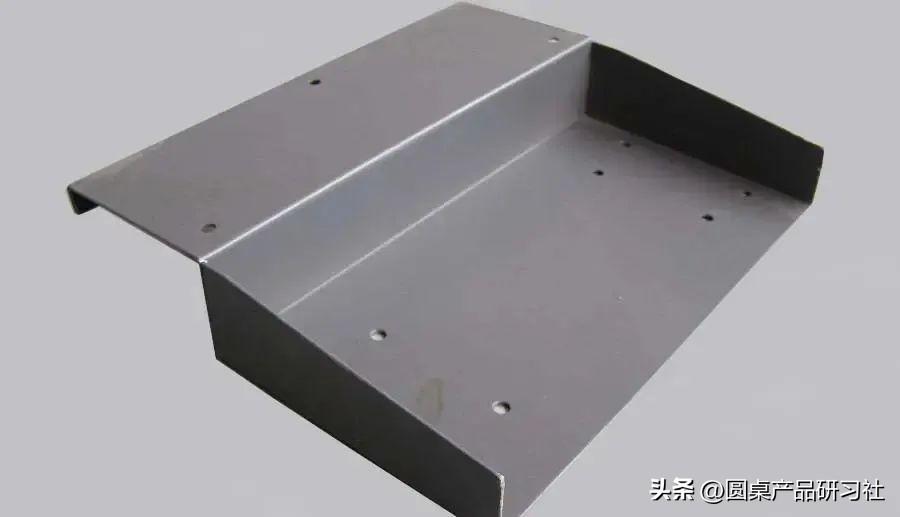
1,Pliere pat conținut de procesare: 1. L pliere este împărțită în 90 de grade pliere și non 90 de grade pliere în funcție de unghi.
În funcție de prelucrare, acesta poate fi împărțit în prelucrare generală (L>V/2) și prelucrare specială (L 1> Mucegaiul este selectat în funcție de material, grosimea plăcii și unghiul de formare. 2> Principiul încrederii 1) Pe baza principiului a două reguli de poziționare spate și poziționare în funcție de forma piesei de prelucrat. 2) Atunci când poziționați un ecartament spate, acordați atenție abaterii și asigurați-vă că acesta este pe aceeași linie centrală ca dimensiunea de îndoire a piesei de prelucrat. 3) Atunci când îndoiți pliuri mici, este mai bine să le procesați în poziția inversă. 4) Este mai bine să setați regulile spre spate și spre mijloc. (Atunci când se sprijină de poziție, nu este ușor pentru reglarea din spate să se ridice) 5) Este mai bine să fiți aproape de marginea poziției și de reglarea din spate. 6) Este mai bine să vă sprijiniți pe partea lungă. 7) Utilizați dispozitive de fixare pentru a ajuta la poziționare (poziționarea neregulată a marginilor înclinate). 3> Precauţii 1. Trebuie acordată atenție metodei de poziționare în timpul procesării și modului standardizat de mișcare între diferitele metode de procesare a poziționării. 2. Când matrița este asamblată, trebuie îndoită și trasă înapoi pentru a preveni deformarea piesei de prelucrat în timpul îndoirii. 3. Atunci când îndoiți piese de prelucrat mari intern, datorită formei mari a piesei de prelucrat și a zonei mici de îndoire, este dificil ca instrumentul de tăiere și zona de îndoire să coincidă, rezultând dificultăți în poziționarea piesei de prelucrat sau deteriorarea piesei de prelucrat îndoite. Pentru a evita situația de mai sus, se poate adăuga un punct de poziționare în direcția longitudinală a prelucrării, astfel încât prelucrarea să poată fi poziționată din două direcții, făcând poziționarea prelucrării convenabilă și îmbunătățind siguranța prelucrării, evitând deteriorarea pieselor de prelucrat și sporind eficiența producției. 2. N-fold necesită diferite metode de prelucrare în funcție de formă. La îndoire, dimensiunile interne ale materialului ar trebui să fie mai mari de 4MM, iar dimensiunea dimensiunii X este limitată de forma matriței. Dacă dimensiunea din interiorul materialului este mai mică de 4MM, trebuie utilizate metode speciale pentru prelucrare. 1> Alegeți matrița pe baza grosimii materialului, dimensiunii, materialului și unghiului de îndoire. 2> Principiul încrederii 1) Asigurați-vă că piesa de prelucrat nu interferează cu scula 2) Asigurați-vă că unghiul de poziționare este puțin mai mic de 90 de grade. 3) Cel mai bine este să utilizați două reguli de poziționare spate, cu excepția circumstanțelor speciale. 3> Precauţii 1) După îndoirea L, unghiul trebuie menținut la sau puțin mai mic de 90 de grade pentru a facilita prelucrarea și poziționarea. 2) În timpul celui de-al doilea proces de pliere, este necesar să se alinieze poziția cu suprafața de prelucrare ca centru. 3. Îndoirea Z, cunoscută și sub numele de diferență de segment, se referă la îndoirea unui pozitiv și unul negativ. Împărțiți diferența segmentului de margine oblică și diferența segmentului de margine dreaptă în funcție de unghi. Dimensiunea minimă pentru prelucrarea îndoirii este limitată de matrița de prelucrare, în timp ce dimensiunea maximă de prelucrare este determinată de forma mașinii de prelucrare. În general, atunci când dimensiunea internă a materialului pliat Z este mai mică de 3,5T, se utilizează procesarea matriței segmentate. Când este mai mare de 3,5T, se utilizează metode normale de procesare. 1> Principiul încrederii 1) Poziționare convenabilă și stabilitate bună. 2) În general, poziționarea este aceeași cu pliul L. 3) Poziționarea secundară necesită ca piesa prelucrată să fie spălată cu matrița inferioară. 2> Precauţii 1) Unghiul de prelucrare al pliului L trebuie să fie în poziție, în general necesar să fie între 89,5-90 de grade. 2) Atunci când trageți înapoi în conformitate cu specificațiile ulterioare, trebuie acordată atenție deformării piesei de prelucrat. 3) Ordinea de prelucrare trebuie să fie corectă. 4) Pentru prelucrarea specială, se pot utiliza următoarele metode: Metoda de separare a liniei centrale (prelucrare excentrică) Prelucrarea V mică (necesită creșterea coeficientului de îndoire) Formare ușor de modelat Măcinarea mucegaiului inferior 4. pliere inversă și aplatizare, cunoscută și sub numele de compresie a marginilor. Etapele de prelucrare pentru marginile moarte sunt: 1. Îndoiți și introduceți mai întâi la o adâncime de aproximativ 35 de grade. Apoi se aplatizează și se formează până când este plat și strâns atașat. 1> Metoda de selecție a modelului Selectați lățimea canelurii V a matriței inferioare cu o adâncime de 30 de grade în funcție de 5-6 ori grosimea materialului și alegeți matrița superioară în funcție de situația specifică de prelucrare a marginilor moarte. 2> Precauţii Atunci când dimensiunea de prelucrare a marginii moarte este relativ lungă, marginea aplatizată poate fi pliată mai întâi într-un unghi ridicat și apoi aplatizată. Pentru marginile moarte mai scurte, se poate utiliza prelucrarea căptușelii. 5. hardware de presare utilizează un pat pliant pentru a presa și sigila componentele hardware, de obicei utilizând matrițe auxiliare, cum ar fi matrițe concave și corpuri de fixare pentru prelucrare. În general, există: piulițe de compresie, șuruburi de compresie, șuruburi de compresie și alte componente hardware. Precauţii de prelucrare: 1. Atunci când forma piesei de prelucrat trebuie evitată în timpul prelucrării, trebuie luate măsuri de evitare. 2. După prelucrare, este necesar să verificați dacă cuplul și forța îndeplinesc standardele și dacă hardware-ul și piesa de prelucrat sunt înclinate și strâns atașate. 3. După îndoire și presare, atunci când apăsați lângă mașina unealtă, acordați atenție evitării prelucrării și paralelismului matriței. 4. Dacă este umflat, este, de asemenea, important să rețineți că nu trebuie să existe fisuri pe marginea umflată, iar marginea umflată nu trebuie să iasă deasupra suprafeței piesei de prelucrat. 6. Conținutul de prelucrare a turnării ușoare include în general: mici diferențe, cârlige, poduri, pungi, arcuri sub presiune și unele forme neregulate. Principiul de proiectare al Easy Mold se referă la "Principiul de proiectare ușoară a matriței de tăiere cu laser" Ușor de modelat utilizează, în general, poziționarea post sau auto-poziționarea. Cel mai important lucru în procesarea conținutului de mai sus cu o matriță ușoară este că cerințele sale de funcționare și asamblare nu sunt afectate, iar aspectul este normal 2,Probleme comune și soluții în procesarea patului pliant: 1. Analiza cauzelor alunecării în timpul procesării: 1. Atunci când selectați o matriță de îndoire, o lățime V-canelură de (4-6) T este, în general, aleasă. Când dimensiunea curbei este mai mică de jumătate din lățimea canelurii V selectate, va apărea un fenomen de alunecare. 2. Slotul V selectat este prea mare 3. Prelucrarea proceselor Metoda soluției 1. Metoda deviației liniei centrale (prelucrare excentrică). Dacă dimensiunile interne ale materialului îndoit sunt mai mici de (4-6) T/2, compensați diferența cât mai mult posibil 2. Prelucrarea tampoanelor. 3. Îndoiți cu o canelură V mică și aplicați presiune cu o canelură V mare. 4. Alege un slot V mai mic. 2. Analiza motivelor pentru care lățimea de îndoire internă este mai îngustă decât lățimea standard a matriței: Datorită lățimii standard minime a matriței pliante fiind de 10MM, partea de prelucrare a îndoirii are o lățime mai mică de 10MM. Dacă este o curbă de 90 de grade, dimensiunea lungimii sale nu trebuie să fie mai mică de 2 (L+V/2)+T. Pentru acest tip de îndoire, matrița trebuie fixată pe scaunul matriței (cu excepția libertății nerestricționate în direcția ascendentă) pentru a evita deplasarea matriței, ceea ce poate cauza dezmembrarea piesei de prelucrat sau accidente de siguranță. Soluţie: 1> Creșteți dimensiunea (pentru a fi coordonată cu clientul), adică creșteți lățimea pliului interior. 2> Procesare ușor de modelat 3> Unelte de șlefuit (ceea ce duce la o creștere a costurilor de prelucrare) 3. Gaura este prea aproape de linia de îndoire, iar îndoirea va determina gaura pentru a trage materialul. Analiza motivelor pentru răsturnare: Presupunând că distanța dintre gaură și linia de îndoire este L, atunci când L<; La (4-6) T/2, gaura va trage materialul. În principal datorită forței de întindere în timpul procesului de îndoire, materialul suferă deformare, rezultând fenomenul de tragere și răsturnare. În conformitate cu lățimea standard existentă a canelurii matriței, valoarea minimă L pentru diferite grosimi ale plăcii este prezentată în tabelul următor: Soluţie: 1> Măriți dimensiunea și șlefuiți marginile pliate după formare. 2> Extindeți gaura la linia de îndoire (trebuie să nu aibă impact asupra aspectului sau funcției, iar clientul este de acord). 3> Prelucrarea liniilor de tăiere sau prelucrarea liniilor de presiune 4> Prelucrarea excentrică a mucegaiului 5> Modificați dimensiunea găurii 4. Analiza motivelor de deformare la punctul de extracție după îndoire datorită distanței mici L dintre marginea de extracție și linia de îndoire: Când L<; La (4-6) T/2, datorită contactului dintre desen și matrița inferioară, deformarea are loc în timpul procesului de îndoire datorită forței exercitate asupra desenului. Soluţie: 1> Taie sau apasă linia. 2> Modificați dimensiunea desenului. 3> Folosirea matrițelor speciale pentru prelucrare 4> Prelucrarea excentrică a mucegaiului 5. Analiza cauzelor deformării după aplatizarea marginii moarte lungi: Datorită marginii moarte lungi, acesta nu poate adera strâns atunci când este aplatizat, rezultând ca capătul său să se curbe după aplatizare. Această situație este strâns legată de poziția aplatizată, deci trebuie acordată atenție poziției aplatizate atunci când aplatizați Soluţie: 1> Înainte de a plia marginea moartă, mai întâi pliați colțul ridicat (așa cum se arată în diagramă), apoi aplatizați-l. 2> Aplatizare în mai multe etape: Apăsați capătul mai întâi pentru a îndoi marginea moartă în jos. Aplatizează rădăcinile. Atenție: Efectul de aplatizare este legat de abilitățile operaționale ale operatorului, astfel încât vă rugăm să acordați atenție situației reale în timpul aplatizării. 6. Analiza motivelor pentru fractura ușoară a tragerii podului de înaltă înălțime: 1> Datorită înălțimii ridicate a podului, materialul a fost grav întins, rezultând fracturi. 2> Colțurile matriței nu sunt lustruite sau nu sunt lustruite suficient. 3> Duritatea materialului este prea slabă sau corpul podului este prea îngust. Soluţie: 1> Extindeți gaura de proces pe partea laterală a fracturii. 2> Măreşte lăţimea podului. 3> Grind unghiul R al matriței și crește tranziția arcului. 4> Adăugaţi ulei lubrifiant pe puntea de aspiraţie. (Prin urmare, această metodă va face suprafața piesei de prelucrat murdară, astfel încât să nu poată fi utilizată pentru piese AL etc.) 7. Analiza motivelor pentru funcționarea dimensiunilor de prelucrare în timpul prelucrării ușoare a matriței: Datorită forței de compresie înainte exercitate asupra piesei de prelucrat în timpul procesului de prelucrare, piesa de prelucrat se deplasează înainte, rezultând o creștere a unghiului mic de greblă L din față. Soluţie: 1> Șlefuiți zonele umbrite din imagine. De obicei, diferența este făcută cât mai mult posibil. 2> Șlefuiți toate părțile de auto-poziționare ale matriței și comutați la poziționarea fixă. (După cum se arată în figura de mai jos) 8. Dimensiunea generală a materialului (referindu-se la desfășurare) este prea mică sau prea mare, ceea ce nu se potrivește cu suprafața circulară. Analiza cauzei: 1> Proiectul a fost lansat incorect. 2> Dimensiunea de tăiere este incorectă. Soluţie: Calculați abaterea alocată pentru fiecare curbă pe baza abaterii totale în direcția abaterii și a numărului de lame de îndoire. Dacă toleranța calculată de alocare se situează în intervalul de toleranță, piesa de prelucrat este acceptabilă. Dacă dimensiunea este prea mare, o canelură V mică poate fi utilizată pentru prelucrare. Dacă dimensiunea este prea mică, o canelură V mare poate fi utilizată pentru prelucrare. 9. Analiza motivelor deformării cauzate de expansiune sau potrivire liberă după perforarea și mortizarea găurilor: 1> Umflarea este cauzată de unghiul R al perforatorului de gaură fiind prea mic sau bavurile de pe flanșă fiind prea mari. 2> Potrivirea liberă se datorează extinderii inadecvate a găurii. 3> Deformarea poate fi cauzată de alinierea greșită a găurilor sau metoda incorectă de împerechere. Soluţie: 1> Alege un pumn cu un unghi R mare în schimb. Atenție: Freze în jurul găurii în timpul desenării găurilor și flanșării. 2> Creșteți presiunea, măriți și adânciți gaura de salată și folosiți un pumn cu un unghi R mare în schimb. 3> Metoda de excavare a motivelor pentru schimbarea metodei de împerechere și dezaliniere a găurilor. 10. Analiza cauzelor neclarității sau deformării piesei de prelucrat după presarea cu șurub: 1> În timpul prelucrării produsului, nu au existat piese de prelucrat plate sparte. 2> Forță inegală sau presiune excesivă pe suprafața inferioară a piesei de prelucrat. Soluţie: 1> Când apăsați șurubul, piesa de prelucrat trebuie să fie nivelată. 2> Fă un cadru de sprijin. 3> Reglează presiunea din nou. 4> Măriți intervalul de forță pe suprafața inferioară și scădeți intervalul de forță aplicat pe suprafața superioară. 11. Analiza motivelor neparalelismului dintre cele două părți după diferența de segment: 1> Mucegaiul nu a fost calibrat. 2> Garniturile superioare și inferioare ale mucegaiului nu sunt reglate corespunzător. 3> Selectarea suprafețelor de mucegai superioare și inferioare este diferită. Soluţie: 1> Calibrează matriţa. 2> Adăugați sau eliminați șireturile. (Pentru metode specifice de ajustare, consultați "Tehnologia de procesare a segmentului") 3> Mucegaiul e excentric. 4> Înlocuiți suprafața astfel încât suprafețele matrițelor superioare și inferioare să fie aceleași. 12. Analiza motivelor cutelor adânci de pe suprafața produsului: 1> Scanelura V a matriței inferioare este mică 2> Unghiul R al canelurii V în matrița inferioară este mic 3> Materialul e prea moale. Soluţie: 1> Folosind prelucrarea canelurilor V mari 2> Utilizarea unei matrițe cu un unghi R mare pentru prelucrare 3> Îndoirea materialului pernei (tablă de oțel pernă sau lipici Yuli) 13. Analiza cauzelor deformării în apropierea punctului de îndoire după îndoire: Mașina funcționează rapid în timpul procesului de îndoire, iar viteza de îndoire în sus a piesei de prelucrat în timpul deformării este mai mare decât viteza la care operatorul susține mișcarea piesei de prelucrat cu mâinile lor. Soluţie: 1> Reducerea vitezei de funcționare a mașinii 2> Creșteți viteza suportului de mână al operatorului. 14. Analiza cauzelor fisurării pieselor AL în timpul îndoirii: Datorită structurii unice de cristal a materialului AL, este predispus la fractură atunci când este îndoit în paralel cu direcția granulației. Soluţie: 1> La tăiere, luați în considerare rotirea materialului AL perpendicular pe direcția de îndoire (chiar dacă direcția de îndoire a materialului este perpendiculară pe bob). 2> Măriți unghiul R al matriței superioare.