Як визначити параметри процесу порізання лазером у Шеніангу?
Працюючий принцип резьміну лазером
Лазерне обробка вирізання замінює традиційні механічні ножі невидимими промінами, і має характеристики високої точності, швидкого вирізання, не обмежені на шаблони вирізання, автоматичне вирізання для збереження матеріалів, гладкого вирізання і низьких витрат обробки. Воно The mechanical part of the laser blade has no contact with the workpiece and will not cause scratches on the surface of the workpiece during operation; Швидкість різки лазера швидка, різка гладка і плоска, і зазвичай не потребує більшого обробки; Зона, на яку впливає на тепло, мала, деформування дошки мала, а вирізання (0,1 мм~0,3 мм); У розрізку немає механічного стресу і немає вибухів. Висока точність обробки, добра повторливість і жодної шкоди на поверхні матеріалу; Числове програмування керування, здатне обробляти будь-який плоский план, може розрізати великі цілі дошки без потреби форм, збереження часу і економіки.
Зміст лазерового вирізку
Лазеровий уряд складається основно з лазера, світлової системи керування, системи руху СНК, автоматичного уряду висоти голови, робочої платформи і високотискової газової дихальної системи. Багато параметрів може впливати на процес вирізання лазера, деякі з них залежать від технічної здатності лазера та машинного інструменту, а інші змінні. Головними параметрами лізерового вирізку є:
Головні параметри вирізання лазера
Режим 1 проміну
Фундаментальний режим, також відомий як режим Гаусії, є ідеальним режимом для вирізання, у основному з'являється у лазерах з низькою потужністю меншою за 1 кВ. Мультирежим — це змішаний режим вищого порядку, з поганим фокусом і низькою здатністю вирізати з однаковою потужністю. Лазери в одному режимі мають кращу здатність вирізати і якість, ніж багаторядкові лазери.
2 лазерні сили
Лазерова енергія, яка потрібна для порізання лазером, залежить основно від матеріалу порізання, товщини матеріалу і вимог швидкості порізання. Лазерова енергія має значний вплив на товщину вирізання, швидкість вирізання і ширину вирізання. Загалом, коли сила лазера збільшується, товщина матеріалу, який можна вирізати, також збільшується, швидкість вирізання прискорюється, а ширина вирізання також збільшується.
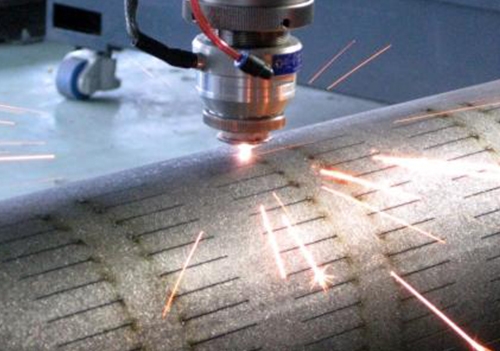
3 позиції фокусу
Фокальна позиція має значний вплив на ширину різка. Загалом, фокус буде розташовано близько третини товщини під матеріальною поверхнею, з більшою глибиною різка і меншою шириною рота.
4 фокальні моменти
Під час порізання товщіших сталевих плиток слід використовувати промінь з довшою фокальною довжиною, щоб отримати поверхню порізання з доброю вертикальністю. Глибина фокусу збільшується, діаметр точки світла також збільшується, а щільність потужності відповідно зменшується, що призводить до зменшення швидкості вирізання. Щоб зберегти певну швидкість вирізання, необхідно збільшити силу лазера. Рекомендується використовувати промінь з меншою фокусною довжиною для різки тонких плиток, що призведе до меншого діаметра точки, більшої щільності потужності і швидшої швидкості різки.
5 Додаткових гасів
Вирізання низької кількості вуглецевої сталі часто використовує кисню, як газ для вирізання, щоб підтримувати процес вирізання, використовуючи тепло железної реакції на спалення кисню. Крім того, швидкість вирізання швидка, якість вирізання добра, і можна отримати Тиск збільшується, кінетична енергія збільшується, а потужність випуску щури збільшується; Тиск різки визначається на основі факторів, таких як матеріал, товщина плитки, швидкість різки і якість поверхні різки.
Структура шматочка
Структура та форма тузли, також розмір виходу світла, також впливають на якість і ефективність вирізання лазера. Розні вимоги вирізання вимагають використання різних тузлів. Зазвичай використовуються форми дужки: циліндричні, конічні, квадратні та інші форми. Лазеровий виріз зазвичай використовує коксіальний (концентральний потік повітря з оптичною осею) спосіб дихання. Якщо потік повітря не вирівнюється з оптичною осею, під час вирізання легко створюється велика кількість розбиття. Щоб забезпечити стабільність процесу вирізання, зазвичай, необхідно керувати відстаниною між кінцевою обличчю дужки та поверхнею робочої частини, яка зазвичай дорівнює 0,5-2,0 мм, щоб полегшити гладкий виріз.
Вміст статті отримується з інтернету. Якщо у вас є питання, будь ласка, зв’ яжіться зі мною, щоб вилучити її!