Multe dintre profilele noastre de aluminiu necesită post-prelucrare după producția de extrudare, deoarece acestea trebuie să fie asamblate pentru scenarii de utilizare specială. O anumită precizie de asamblare este foarte mare, astfel încât este necesar să se reducă cantitatea de deformare a prelucrării. Există multe motive pentru deformarea profilelor din aliaj de aluminiu în timpul prelucrării de precizie, care sunt legate de materiale, forme de piese, standarde de producție și fabricație etc. Există în principal mai multe niveluri de deformare: deformare cauzată de stresul termic asupra embrionului, deformare cauzată de forța de tăiere și căldura de tăiere și deformare cauzată de forța de strângere.
Contramăsuri tehnologice de prelucrare pentru reducerea deformării prelucrării
1. Reducerea stresului termic al billet
Utilizarea soluțiilor naturale sau artificiale de îmbătrânire și vibrații poate elimina parțial stresul termic al golului. Prelucrarea prealabilă este, de asemenea, o tehnică practică și fezabilă de prelucrare. Pentru părul dur și dur brut, datorită capacității lor mari, există, de asemenea, deformări semnificative după prelucrare. Dacă părțile inutile ale golului sunt prelucrate în avans și capacitatea fiecărei părți este redusă, nu numai că poate reduce deformarea de procesare a fluxului de proces ulterior, ci poate elibera și o anumită tensiune termică după ce a fost prelucrată în avans și lăsată pentru o perioadă de timp.
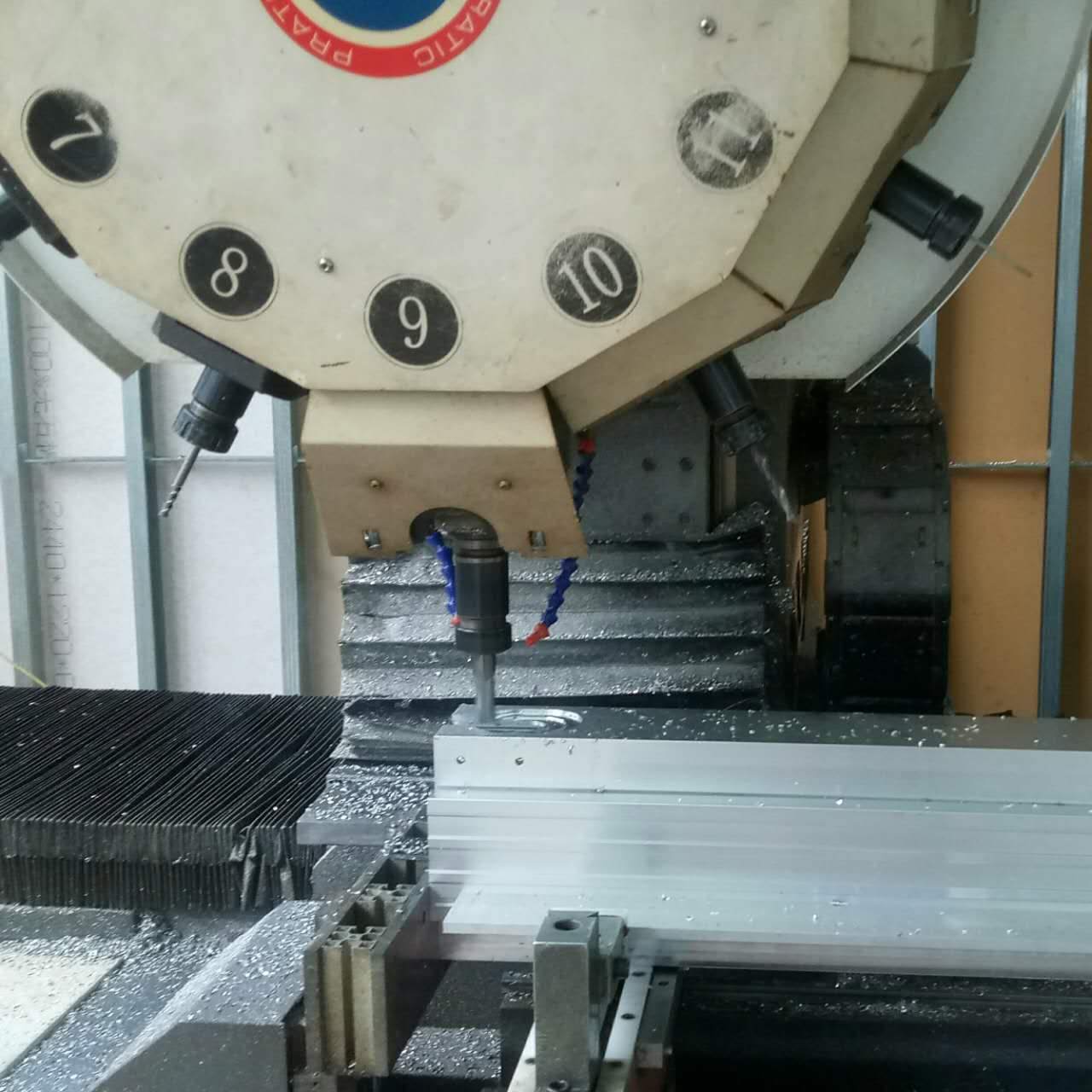
2. Îmbunătățirea capacității de tăiere a uneltelor de tăiere
Materialele prime și parametrii geometrici ai sculelor de tăiere au un impact semnificativ asupra forței de tăiere și căldurii de tăiere.Selectarea corectă a sculelor de tăiere este deosebit de importantă pentru reducerea deformării în timpul prelucrării de precizie a pieselor din aliaj de aluminiu.
(1) Selectați eficient parametrii principali ai geometriei sculei.
① Unghi anterior: Sub standardul de menținere a rezistenței la compresie a marginii de tăiere, unghiul frontal ar trebui selectat moderat pentru a fi mai mare. Pe de o parte, poate lustrui marginea ascuțită de tăiere și, pe de altă parte, poate reduce deformarea de tăiere, face suprafața de frezare completă și, astfel, reduce forța de tăiere și temperatura de tăiere. Nu utilizaţi unelte cu unghi negativ de greblă.
② Colțul din spate: Dimensiunea colțului din spate are un impact semnificativ asupra deteriorării marginii de tăiere din spate și asupra performanței de procesare. Grosimea de tăiere este criteriul cheie pentru selectarea colțului din spate. În timpul frezării brute, datorită vitezei mari de tăiere, sarcinii mari de tăiere și valorii ridicate a căldurii, este necesar să se stabilească un standard bun pentru disiparea căldurii conductelor termice a uneltei de tăiere. Prin urmare, trebuie selectat un unghi de spate mai mic. La frezarea de precizie, este necesar ca muchia de tăiere să fie ascuțită pentru a atenua frecarea dintre muchia de tăiere spate și suprafața prelucrată, pentru a reduce deformarea ductilă și, prin urmare, colțul din spate ar trebui selectat pentru a fi mai mare.
② Unghi spiral: Pentru a asigura tăierea stabilă și a reduce forța de tăiere, unghiul spiralei trebuie selectat cât mai mare posibil.
② Unghiul principal de înclinare: Reducerea moderată a unghiului principal de înclinare poate îmbunătăți standardul de disipare a căldurii conductei termice și reduce temperatura medie în zona de prelucrare de precizie a profilului de aluminiu.
(2) Îmbunătățirea construcției uneltelor.
① Reduceți numărul de dinți pe unealta de tăiere și creșteți spațiul din interiorul compartimentului de cipuri. Datorită deformării plastice semnificative a materiilor prime turnate sub presiune și deformării de tăiere în timpul procesării, este necesar un spațiu mare în interiorul camerei de așchii. Prin urmare, raza inferioară a camerei de așchii ar trebui să fie mare, iar numărul de dinți de pe scula de tăiere ar trebui să fie relativ mic.
② Tehnica fină de ascuțire a dinților. Valoarea rugozității suprafeței marginii de tăiere laterale trebuie să fie mai mică decât Ra = 0,4um. Înainte de a aplica un nou cuțit, trebuie folosită o piatră fină de măcinare pentru a măcina ușor lama laterală de două ori în față și în spate pentru a îndepărta orice bavuri rămase și urme ușoare dentare din dinții tehnici de ascuțire. Astfel, nu numai că căldura de tăiere poate fi redusă, dar deformarea de tăiere este, de asemenea, relativ mică.
② Controlați strict specificațiile de daune ale sculelor de tăiere. După deteriorarea uneltei, valoarea rugozității piesei de prelucrat crește, temperatura de tăiere crește și deformarea piesei de prelucrat crește în consecință. Prin urmare, în plus față de utilizarea materiilor prime rezistente la uzură a sculelor, specificația de deteriorare a sculelor nu trebuie să depășească 0,3 mm, altfel este foarte ușor să cauzeze depuneri de cipuri. În timpul tăierii, temperatura piesei de prelucrat, în general, nu trebuie să depășească 100 ℃ pentru a evita deformarea.
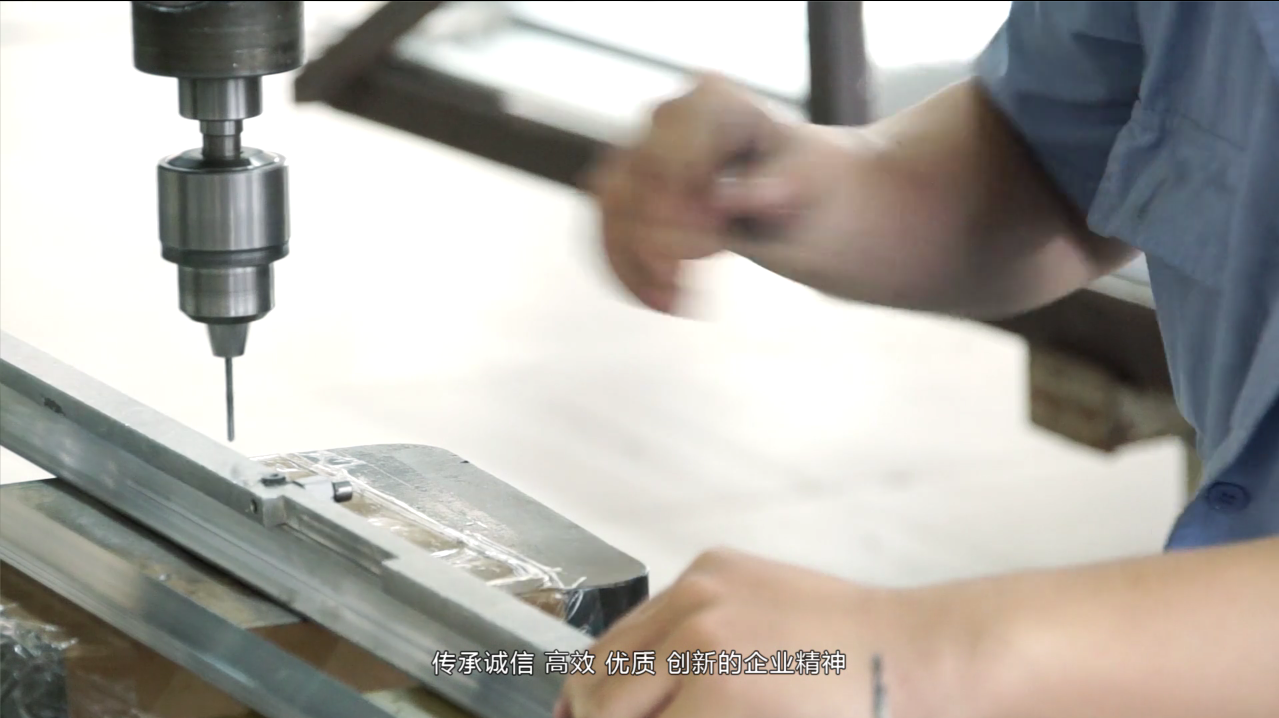
3. Îmbunătățirea metodei de prindere a pieselor de prelucrat
Pentru piesele turnate sub presiune cu pereți groși cu rigiditate slabă, pot fi utilizate următoarele metode de prindere pentru a reduce deformarea:
① Pentru piesele manșonului arborelui cu pereți groși, dacă se utilizează o mandrină hidraulică cu trei fălci sau o mandrină elastică pentru a prinde din direcția axială, odată ce se slăbește după prelucrare, piesa de prelucrat cu profil de aluminiu se va deforma inevitabil. În acest moment, ar trebui utilizată o metodă radială de fixare a găurilor interioare cu rigiditate bună. Folosind filetele interne ale componentei pentru poziționarea precisă, creați un gât filetat al arborelui cu filete externe și introduceți-l în filetele interne ale componentei. Fixați gaura interioară cu o placă de acoperire spate și strângeți-l cu un capac cu șurub. Atunci când prelucrează cercul exterior, poate preveni deformarea prinderii și poate obține o precizie satisfăcătoare de prelucrare.
② Atunci când prelucrați piese de prelucrat din tablă metalică cu pereți groși, cel mai bine este să utilizați o cupă de aspirare vid pentru a obține forța de prindere distribuită uniform și apoi utilizați o cantitate mică de tăiere pentru a procesa, ceea ce poate evita în mod eficient deformarea piesei de prelucrat.
În plus, se poate aplica și metoda de etanșare. Pentru a îmbunătăți rigiditatea de prelucrare a pieselor de prelucrat din aluminiu cu pereți groși, pot fi adăugate materiale în interiorul piesei de prelucrat pentru a reduce deformarea în timpul proceselor de prindere și tăiere. De exemplu, prin turnarea unei soluții de uree care conține nitrat de potasiu între 3% și 6% în piesa de prelucrat și prelucrarea acesteia, piesa de prelucrat cu profil de aluminiu poate fi scufundată în apă sau etanol pentru a dizolva și turna materialul de umplere.
4. Aranjarea științifică a fluxului de proces
În timpul tăierii de mare viteză, datorită capacității mari de prelucrare și tăierii intermitente, întregul proces de tăiere provoacă de obicei vibrații, ceea ce pune în pericol precizia și rugozitatea prelucrării profilului de aluminiu. Prin urmare, întregul proces de tăiere și prelucrare de mare viteză a mașinilor-unelte CNC poate fi în general împărțit în prelucrare dură, prelucrare semi-precizie, frezare de suprafață, prelucrare de precizie și alte fluxuri de proces. Pentru piesele cu cerințe de înaltă precizie, uneori este necesar să se efectueze prelucrări secundare de semi precizie înainte de a continua cu prelucrarea de precizie. După prelucrarea dură, piesele se pot răci în mod natural, pot elimina stresul termic cauzat de prelucrarea dură și pot reduce deformarea. Capacitatea rămasă după prelucrarea dură ar trebui să depășească valoarea deformării, de obicei 1-3mm. La prelucrarea de precizie a profilelor din aluminiu, este necesar să se mențină o capacitate uniformă de prelucrare pe suprafață, în general între 0,2-0,5 milimetri, pentru a se asigura că scula de tăiere este într-o stare stabilă pe tot parcursul procesului de prelucrare, reducând considerabil deformarea tăierii și obținând o calitate excelentă de prelucrare a suprafeței, asigurând precizia produsului.
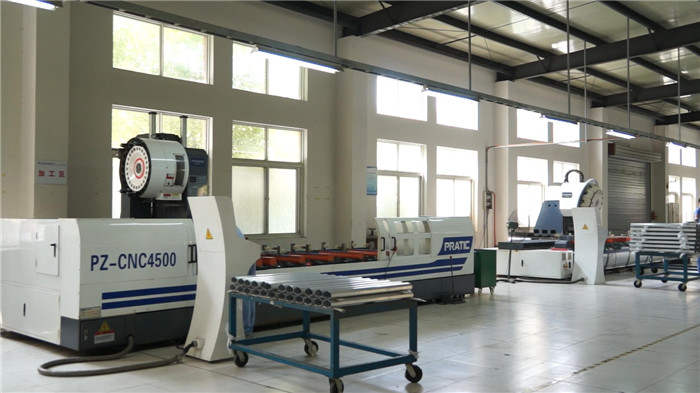
Metode practice pentru reducerea deformării prelucrării
Piesele fabricate din materii prime din aliaj de aluminiu se deformează în timpul întregii prelucrări, iar pe lângă motivele menționate mai sus, etapele de operare sunt, de asemenea, esențiale în timpul procesului de operare.
1. Pentru piesele cu capacitate mare de prelucrare, pentru a atinge standarde bune de disipare a căldurii conductelor de căldură pe tot parcursul procesului de prelucrare și pentru a preveni concentrarea căldurii, procesarea simetrică ar trebui selectată în timpul prelucrării. Dacă există o placă groasă de 90mm care trebuie prelucrată la 60mm, iar cealaltă parte este tăiată imediat după frezarea unei părți, planitatea poate ajunge la 5mm după prelucrare la specificația finală dintr-o singură dată; Dacă se alege prelucrarea simetrică continuă, fiecare parte este prelucrată de două ori la specificația finală, asigurând o planitate de 0,2 mm.
2. Dacă există mai multe matrițe concave pe profilul aliajului de aluminiu, nu este potrivit să utilizați o metodă de prelucrare secvențială a unui matriță concavă după altul în timpul prelucrării, ceea ce poate duce cu ușurință la suport neuniform al pieselor și deformare. Selectați mai multe straturi pentru prelucrare, fiecare strat fiind prelucrat cât mai mult posibil pentru a acoperi toate matrițele concave, apoi prelucrarea stratului următor pentru a asigura sprijinul uniform al pieselor și a reduce deformarea.
3. Reduceți forța de tăiere și căldura de tăiere prin schimbarea utilizării de tăiere. Dintre cele trei elemente de utilizare a tăierii, cantitatea de scula de tăiere din spate are un impact semnificativ asupra forței de tăiere. Dacă capacitatea de prelucrare este mare și forța de tăiere a unei alimente este ridicată, aceasta nu numai că va provoca deformarea pieselor, dar, de asemenea, va continua să dăuneze rigiditatea axului strungului și să reducă rezistența la uzură a sculelor de tăiere. Dacă cantitatea de hrănire înapoi și tăiere cuțit este redusă, aceasta va avea un impact semnificativ asupra productivității. Cu toate acestea, tăierea de mare viteză este utilizată în mod obișnuit în prelucrarea CNC, care poate depăși această dificultate. În plus față de reducerea cantității de backstepping și tăiere, dacă viteza de tăiere este relativ crescută și raportul de viteză al strungului CNC este crescut, forța de tăiere poate fi redusă, iar eficiența de prelucrare poate fi asigurată.
4. Trebuie acordată atenție și secvenței de tăiere. Prelucrarea dură se concentrează pe îmbunătățirea eficienței procesării și urmărirea unei rate de tăiere perfecte pe unitate de timp. În general, se poate utiliza frezarea inversă. Îndepărtați materiile prime inutile de pe suprafața germenilor de păr în cel mai scurt și cel mai mic timp și generați conturul geometric necesar pentru prelucrarea de precizie. Accentul prelucrării de precizie se concentrează pe precizie ridicată și calitate ridicată și este recomandabil să alegeți suprafețe de frezare. Datorită scăderii treptate a grosimii de tăiere a dinților de tăiere de la mari la zero în timpul frezării secvențiale, nivelul de întărire a prelucrării este foarte redus, iar nivelul de deformare a pieselor este, de asemenea, atenuat.
5. Piesele de prelucrat cu pereți groși sunt inevitabil deformate în timpul prelucrării datorită prinderii, chiar și în timpul prelucrării de precizie. Pentru a minimiza deformarea piesei de prelucrat, piesa de prindere poate fi slăbită înainte ca profilul de aluminiu să fie finalizat la specificațiile finale, permițând piesei de prelucrat să fie reparată la aspectul său original la dorință. Apoi, aceasta poate fi ușor prinsă la standardul de a putea ține piesa de prelucrat ferm (complet prin atingere), astfel încât să obțină efectul dorit de prelucrare. Pe scurt, punctul de aplicare a forței de strângere este de preferat pe suprafața plăcii de sprijin, iar forța de strângere trebuie aplicată în direcția unei rigidități bune a piesei de prelucrat Sub premisa asigurării că piesa de prelucrat nu se slăbește, cu cât forța de strângere este mai mică, cu atât mai bine.
6. Atunci când prelucrați piese din aliaj de aluminiu cu o matriță concavă, nu este necesar să lăsați inserția uneltei de strunjire în piese imediat ca un burghiu Fried Dough Twists atunci când prelucrați matrița concavă pe cât posibil, rezultând în spațiu insuficient în camera de cip a sculei de strunjire, suprafața de frezare fără lună și condiții proaste, cum ar fi supraîncălzirea, umflarea, colapsul uneltei și ruperea uneltei a pieselor. Mai întâi, adăugați un burghiu Fried Dough Twists cu aceeași specificație sau cu o dimensiune mai mare decât unealta de strunjire pentru a găsi gaura sculei, apoi utilizați unealta de strunjire pentru a tăia. Alternativ, procesul programului de tăiere în spirală poate fi produs folosind software-ul CAM.