Hur man bestämmer processparametrarna för laserskärning i Shenyang?
Arbetsprincip för laserskärning
Laserskärning bearbetning ersätter traditionella mekaniska knivar med osynliga balkar och har egenskaper som hög precision, snabb skärning, inte begränsat till skärmönster, automatisk typinställning för att spara material, smidig skärning och låga bearbetningskostnader.Det kommer gradvis att förbättra eller ersätta traditionell metallskärningsutrustning. Den mekaniska delen av laserbladet har ingen kontakt med arbetsstycket och kommer inte att orsaka repor på arbetsstyckets yta under drift; Laserskärningshastigheten är snabb, snittet är slät och platt och kräver generellt inte ytterligare bearbetning; Den skärvärmepåverkade zonen är liten, deformationen av brädet är liten och skärsömmen är (0,1 mm ~ 0,3 mm); Snittet har ingen mekanisk påfrestning och inga skjuvbärar; Hög bearbetningsnoggrannhet, god repeterbarhet och ingen skada på materialytan; Numerisk styrprogrammering, som kan bearbeta alla plan planer, kan skära stora hela skivor utan behov av formar, vilket sparar tid och ekonomi.
Sammansättning av laserskärutrustning
Laserskärningsutrustning består huvudsakligen av laser, ljusstyrsystem, CNC-rörelsesystem, automatisk höjdjustering skärhuvud, arbetsplattform och högtrycksgasblåssystem. Många parametrar kan påverka laserskärningsprocessen, varav vissa beror på laserns och verktygsmaskinens tekniska prestanda, medan andra är variabla. De viktigaste parametrarna för laserskärning är:
Huvudparametrar för laserskärning
1 Strålningsläge
Det grundläggande läget, även känt som Gaussian mode, är det idealiska läget för skärning, främst visas i lågeffektlasrar med en effekt på mindre än 1 kW. Multimode är en blandning av höggradiga lägen, med dålig fokusering och låg skärförmåga vid samma effekt.Enlägeslaser har bättre skärförmåga och kvalitet än multimode lasrar.
2 lasereffekt
Den lasereffekt som krävs för laserskärning beror huvudsakligen på skärmaterialet, materialtjockleken och skärhastighetskraven. Laserskraft har en betydande inverkan på skärtjocklek, skärhastighet och skärbredd. Generellt ökar också tjockleken på det material som kan skäras, skärhastigheten accelereras och snittbredden ökar också.
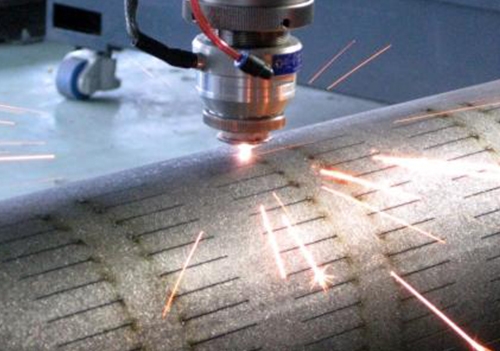
3 Fokuspositioner
Fokuspositionen har en betydande inverkan på snittets bredd. Generellt väljs fokus för att ligga ungefär en tredjedel av tjockleken under materialytan, med ett större skärdjup och en mindre munbredd.
4 fokusmoment
Vid skärning av tjockare stålplåtar bör en balk med längre brännvidd användas för att få en skäryta med god vertikalitet. Fokusdjupet ökar, ljuspunktens diameter ökar också och effekttätheten minskar därefter, vilket resulterar i en minskning av skärhastigheten. För att upprätthålla en viss skärhastighet är det nödvändigt att öka lasereffekten. Det är lämpligt att använda en stråle med mindre brännvidd för skärning av tunna plattor, vilket resulterar i en mindre punktdiameter, högre effekttäthet och snabbare skärhastighet.
5 Hjälpgaser
Skärning av lågkolstål använder ofta syre som skärgas för att främja skärprocessen genom att utnyttja värmen från järn syreförbränningsreaktion.Dessutom är skärhastigheten snabb, skärkvaliteten är god och en slaggfri skärning kan erhållas. Trycket ökar, den kinetiska energin ökar och slagglödningskapaciteten förbättras; Skärtrycket bestäms utifrån faktorer som material, plåttjocklek, skärhastighet och skärytkvalitet.
6 munstycke struktur
Munstyckets struktur och form samt storleken på ljusutloppet påverkar också laserskärningens kvalitet och effektivitet. Olika skärkrav kräver användning av olika munstycken. De vanligaste munstyckeformerna inkluderar cylindriska, koniska, fyrkantiga och andra former. Laserskärning använder vanligtvis koaxial (luftflöde koncentriskt med den optiska axeln) blåsmetod Om luftflödet inte är i linje med den optiska axeln genereras en stor mängd stänk lätt under skärningen. För att säkerställa skärprocessens stabilitet är det vanligtvis nödvändigt att kontrollera avståndet mellan munstyckets ändyta och arbetsstyckets yta, som i allmänhet är 0,5-2,0 mm, för att underlätta jämn skärning.
Innehållet i artikeln kommer från internet, om du har några frågor, kontakta mig för att radera den!