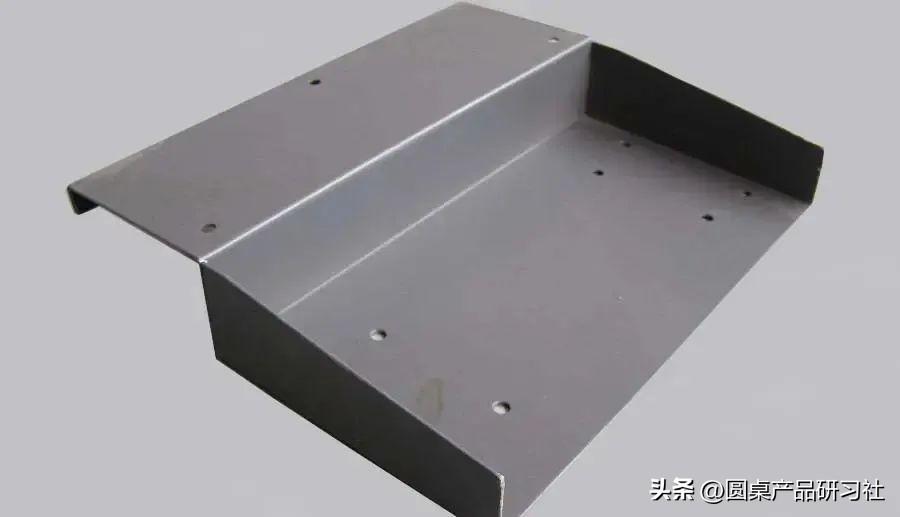
1, yatak işleme içeriğini kapatmak: 1. L katlamak 90 derece katlamaya ve 90 derece katlamaya göre bölüyor.
İşleme göre, genel işleme (L>V/2) ve özel işleme (L 1 Toplu materyal, tabak kalınlığı ve açı oluşturma üzerinde seçildir. 2. Güvenlik prensipi 1) İki arka pozisyon kurallarının ve çalışma parçasının şeklini göre yerine koyma prensipine dayandı. 2) Arka bölge yerleştirildiğinde, ayrılığa dikkat edin ve çalışma parças ının büyüklüğünün aynı merkezde olduğundan emin olun. 3) Küçük katları eğerken, onları tersi pozisyonda işlemek daha iyi. 4) Kuralları arkaya ve ortaya doğru koymak daha iyi. (Göreve karşı sıkıştığında, arka düzenin kaldırması kolay değil) 5) Görevin ve arka düzenin kenarına yakın olmak daha iyi. 6) Uzun tarafa güvenmek daha iyi. 7) Yerleştirmeye yardım etmek için fixtürler kullanın (düzensiz bir kenar pozisyonu). 3 , Özellikler 1. İşlenme sırasında ve çeşitli pozisyon işleme metodlarının arasında standartlaştırılmış hareket moduna dikkat vermelidir. 2. Kıpırdam toplandığında, çökme sırasında çalışma parçasının deformasyonu önlemek için eğilmeli ve geri çekilmeli. 3. Çalışma parçasının büyük şeklini ve küçük sıçrama bölgesinin içine büyük parçaları sıçrayken, kesme aracı ve sıçrama bölgesinin tesadüf olması zor, işçilik parçasını veya işçilik parçasının hasarını yerleştirmesi için zor oldu. Yukarıdaki durumdan kaçınmak için makinelerin uzunluğu yönünde bir pozisyon noktası eklenebilir, böylece makinelerin iki yönden yerleştirilmesi, makinelerin pozisyonu uygun ve makinelerin güvenliğini geliştirmesi, işlem parçalarının hasarından kaçınması ve üretim etkinliğini arttırması. 2. N-fold şekilde bağlı farklı işleme metodları gerekiyor. Kökerken, materyalin iç boyutları 4MM'den daha büyük olmalı ve X boyutunun ölçüsü molun şeklinde sınırlı. Eğer materyalin içindeki ölçü 4MM'den az olsa, işleme için özel metodlar kullanılmalı. 1 Material kalınlığı, boyutlu, materyal ve dikme açısına dayalı mol seçin. 2. Güvenlik prensipi 1) Çalışma parçasının aracıya karışmasını sağlayın 2) Yerleştirme açının 90 dereceden az olduğundan emin olun. 3) Özel koşullardan başka iki arka pozisyon kuralı kullanmak daha iyi. 3 , Özellikler 1) L'yi sıkıştırdıktan sonra, makinelerin ve pozisyonlarının kolaylaştırması için 90 dereceden az ya da az tutulmalı. 2) İkinci katlanma sürecinde, makinelerin yüzeyi merkez olarak ayarlamak gerekir. 3. Z-bend, ayrıca bölüm farklısı olarak bilinen, bir pozitif ve bir negatif bölümünün çevirmesini anlatır. Köşe göre kıyım bölümünün farklığını ve doğru kenar bölümünün farklığını bölün. İşlenme için en az boyutlu işleme örgütü tarafından sınırlı, işleme makinesinin şeklinde maksimum işleme boyutunu belirliyor. Genelde, Z katlanmış materyalin iç boyutu 3,5T'den az olduğunda, bölümlü ölüm işleme kullanılır. 3,5T'den büyük olduğunda normal işleme metodları kullanılır. 1 Güvenlik prensipi 1) İyileştirici pozisyon ve iyi stabilit. 2) Genelde pozisyon L katı ile aynı. 3) İkinci pozisyon işletilen çalışma parçasının aşağıdaki çöplüklerle patlamasını gerekiyor. 2. , Özellikler 1) L katının işleme açısı yerinde olmalı, genellikle 89,5-90 derece arasında olmalı. 2) Daha sonra belirtilenlere göre geri çekildiğinde işin deformasyonuna dikkat verilmesi gerekir. 3) İşlemin sırası doğru olmalı. 4) Özel işleme için, bu metodlar kullanılabilir: Orta çizgi ayrılma yöntemi (eccentric makineler) Küçük V işleme (dikme koefitörü arttırması gerekiyor) Yavaşlanmak kolay Aşağıdaki kaldırım 4. Döndürme ve düzeltme, aynı zamanda sınır sıkıştırma olarak bilinir. Ölü kenarlar için işleme adımları: 1. Önce yaklaşık 35 derece derinliğine girin. 2. Sonra düzlük ve sıkı bağlanana kadar düzlük ve biçimlenmiş. 1 Model Seçimi Metodi Aşa ğıdaki boğazın V-groove genişliğini 5-6 kat katına göre 30 derece derinlikle seçin ve ölü kenarları işlemenin özel durumlarına göre yukarıdaki boğazı seçin. 2. , Özellikler Ölü kenarın her iki tarafındaki parallelizme dikkat edilmeli. Ölü kenarın işleme boyutları relativ uzun olduğunda, düzlük kenarı ilk olarak yükselmiş bir a çıya katlanabilir ve sonra düzlüklendirilir. Kısa ölü kenarlar için, bölüm işleme kullanılabilir. 5. Yazılımları bastırmak için donanım komponentlerini bastırmak ve mühürlemek için bir yatak kullanır. Genelde işlemek için bir şekilde yardımcı mold kullanır. Genelde, sıkıştırma fıstıkları, sıkıştırma fıstıkları, sıkıştırma fıstıkları ve diğer donanım komponentleri var. İzleme önlemleri: 1. Makineler sırasında çalışma parçasının şeklinin kaçınması gerektiğinde, kaçınma ölçüleri alınmalıdır. 2. İşlemden sonra, sıcaklık ve sıkıştırma standartlarına uygun olup olmadığını ve donanım ve çalışma parçası sıkı olarak bağlı olup olmadığını kontrol etmek gerekir. 3. Makine aracının yanına basınca, dikkat et ve bastıktan sonra, makinelerin kaçınılmasına ve parallelizmine dikkat et. 4. Eğer büyülüyorsa, çöplük kenarında çatlak olmaması da önemli. Çalışma parçasının yüzeyinin üstünde yükselmesi de önemli. 6. Kolay kaplanın işleme içerikleri genellikle: küçük farklılıklar, kaplanlar, köprüler, çantalar, basınç kaynakları ve bazı sıradan şekiller içeriyor. Easy Mold'un tasarım prensipi "Laser Cutting Easy Mold Design Principle" diyor. Soğulmak kolay genelde post pozisyonu ya da kendi pozisyonu kullanır. Yukarıdaki içerikleri kolay bir şekilde işlemek için en önemli şey, fonksiyonu ve toplantı ihtiyaçlarını etkilenmiyor ve görünüşü normal. 2,Yatak işlemlerinde sık sorunlar ve çözümler: 1. İşlemde sıçrama sebeplerinin analizi: 1. Kıpırdama çubuğunu seçtiğinde, genelde T'nin V-groove genişliği seçildir. Seçilen V-groove genişliğinin yarısından az olduğunda bir parçalanma parçası oluşacak. 2. Seçilen V-slot çok büyük 3. İşlemi Çözüm yöntemi 1. Orta çizgi ayrılma yöntemi (eccentric machining). Eğer sıkıştırılmış maddelerin iç boyutları (4-6) T/2'den daha az olursa, mümkün olduğunca farkı yapalım. 2. Pad işleme. 3. Küçük bir V-groove ile dolu ve büyük bir V-groove ile basınç uygulayın. 4. Küçük bir V slot seçin. 2. İçindeki kilitleme genişliğinin standart genişliğinden daha az olduğu sebeplerin analizi: Yatağın küçük standart genişliğinin 10MM olması yüzünden, sıkıştırma işleme parçası 10 MM'den az genişliğinde. Eğer 90 derece eğilirse, uzunluğu boyutu 2'den az olmayacak (L+V/2)+T. Bu çeşit düşürme için, süzgün koltuğun üzerinde (yukarı yönünde sınırlı özgürlük dışında) ayarlanması gerekiyor. Çalışma parçasının yıkılmasını veya güvenlik kazalarına neden olabilir. Çözüm: 1 Ölçünü arttır (müşterilerle koordinat edilecek), yani iç katının genişliğini arttır. 2. İşlenme kolay 3 Sistem araçları (işleme maliyetlerini arttırır) 3. Döşek dikme hattına çok yakın ve dikme deliğin materyali çekmesine sebep olur. L < olduğunda, delik ve sıçrama çizgi arasındaki mesafe L olduğunu tahmin ediyorsunuz; T/2'de delik materyali çekecek. Özellikle sıkıştırma sürecinde genişleme gücü yüzünden, materyal deformasyonu yapıyor, çekmek ve dönüştüğü fenomene neden oluyor. Mevcut standart mold groove genişliğine göre, farklı plate kalıntıları için en az L değeri aşağıdaki tabelde gösterilir: Çözüm: 1 Büyüklüğü arttır ve oluşturduğundan sonra sıkıştırılmış kenarları sıkıştırır. 2. Döşeni küçük hatta genişletin (görünüşe ya da fonksiyona etkisi olmamalı ve müşteri kabul ediyor). 3 Çizgi işleme veya basınç çizgi işleme kesin 4 Mold eccentric processing 5 Delik boyutunu değiştir 4. Çıkarma noktasındaki deformasyon sebeplerinin analizi L çıkarma kenarı ve eğme hattı arasındaki küçük uzaktan dolayı eğildikten sonra: L < ; Çizim ve aşağı çörek arasındaki bağlantısı yüzünden (4-6) T/2'de çizimde çalışan güç yüzünden çevirme sürecinde deformasyon oluyor. Çözüm: 1 Kes ya da basın. 2. Çizim boyutunu değiştir. 3 İşlenmek için özel mollar kullanılıyor 4 Mold eccentric processing 5. Uzun ölü kenarı patlattıktan sonra savaştırma sebeplerinin analizi: Uzun ölü kenarı yüzünden, yumruklandığında sıkı bir şekilde tutamaz. Sonuçta yumruklandıktan sonra yuvarlanıyor. Bu durum yerleştirilmiş pozisyonla yakın bir bağlantıdır, bu yüzden düzlük yaparken dikkat çekilmeli. Çözüm: 1 Ölü kenarı çarpmadan önce, ilk köşeyi çarpın (diagramda gösterildiği gibi), sonra da düzeltin. 2. Birden fazla adımlarda dağıt: Ölü kenarı indirmek için önce sonu basın. Kökeleri parçalayın. Dikkati: İşletimin etkisi operatörün operatörün operatör yetenekleriyle bağlı. Lütfen düzeltme s ırasında gerçek duruma dikkat edin. 6. Yüksek Yüksek Köprü çekmesinin kolay kırıklığı sebeplerinin analizi: 1 Köprüsün yüksek yüksekliğinden dolayı, materyal çok uzatılmıştı ve kırıklığın sonucuna ulaştı. 2. Köşelerin köşeleri doldurulmuyor ya da yeterince polis edilmiyor. 3 Materialin zorluğu çok fakir ya da köprü cesedi çok kısa. Çözüm: 1 Süreç deliğini kırıklığın tarafından uzatın. 2. Köprünün genişliğini arttır. 3 Kıçının R açısını sıkıştırın ve çağın geçişini arttırın. 4 Sıçrama köprüsüne lübrik yağı ekle. Bu yöntem çalışma parçasının yüzeyini kirleyecek, bu yüzden AL parçaları için kullanılamaz. 7. Kolay bir şekilde işleme sırasında makinelerin boyutlarının çalışmasının sebeplerinin analizi: Makineler sürecinde çalışma parçasında yapılan ileri sıkıştırma gücü yüzünden çalışma parçası önünde ilerliyor ve önünde küçük rake açısı L arttırıyor. Çözüm: 1 Resimdeki gölgeden bölgeleri çıkar. Genelde fark mümkün olduğunca oluşturuyor. 2. Bütün kendi yerleştirme parçalarını kapatın ve düzeltme yerine geçin. (Aşağıdaki şekilde gösterildiği gibi) 8. Matematiklerin genel boyutu (açılırken) çok küçük veya çok büyük, devre yüzeyine uymuyor. Çünkü analiz: 1 Proje yanlış başlatıldı. 2. Keme boyutu yanlış. Çözüm: Her bölüm için, ayrılığın yönündeki toplam ayrılığın ve sıçrama kılıçların sayısına dayanılan ayrılığı hesaplayın. Eğer hesaplanmış bölüm toleransiyonu toleransiyonun içindeyse, çalışma parçası kabul edilebilir. Eğer büyüklüğü fazla büyüklüyse, işleme için küçük bir V-groove kullanılabilir. Eğer büyüklüğü çok küçük olursa, işleme için büyük bir V-groove kullanılabilir. 9. Döşeme vurduğundan sonra genişleme ya da serbest uygulama sebeplerinin analizi: 1 Döşeğin parçası çok küçük olduğu R açısına neden oluyor ya da flançadaki patlamalar çok büyük. 2. Büyük uyuşturma deliğin yetersiz genişlemesinin sebebi. 3 Bu deformasyon delik kötülüğü veya yanlış yerleştirme yöntemi tarafından sebep olabilir. Çözüm: 1 Onun yerine büyük bir R-a çıyla yumruk seç. Dikkat: deliğin çizimi ve yandırma sırasında deliğin etrafında sıkıştırıyor. 2. Basıncı arttırın, salata deliğini genişletin ve bunun yerine büyük bir R-a çıyla yumruk kullanın. 3 Çölme yöntemini ve delik kötülüğünü değiştirme sebeplerini boşaltma yöntemi. 10. Çalışma parçası bastıktan sonra şaşırtma veya deformasyonun sebeplerinin analizi: 1 Ürünün işleme sırasında, kırık düz çalışma parçaları yoktu. 2. Çalışma parçasının aşağıdaki yüzeyinde bile güç veya fazla baskı yok. Çözüm: 1 Çalışmayı bastığında çalışma parçası yükselmeli. 2. Destek çerçevesi yap. 3 Basıncıyı tekrar ayarlayın. 4 Aşağıdaki yüzeyde güç menzilini arttır ve üst yüzeyde uygulanan güç menzilini azaltır. 11. Bölüm farkından sonra iki tarafın arasındaki parallelizm olmayan sebeplerinin analizi: 1 Kalibre kalibrelenmedi. 2. Yukarı ve aşağı gövdeler doğru ayarlanmıyor. 3 Yüksek ve aşağı toprakların seçimi farklıdır. Çözüm: 1 Kalibreyi yeniden kalibre edin. 2. Pislikleri ekle ya da kaldır. (Özellikle ayarlama metodları için lütfen "Bölüm İşlemi Teknolojisine referans edin") 3 Kıçı eksantrik. 4 Yüzünü değiştirin, yukarı ve aşağı toprakların yüzleri aynı şekilde. 12. Ürünün yüzeyinde derin kırıklığın sebeplerinin analizi: 1 Aşağıdaki toprakların V-grubu küçük. 2. Aşağıdaki V-groove açısı küçük. 3 Material çok yumuşak. Çözüm: 1 Büyük V-groove işleme kullanılıyor 2. İşlenmek için büyük bir R-a çıyla bir kadeh kullanılıyor 3 , balık materyal yıkımı (balık çelik çarşafı ya da Yuli yapıştırımı) 13. Kıçrama noktasının yakınlarında deformasyon sebeplerinin analizi: Makine sıkıştırma sürecinde hızlı çalışır, ve deformasyon sırasında çalışma parçasının yukarı sıkıştırma hızı, operatörün elleriyle çalışma parçasının hareketini destekleyen hızdan daha büyük. Çözüm: 1 Makinenin operasyon hızını azaltın 2. Operatörün elin desteğinin hızını arttır. 14. AAL parçalarında kırılma sebeplerinin analizi: AL materyalinin eşsiz kristal yapısı yüzünden, tahıl yöntemiyle paralel düştüğünde kırıklığına yakın olur. Çözüm: 1 Keçirken, AL maddelerini dikme yönüne perpendikli döndürmeyi düşünün (maddelerin dikme yönünü tahminlere perpendikli olsa bile). 2. Üst katının R açısını arttır.