Spracovanie listových kovov je komplexný chladný spracovateľský proces pre kovové listy (zvyčajne pod 6 mm), vrátane rezania, bodkovania, naklonia, zvárania, riveting, tvarovania tvaru a povrchového spracovania. Jeho významnou črtou je, že hrúbka tej istej časti je konzistentná.
Metóda spracovania listových kovov: Spracovanie listových kovov bez tvaru: Proces spracovania listových kovov prostredníctvom zariadení, ako sú číselné vpichovanie, rezanie laserov, rezačné stroje, brzdové stroje, rievacie stroje atď. Všeobecne sa používa na výrobu vzoriek alebo výrobu malých šarží s vysokými nákladmi. Krátky cyklus spracovania a rýchla reakcia. Spracovanie moldov: Na spracovanie kovových listov sa vo všeobecnosti rezajú moldy a formujú moldy, ktoré sa používajú najmä na masovú výrobu s nižšími nákladmi. Počiatočné náklady na molovanie sú vysoké a kvalita častí je zaručená. Cyklus predčasného spracovania je dlhý a náklady na tvar sú vysoké. Proces spracovania listových kovov: rezanie: číselné bodnutie, rezanie laserov, rezanie strojov
Formovanie – ohnutie, ťahanie, bodnutie: ohnutie strojov, bodnutie strojov atď.
Ostatné spracovanie: riveting, tapping atď.
zváranie: metóda spojenia kovových listov
Oprava povrchu: spraying prášku, elektroplating, drôtový výkres, tlač obrazovky atď.
Technológia spracovania listových kovov – Hlavné metódy rezania pre listové kovy zahŕňajú číselné bodkovanie, rezanie laserov, rezanie strojov a rezanie tvaru. CNC je v súčasnosti bežne používaná metóda a rezanie laserov sa používa prevažne v štádiu odberu vzoriek (alebo môže tiež spracovať kovové časti z nehrdzavejúcej ocele) s vysokými spracovateľskými nákladmi.
Ďalej budeme predovšetkým zavádzať rezanie listových kovov pomocou číselného bodnutia
Číselné bodnutie, tiež známe ako bodovacie zariadenie CNC na koliesku, sa môže použiť na rezanie, bodnutie, ťahanie dier, valcovanie rebier, bodovacie slepy atď. Jeho presnosť strojov môže dosiahnuť +/-0,1 mm.
Hrúbka strojových listových kovov CNC je:
Platne valcované za studena a valcované za tepla 4,0 mm
hliníková doska 5,0 mm
Škatuľa z nehrdzavejúcej ocele 2,0 mm
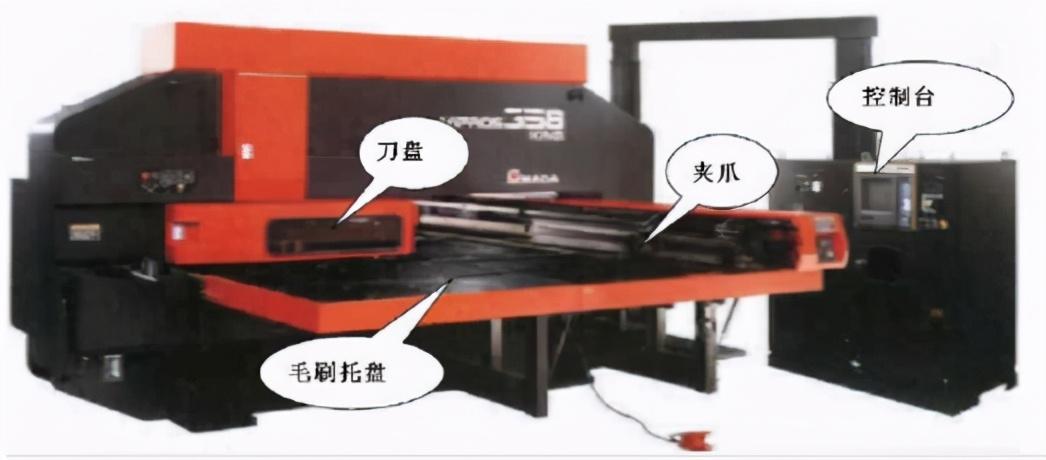
Existuje požiadavka minimálnej veľkosti na úder. Minimálna veľkosť bodnutia súvisí s tvarom diery, mechanickými vlastnosťami materiálu a hrúbkou materiálu. (Ako sa uvádza na nižšie uvedenom obrázku)
2) Rozmedzenie a vzdialenosť hrany tlakových dier. Ak minimálna vzdialenosť medzi bodnou hranou časti a vonkajšou hranou časti nie je rovnobežná s vonkajšou hranou časti, minimálna vzdialenosť by nemala byť menšia ako hrúbka materiálu t; Ak je paralelná, nemala by byť nižšia ako 1,5 t. (Ako sa uvádza na nižšie uvedenom obrázku)
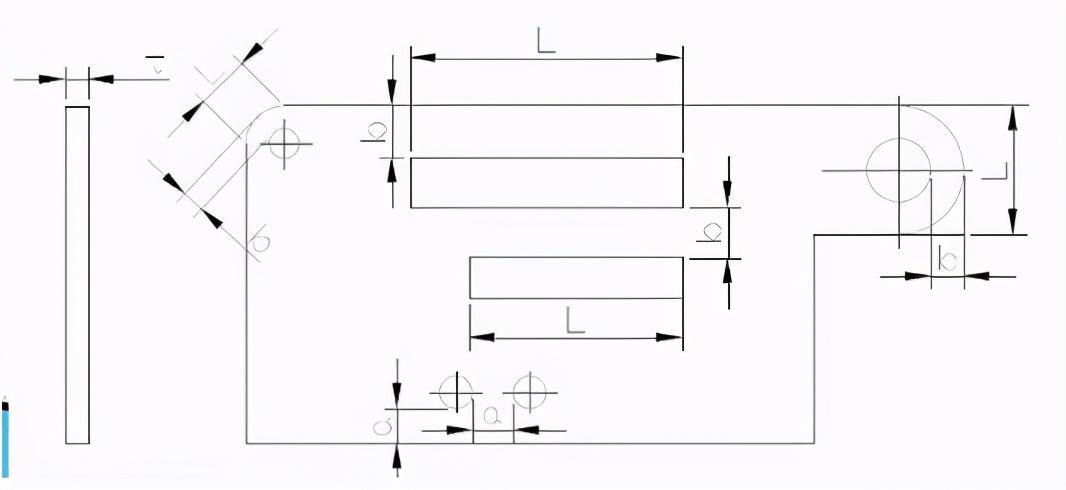
(3) Pri roztiahnutí dier je minimálna vzdialenosť medzi roztiahnutou dierou a okrajom 3T, minimálna vzdialenosť medzi dvoma roztiahnutými dierami 6T a minimálna bezpečná vzdialenosť medzi roztiahnutou dierou a ohnivou hranou (vnútri) 3T+R (T je hrúbka kovového listu, R je ohnivá filéta)
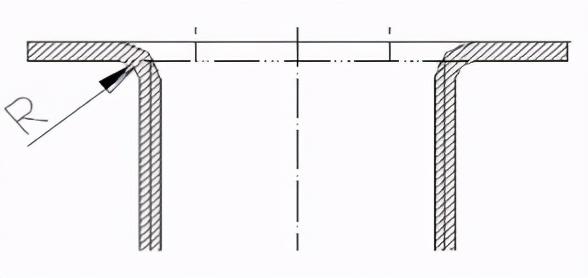
(4) Pri bodaní dier v roztiahnutých a zaklenutých častiach a hlboko ťahaných častiach by sa mala zachovať určitá vzdialenosť medzi stenou diery a priamym stenom. (Ako sa uvádza na nižšie uvedenom obrázku)
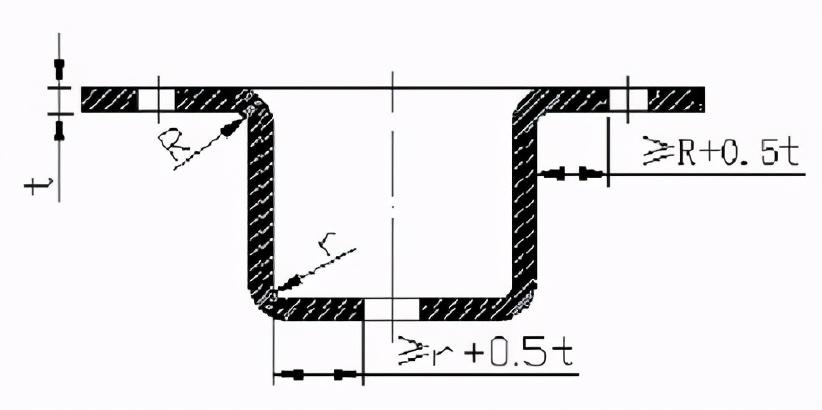
Technológia spracovania listových kovov – Formovanie listových kovov zahŕňa hlavne ohnutie a šírenie listových kovov.
1. Oblenie listového kovu 1.1 Oblenie listového kovu používa hlavne oblené stroje.
presnosť strojového zariadenia na zloženie;
Jednokrát:+/-0,1mm
Polovicové pletenie:+/-0,2 mm
Pre 20 % zľavu:+/-0,3 mm
Základnou zásadou postupu posúvania je posúvať sa z vnútorného vonku a z malého na veľkého. Najprv by sa mali posúvať osobitné tvary a predchádzajúci proces by nemal ovplyvniť alebo zasahovať do následných procesov po tvorbe.
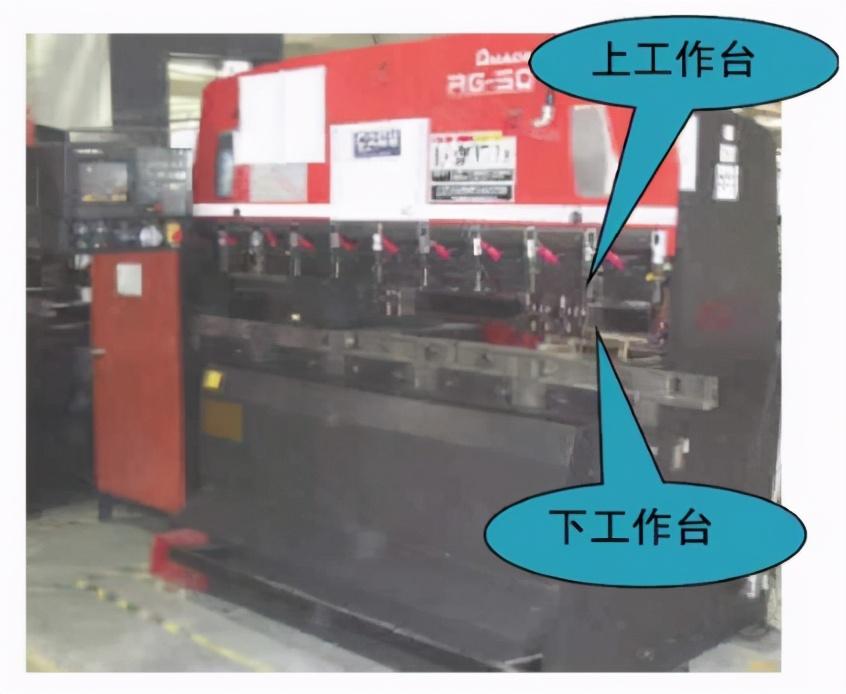
1.3 Časté tvary ohybného nôž:
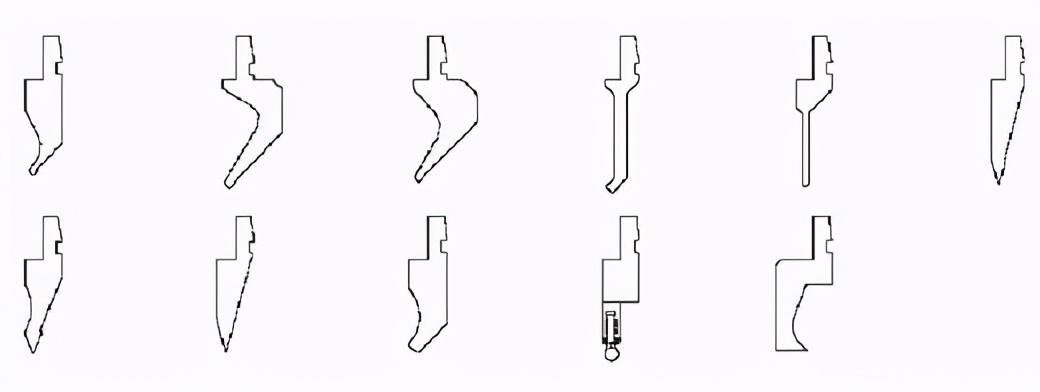
Časté tvary V-groove:
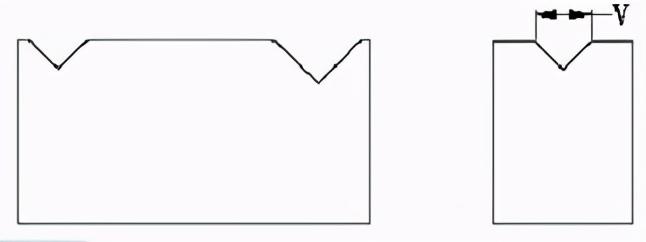
1.4 Minimálny polomer ohnutia ohnutých častí:
Keď je materiál zaklenutý, vonkajšia vrstva sa roztiahne a vnútorná vrstva sa stlačí v zaokrúhlenej oblasti. Ak je hrúbka materiálu konštantná, čím menšia je vnútorná r, tým závažnejšie je napätie a kompresia materiálu; Keď ťahový napätie vonkajšieho zaokrúhleného rohu prekročí konečnú silu materiálu, vzniknú zlomeniny a zlomeniny. Preto by sa štrukturálna konštrukcia zaklených častí mala vyhnúť príliš malému okrúhlemu okrúhlemu okrúhlemu okrúhlemu okrúhlemu okrúhlemu okrúhu. Minimálny okraj ohybu bežne používaných materiálov v spoločnosti je uvedený v tabuľke nižšie.
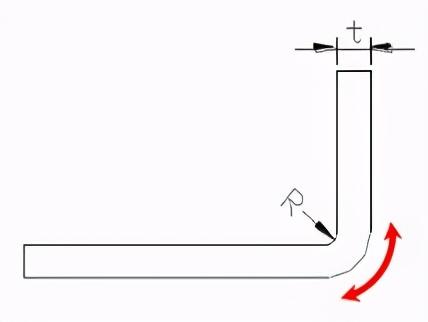
Minimálna tabuľka polomeru ohnutia pre ohnuté časti:
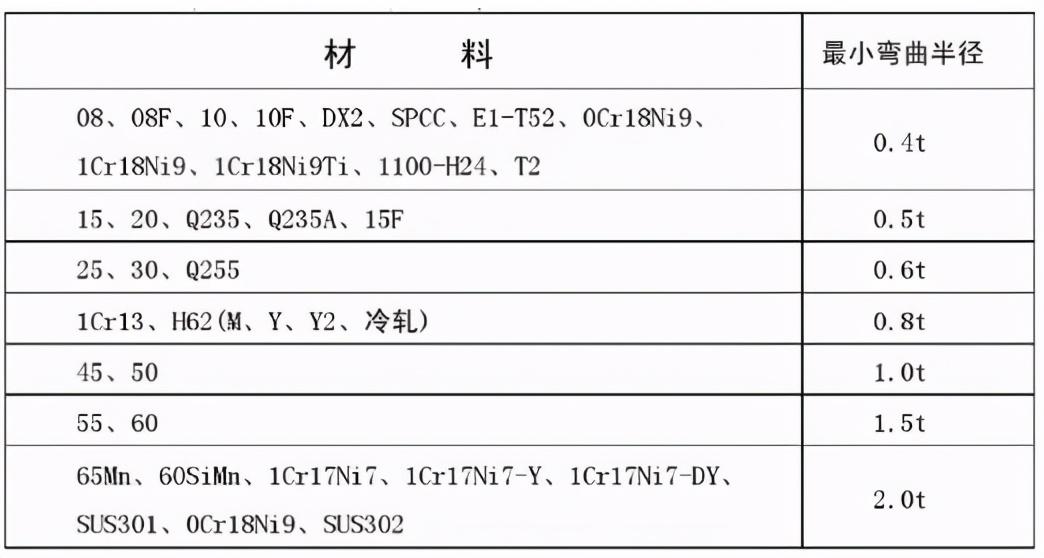
Obrázok ohybu sa vzťahuje na vnútorný obrázok ohybnej časti a t je hrúbka steny materiálu.
Výška priameho okraja uhnutej časti je 1,5:
Vo všeobecnosti by minimálna výška rovného okraja nemala byť príliš malá a požiadavka minimálnej výšky je: h>2t
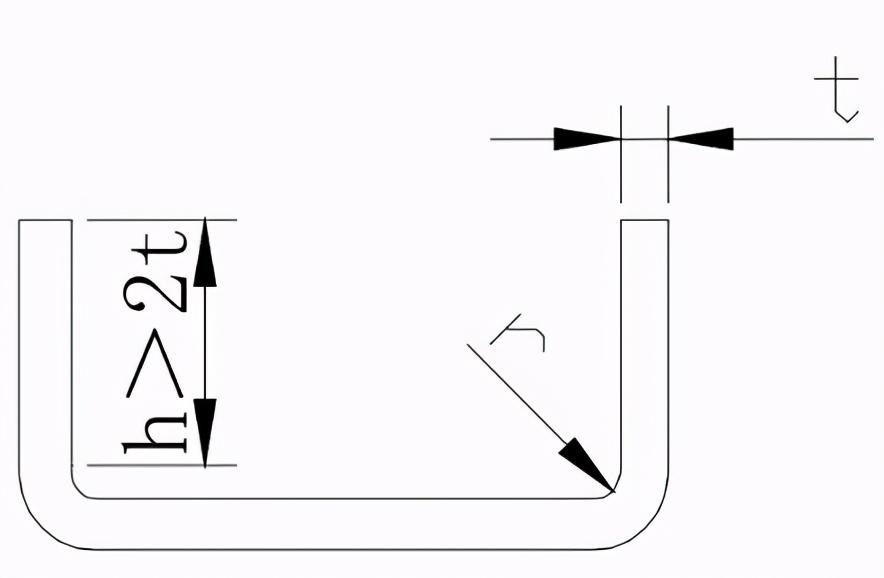
Ak sa vyžaduje výška rovnej hrany h2t ohnutej časti, najprv zvýšte výšku ohnutej hrany a potom ju spracovajte na požadovanú veľkosť po ohnutí; Alebo po spracovaní plochých škvrnov v zóne deformácie ohybu vykonajte ohyb.
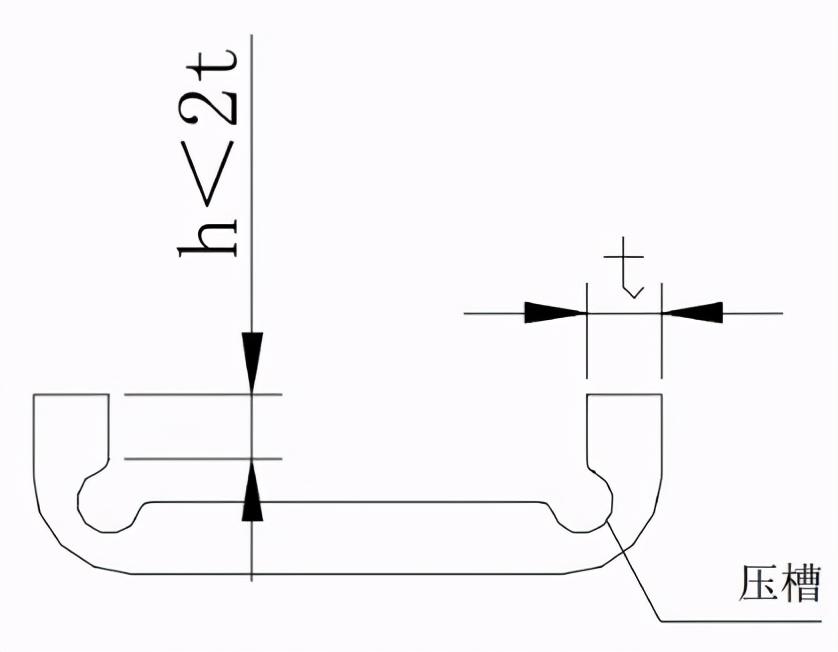
1.6 Minimálna výška ohybu priameho okraja s okrajovým uhlom na zakrivenom okraji:
Ak je zakrivená časť s sklenenou hranou zaklená, minimálna výška strany je: h=(2-4) t> 3mm
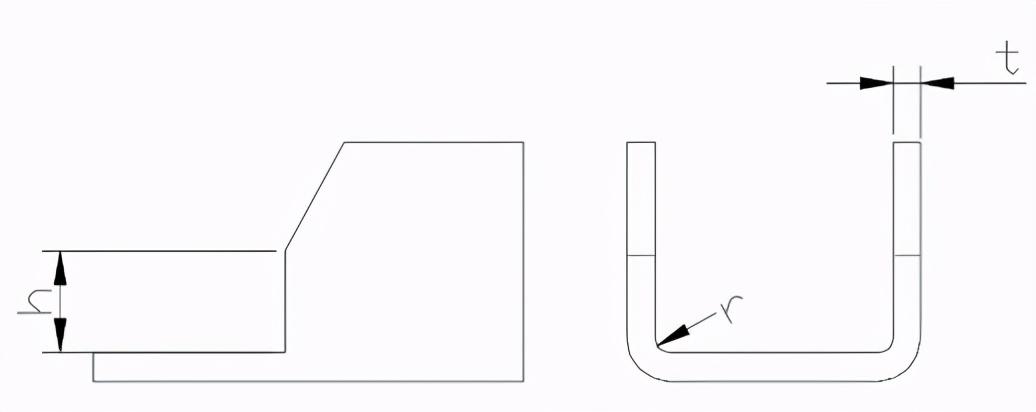
1.7 Rozmedzenie okrajov dier na zaklených častiach:
vzdialenosť okraja diery: Najprv zadajte dieru a potom ju zaklopte. Poloha diery by mala byť mimo zóny deformácie ohybu, aby sa zabránilo deformácii diery počas ohybu. V tabuľke sa uvádza vzdialenosť od steny diery k krivenému okraju.
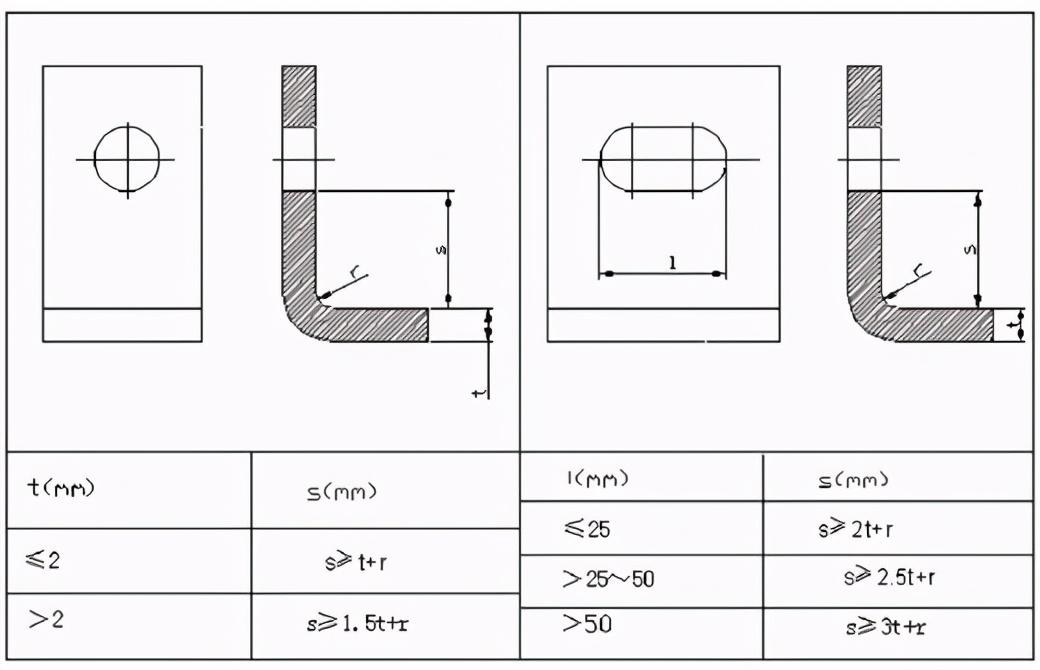
1.8 Prerez procesu na miestne ohyby:
Ohybná čiara ohybnej časti by sa mala vyhnúť náhlej zmene veľkosti. Pri miestnom ohynutí určitého segmentu okraja, aby sa zabránilo koncentrácii stresu a krakovaniu v ostrých rohoch, možno ohynutú krivku presunúť určitú vzdialenosť, aby sa neodkladná zmena veľkosti (obrázok a), alebo aby sa otvorila priehrada procesu (obrázok b), alebo aby sa mohla bodnúť priehrada procesu (obrázok c). venujte pozornosť požiadavkám na veľkosť v diagrame: SR; šírka prevádzkových intervalov kt; Hĺbka prevádzkových intervalov Lt+R+k/2.
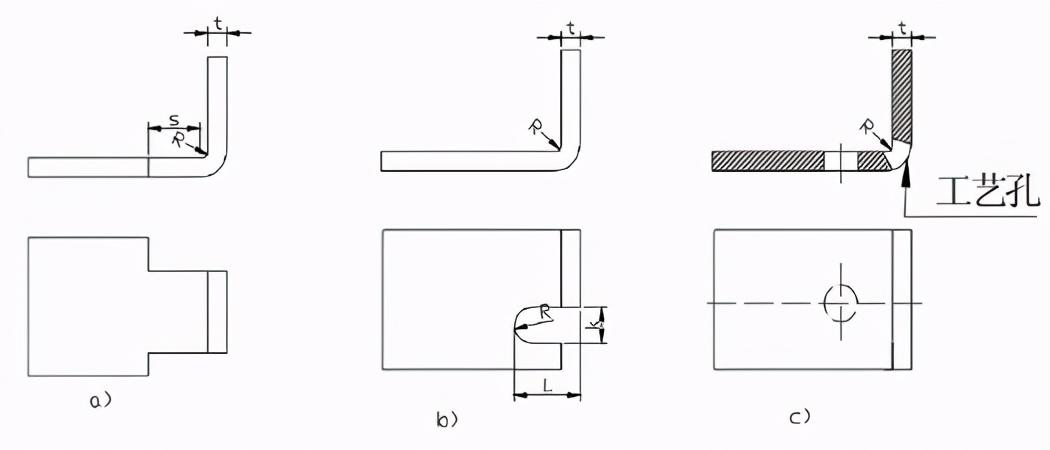
1.9 Obližovacie okraje s nápojovými okrajmi by sa mali vyhnúť deformáciám:
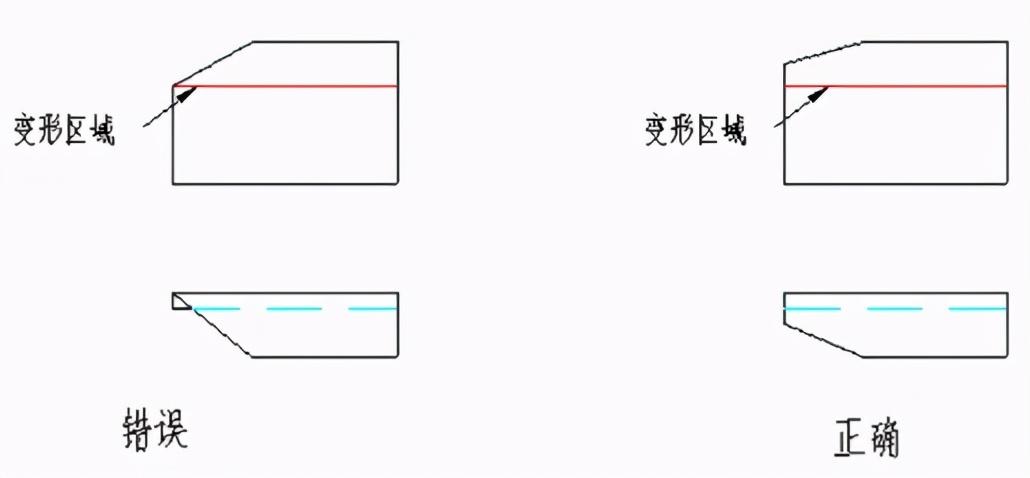
1.10 Konštrukčné požiadavky na plochy z kovových listov (mŕtve okraje):
Dĺžka mrtvej hrany plechových kovových plátov súvisí s hrúbkou materiálu. Ako sa uvádza na nasledujúcom obrázku, minimálna dĺžka mŕtveho okraja je vo všeobecnosti L3,5t+R.
Medzi nimi je t hrúbka materiálnej steny a R je minimálny vnútorný polomer ohnutia predchádzajúceho procesu (ako sa uvádza vpravo na obrázku nižšie) pred zabitím okraja.

1.11 Pridané otvory na umiestnenie procesu:
Aby sa zabezpečilo presné umiestnenie prázdneho priestoru v tvare a zabránilo sa odchýleniu prázdneho priestoru počas ohynutia, počas konštrukcie by sa mali vopred pridať procesné polohovacie diery, ako sa uvádza na nasledujúcom obrázku. Najmä v prípade častí, ktoré boli viackrát zaklené, sa procesné diery musia použiť ako referenčné položenie na zníženie kumulatívnych chyb a zabezpečenie kvality výrobku.
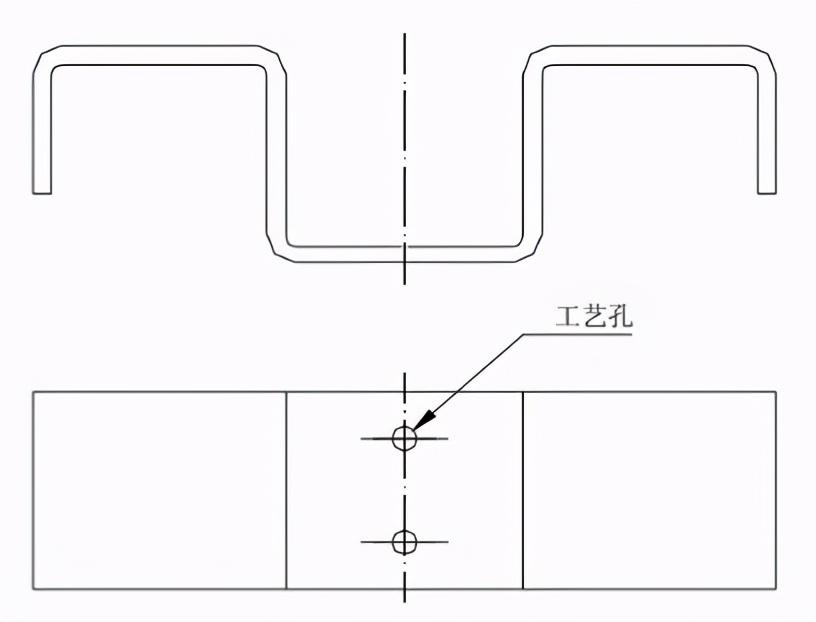
Pri označovaní rozmerov zaklených častí by sa mala zvážiť spracovateľnosť:
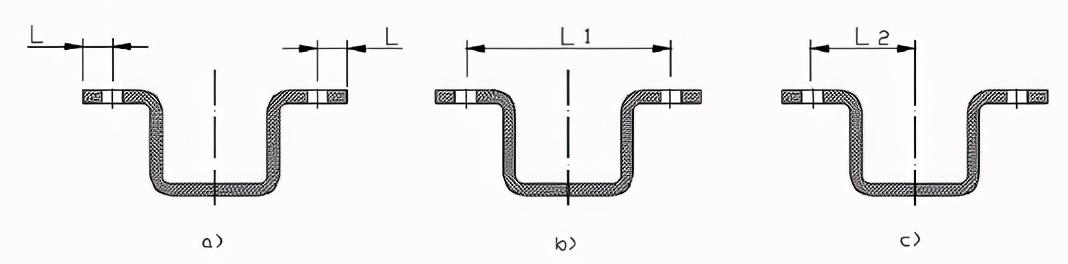
Ako sa uvádza na vyššie uvedenom obrázku, a) prvý úder a potom ohyb, je jednoduché zabezpečiť presnosť rozmeru L a spracovanie je vhodné. b) Ak je požiadavka na presnosť pre rozmer L vysoká, je potrebné najprv zaklenúť a potom spracovať dieru, ktorá je problematická pri spracovaní.
Existuje mnoho faktorov, ktoré ovplyvňujú spätnú väzbu zaklených častí vrátane mechanických vlastností materiálu, hrúbky steny, polomeru zaklenutia a pozitívneho tlaku počas zaklenutia. Čím väčší je pomer vnútorného polomeru ohnutej časti k hrúbke tabuľky, tým väčší je návrat. Výrobcovia sa v súčasnosti predovšetkým pri navrhovaní tvaru vyhýbajú metóde potláčania návratu z konštrukčného hľadiska, ako je napríklad návrat zaklených častí. Zároveň zlepšenie určitých konštrukcií v konštrukcii môže znížiť uhol spätnej väzby, ako sa uvádza v nasledujúcom obrázku: tlačenie posilnených rebier v ohnivej oblasti môže nielen zvýšiť pevnosť pracovného diela, ale tiež pomôcť potlačiť spätnú väzbu.
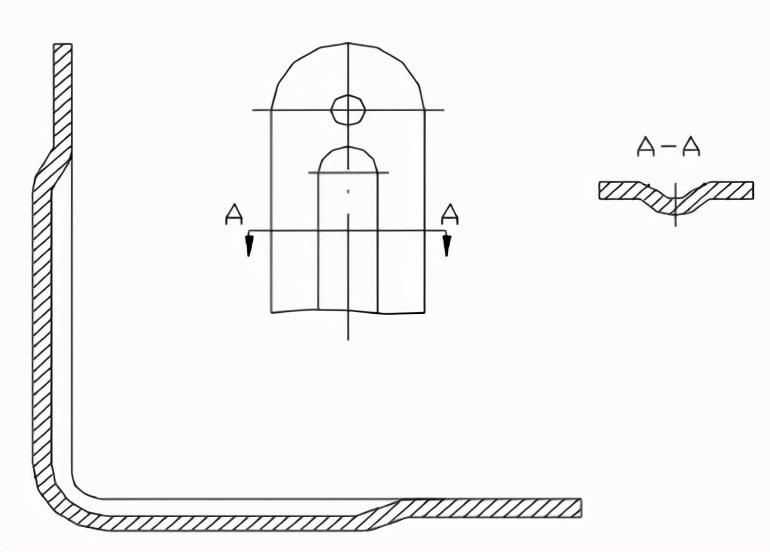
2) Tkanie listových kovov Tkanie listových kovov sa uskutočňuje hlavne CNC alebo konvenčným úderom, ktoré si vyžadujú rôzne ťahové údery alebo tvary.
Forma roztiahnutej časti by mala byť čo najjednoduchšia a symetrická a mala by sa formovať v jednom roztiahnutí čo najviac.
Časti, ktoré si vyžadujú viaceré rozťahy, by mali umožniť možné povrchové znaky počas procesu rozťahu.
Na predpoklade zabezpečenia požiadaviek na montáž by sa malo umožniť roztiahnuť bočné steny určit ým sklonom.
2.1 Požiadavky na polomer filéty medzi dnom roztiahnutej časti a rovnou stenou:
Ako sa uvádza na obrázku nižši e, polomer filéty medzi dnom roztiahnutej časti a rovnou stenou by mal byť väčší ako hrúbka tabuľky, t. j. r1t. Aby sa proces roztiahnutia dosiahol hladnejší, všeobecne sa prijme r1=(3-5) t a maximálny polomer filéty by mal byť menej alebo rovný 8-násobku hrúbky tabuľky, čo je r18t.
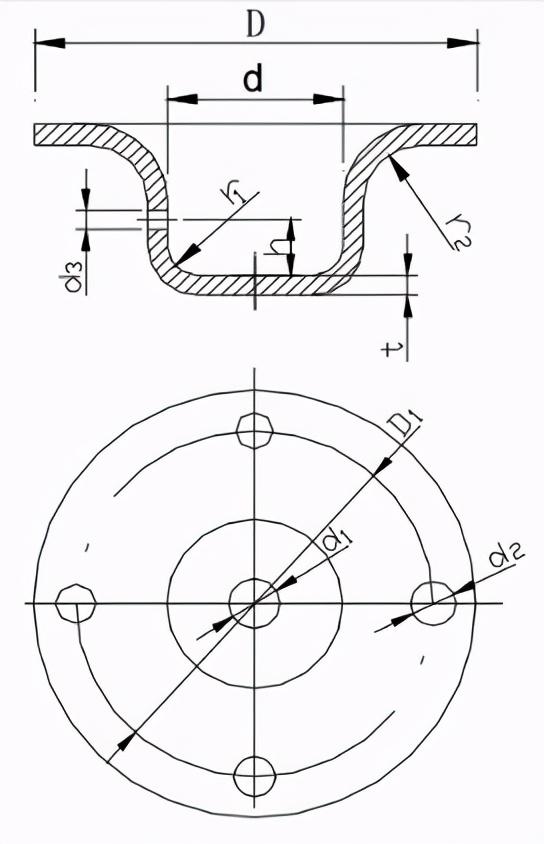
2.2 Obrázok zaokrúhlenia medzi bránou a stenou roztiahnutej časti
Polmer filéty medzi flangom a stenou roztiahnutej časti by mal byť väčší ako dvakrát hrúbka tabuľky, t. j. r22t. Aby sa proces roztiahnutia zvyčajne dosiahol hladnejší, vznikne r2=(5-10) t a maximálny polomer flange by mal byť menej alebo rovný 8-násobku hrúbky tabuľky, t. j. r28t. (Pozri uvedené číslo)
2.3 Priemer vnútornej dutiny kruhových roztiahnutých častí
Vnútorný priemer kruhového ťahového kusu sa má vziať ako D d+10t, aby sa tlaková tabuľka počas ťahovania pevne tlačila bez mraknutia. (Pozri uvedené číslo)
2.4 Obrázok zaokrúhlenia medzi vedľajšími stenami pravouhlých roztiahnutých častí
Polmer filéty medzi vedľajšími stenami obdĺžnikového roztiahnutého kusu by sa mal vziať ako r3 3t. Aby sa znížil počet roztiahnutí, r3 H/5 by sa mal vziať čo najviac, aby sa mohol vytiahnuť jednorazovo.
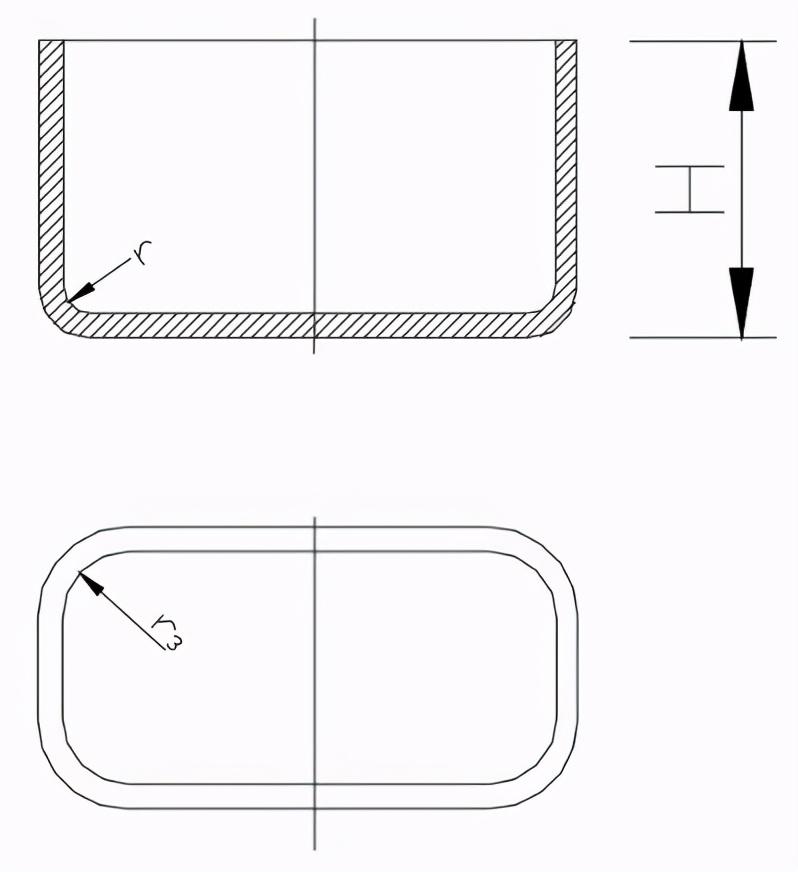
Požiadavky na rozmerný vzťah medzi výškou a priemerom 2,5 okrúhlej časti bez prieťahu počas jednorazového tvorby
Pri tvorbe okrúhlej časti bez prieťahu v jednom pohybe by mal byť pomer výšky H k priemeru d menší alebo rovný 0,4, t. j. H/d 0,4, ako sa uvádza na nasledujúcom obrázku.
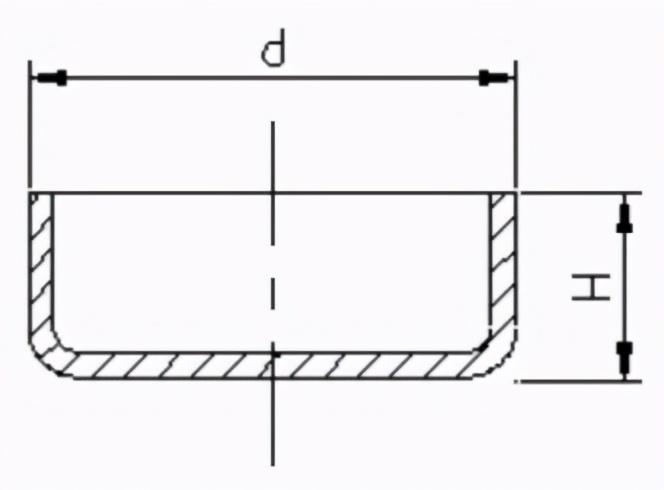
2.6 Variácia hrúbky roztiahnutého materiálu:
Hrúbka roztiahnutého materiálu sa mení v dôsledku rôznych úrovní napätia, ktoré sa uplatňujú na každú časť. Vo všeobecnosti sa pôvodná hrúbka udržiava v strede dna, materiál v zaokrúhlených rohoch dna sa stane tenkší, materiál v blízkosti flange na vrchu sa stane hrúbším a materiál okolo zaokrúhlených rohov pravouhlého roztiahnutej časti sa stane hrúbším.
2.7 Metóda označovania rozmerov výrobku roztiahnutých častí
Pri navrhovaní výrobkov na ťahu by sa mali jasne uviesť rozmery na kresle výrobku, aby sa zabezpečilo zaručenie vonkajších aj vnútorných rozmerov a vnútorných a vonkajších rozmerov nemožno označiť súčasne.
2.8 Metóda zaznamenávania rozmerných tolerancií roztiahnutých častí
Vnútorný polomer konkávneho konvexného uhla roztiahnutej časti a tolerancia výšky rozmeru cylindrickej roztiahnutej časti vytvorenej v jednom pohybe sú dvojstranné symetrické odchýlky s odchýlkou polovice absolútnej hodnoty presnej tolerancie vnútroštátnej normy (GB) úrovne 16 a sú číslované.
3. Ostatné tvorby plechových kovov: posilnenie rebier - Tlačenie rebier na rovné kovové časti pomáha zvýšiť štrukturálnu rigiditu.
Louvers – Louvers sa bežne používajú na rôznych nádobách alebo nádobách na zabezpečenie ventilácie a rozptýlenia tepla.
Fľanka diery (prieťahová diera) – používaná na strojové nity alebo zvýšenie pevnosti otvorenia diery.
3.1 Posilnenie:
Posilnenie štruktúry a výberu veľkosti
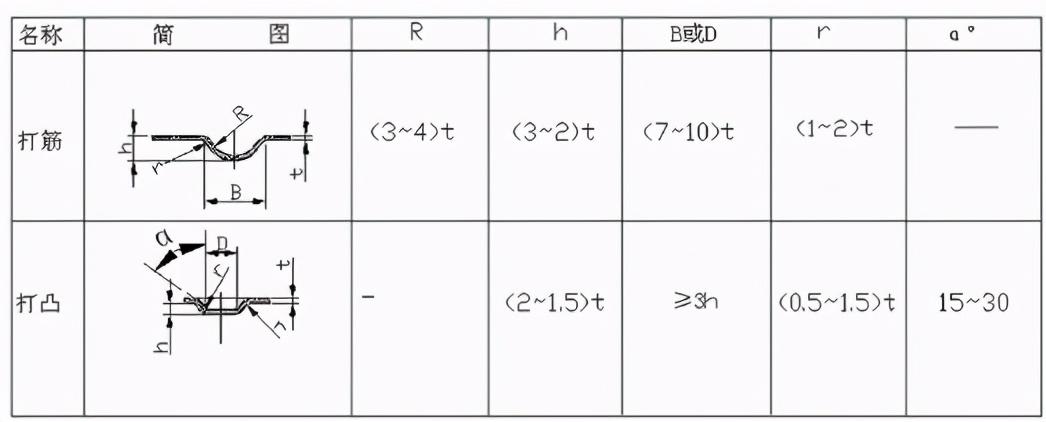
Maximálne rozmery konvexného priestoru a konvexnej vzdialenosti okraja sa vyberú podľa nižšie uvedenej tabuľky.
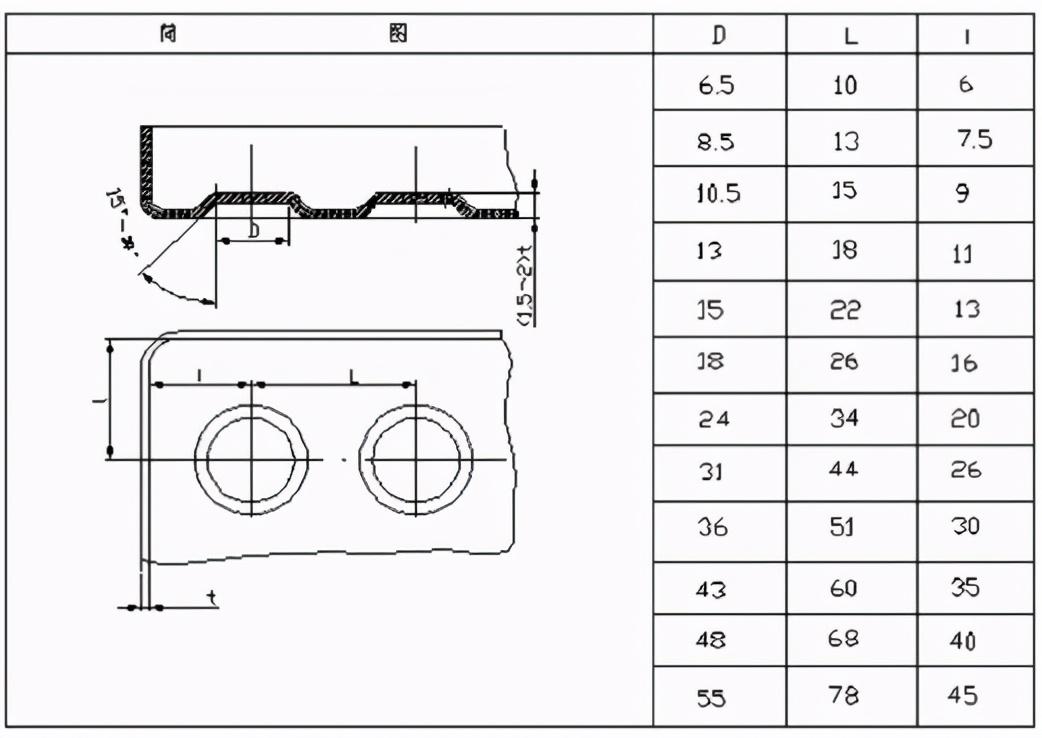
3.2 Louvers
Metódou tvorby slepín je otvoriť materiál jedným okrajom konvexného tvaru, zatiaľ čo zvyšné časti konvexného tvaru sa súčasne roztiahnu a deformujú materiál a tvoria neobmedzený tvar s otvorením jednej strany.
Typická štruktúra farby je zobrazená na nasledujúcom obrázku:
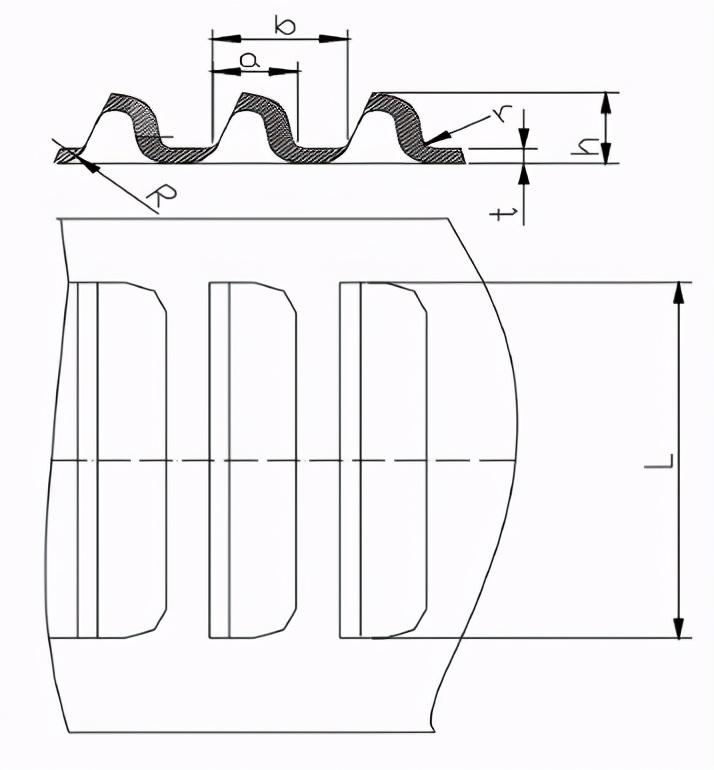
Požiadavka na vyššiu veľkosť: a4t; b6t;h5t;L24t;r0.5t。
3.3 Plynovanie dier (prieťahové diery)
Existujú mnohé formy otvorenia, a bežným je strojovať vnútornú otvorenie otvorenia vlákien.
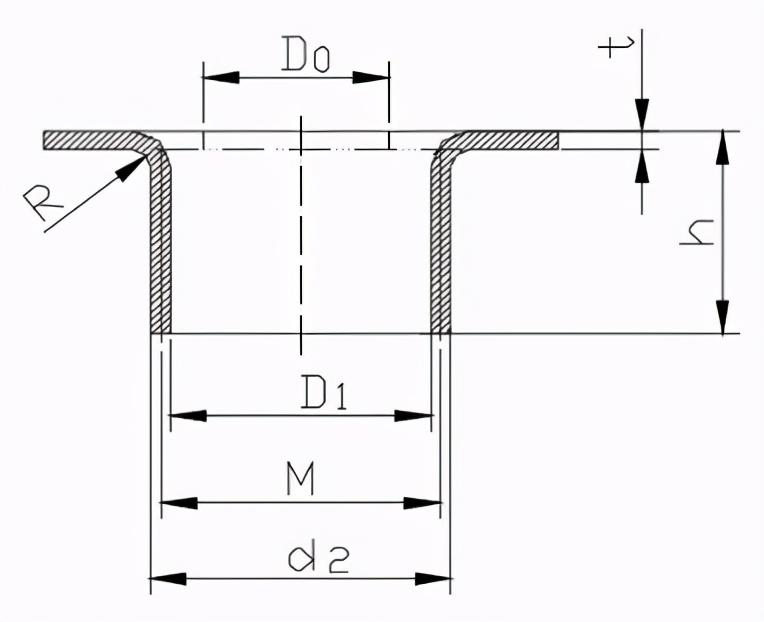
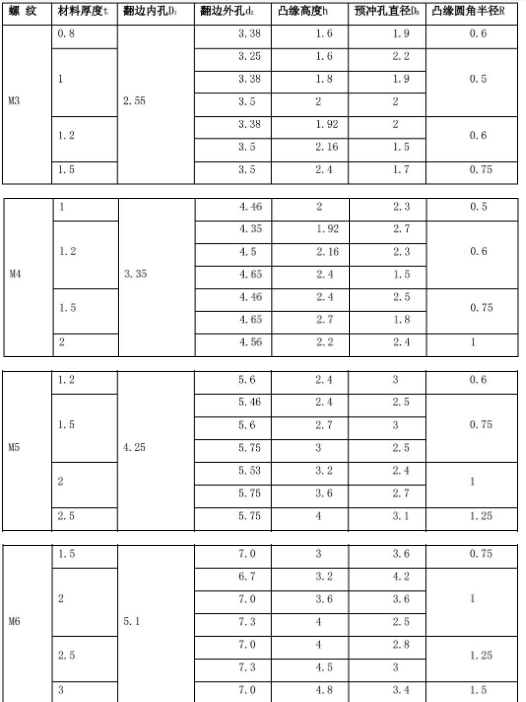
Technológia spracovania listových kovov – riedenie iných spracovaných listových kovových príslušenstiev, ako sú riedkové orechy, riedkové kryty, riedkové príručné stĺpce atď.
2. Vkladanie vláknených dier na kovové listy.
Hrúbka kovových listov t< O 1.5 hodine, použite obrátený tep. Keď je hrúbka kovového listu t1,5, môže sa použiť priame priťahovanie.
Technológia spracovania listových kovov – Pri zváraní pri konštrukcii zváracích konštrukcií listových kovov by sa mala implementovať s cieľom „symetricky nastaviť zvárania a zváracie body a zabrániť prierezu, agregácii a prekrývaniu. Sekundárne zvárania a zváracie body sa môžu prerušiť a hlavné zvárania a zváracie body by sa mali pripojiť.“
Sverovanie bežne používané v listových kovoch zahŕňa zváranie uhlov, zváranie odolnosti atď.
Medzi zváracími listami s uhlom by mal byť dostatočný priestor na zváranie a maximálny zvárací priestor by mal byť medzi 0,5 a 0,8 mm. zvárací závor by mal byť jednotný a rovný.
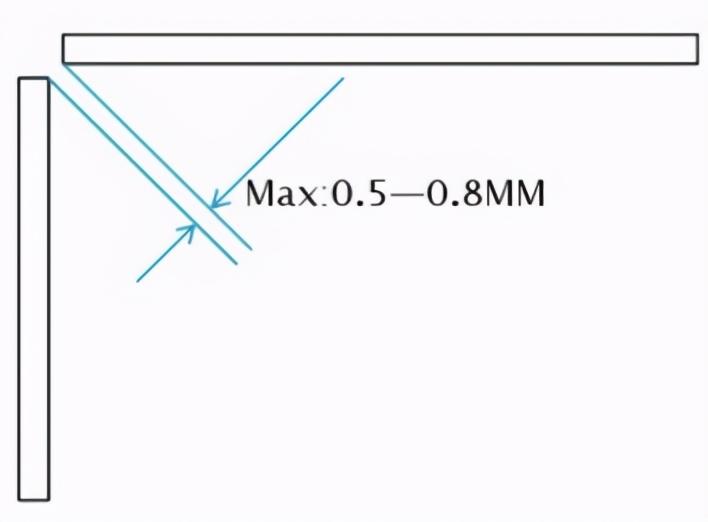
2. zvárací povrch zvárania odolnosti by mal byť rovný, bez škriatkov, opätovného zvárania atď.
Rozmery zvárania odolnosti sú uvedené v nasledujúcej tabuľke:
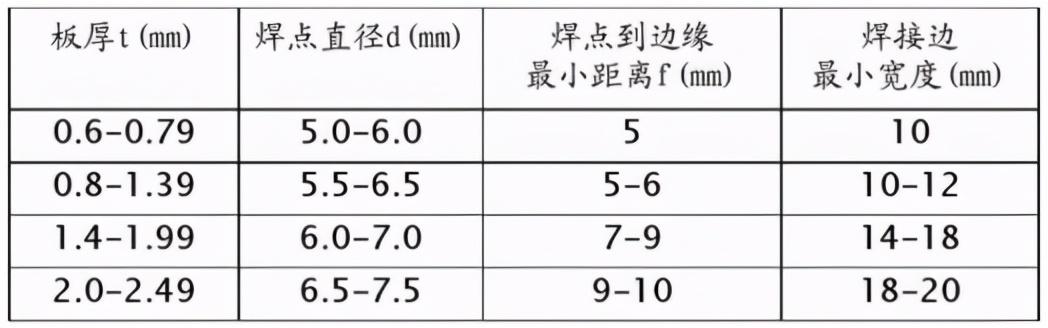
vzdialenosť medzi kĺbami rezistentného roztoku
Pri praktických aplikáciách sa pri zváraní malých častí môžu uvádzať údaje uvedené v nižšie uvedenej tabuľke.
Pri zváraní veľkých častí sa vzdialenosť medzi bodmi môže primerane zvýšiť, zvyčajne nie nižšia ako 40-50 mm. V prípade neostresovaných častí sa vzdialenosť medzi zváracími bodmi môže rozšíriť na 70-80 mm.
Hrúbka dosky t, priemer kĺbov rozpúšťa ča d, minimálny priemer kĺbov rozpúšťača dmin a minimálna vzdialenosť e medzi kĺbami rozpúšťača. Ak je doska kombinovaná rôznymi hrúbkami, vyberte podľa najtenkejšej dosky.
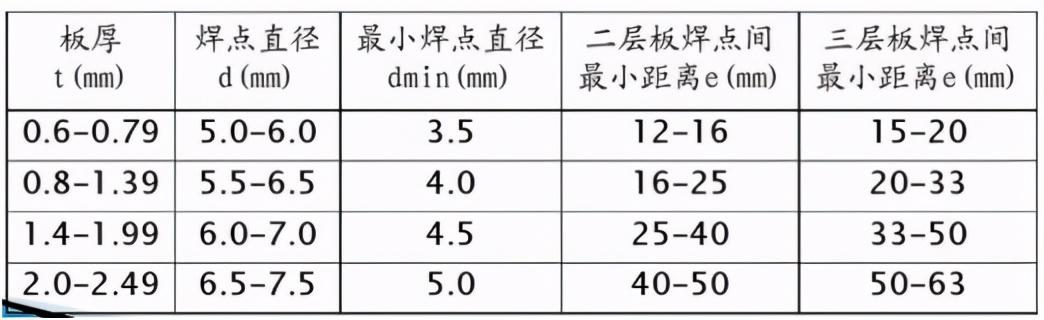
Počet vrstiev a pomer hrúbky materiálu vo zváracích listoch odolnosti
Plášť kovov na zváranie na mieste odolnosti je vo všeobecnosti 2 vrstvy s maximálne 3 vrstvami. Pomer hrúbky každej vrstvy zváraného kĺbu by mal byť medzi 1/3 a 3.
Ak je potrebné zvárať trojrozmernú tabuľku, najskôr by sa mal kontrolovať pomer hrúbky materiálu. Ak je to primerané, zváranie sa môže vykonať. Ak nie je to primerané, mali by sa zvážiť spracovateľské diery alebo spracovateľské škvrny. V prípade dvojrozmerného zvárania by sa mali zváracie body rozdeliť.
Technológia spracovania listových kovov – Metódy spojenia: Týmto sa zavádzajú najmä metódy spojenia listových kovov počas spracovania vrátane riveting, zvárania (ako sa uvádza vyššie), riveting vyťahovania dier a TOX riveting.
Rivet riveting: Tento typ rivet sa zvyčajne nazýva pull rivet, ktorý zahŕňa riveting dvoch kusov plechového kovu spolu cez pull rivet. Spoločné riveting tvary sú zobrazené na obrázku:
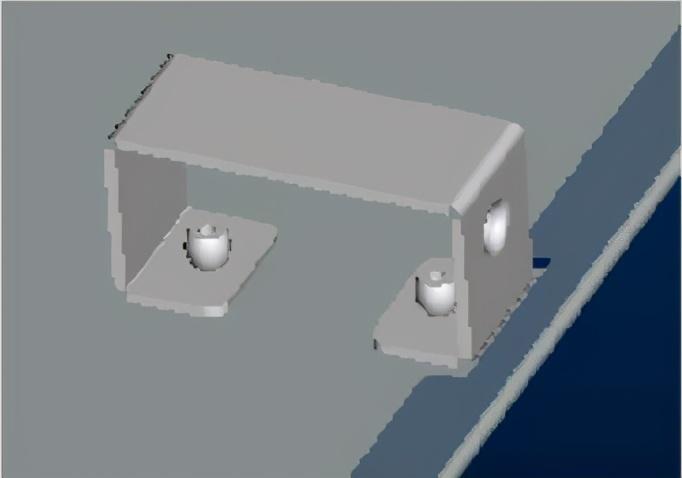
2. zváranie (ako už bolo uvedené) 3. výkres a riešenie: jedna čas ť je prieťahová diera a druhá časť je prieťahová diera, ktorá sa vyrába do neoddeliteľného spojovacieho tela prostredníctvom riešenia.
Výťažná diera a jej zodpovedajúca topiaca diera majú polohovaciu funkciu. Riečná sila je vysoká a účinnosť riečania cez moldy je tiež relatívne vysoká.
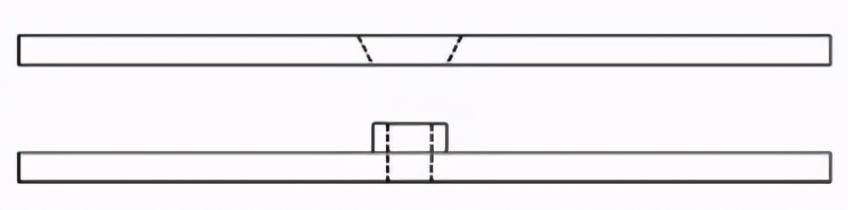
4. TOX riveting: Tlačte spojenú časť do konkávneho tvaru jednoduchým konkávnym tvarom. Pod ďalším tlakom sa materiál vo vnútri konkávneho tvaru vyteká vonku. Výsledkom je kruhový spojovací bod bez akýchkoľvek okrajov alebo vlákien, ktorý neovplyvňuje jeho odolnosť voči korózii. Aj v prípade dosiek s vrstvou náterovej farby alebo rozprašovacej farby na povrchu sa môžu zachovať pôvodné charakteristiky odolnosti voči korózii a hrudníku, pretože vrstva náterovej farby a náterovej farby môžu zachovať aj pôvodné charakteristiky odolnosti voči hrudníku a korózii, keďže vrstva náterovej farby sa tiež deformujú a pret Materiál sa stlačí na obidve strany a do tabuľky vedľa konkávneho tvaru a tvorí TOX spojovacie bodky. Ako sa uvádza na nasledujúcom obrázku:
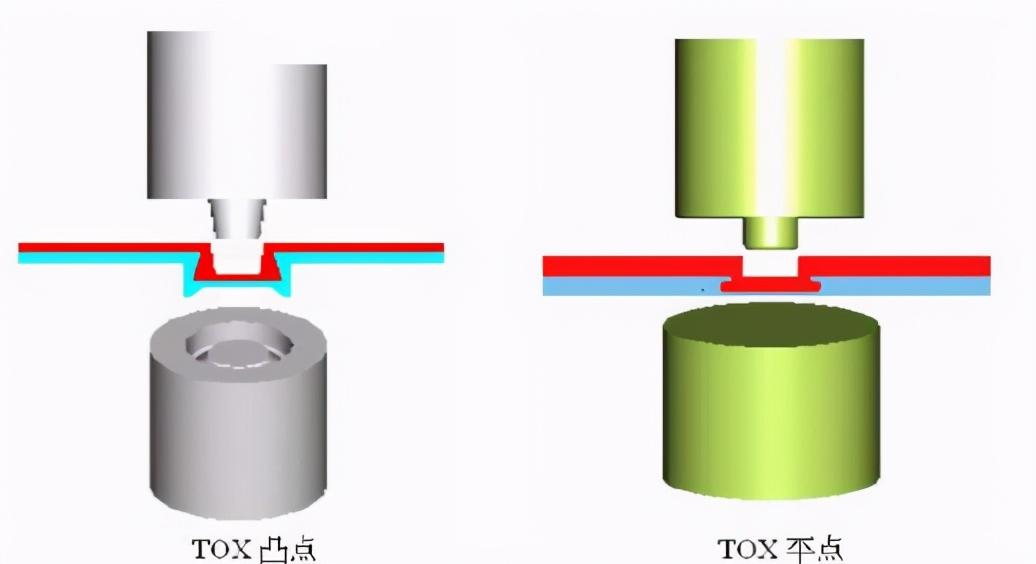
Technológia spracovania listových kovov – Spracovanie povrchu môže zabezpečiť ochranu proti korózii a dekoratívne účinky na povrch listových kovov. Spoločné povrchové ošetrenia pre plechové kovy zahŕňajú spraying prášku, elektrogalvanizáciu, galvanizáciu tepla, oxidáciu povrchu, výkres povrchu, tlač obrazovky atď.
Pred povrchovou úpravou listových kovov sa majú z povrchu listových kovov odstrániť olejové farby, hrudník, zváracia špina atď.
Práškové rozprašovanie: Existujú dva typy povrchového rozprašovania pre plechové kovy: tekuté a práškové farby. Obyčajne používané je práškové farby. Sprašovaním prášku, elektrostatickou adsorpciou, vysokoteplotným pekením a inými metódami sa na povrchu plechového kovu rozprašuje vrstva rôznych farbov, aby sa vylepšil vzhľad a zvýšila protikorózia materiálu. Je to bežne používaná metóda povrchovej úpravy.
Poznámka: Môže existovať určitý farebný rozdiel v farbách rozprašovaných rôznymi výrobcami, takže na tom istom zariadení by sa metaly z listov rovnakej farby mali rozprašovať od toho istého výrobcu čo najviac.
(2) Povrchová galvanizácia galvanizovaného a teplo-dip galvanizovaného listového kovu je bežne používaná metóda antikoróznej úpravy povrchu a môže zohrávať určitú úlohu pri nádhere vzhľadu. Galvanizácia sa môže rozdeliť na elektrogalvanizáciu a galvanizáciu tepla.
Výhľad elektrogalvanizácie je relatívne jasný a rovný s tenkou galvanizovanou vrstvou, ktorá sa bežne používa.
Obal zinku s teplým podliatím je hrúbší a môže vytvárať vrstvu zliatin zinku so železom, ktorá má silnejšiu koróznu odolnosť ako elektrogalvanizácia.
3. Oxidácia povrchu: Týmto sa predovšetkým zavádza povrchová anodizácia hliníkových a hliníkových zliatin.
Povrchové anodizovanie hliníkových a hliníkových zliatin sa môže oxidovať na rôzne farby, čo poskytuje ochranné aj dekoratívne účinky. Zároveň sa na povrchu materiálu, ktorý má vysokú tvrdosť a odolnosť voči noseniu, ako aj dobré vlastnosti elektrickej izolácie a tepelnej izolácie môže formovať film s oxidom anodíkom.
4. Výkres povrchového drôtu: Umiestnite materiál medzi horné a dolné valce drôtového ťahovacieho zariadenia s pieskovým pásom pripevneným k valcom. Vedený motorom, materiál prechádza cez horné a dolné pieskové pásy a ponecháva značky na povrchu materiálu. Hrúbka značiek sa líši v závislosti od typu pieskového pásu a ich hlavnou funkciou je vylepšenie vzhľadu. Metóda povrchovej úpravy drôtového ťahu sa zvyčajne zváži v prípade hliníkových materiálov.
5. Tlač obrazovky je proces tlačenia rôznych označení na povrchu materiálov. Vo všeobecnosti existujú dve metódy: tlač na plochú obrazovku a prenos. Tlač na plochú obrazovku sa používa hlavne na všeobecných plochých povrchoch, ale ak existujú hlbšie diery, je potrebné prenos tlačenia.
Tlač hodvábneho obrazu si vyžaduje hodvábne tvary.
Referenčné pripojenie na presnosť spracovania kovov listov:
GBT13914-2002 Rozmerné tolerancie pre pečiatkové časti
GBT13915-2002-T Tolerancia uhlových uhlových častí
GB-T15005-2007 Tlačené časti – Obmedzujúce odchýlky bez špecifikovaných tolerancií
GB-T 13916-2002 Tlačené časti – tvar a poloha bez špecifikovaných tolerancií
schopnosť bežne používaných zariadení na spracovanie kovových listov a rozsah spracovania bežných kovových listov
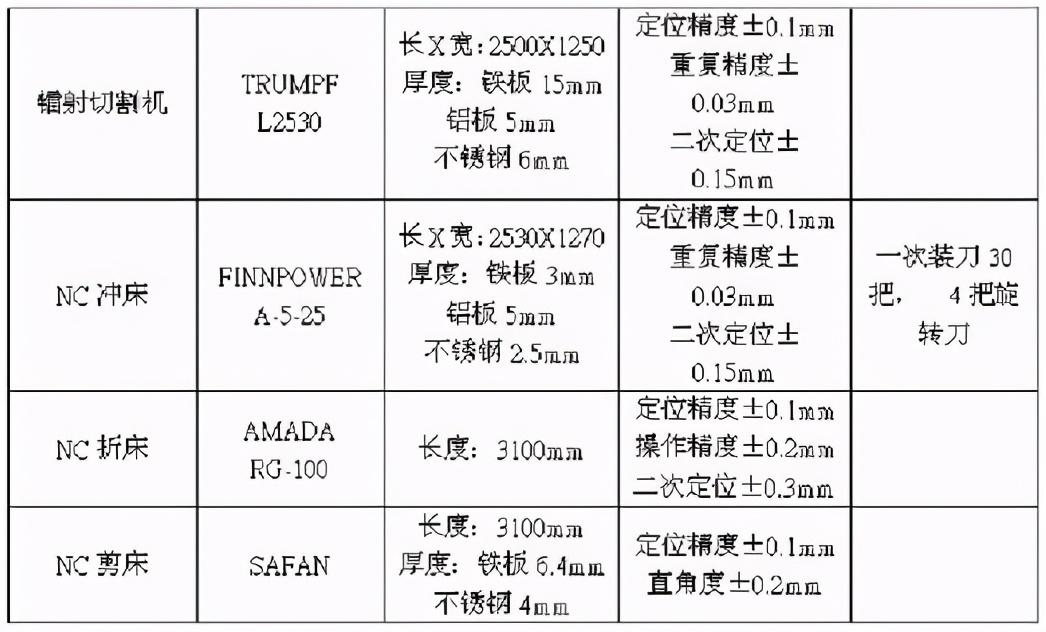