Editorul va organiza multe metode practice de cunoștințe și știri fierbinți pentru toată lumea. Vă rugăm să acordați mai multă atenție și vă va fi prezentat conținut mai bun
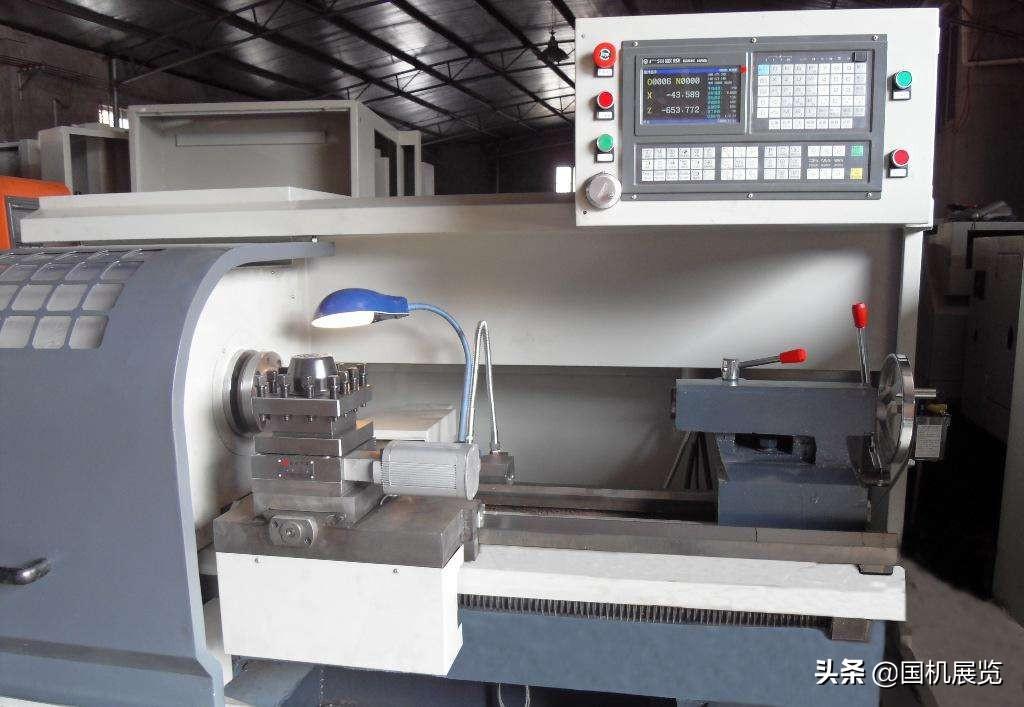
Pe un strung CNC pot fi prelucrate patru fire standard: metric, inch, modul și radial. Indiferent de tipul de filet este prelucrat, trebuie menținută o relație strictă de mișcare între fusul strung și sculă: adică, pentru fiecare rotație a fusului (adică, o rotație a piesei de prelucrat), scula trebuie să se deplaseze uniform cu o distanță de plumb (a piesei de prelucrat). Analizând firele obișnuite, ne propunem să îmbunătățim înțelegerea lor pentru a le procesa mai bine.
1,Analiza dimensională a firelor obișnuite
Prelucrarea filetelor obișnuite cu strunguri CNC necesită o serie de dimensiuni, iar calcularea dimensiunilor și analiza necesară pentru prelucrarea filetelor obișnuite includ în principal următoarele două aspecte:
1. Diametrul piesei de prelucrat înainte de prelucrarea filetului
Având în vedere extinderea profilului filetului în timpul prelucrării filetului, diametrul piesei de prelucrat înainte de prelucrarea filetului este d / d-0,1p, ceea ce reprezintă reducerea pasului filetului cu 0,1 din diametrul mai mare al filetului. În general, pe baza capacității de deformare a materialului, diametrul mai mic este luat ca 0,1 la 0,5 comparativ cu diametrul mai mare al filetului.
2. Viteza de alimentare a prelucrării filetului
Cantitatea de inserare a filetului se poate referi la diametrul inferior al filetului, care este poziția finală de tăiere a tăietorului filetului.
Diametrul firului este: diametru mare -2 ori înălțimea dinților; Înălțimea dinților = 0,54p (p este pas)
Rata de alimentare pentru prelucrarea filetului trebuie redusă continuu, iar rata specifică de alimentare trebuie selectată pe baza uneltei și a materialului de lucru.
2,Asamblarea și alinierea instrumentelor obișnuite de tăiere a filetului
Dacă unealta de tăiere este instalată prea înaltă sau prea joasă sau prea înaltă, atunci când tăierea atinge o anumită adâncime, fața din spate a uneltei de tăiere va apăsa pe piesa de prelucrat, crescând frecarea și chiar îndoind piesa de prelucrat, cauzând fenomenul mușcării uneltei; Dacă așchiul este prea scăzut, este dificil să descărcați așchiile. Direcția forței radiale a uneltei de strunjire este în centrul piesei de prelucrat. În plus, distanța dintre șurubul transversal și piulița este prea mare, determinând creșterea automată a adâncimii de tăiere, ridicând astfel piesa de prelucrat și cauzând mușcătura uneltei. În acest punct, înălțimea uneltei de strunjire trebuie reglată în timp util pentru a se asigura că vârful său este la aceeași înălțime cu axa piesei de prelucrat (scula poate fi aliniată cu vârful suportului). În timpul prelucrării dure și semi-precizie, poziția vârfului sculei este cu aproximativ 1% d mai mare decât centrul piesei de prelucrat (d reprezintă diametrul piesei prelucrate).
Piesa de prelucrat nu poate fi strânsă ferm, iar rigiditatea sa nu poate rezista forței de tăiere în timpul strunjirii, rezultând o deformare excesivă și schimbarea înălțimii centrale între scula de tăiere și piesa de prelucrat (piesa de prelucrat este ridicată), cauzând o creștere bruscă a adâncimii de tăiere și mușcătura uneltei. În acest moment, piesa de prelucrat trebuie strânsă ferm, iar vârfurile de coadă pot fi utilizate pentru a crește rigiditatea piesei de prelucrat.
Metodele de aliniere a filetelor obișnuite includ tăierea de încercare și alinierea automată cu un dispozitiv de aliniere a uneltei. Scula poate fi utilizată direct pentru alinierea de încercare a tăierii, sau punctul zero al piesei de prelucrat poate fi setat cu G50 și punctul zero al piesei de prelucrat poate fi setat cu mișcarea piesei de prelucrat pentru aliniere. Cerințele pentru alinierea sculelor în prelucrarea filetului nu sunt foarte ridicate, mai ales în direcția z, unde nu există restricții stricte privind alinierea sculelor, care pot fi determinate în funcție de cerințele de prelucrare de programare.
3,Programarea și prelucrarea firelor obișnuite
În strungurile CNC actuale, există în general trei metode de prelucrare pentru tăierea filetului: metoda de tăiere dreaptă g32, metoda de tăiere dreaptă g92 și metoda de tăiere oblică g76. Datorită diferitelor metode de tăiere și metode de programare, erorile de prelucrare sunt, de asemenea, diferite. Trebuie să analizăm cu atenție operațiunile noastre și să ne străduim să producem piese de înaltă precizie.
1. Metoda de tăiere directă G32 are o forță mare de tăiere și dificultate în tăiere datorită funcționării simultane a ambelor muchii de tăiere. Prin urmare, ambele muchii de tăiere sunt predispuse la uzură în timpul tăierii. Atunci când tăiați fire cu pas mai mare, datorită adâncimii de tăiere mai mari, uzura lamei este mai rapidă, rezultând erori în diametrul pas al filetului; Cu toate acestea, precizia sa de prelucrare este relativ ridicată, astfel încât este utilizat în general pentru prelucrarea filetului cu pas mic. Datorită mișcării sculei și tăierii care sunt finalizate prin programare, programul de prelucrare este relativ lung; Datorită uzurii ușoare a lamei, este necesar să se măsoare frecvent în timpul prelucrării.
2. Metoda de tăiere directă g92 simplifică programarea și îmbunătățește eficiența în comparație cu instrucțiunile g32.
3. Metoda de tăiere oblică G76, datorită prelucrării marginilor sale cu o singură față, este predispusă la deteriorarea și uzura lamei de prelucrare, rezultând suprafețe filetate neuniforme și modificări în unghiul vârfului sculei, ducând la o precizie slabă a profilului dinților. Cu toate acestea, datorită funcționării lamei cu o singură față, sarcina sculei este relativ mică, îndepărtarea așchiilor este ușoară, iar adâncimea de tăiere scade. Prin urmare, această metodă de prelucrare este, în general, potrivită pentru prelucrarea filetelor cu pas mare. Datorită îndepărtării ușoare a cipului și condițiilor bune de prelucrare a lamei, această metodă de prelucrare este mai convenabilă în situațiile în care nu este necesară o precizie ridicată a filetului. La prelucrarea filetelor de înaltă precizie, se pot utiliza două tăieturi pentru a finaliza prelucrarea, mai întâi utilizând metoda de prelucrare G76 pentru strunjirea dură, apoi utilizând metoda de prelucrare G32 pentru strunjirea fină. Cu toate acestea, este important să rețineți că punctul de pornire al uneltei de tăiere ar trebui să fie precis, în caz contrar este ușor să faceți greșeli și să determinați piesele să fie dezmembrate.
4. După finalizarea prelucrării firului, calitatea firului poate fi evaluată prin observarea profilului firului și luarea măsurilor în timp util. Când creasta firului nu este îndreptată, creșterea cantității de tăiere a cuțitului va crește efectiv diametrul firului, ceea ce depinde de plasticitatea materialului. Când creasta a fost ascuțită, creșterea cantității de tăiere a cuțitului va reduce proporțional diametrul. Pe baza acestei caracteristici, cantitatea de tăiere a firului trebuie tratată corect pentru a preveni resturile.
4,Inspecția firelor obișnuite
Pentru filetele standard generale, pentru măsurare sunt utilizate măsurătoare inele filetate sau mufe. La măsurarea filetelor externe, dacă filetul; Trecând prin capăt"; Indicatorul inelului se rotește cu precizie și; End to End"; Dacă manometrul inelului nu poate fi înșurubat, indică faptul că filetul prelucrat îndeplinește cerințele, în caz contrar este necalificat. Atunci când măsurați filetele interne, utilizați un indicator de filet și măsurați utilizând aceeași metodă. Pe lângă măsurarea cu măsurători cu inele de filet sau cu măsurători de priză, pot fi utilizate și alte instrumente de măsurare pentru măsurare.Utilizați un micrometru de filet pentru a măsura diametrul pas firului, utilizați un cleme vernier grosime dinților pentru a măsura diametrul pas firului trapezoidal, grosimea dinților și diametrul pas dinților și utilizați un ac de măsurare pentru a măsura diametrul pas firului în conformitate cu metoda de măsurare a trei ace.