ในการแปรรูปชิ้นส่วนเหล็ก การตรวจสอบคุณภาพการเชื่อมเป็นส่วนสำคัญ ซึ่งเกี่ยวข้องโดยตรงกับคุณภาพโดยรวมและความปลอดภัยของชิ้นส่วน ต่อไปนี้เป็นประเด็นหลักของการตรวจสอบคุณภาพการเชื่อมของชิ้นส่วนเหล็ก นำเสนอในลักษณะที่ชัดเจนและเป็นจุด และพยายามอ้างอิงถึงตัวเลขและข้อมูลในบทความที่เกี่ยวข้อง: 1. การตรวจสอบก่อนการเชื่อม 1. โลหะฐานและวัสดุเชื่อม: ตรวจสอบวัสดุ ข้อมูลจำเพาะ ใบรับรองคุณภาพ ฯลฯ ของเหล็กและวัสดุเชื่อมเพื่อให้แน่ใจว่าตรงตามข้อกำหนดการออกแบบและมาตรฐานที่เกี่ยวข้อง 000@0002 ร่องและคู่: ตรวจสอบขนาด รูปร่าง และความสะอาดของร่อง ตลอดจนช่องว่าง จำนวนขอบที่เซ ฯลฯ หลังจากการจับคู่กลุ่ม เพื่อให้แน่ใจว่าตรงตามข้อกำหนดของกระบวนการเชื่อม3. อุปกรณ์เชื่อม: ตรวจสอบประสิทธิภาพและความสมบูรณ์ของอุปกรณ์เชื่อม (เช่นเครื่องเชื่อม ปืนเชื่อม ฯลฯ) รวมถึงการจัดหาแหล่งจ่ายไฟและก๊าซ 2. การตรวจสอบกระบวนการเชื่อม 1. พารามิเตอร์การเชื่อม: ตรวจสอบว่าพารามิเตอร์เช่นกระแสเชื่อมแรงดันไฟฟ้าความเร็วในการเชื่อมและพารามิเตอร์อื่น ๆ ถูกตั้งค่าอย่างถูกต้องและบันทึกพารามิเตอร์การเชื่อมจริง 2. การดำเนินการเชื่อม: สังเกตว่าการดำเนินการเชื่อมเป็นมาตรฐานเช่นมุมเชื่อม ลำดับการเชื่อม การเชื่อมรอบ ฯลฯ 3. การทำความสะอาดระหว่างชั้น: ตรวจสอบว่าสิ่งสกปรกเช่นตะกรันเชื่อมและการกระเด็นได้รับการทำความสะอาดในเวลาหลังจากการเชื่อมแต่ละชั้นเพื่อให้แน่ใจว่าคุณภาพของการเชื่อมชั้นถัดไป 3. การตรวจสอบหลังการเชื่อม 1. การตรวจสอบลักษณะที่ปรากฏ: พื้นผิวของรอยเชื่อมควรเรียบและเรียบโดยไม่มีข้อบกพร่องเช่นรอยแตกการรวมตะกรันและรูพรุนความกว้างและความสูงของรอยเชื่อมควรเป็นไปตามข้อกำหนดการออกแบบ และทั้งสองด้านของรอยเชื่อมควรเปลี่ยนอย่างสม่ำเสมอ ตรวจสอบว่ามีข้อบกพร่องที่ไม่ได้รับอนุญาต เช่น การกัดขอบ การเชื่อมไม่เต็ม และการหดตัวของรากหรือไม่ 2. การตรวจสอบขนาด: ใช้เครื่องมือวัดเพื่อตรวจสอบความเบี่ยงเบนของมิติ ความเบี่ยงเบนของรูปร่าง ฯลฯ ของรอยเชื่อมเพื่อให้แน่ใจว่าตรงตามข้อกำหนดของภาพวาดและข้อกำหนด 3. การทดสอบแบบไม่ทำลาย: สำหรับรอยเชื่อมที่สำคัญหรือซับซ้อน ควรทำการทดสอบแบบไม่ทำลาย เช่น การทดสอบเอ็กซ์เรย์ การทดสอบอัลตราโซนิก ฯลฯ เพื่อค้นหาข้อบกพร่องภายในรอยเชื่อม ตามเกรดและข้อกำหนดของรอยเชื่อม ควรทำการทดสอบแบบไม่ทำลายตามสัดส่วนและการเลือกวิธีการที่สอดคล้องกัน ตัวอย่างเช่น รอยเชื่อมหลักควรได้รับการตรวจสอบ UT (อัลตราโซนิก) 100% ในขณะที่รอยเชื่อมรองสามารถตรวจสอบ lOT (รังสี) ได้ 20%4. การทดสอบคุณสมบัติทางกล: ทำการทดสอบคุณสมบัติทางกลเช่นการทดสอบแรงดึงและการทดสอบแรงกระแทกตามความจำเป็นเพื่อประเมินความแข็งแรงและความเหนียวของรอยเชื่อม IV บันทึกและรายงาน 1. บันทึกการเชื่อม: บันทึกรายละเอียดพารามิเตอร์ต่าง ๆ ผลการตรวจสอบและข้อมูลอื่น ๆ ในกระบวนการเชื่อมเพื่อติดตามและวิเคราะห์ 2. รายงานการตรวจสอบ: ออกรายงานการตรวจสอบคุณภาพการเชื่อมที่สมบูรณ์ระบุระดับคุณภาพของรอยเชื่อมและปัญหาที่มีอยู่อย่างชัดเจนสำหรับการอ้างอิงและการใช้งานของผู้ใช้
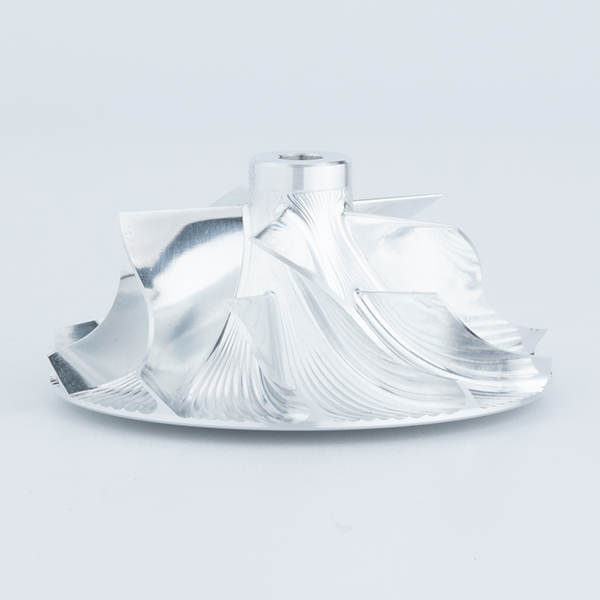