Выбор инструмента и инструмента является одним из важных элементов процесса обработки с ЧПУ, который не только влияет на эффективность обработки станка, но и напрямую влияет на качество обработки. По сравнению с традиционными методами обработки, обработка с ЧПУ требует более высоких требований к инструментам и инструментам. Не только требует высокой точности, хорошей жесткости, высокой долговечности, но и требует стабильного размера, удобной настройки установки.
Материалы для ножей с ЧПУ 1, высокоскоростная сталь
Высокоскоростная сталь также называется фронтальной сталью, белой сталью. Это легированная сталь, содержащая вольфрам (W), молибден (Mo), хром (Cr), ванадий (V), кобальт (Co) и другие элементы, разделенные на две основные серии вольфрама и молибдена, является традиционным материалом для ножей. Твердость при комнатной температуре составляет от 62 до 65 HRC, а тепловая твердость может быть увеличена до 500 ° C до 600 ° C. После закалки деформация мала, легко измельчается, может быть кована и резана. Он может использоваться не только для изготовления долота, фрезы, но и для изготовления зубчатых ножей, формовочных фрез и других сложных инструментов. Однако из - за более низкой разрешенной скорости резания (50 м / мин) он в основном используется для низкоскоростной обработки станков с ЧПУ. Обычная высокоскоростная сталь представлена на W18Cr4V.
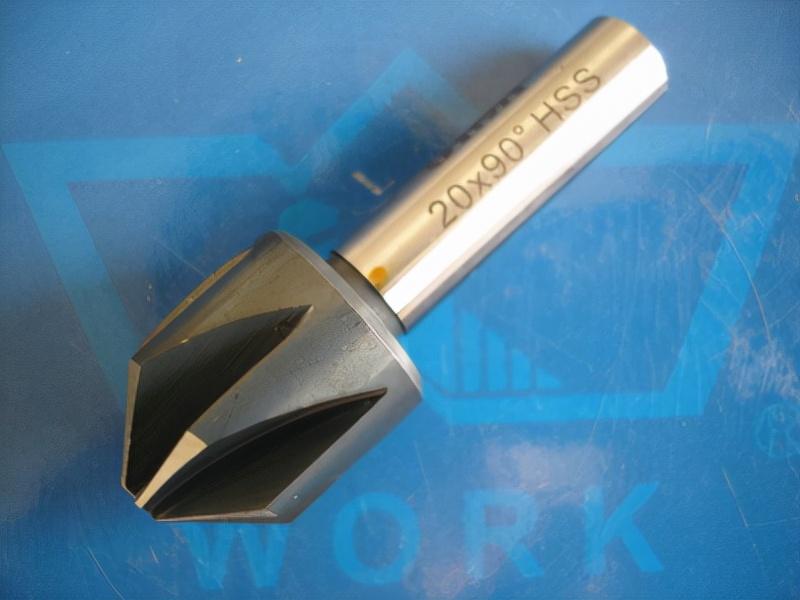
2. Твердые сплавы
Твердые сплавы представляют собой порошковые металлургические продукты, изготовленные из карбидов с высокой твердостью и температурой плавления (WC, TiC, TaC, NbC и т. Д.), которые используют Co, Mo, Ni в качестве связующего вещества. Его твердость при комнатной температуре может достигать 74 - 82 HRC и может выдерживать высокие температуры от 800 ° C до 1000 ° C. Более низкая себестоимость производства, в средней скорости (150 м / мин), большая подача резания может играть отличную режущую производительность, поэтому он стал наиболее широко используемым материалом инструмента в обработке с ЧПУ. Однако его ударная вязкость и прочность на изгиб намного ниже, чем высокоскоростная сталь, поэтому он редко превращается в цельный инструмент. В практическом использовании твердосплавные блоки обычно прикрепляются к корпусу ножа сваркой или механическим зажимом. Наиболее распространенными твердыми сплавами являются вольфрамово - кобальтовые (YG) сплавы (YG8, YG6, YG3), вольфрамово - титановые (YT) сплавы (YT5, YT15, YT30) и вольфрамово - титановый тантал (ниобий) (YW) (YW1, YW2) сплавы трех основных категорий.
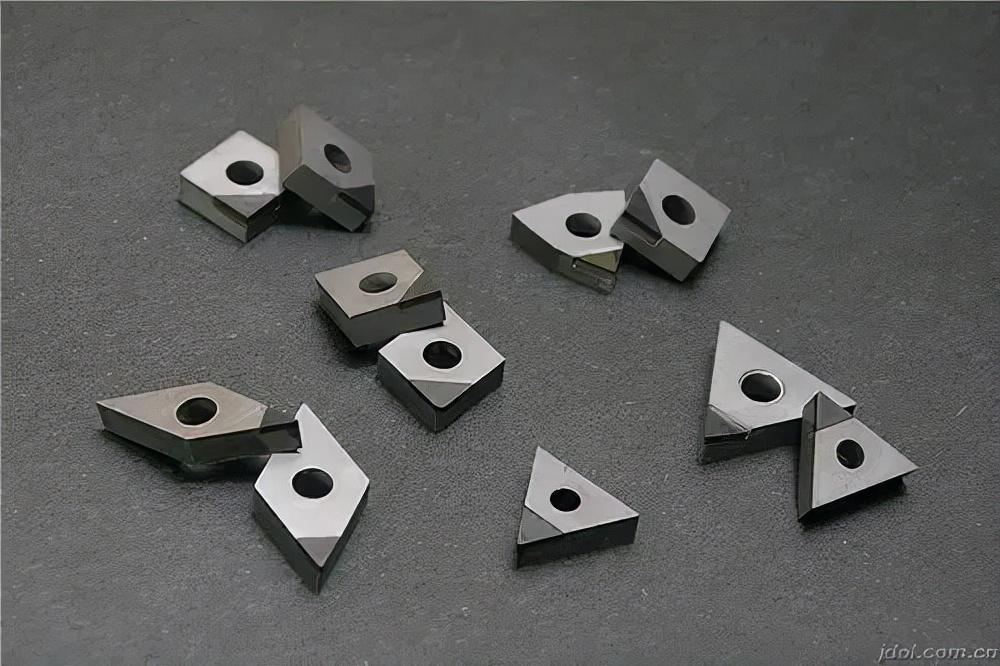
3. Твердые сплавы с покрытием
Жесткий сплав с покрытием - это один или несколько слоев твердосплавного инструмента с хорошей износостойкостью TiN, TiCN, TiAlN и Al2O3, толщина покрытия от 2 мкм до 18 мкм. Покрытие обычно выполняет две функции: с одной стороны, оно имеет гораздо более низкий коэффициент теплопроводности, чем матрица инструмента и материал изделия, уменьшая тепловое действие матрицы инструмента; С другой стороны, он может эффективно улучшить трение и адгезию процесса резания и уменьшить образование тепла резания. TiN обладает свойствами низкого трения, которые уменьшают потери тканей покрытия. TiCN может уменьшить износ задней поверхности ножа. Твердость покрытия TiCN выше. Покрытие Al2O3 обладает отличным теплоизоляционным эффектом. Покрытие твердосплавного инструмента по сравнению с твердосплавным ножом, как с точки зрения прочности, твердости и износостойкости значительно улучшилось. Для резки деталей с твердостью от 45 до 55 HRC, недорогие твердые сплавы с покрытием обеспечивают высокоскоростное резание. В последние годы некоторые производители полагаются на улучшение материала покрытия и пропорции метода, но также делают характер покрытия ножа значительно улучшился.
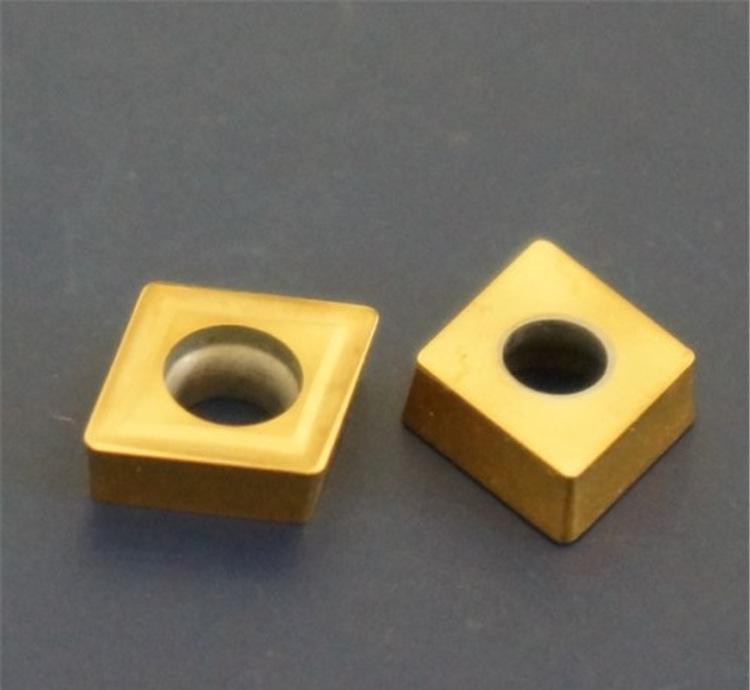
4. Керамические материалы
Керамика является одним из быстрорастущих и все более широко используемых ножевых материалов за последние 20 лет. В ближайшем будущем керамика может вызвать третью революцию в обработке резания после высокоскоростной стали и твердых сплавов.
Керамические ножи имеют высокую твердость (91 - 95 HRA), высокую прочность (прочность на изгиб 750 МПа - 1000 МПа), хорошую износостойкость, хорошую химическую стабильность, хорошую устойчивость к сцеплению, низкий коэффициент трения и низкую цену. Мало того, керамические ножи также имеют высокую высокотемпературную твердость, достигающую 80HRA при 1200°C. При нормальном использовании керамический инструмент имеет чрезвычайно длительный срок службы, скорость резания может быть в 2 - 5 раз выше, чем твердосплавный инструмент, особенно подходит для обработки материалов высокой твердости, точной обработки и высокоскоростной обработки, твердости обработки до 60 HRC различных видов закаленной стали и закаленного чугуна и так далее. Обычно используются керамика на основе оксида алюминия, керамика на основе нитрида кремния и металлическая керамика. Керамические ножи на основе оксида алюминия имеют более высокую термическую твердость, чем твердые сплавы, режущие лезвия в высокоскоростном режущем состоянии, как правило, не производят пластическую деформацию, но их прочность и вязкость ниже. В дополнение к высокой термической твердости, керамика на основе нитрида кремния также обладает хорошей вязкостью, по сравнению с керамикой на основе оксида кремния, ее недостатком является то, что при обработке стали она подвержена высокотемпературной диффузии, усиливает износ инструмента, керамический инструмент на основе нитрида кремния в основном используется для прерывистого токарного серого чугуна и фрезерованного серого чугуна. Металлическая керамика - это карбид в качестве основного материала, похожий на жесткий сплав, но он имеет более низкую сродство, хорошую фрикционность и лучшую износостойкость, он может выдерживать более высокую температуру резания, чем обычный твердый сплав, но не имеет устойчивости к удару твердого сплава, вязкости при тяжелой обработке и низкоскоростной прочности при подаче. В последние годы благодаря большому количеству исследований, улучшений и внедрению новых производственных процессов прочность на изгиб и вязкость керамических материалов значительно улучшилась, например, новая металлическая керамическая конструкция NX2525, разработанная японской компанией Mitsubishi Metal, новая серия металлических керамических лезвий CT и покрытая металлическая керамическая серия лезвий, прочность на изгиб и износостойкость намного выше, чем у обычной металлической керамики, что значительно расширяет сферу применения керамических материалов.
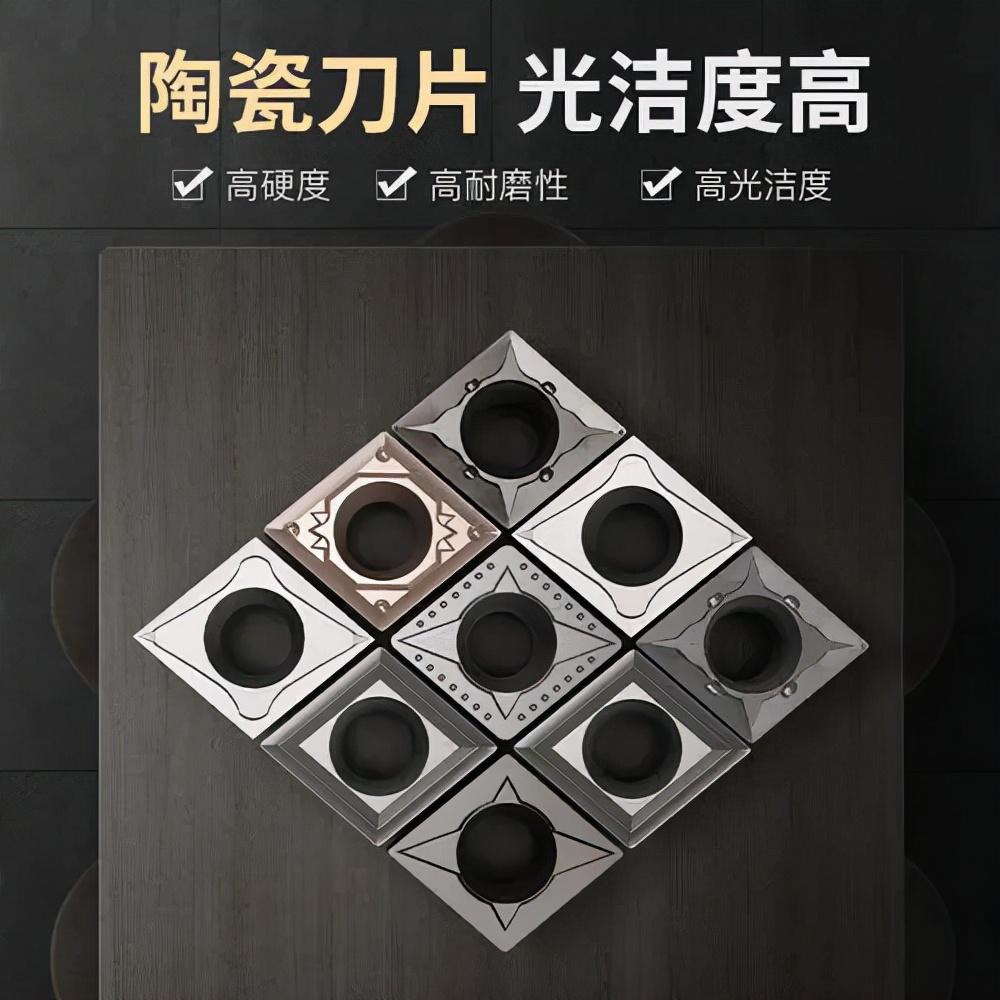
Кубический нитрид бора (CBN)
CBN - это синтетический материал высокой твердости, его твердость до 7300 - 9000 HV, его твердость и износостойкость уступают только алмазу, имеет отличную высокотемпературную твердость, по сравнению с керамическим ножом, его термостойкость и химическая стабильность немного хуже, но ударная вязкость и устойчивость к разрушению лучше.
Он широко используется для резки закаленной твердой стали (более 50 HRC), перлитного серого чугуна, холодного чугуна и высокотемпературных сплавов. По сравнению с твердосплавным ножом скорость резания может быть увеличена на порядок. Высокое содержание CBN PCBN (поликристаллический кубический нитрид бора) нож с высокой твердостью, хорошей износостойкостью, высокой прочностью на сжатие и хорошей ударной вязкостью, его недостатком является плохая термостабильность и низкая химическая инерция, подходит для обработки термостойких сплавов, чугуна и железосодержащих спеченных металлов. Композитный инструмент PCBN имеет более низкое содержание частиц CBN, использует керамику в качестве связующего вещества, его низкая твердость, но компенсирует высокое содержание CBN с плохой тепловой стабильностью PCBN, низкую химическую инерцию характеристик, подходит для резки закаленной стали. В области применения пылевого чугуна и закаленной стали керамические инструменты и инструменты CBN доступны одновременно. При сухом резании закаленной стали стоимость выбора керамики Al2O3 ниже, чем у материала PCBN, поскольку керамический инструмент обладает хорошей термохимической стабильностью, но не такой прочностью и твердостью, как инструмент PCBN. Керамические ножи являются лучшим выбором для деталей с твердостью резания ниже 60 HRC и небольшой подачей. Ножи PCBN подходят для твердости деталей выше 60 HRC, особенно для автоматизации и высокоточной обработки.
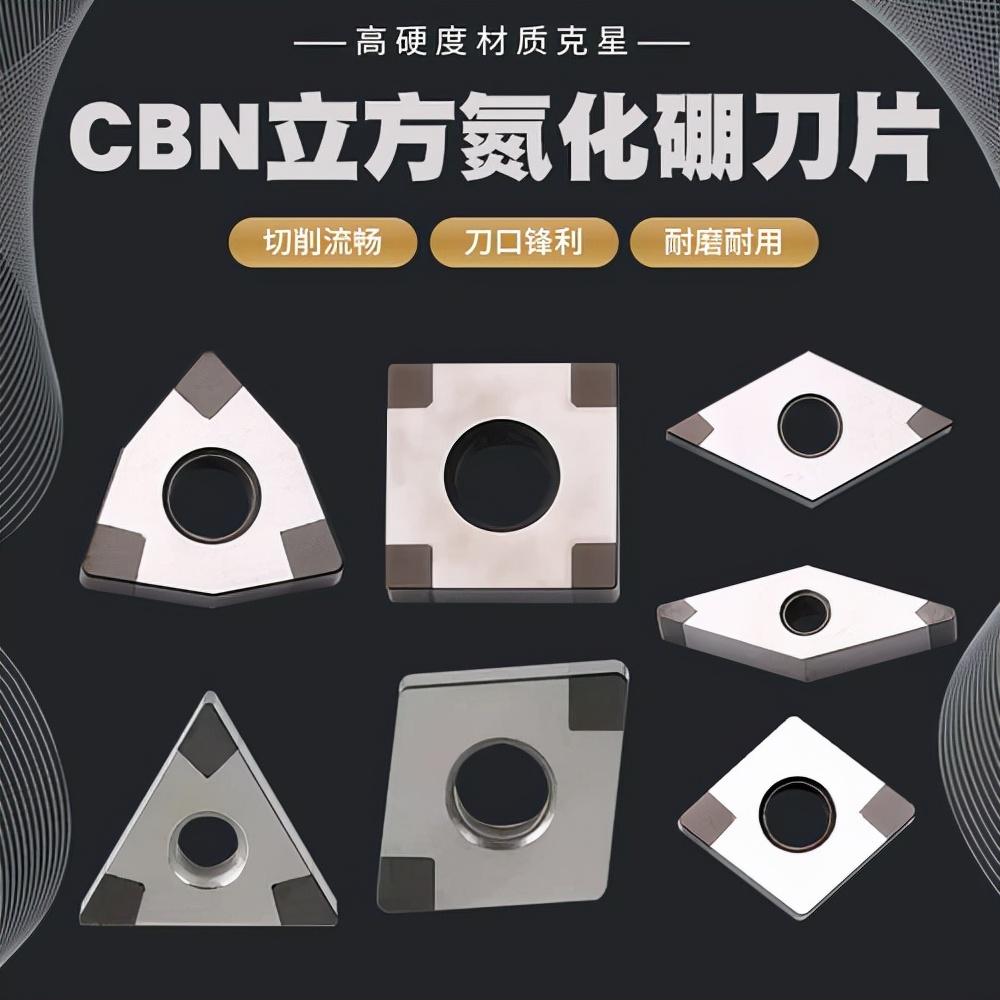
Поликристаллический алмаз (PCD)
PCD, как самый жесткий режущий материал, твердость до 10000HV, обладает наилучшей износостойкостью, он способен обрабатывать мягкие цветные металлы с высокой скоростью (1000 м / мин) и высокой точностью, но он чувствителен к удару, легко разрушается, а также имеет сильную сродство к железу в черных металлах, легко вызывает химические реакции, как правило, только для обработки неметаллических деталей, таких как цветные металлы и их сплавы, стекловолокно, инженерная керамика и твердые сплавы.
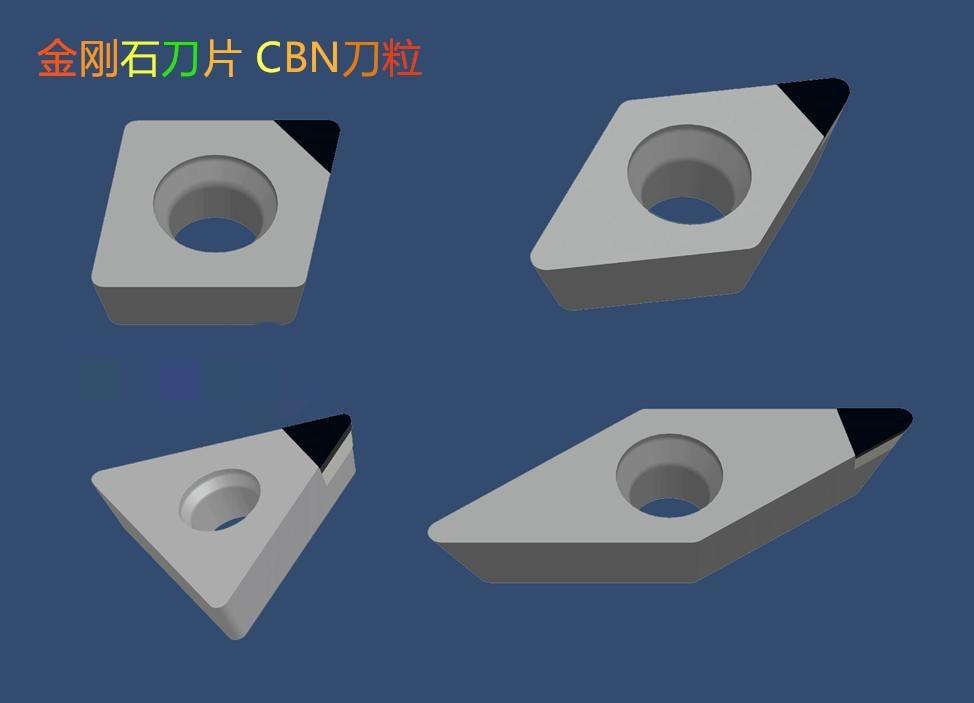