ในกระบวนการตัดแผ่นโลหะด้วยเครื่องตัดเลเซอร์เสิ่นหยางมักพบปัญหาต่าง ๆ เพื่อรับประกันคุณภาพการตัดต่อไปนี้เป็นปัญหาทั่วไปและวิธีแก้ปัญหาทั่วไป:
1. เทคโนโลยีการตัดและเจาะรู:
เทคโนโลยีตัดความร้อนใด ๆ ยกเว้นบางกรณีสามารถเริ่มต้นจากขอบของแผ่นโดยทั่วไปจะต้องสวมใส่รูเล็ก ๆ บนแผ่น ก่อนหน้านี้ในเครื่องเคลือบปั๊มเลเซอร์ใช้หมัดเจาะรูก่อน จากนั้นใช้เลเซอร์เพื่อเริ่มตัดจากรูเล็ก ๆ มีสองวิธีพื้นฐานของการเจาะสำหรับเครื่องตัดเลเซอร์โดยไม่ต้องเจาะอุปกรณ์:
การเจาะแบบระเบิด - วัสดุหลังจากการฉายรังสีด้วยเลเซอร์อย่างต่อเนื่องจะสร้างหลุมที่แกนกลางจากนั้นวัสดุหลอมเหลวจะถูกลบออกอย่างรวดเร็วเพื่อสร้างรูโดยกระแสออกซิเจนโคแอกเซียลกับลำแสงเลเซอร์ ขนาดของรูทั่วไปมีความสัมพันธ์กับความหนาของแผ่นเส้นผ่าศูนย์กลางเฉลี่ยของการเจาะรูระเบิดคือครึ่งหนึ่งของความหนาของแผ่นดังนั้นรูพรุนของแผ่นหนากว่ามีขนาดใหญ่และไม่กลมไม่ควรใช้กับชิ้นส่วนที่ต้องการความแม่นยำในการประมวลผลสูง สามารถใช้กับเศษวัสดุเท่านั้น นอกจากนี้ เนื่องจากแรงดันออกซิเจนที่ใช้ในการเจาะรูจะเหมือนกับตอนที่ตัดจึงทำให้กระเด็นไปมาก
Pulse Perforation - เลเซอร์พัลส์ที่ใช้พลังงานสูงสุดทำให้วัสดุจำนวนน้อยละลายหรือไอระเหยมักใช้อากาศหรือไนโตรเจนเป็นก๊าซเสริมเพื่อลดการขยายตัวของรูเนื่องจากการออกซิเดชัน exothermic ความดันของก๊าซมีขนาดเล็กกว่าความดันออกซิเจนเมื่อตัด เลเซอร์พัลส์แต่ละตัวจะสร้างการฉีดอนุภาคขนาดเล็กซึ่งจะค่อยๆลึกลงไปดังนั้นเวลาในการเจาะแผ่นหนาจะใช้เวลาไม่กี่วินาที เมื่อเจาะเสร็จให้เปลี่ยนก๊าซเสริมเป็นออกซิเจนสำหรับตัดทันที ดังนั้นเส้นผ่านศูนย์กลางการเจาะมีขนาดเล็กและคุณภาพการเจาะดีกว่าการเจาะแบบระเบิด เลเซอร์ที่ใช้ในการนี้ไม่เพียง แต่ควรมีกำลังขับสูง สิ่งที่สำคัญกว่าคือคุณสมบัติของเวลาและพื้นที่ของลำแสงดังนั้นเลเซอร์ CO2 แบบไหลข้ามทั่วไปจึงไม่สามารถปรับให้เข้ากับความต้องการของการตัดด้วยเลเซอร์ได้ นอกจากนี้การเจาะพัลส์ยังต้องมีระบบควบคุมเส้นทางก๊าซที่เชื่อถือได้มากขึ้นเพื่อให้บรรลุประเภทของก๊าซการสลับความดันก๊าซและการควบคุมเวลาในการเจาะ
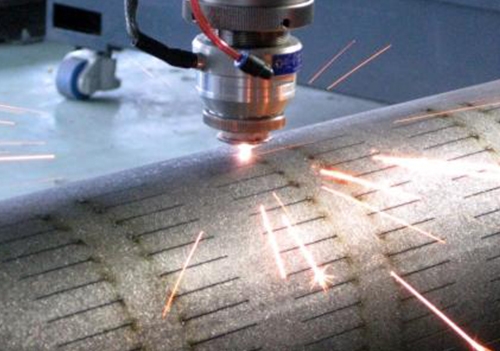
ในกรณีที่มีการเจาะพัลส์เพื่อให้ได้รอยบากที่มีคุณภาพสูงเทคโนโลยีการเปลี่ยนจากการเจาะพัลส์ในขณะที่ชิ้นงานหยุดนิ่งไปจนถึงการตัดชิ้นงานอย่างต่อเนื่องด้วยความเร็วเท่ากันควรให้ความสำคัญ ในทางทฤษฎีมักจะเปลี่ยนเงื่อนไขการตัดของส่วนการเร่งความเร็วเช่นความยาวโฟกัสตำแหน่งหัวฉีดความดันก๊าซ ฯลฯ แต่ในความเป็นจริงเนื่องจากเวลาสั้นเกินไปในการเปลี่ยนเงื่อนไขข้างต้นไม่น่าเป็นไปได้ ในการผลิตภาคอุตสาหกรรมส่วนใหญ่ใช้วิธีการเปลี่ยนพลังงานเฉลี่ยของเลเซอร์ค่อนข้างสมจริง วิธีการเฉพาะคือการเปลี่ยนความกว้างของพัลส์ เปลี่ยนความถี่พัลส์; เปลี่ยนความกว้างและความถี่ของพัลส์ในเวลาเดียวกัน ผลจริงปรากฏว่า แบบที่ 3 จะได้ผลดี
2. การวิเคราะห์สภาพการเปลี่ยนรูปของรูขนาดเล็ก (เส้นผ่านศูนย์กลางขนาดเล็กและความหนาของแผ่น):
นี่เป็นเพราะเครื่องมือเครื่อง (เฉพาะเครื่องตัดเลเซอร์กำลังสูง) ในการประมวลผลรูเล็ก ๆ ไม่ได้ใช้วิธีการเจาะระเบิด แต่ใช้วิธีการเจาะพัลส์ (การเจาะอ่อน) ซึ่งทำให้พลังงานเลเซอร์มีความเข้มข้นมากเกินไปในพื้นที่เล็ก ๆ และพื้นที่ที่ไม่ได้ประมวลผลจะถูกเผาไหม้ทำให้เกิดการเสียรูปของหลุมและส่งผลต่อคุณภาพการประมวลผล ในเวลานี้เราควรเปลี่ยนวิธีการเจาะพัลส์ (การเจาะอ่อน) เป็นวิธีการเจาะระเบิด (การเจาะทั่วไป) ในขั้นตอนการประมวลผลเพื่อแก้ไข สำหรับเครื่องตัดเลเซอร์ที่มีกำลังไฟน้อยกว่านั้นตรงกันข้ามควรใช้วิธีการเจาะแบบพัลส์ในการประมวลผลรูเล็ก ๆ เพื่อให้ได้พื้นผิวที่ดีขึ้น
เนื้อหาของบทความมาจากเว็บ, กรุณาติดต่อฉันถ้ามีปัญหาเพื่อลบ!