiere)
În cazul prelucrării de precizie, este în general recomandabil să se ia o valoare de rază de 0,5 sau mai mică. În timpul prelucrării brute, se determină în funcție de starea piesei de prelucrat, a uneltei și a mașinii unelte. În general, strunguri mici (cu un diametru maxim de prelucrare de 400 mm sau mai puțin) sunt utilizate pentru a transforma oțel 45 # într-o stare normalizată, iar adâncimea uneltei de tăiere radială nu este în general mai mare de 5mm. În plus, trebuie remarcat faptul că dacă viteza arborelui strungului adoptă reglarea obișnuită a vitezei de frecvență variabilă, atunci când viteza arborelui este foarte scăzută pe minut (sub 100-200 rotații pe minut), puterea de ieșire a motorului va scădea semnificativ, iar adâncimea de tăiere și rata de alimentare pot fi atinse doar foarte puțin în acest moment.
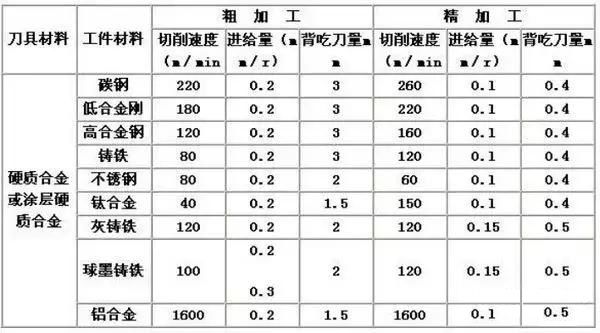
Selectarea rezonabilă a uneltelor de tăiere
La strunjirea dură, este necesar să alegeți unelte de tăiere cu rezistență ridicată și durabilitate bună pentru a satisface cerințele de tăiere spate mare și viteza mare de alimentare în timpul strunjirii dure.
La prelucrarea de precizie, este necesar să alegeți unelte cu precizie ridicată și durabilitate bună pentru a asigura precizia de prelucrare necesară.
Pentru a reduce timpul de schimbare a sculelor și pentru a facilita alinierea sculelor, trebuie utilizate cât mai mult cuțite prinse de mașină și lame prinse de mașină.
Alegeți în mod rezonabil corpurile de iluminat
1. Încercați să utilizați corpuri de fixare universale pentru a prinde piesele de prelucrat și a evita utilizarea corpurilor de fixare specializate;
2. Aliniați reperele de poziționare ale pieselor pentru a reduce erorile de poziționare.
Determinați calea de procesare
Traseul de prelucrare se referă la traiectoria de mișcare și direcția sculei în raport cu piesa în timpul procesului de Prelucrare CNC.
1. Ar trebui să fie în măsură să asigure exactitatea prelucrării și rugozitatea suprafeței;
2. Traseul de prelucrare trebuie scurtat cât mai mult posibil pentru a reduce timpul de inactivitate al sculei.
Relația dintre ruta de prelucrare și alocația de prelucrare
În prezent, în absența utilizării pe scară largă a strungurilor CNC, ar trebui să fie aranjată, în general, o reducere excesivă a golului, în special reducerea care conține straturi de piele tare forjate sau turnate, pentru prelucrarea pe strunguri obișnuite. Dacă este necesar să utilizați un strung CNC pentru prelucrare, trebuie acordată atenție aranjamentului flexibil al programului.
Puncte cheie pentru instalarea dispozitivelor de fixare
În prezent, conexiunea dintre mandrina hidraulică și cilindrul hidraulic de prindere este realizată printr-o tijă de tragere. Punctele cheie ale prinderii mandrinei hidraulice sunt următoarele: în primul rând, utilizați un mâner pentru a elimina piulița de pe cilindrul hidraulic, scoateți tubul de tragere și extrageți-l din partea din spate a arborelui. Apoi, utilizați un mâner pentru a elimina șurubul de fixare a mandrinei pentru a elimina mandrina.