Kako določiti procesne parametre laserskega rezanja v Shenyang?
Načelo delovanja laserskega rezanja
Laserska obdelava nadomešča tradicionalne mehanske nože z nevidnimi žarki in ima značilnosti visoke natančnosti, hitrega rezanja, ki ni omejeno na rezalne vzorce, avtomatsko oblikovanje za varčevanje materialov, gladkega rezanja in nizkih stroškov obdelave.Postopoma bo izboljšala ali nadomestila tradicionalno opremo za rezanje kovin. Mehanski del laserskega rezila nima stika z obdelovancem in med delovanjem ne bo povzročil prask na površini obdelovanca; Hitrost laserskega rezanja je hitra, rez je gladek in raven in na splošno ne zahteva nadaljnje obdelave; Območje, prizadeto s toploto rezanja, je majhno, deformacija plošče je majhna, rezalni šiv pa je (0,1 mm ~ 0,3 mm); Rez nima mehanske obremenitve in strižnih rebrcev; Visoka natančnost obdelave, dobra ponovljivost in brez poškodb materialne površine; Programiranje numeričnega krmiljenja, ki lahko obdeluje kateri koli ravni načrt, lahko reza velike celotne plošče brez potrebe po kalupih, kar prihrani čas in ekonomičnost.
Sestava opreme za lasersko rezanje
Oprema za lasersko rezanje je sestavljena predvsem iz laserja, svetlobnega vodilnega sistema, CNC sistema gibanja, avtomatske rezalne glave za nastavitev višine, delovne ploščadi in visokotlačnega sistema za pihanje plina. Številni parametri lahko vplivajo na postopek laserskega rezanja, od katerih so nekateri odvisni od tehnične zmogljivosti laserja in obdelovalnega orodja, medtem ko so drugi spremenljivi. Glavni parametri laserskega rezanja so:
Glavni parametri laserskega rezanja
1 način žarka
Temeljni način, znan tudi kot gausijski način, je idealen način rezanja, ki se pojavlja predvsem v laserjih z nizko močjo z močjo manj kot 1 kW. Multimode je mešanica načinov višjega reda, s slabim ostrenjem in nizko zmožnostjo rezanja pri isti moči.
2 laserska moč
Laserska moč, potrebna za lasersko rezanje, je odvisna predvsem od rezalnega materiala, debeline materiala in zahtev po hitrosti rezanja. Laserska moč pomembno vpliva na debelino rezanja, hitrost rezanja in širino rezanja. Na splošno, ko se laserska moč povečuje, se poveča tudi debelina materiala, ki ga je mogoče rezati, pospeši hitrost rezanja in poveča se tudi širina reza.
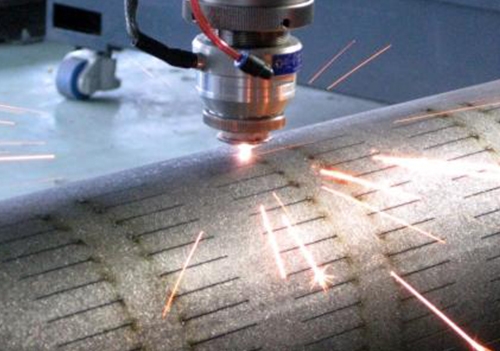
3 položaji ostrenja
Goriščni položaj pomembno vpliva na širino reza. Na splošno je fokus izbran tako, da se nahaja približno tretjina debeline pod površino materiala, z večjo globino rezanja in manjšo širino ust.
4 fokusni momenti
Pri rezanju debelejših jeklenih plošč je treba uporabiti žarek z daljšo goriščno razdaljo, da se dobi rezalna površina z dobro navpičnostjo. Globina ostrenja se poveča, poveča se tudi premer svetlobne točke, gostota moči pa se ustrezno zmanjša, kar povzroči zmanjšanje hitrosti rezanja. Da bi ohranili določeno hitrost rezanja, je treba povečati lasersko moč. Priporočljivo je uporabiti žarek z manjšo goriščno razdaljo za rezanje tankih plošč, kar ima za posledico manjši premer točk, večjo gostoto moči in hitrejšo hitrost rezanja.
5 Pomožni plini
Rezanje nizkoogljičnega jekla pogosto uporablja kisik kot rezalni plin za spodbujanje procesa rezanja z uporabo toplote reakcije zgorevanja kisika železa.Poleg tega je hitrost rezanja hitra, kakovost rezanja je dobra in lahko dobimo rezanje brez žlindre. Tlak se poveča, kinetična energija se poveča in zmogljivost praznjenja žlindre se poveča; Tlak rezanja se določi na podlagi dejavnikov, kot so material, debelina plošče, hitrost rezanja in kakovost rezalne površine.
6 struktura šobe
Na kakovost in učinkovitost laserskega rezanja vplivata tudi struktura in oblika šobe ter velikost svetlobne vtičnice.Različne zahteve za rezanje zahtevajo uporabo različnih šob. Običajno uporabljene oblike šobe vključujejo valjaste, stožčaste, kvadratne in druge oblike. Lasersko rezanje običajno uporablja koaksialno (koncentrično pretok zraka z optično os), če pretok zraka ni poravnan z optično os, se med rezanjem zlahka ustvari velika količina brizganja. Da bi zagotovili stabilnost procesa rezanja, je običajno treba nadzorovati razdaljo med končno površino šobe in površino obdelovanca, ki je običajno 0,5-2,0 mm, da bi olajšali gladko rezanje.
Če imate kakršna koli vprašanja, me kontaktirajte, da ga izbrišete!