Как определить параметры процесса лазерной резки в Шэньяне?
принцип работы лазерной резки
Обработка лазерной резки - это замена традиционного механического ножа невидимым световым лучом, с высокой точностью, быстрой резки, не ограничиваясь ограничениями на рисунок резки, автоматической сортировкой, чтобы сэкономить материал, гладкий разрез, низкая стоимость обработки и другие характеристики, будут постепенно улучшаться или заменяться традиционным оборудованием для резки металла. Механическая часть головки лазерного ножа не контактирует с деталью и не наносит царапин поверхности детали во время работы; Лазерная резка быстро, разрез гладкий и ровный, как правило, не требует последующей обработки; Зона теплового воздействия резки мала, деформация пластины мала, щель разреза (0,1 мм ~ 0,3 мм); В разрезе нет механического напряжения, нет заусенцев сдвига; Высокая точность обработки, хорошая повторяемость, не повредить поверхность материала; Программирование с ЧПУ, которое может обрабатывать любой план, можно разрезать всю пластину большого формата, не нужно открывать форму, экономия времени.
Состав лазерных режущих устройств
Лазерная режущая установка в основном состоит из лазеров, светопроводных систем, систем движения с ЧПУ, головок автоматической регулировки высоты и резки, рабочих платформ и выдуваемых газов высокого давления и других систем. Многие параметры влияют на процесс лазерной резки, некоторые из которых зависят от технических характеристик лазера и станка, в то время как другие изменяются. Основными параметрами лазерной резки являются:
Основные параметры лазерной резки
1 Режим луча
Базовые модули, также известные как гауссовые модули, являются идеальными режимами для резки и в основном появляются в маломощных лазерах мощностью менее 1 кВт. Многомодовый, является смесью высокоступенчатых модулей, имеет плохую фокусировку на многомодовом режиме при той же мощности, низкую способность к резке, способность к резке и качество резки одномодового лазера лучше, чем у многомодового.
2 Лазерная мощность
Мощность лазера, необходимая для лазерной резки, в основном зависит от требований к режущему материалу, толщине материала и скорости резки. Мощность лазера оказывает большое влияние на толщину резки, скорость резки, ширину разреза и так далее. Общая мощность лазера становится больше, толщина материала, который можно разрезать, также увеличивается, скорость резки ускоряется, ширина разреза также увеличивается.
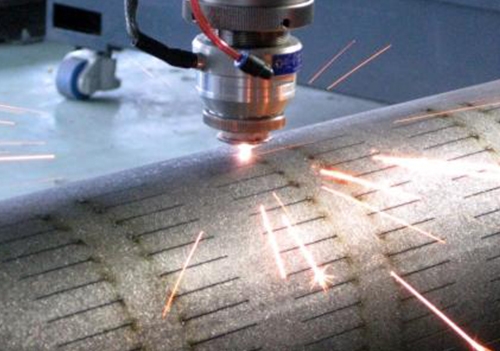
3 Место фокусировки
Фокусное положение оказывает большее влияние на ширину разреза. Как правило, фокус выбора расположен под поверхностью материала около 1 / 3 толщины гаечного отверстия с большой глубиной резки и меньшей шириной отверстия.
4 Фокальный момент
При резке толстой стали следует использовать луч с более длинным фокусным моментом, чтобы получить разрезанную поверхность с хорошей вертикальностью. Глубина фокуса большая, диаметр пятна также становится больше, плотность мощности уменьшается, скорость резки уменьшается. Для поддержания определенной скорости резки требуется увеличение мощности лазера. Для резки тонкой пластины следует использовать луч с меньшим фокусным расстоянием, так что диаметр пятна мал, плотность мощности велика, скорость резки быстра.
5 Вспомогательный газ
Резка низкоуглеродистой стали в основном использует кислород в качестве режущего газа, чтобы использовать тепло реакции горения железа и кислорода для содействия процессу резки, а скорость резки, качество разреза хорошее, вы можете получить разрез без подвесного шлака. Его давление становится больше, кинетическая энергия увеличивается, способность к удалению шлака улучшается; Размер давления резания определяется в зависимости от материала, толщины пластины, скорости резания и коэффициента качества режущей поверхности.
6 Структура сопла
Структурная форма сопла и размер выходного отверстия также влияют на качество и эффективность лазерной резки, различные требования к резке выбирают разные сопла. Часто используемые формы сопла: цилиндрические, конические, квадратные и другие формы. Лазерная резка обычно использует коаксиальный (воздушный поток и концентрический оптический вал) метод продувания, например, воздушный поток и оптическая ось имеют разные оси, тогда при резке легко генерируется большое количество брызг. Чтобы обеспечить стабильность процесса резки, обычно нужно контролировать расстояние между торцом сопла и поверхностью детали, обычно от 0,5 до 2,0 мм, чтобы резка прошла гладко.
Статья взята из Интернета, пожалуйста, свяжитесь со мной, если у вас есть вопросы, чтобы удалить!