I dagens samhälle, med den ökande användningen av plåtbearbetning i Shenyang, har utformningen av plåtdelar blivit en viktig del av produktutvecklingsprocessen.Varje maskiningenjör är skyldig att behärska designfärdigheter för plåtdelar skickligt, vilket gör det möjligt för den konstruerade plåten att uppfylla hårdvarukraven för produktens funktion och utseende, samt förenkla stansningsformproduktionsmetoden och minska den erforderliga kostnaden. Egenskaperna hos plåtdelar inkluderar låg vikt, hög hållfasthet, ledningsförmåga (som kan användas för elektromagnetisk skärmning), låg kostnad och god massproduktionsprestanda.De har använts i stor utsträckning inom områden som elektronik, kommunikation, bilindustri, medicinsk utrustning, etc. Till exempel plåtdelar är en viktig komponent i datorfodral, mobiltelefoner, MP3-spelare och ljudsystem.
Vanliga problem och orsaker vid bearbetning av plåt och stansning av delar
1. Burr: Under processen med stansning eller skärning av hörn lämnas ofullständigt överskottsmaterial, och fräsar uppstår vid den nedre delen av stålplattans tvärsnitt. När höjden på fräsar är 0,2 mm eller mer baserat på tvärsnittet, kommer järnpulvret som genereras att skada formen och orsaka stötar och depressioner.
2. Krossningen av valsmaterialet kan resultera i rynkningar i kanterna: Styrvalsarna på varvningslinjen kan orsaka rynkningar när gapet mellan styrvalsarna på formen är liten, vilket orsakas av att valsmaterialet matas in i den icke givande balansen.
3. glidning utskrift: Det orsakas av glidning av rullen och inträffar mestadels när plötsligt stannar eller accelererar.
4. Repor: Den primära orsaken till repor på delar är vassa repor på formen eller metalldamm som faller i formen.sättet att undvika repor är att slipa repor på formen och ta bort metalldamm.
Konvex konkav: onormala utskjutningar eller tryckningar på ytan av ett material, orsakade av främmande föremål (järnfiling, damm) blandas in under nedbrytningsprocessen.
6. Bottom sprickor: Den primära orsaken till botten sprickor i delar beror på dålig plasticitet hos materialet eller överdriven knådning av formkantpressringen.För att undvika detta, ersätta materialet med bättre plasticitet eller lossa kantpressringen.
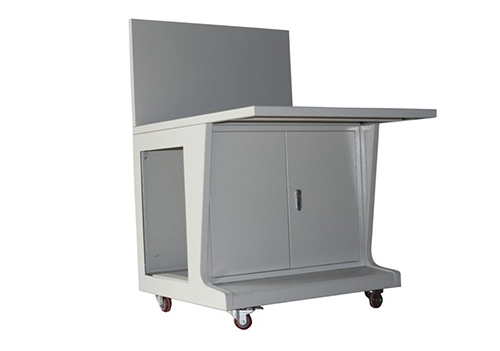
Rulltryck: Rengöring av rullen kan leda till att främmande föremål fäster vid matarrullen (förekommer i en fast höjd), men i allmänhet kan valstryck främmande föremål på arket tas bort.
8. rynkor på sidoväggen: Den primära orsaken till rynkor på sidoväggen av en komponent beror på otillräcklig tjocklek av materialet (relativt liten tjocklek tillåts vara tunnare) eller en liten smärta under övre och nedre mögel installation, vilket resulterar i ett stort gap på ena sidan och ett litet gap på den andra sidan.Undantagsmetoden är att ersätta materialet omedelbart eller justera formen från scratch.
Numerisk kontrollteknik används ofta i plåtmaskiner, vilket löser vissa problem vid plåtbearbetning såsom hög precision, oordnad form och stor satsstorlek av delar.
CNC plåtmaskiner inkluderar CNC skärmaskiner, CNC laserskärmaskiner, CNC stansmaskiner, CNC bockmaskiner, svetsmaskiner, flamskärmaskiner och andra verktygsmaskiner. Deras användning i produktionen förbättrar avsevärt plåtbearbetningsförmågan, säkerställer kvaliteten och utgångsvärdet för plåtdelar, och minskar också arbetsintensiteten hos arbetarna avsevärt.
Plåtbearbetning blir alltmer intelligent tack vare ovannämnda teknik, och de resulterande uppgifterna blir alltmer exakta.
Innehållet i artikeln kommer från internet, om du har några frågor, kontakta mig för att radera den!