Gia công kim loại tấm Gia công kim loại tấm là một quá trình gia công lạnh toàn diện cho tấm kim loại mỏng (thường dưới 6mm), bao gồm cắt, dập, uốn, hàn, tán đinh, tạo khuôn và xử lý bề mặt, v.v. Đặc điểm nổi bật của nó là độ dày của cùng một bộ phận phù hợp.
Phương pháp gia công kim loại tấm: Gia công không khuôn: Phương pháp công nghệ được thực hiện trên kim loại tấm bằng cách vẽ số, cắt laser, máy cắt tấm, máy uốn, máy đinh tán và các thiết bị khác, thường được sử dụng để làm mẫu hoặc sản xuất hàng loạt nhỏ, chi phí cao hơn. Chu kỳ xử lý ngắn và phản ứng nhanh. Gia công khuôn: Thông qua khuôn cố định, gia công kim loại tấm, thường có khuôn xả, khuôn đúc, chủ yếu được sử dụng trong sản xuất số lượng lớn, chi phí thấp hơn. Chi phí khuôn trước cao và chất lượng các bộ phận được đảm bảo. Chu kỳ xử lý giai đoạn đầu dài và chi phí khuôn cao. Quy trình gia công kim loại tấm: xả: đấm kỹ thuật số, cắt laser, máy cắt tấm
Hình thành - uốn, kéo dài, đấm: máy uốn, máy đục lỗ, vv
Chế biến khác: báo chí và tán đinh, tấn công răng, vv
Hàn: cách kết nối kim loại tấm
Xử lý bề mặt: Phun bột, mạ điện, vẽ dây, in lụa, v.v.
Quá trình gia công kim loại tấm - cách làm trống kim loại tấm chủ yếu là một số bản vẽ, cắt laser, máy cắt tấm, làm trống khuôn, v.v., CNC là phương pháp phổ biến hiện nay, cắt laser chủ yếu được sử dụng trong giai đoạn kiểm chứng (cũng có thể xử lý các bộ phận kim loại tấm thép không gỉ), chi phí gia công cao, làm trống khuôn chủ yếu được sử dụng trong chế biến số lượng lớn.
Sau đây chúng tôi chủ yếu giới thiệu về nguyên liệu của tấm kim loại.
Máy đục lỗ số, còn được gọi là máy đục lỗ CNC tháp pháo, có thể được sử dụng để làm trống, đục lỗ, lỗ kéo, gân lăn, đục lỗ và vân vân. Độ chính xác xử lý của nó có thể đạt+/- 0,1mm.
Độ dày của tấm có thể gia công CNC là:
Tấm cán nguội, tấm cán nóng 4.0mm
Tấm nhôm 5.0mm
Tấm thép không gỉ 2.0mm
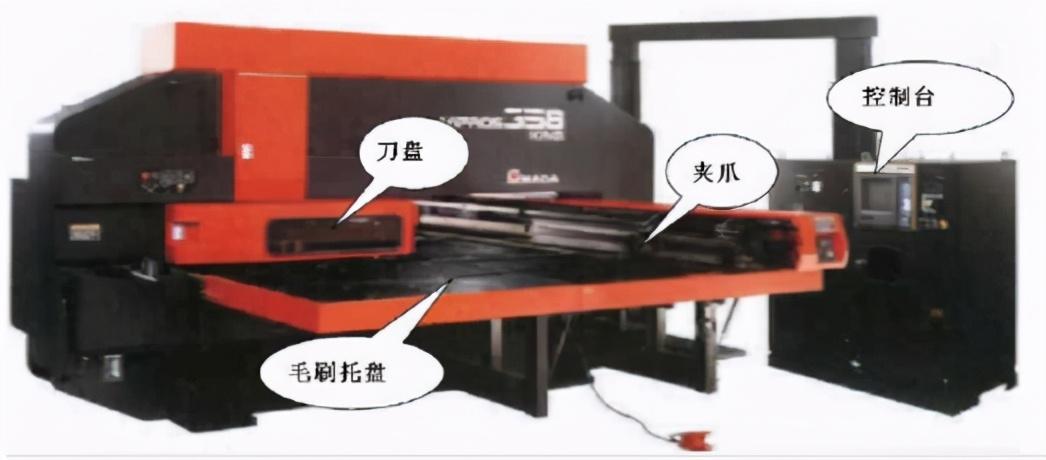
Punch có yêu cầu kích thước tối thiểu. Kích thước tối thiểu của lỗ đục lỗ có liên quan đến hình dạng của lỗ, tính chất cơ học của vật liệu và độ dày của vật liệu. (như sau) 000 @ 000
2. Khoảng cách giữa lỗ và cạnh lỗ. Khoảng cách tối thiểu của cạnh đục lỗ của bộ phận so với hình dạng không song song với cạnh hình dạng của bộ phận, khoảng cách tối thiểu này phải không nhỏ hơn độ dày vật liệu t; Khi song song, nó phải không nhỏ hơn 1,5 t. (như sau)
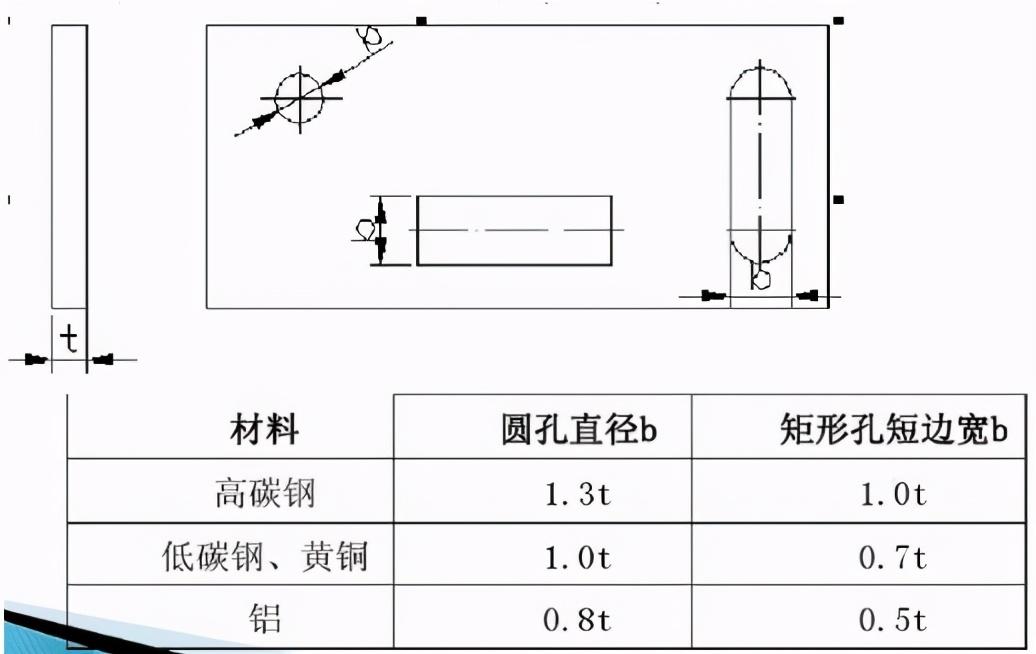
3. Khi mở rộng lỗ, khoảng cách tối thiểu từ cạnh của lỗ kéo dài là 3T, khoảng cách tối thiểu giữa hai lỗ kéo dài là 6T, khoảng cách an toàn tối thiểu từ cạnh uốn (bên trong) của lỗ kéo dài là 3T+R (T là độ dày kim loại tấm, R là góc tròn uốn)
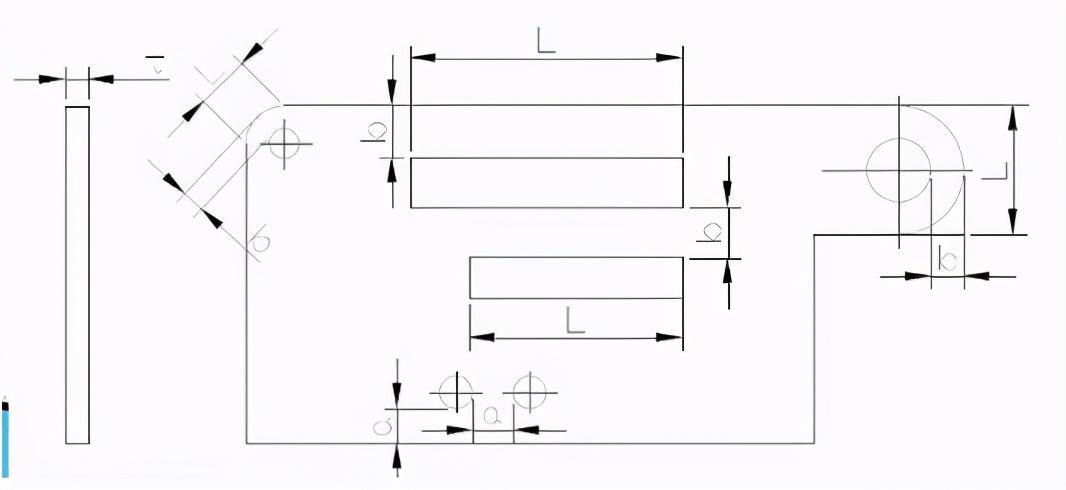
4. Khi uốn và vẽ sâu đục lỗ, nên duy trì một khoảng cách nhất định giữa tường lỗ và tường thẳng. (như sau)
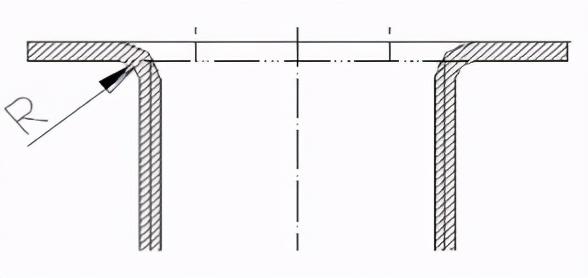
Quá trình gia công kim loại tấm - hình thành kim loại tấm chủ yếu là uốn, kéo dài kim loại tấm.
1. uốn kim loại tấm 1.1 uốn kim loại tấm chủ yếu sử dụng máy uốn.
Gia công chính xác của giường gấp;
Gấp đôi:+/- 0,1mm
Gấp đôi:+/- 0,2mm
Trên gấp đôi:+/- 0,3mm
1.2 Nguyên tắc cơ bản của trình tự xử lý uốn: uốn từ trong ra ngoài, uốn từ nhỏ đến lớn, uốn hình dạng đặc biệt trước, sau khi hình thành quy trình trước không ảnh hưởng hoặc can thiệp vào quy trình tiếp theo.
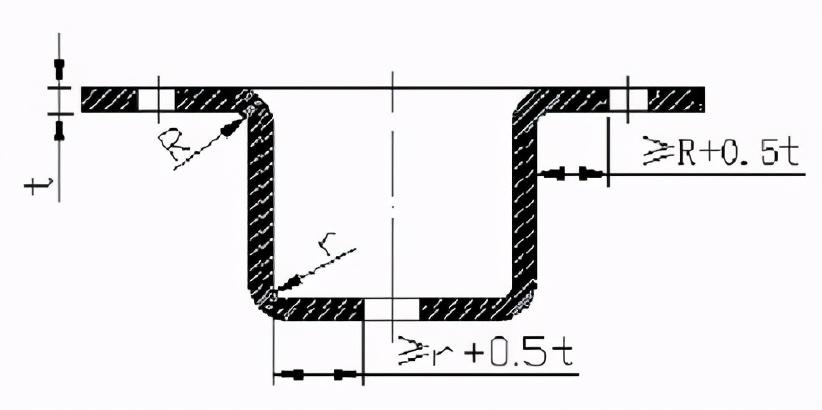
1.3 Hình dạng phổ biến gấp cong:
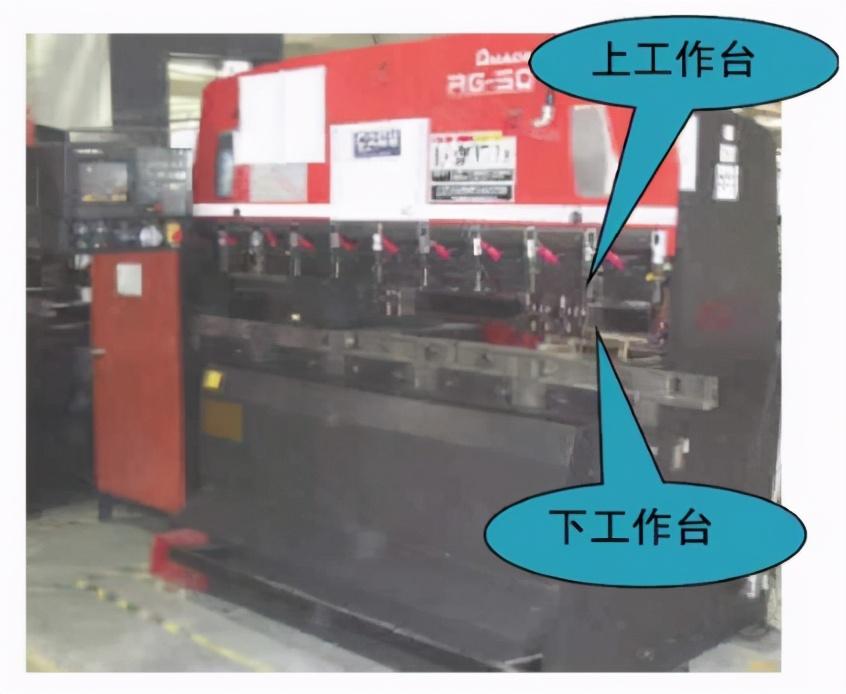
Hình dạng khe chữ V phổ biến:
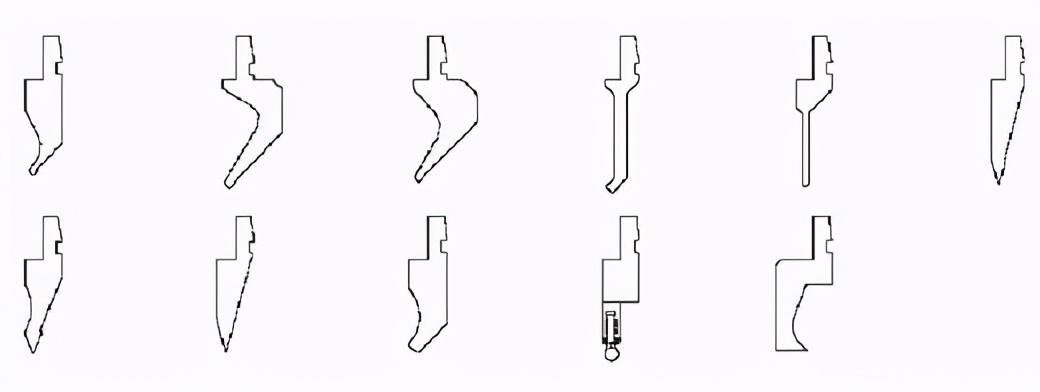
1.4 Bán kính uốn tối thiểu của phần uốn:
Khi vật liệu uốn cong, trên vùng góc tròn, lớp ngoài bị kéo căng, lớp trong bị nén. Khi vật liệu có độ dày nhất định, r bên trong càng nhỏ, độ căng và nén của vật liệu càng nghiêm trọng; Khi ứng suất kéo của các góc tròn bên ngoài vượt quá sức mạnh giới hạn của vật liệu, các vết nứt và gãy sẽ được tạo ra, do đó, thiết kế cấu trúc của các bộ phận uốn cong, nên tránh bán kính góc cong quá nhỏ. Bán kính uốn tối thiểu của vật liệu thường được sử dụng trong công ty được liệt kê trong bảng dưới đây.
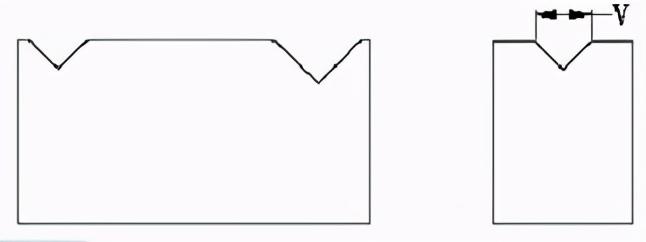
Bảng bán kính uốn tối thiểu cho các bộ phận uốn:
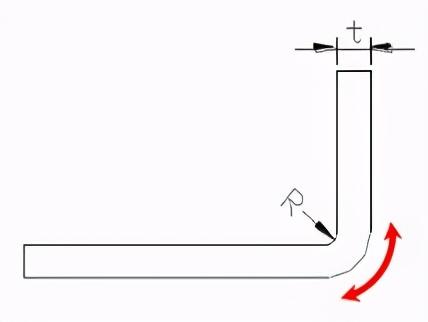
Bán kính uốn đề cập đến bán kính bên trong của phần uốn và t là độ dày thành của vật liệu.
1.5 Chiều cao cạnh thẳng của phần uốn:
Nói chung, chiều cao cạnh thẳng tối thiểu không nên quá nhỏ, yêu cầu chiều cao tối thiểu: h ~ 2t
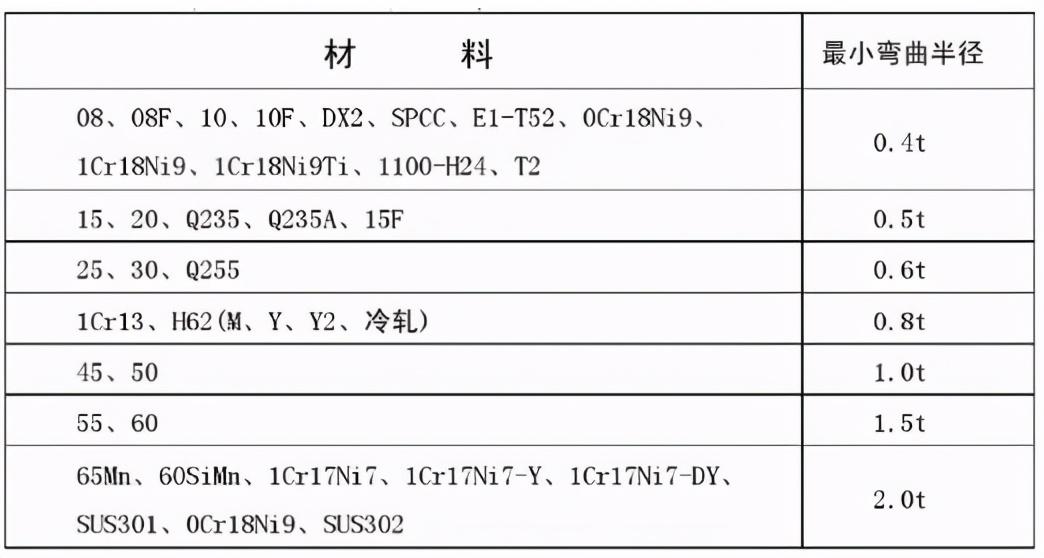
Nếu bạn cần chiều cao cạnh thẳng của phần uốn h2t, trước tiên bạn phải tăng chiều cao cạnh uốn, sau khi uốn xong sẽ xử lý đến kích thước cần thiết; Hoặc sau khi xử lý rãnh nông trong vùng biến dạng uốn, uốn.
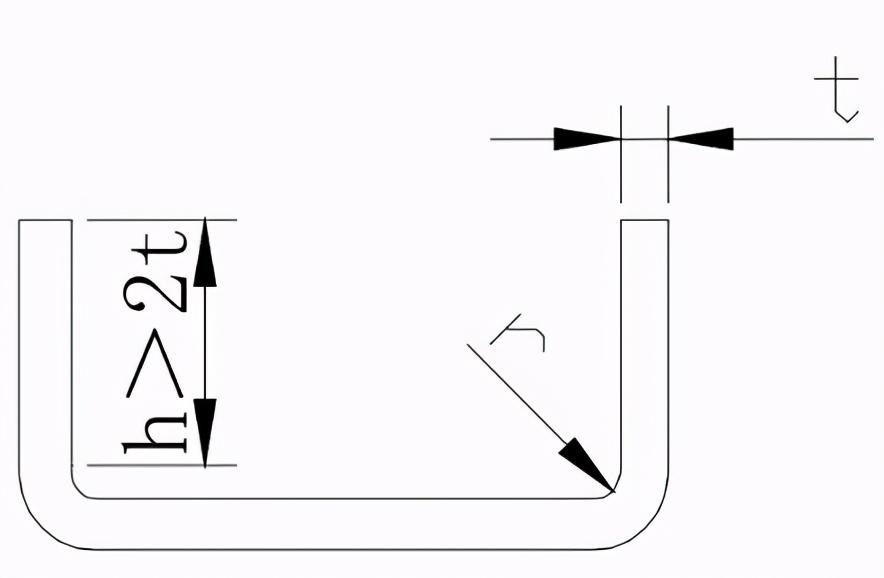
1.6 Chiều cao cạnh thẳng uốn tối thiểu với góc vát bên cạnh cạnh cong:
Khi phần uốn có góc xiên ở bên cạnh cạnh uốn, chiều cao tối thiểu của mặt là: h=(2~4) t> 3mm
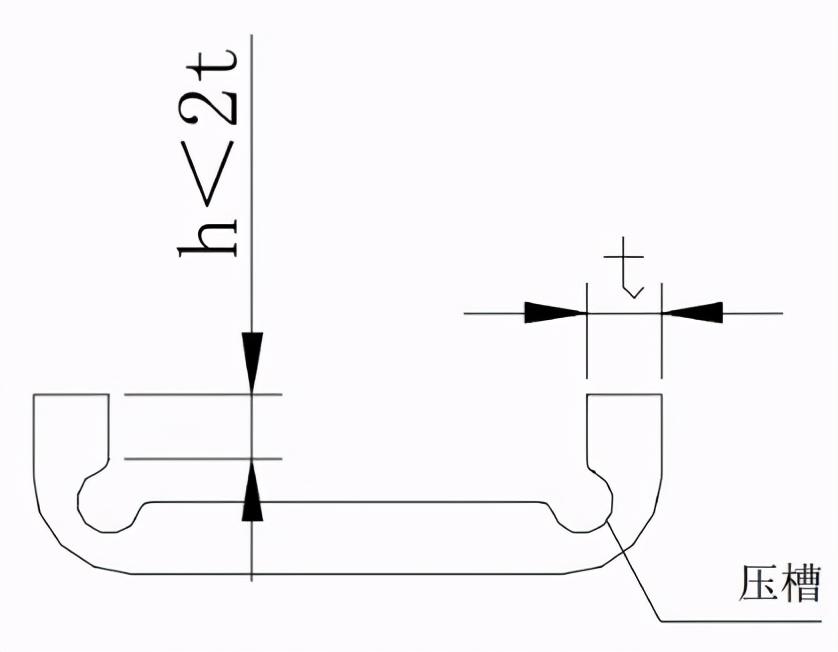
1.7 Cạnh lỗ trên uốn:
Lề lỗ: đấm trước và uốn sau, vị trí của lỗ phải ở bên ngoài khu vực biến dạng uốn, để tránh biến dạng khi uốn. Xem bảng dưới đây về khoảng cách từ thành lỗ đến cạnh cong.
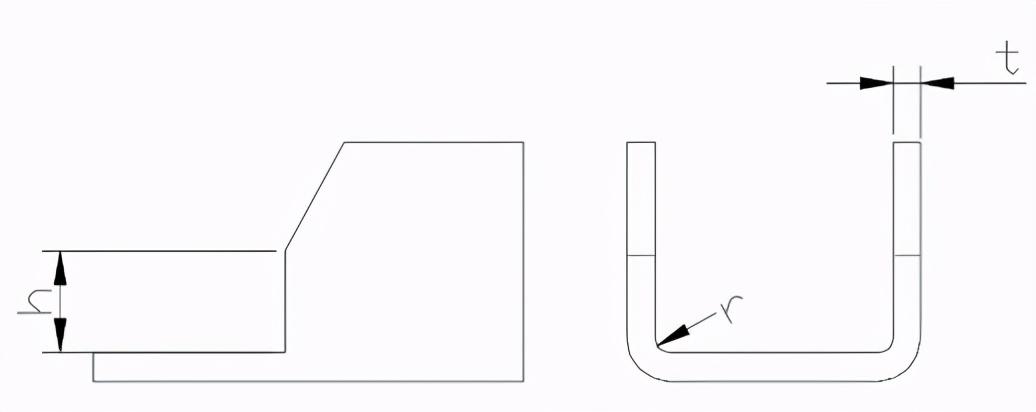
1.8 Quá trình cắt cho uốn cục bộ:
Các đường cong của phần uốn nên tránh vị trí đột biến kích thước. Khi uốn cong cục bộ một phần của cạnh, để ngăn chặn sự tập trung của các ứng suất ra khỏi góc nhọn tạo ra các vết nứt cong, các đường cong có thể được di chuyển một khoảng cách nhất định để thoát khỏi đột biến kích thước (Hình A), hoặc để mở một khe quá trình (Hình B), hoặc để đấm lỗ quá trình (Hình C). Lưu ý các yêu cầu về kích thước trong hình: SR; Khe rộng KT; Độ sâu khe Lt+R+k/2.
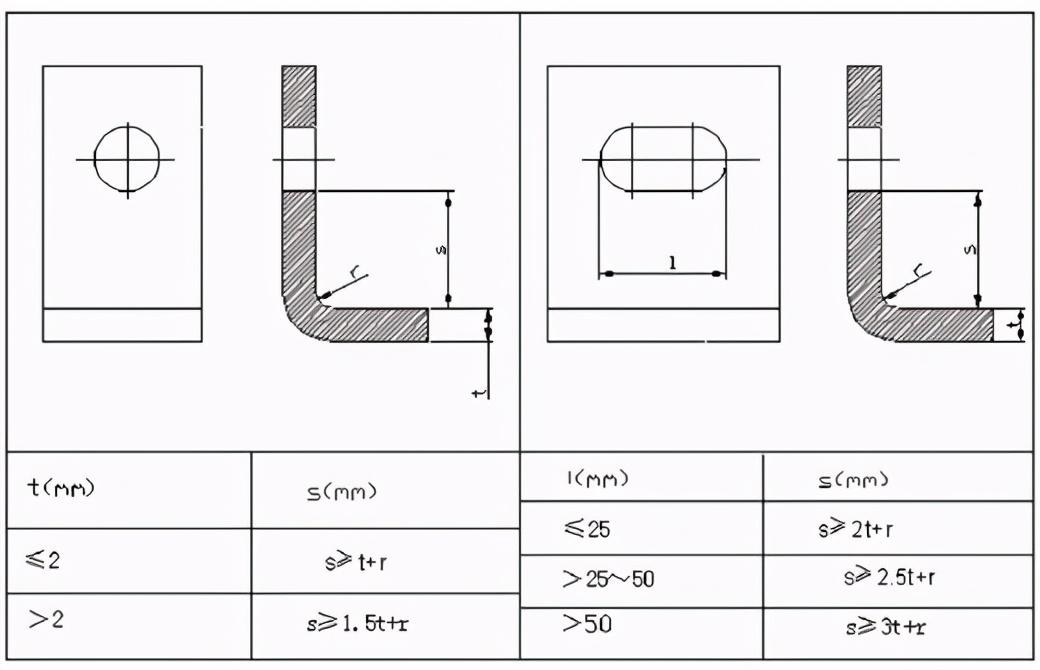
1,9 Cạnh cong có cạnh vát nên tránh vùng biến dạng:
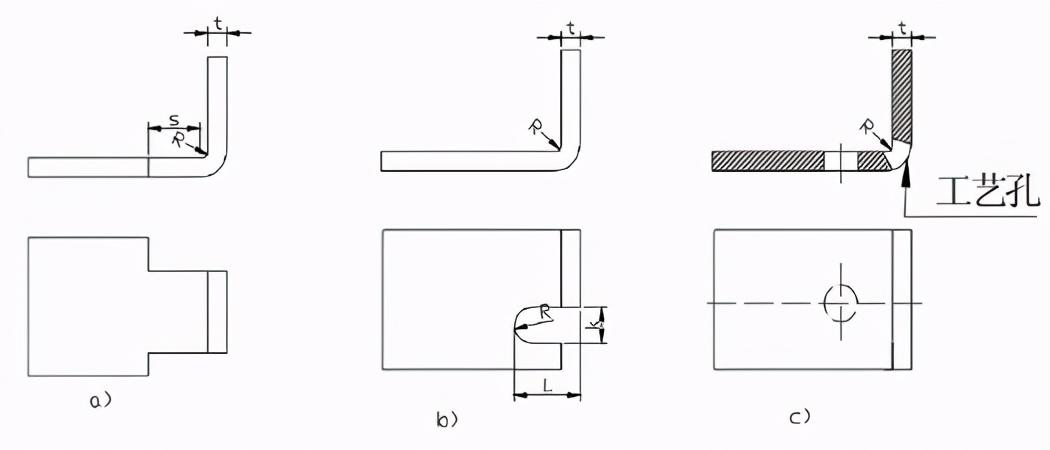
1. Yêu cầu thiết kế cho 10 tấm kim loại xếp li (cạnh chết):
Chiều dài cạnh chết của viền kim loại tấm có liên quan đến độ dày của vật liệu. Như hình dưới đây cho thấy, chiều dài tối thiểu chung của cạnh chết L3.5t+R.
Trong đó t là độ dày của thành vật liệu và R là bán kính uốn bên trong tối thiểu của quy trình trước khi đánh chết cạnh (như thể hiện bên phải trong hình bên dưới).
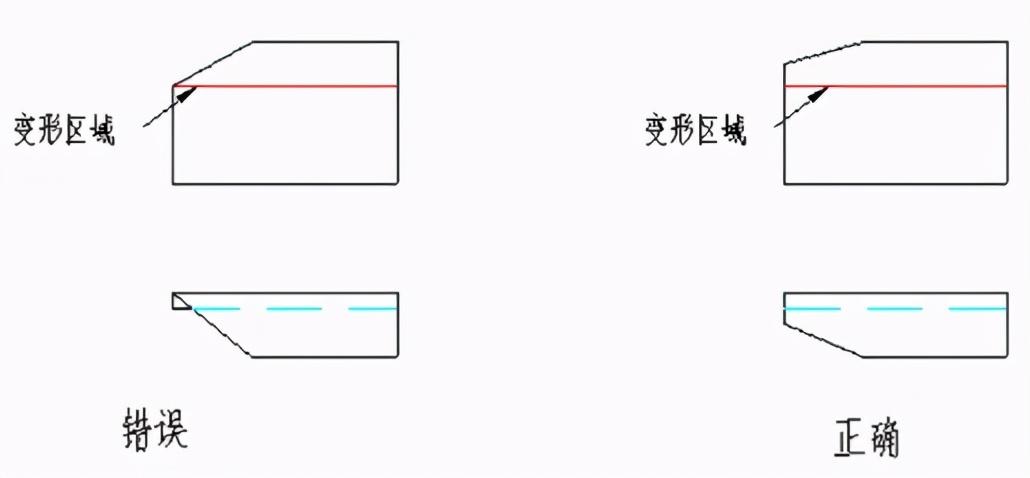
1.11 Thêm lỗ định vị quá trình:
Để đảm bảo rằng khoảng trống được định vị chính xác trong khuôn và ngăn chặn sự dịch chuyển của khoảng trống khi uốn để tạo ra phế liệu, lỗ định vị quá trình nên được thêm vào trước khi thiết kế, như được hiển thị trong hình dưới đây. Đặc biệt là các bộ phận uốn cong nhiều lần, tất cả đều phải sử dụng lỗ quá trình làm chuẩn định vị để giảm lỗi tích lũy và đảm bảo chất lượng sản phẩm.

1. Khi kích thước liên quan đến các bộ phận uốn kích thước, hãy xem xét tính công nghệ:
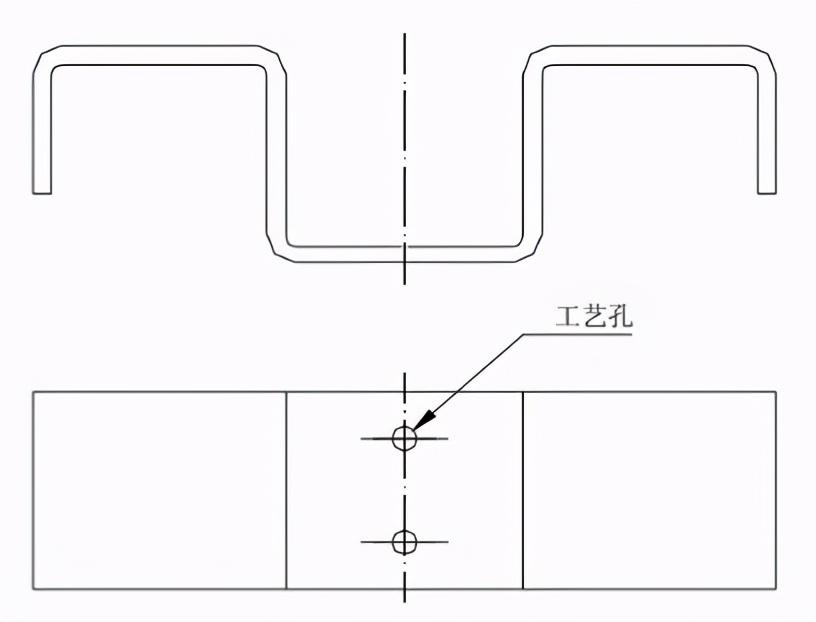
Như bạn có thể thấy trong hình trên, a) đấm trước và uốn sau, độ chính xác kích thước L dễ dàng đảm bảo và xử lý thuận tiện. b) và c) Nếu kích thước L yêu cầu độ chính xác cao, cần phải uốn trước khi xử lý lỗ, xử lý rắc rối.
1.13 Sự phục hồi của bộ phận uốn ảnh hưởng đến sự phục hồi của nhiều yếu tố, bao gồm: tính chất cơ học của vật liệu, độ dày của tường, bán kính uốn và áp suất dương khi uốn, v.v. Bán kính góc tròn bên trong của phần gấu với độ dày của bảng càng lớn, trả lại càng lớn. Ví dụ về phương pháp thiết kế để ức chế sự phục hồi của các bộ phận uốn cong, hiện nay chủ yếu là do các nhà sản xuất thực hiện các biện pháp nhất định để tránh khi thiết kế khuôn. Đồng thời, việc cải tiến một số cấu trúc từ thiết kế đã thúc đẩy góc hồi phục trở nên đơn giản hơn như hình dưới đây cho thấy: trong khu vực uốn cong để ép và tăng cường gân, không chỉ có thể cải thiện độ cứng của phôi, mà còn có lợi cho việc ức chế hồi phục.
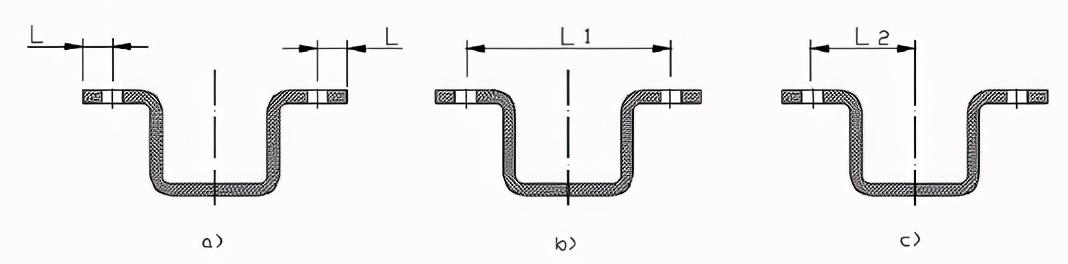
2. Việc kéo dài kim loại tấm chủ yếu được thực hiện bằng CNC hoặc PU Punch, đòi hỏi một loạt các cú đấm kéo hoặc chết.
Hình dạng của phần kéo dài nên càng đơn giản và đối xứng càng tốt, kéo dài hình thành càng nhiều càng tốt.
Các bộ phận cần kéo dài nhiều lần nên cho phép các dấu vết mà bề mặt có thể tạo ra trong quá trình kéo dài.
Dưới tiền đề đảm bảo yêu cầu lắp ráp, nên cho phép kéo dài vách bên có độ nghiêng nhất định.
2.1 Yêu cầu về kích thước bán kính góc tròn giữa đáy của phần kéo và tường thẳng:
Như hình dưới đây cho thấy, bán kính góc tròn giữa đáy của phần kéo dài và bức tường thẳng phải lớn hơn độ dày của tấm, tức là r1t. Để làm cho việc kéo căng diễn ra suôn sẻ hơn, thường lấy r1=(3~5) t, bán kính góc tròn tối đa phải nhỏ hơn hoặc bằng 8 lần độ dày của tấm, tức là r18t.
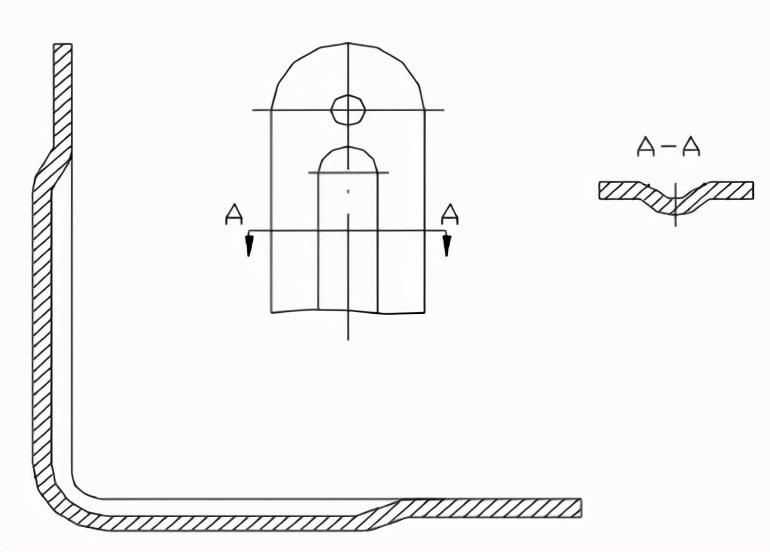
2.2 Bán kính góc tròn giữa cạnh lồi và tường của phần kéo dài
Bán kính góc tròn giữa cạnh lồi và tường của phần kéo dài phải lớn hơn 2 lần độ dày của tấm, tức là r22t, để làm cho việc kéo dài diễn ra suôn sẻ hơn, thường lấy r2=(5~10) t, bán kính cạnh lồi tối đa phải nhỏ hơn hoặc bằng 8 lần độ dày của tấm, tức là r28t. (Xem hình trên)
2.3 Đường kính khoang bên trong của bộ phận kéo tròn
Đường kính khoang bên trong của phần kéo tròn nên được lấy D d+10t để ép tấm không bị nhăn khi kéo dài. (Xem hình trên)
2.4 Bán kính góc tròn giữa hai bức tường liền kề của phần mở rộng hình chữ nhật
Bán kính góc tròn giữa hai bức tường liền kề của phần kéo hình chữ nhật nên được lấy r3 3t, để giảm số lần kéo nên lấy r3 H/5 càng nhiều càng tốt để kéo ra cùng một lúc.
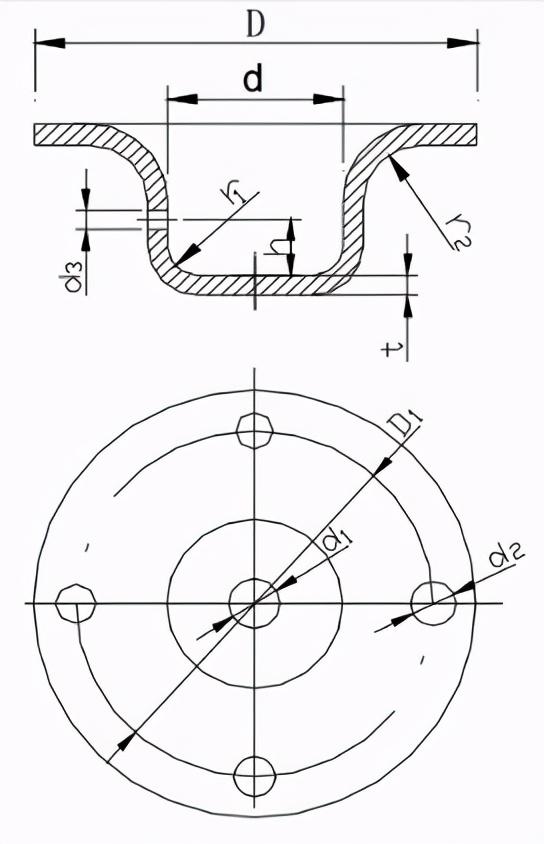
2.5 Yêu cầu về mối quan hệ kích thước giữa chiều cao và đường kính khi vòng không có cạnh lồi được hình thành cùng một lúc
Khi vòng không có cạnh lồi kéo dài được hình thành cùng một lúc, tỷ lệ chiều cao H và đường kính d phải nhỏ hơn hoặc bằng 0,4, đó là H/d 0,4, như trong hình dưới đây.
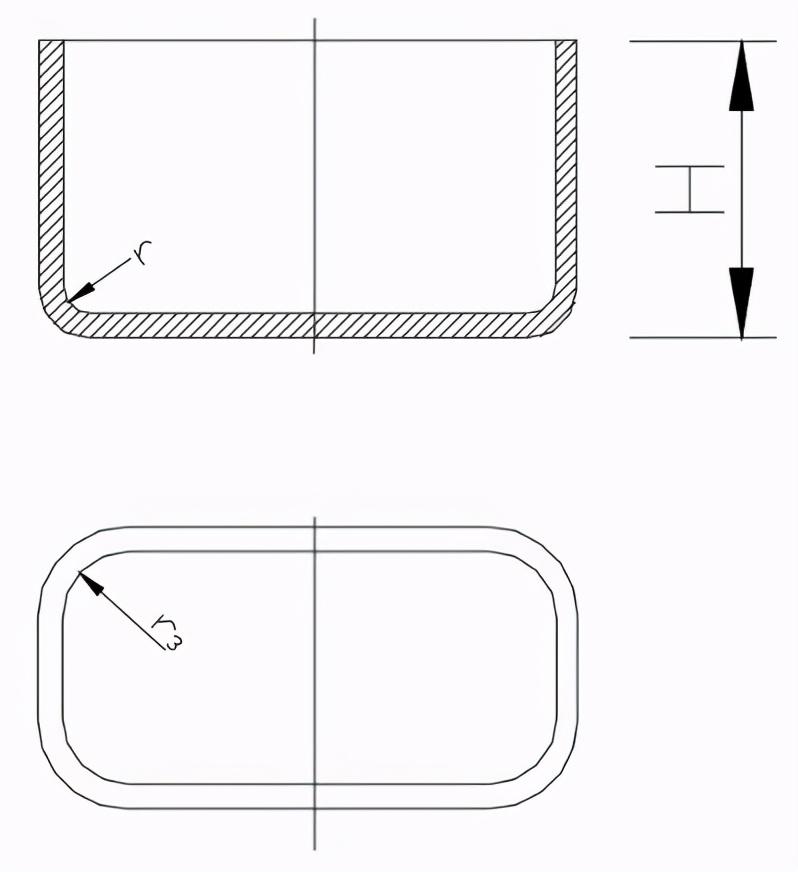
2.6 Thay đổi độ dày của vật liệu kéo dài:
Các bộ phận kéo dài thay đổi độ dày của vật liệu sau khi kéo dài do kích thước ứng suất khác nhau ở mỗi nơi. Nói chung, trung tâm của đáy giữ độ dày ban đầu, vật liệu mỏng hơn ở góc tròn của đáy, vật liệu dày hơn ở đỉnh gần mép lồi và vật liệu dày hơn ở góc tròn xung quanh phần căng hình chữ nhật.
2.7 Phương pháp đánh dấu kích thước sản phẩm của phần kéo dài
Khi thiết kế sản phẩm kéo dài, kích thước trên bản vẽ sản phẩm phải được chỉ rõ rằng kích thước bên ngoài hoặc kích thước bên trong phải được đảm bảo và không thể đánh dấu kích thước bên trong và bên ngoài cùng một lúc.
2.8 Phương pháp đánh dấu dung sai kích thước của phần kéo dài
Bán kính bên trong của vòng cung lồi lõm và dung sai kích thước chiều cao của phần kéo dài hình trụ chính là độ lệch đối xứng hai mặt, giá trị độ lệch của nó là một nửa giá trị tuyệt đối của dung sai chính xác cấp 16 tiêu chuẩn quốc gia (GB) và được đánh dấu.
3. Các hình dạng khác của kim loại tấm: tăng cường gân - nhấn gân trên các bộ phận kim loại dạng tấm, giúp tăng độ cứng của cấu trúc.
Rèm - Rèm thường được sử dụng trên các vỏ bọc hoặc vỏ máy khác nhau để thông gió và tản nhiệt.
Lỗ vát (lỗ kéo dài) - để xử lý các chủ đề hoặc cải thiện độ cứng của lỗ.
3. Tăng cường gân:
Tăng cường cấu trúc gân và lựa chọn kích thước của nó
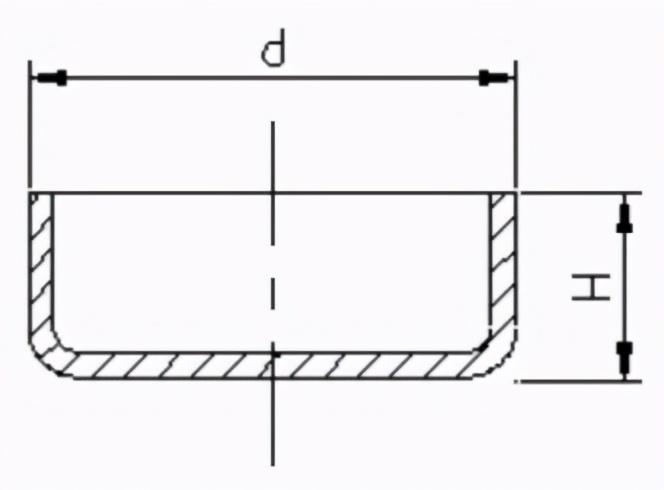
Kích thước cực hạn của khoảng cách nổi bật và khoảng cách nổi bật được chọn dưới bảng.
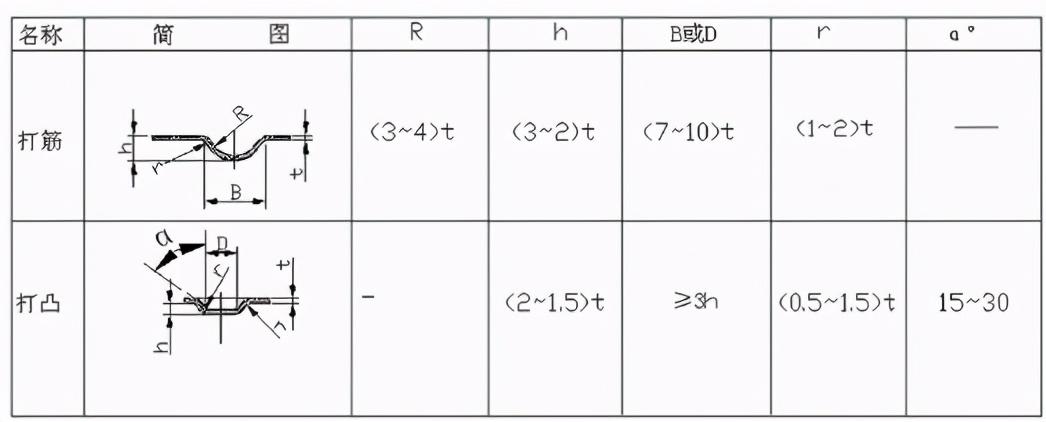
3.2 Cửa chớp
Phương pháp tạo hình rèm là cắt vật liệu bằng một cạnh của khuôn lồi, trong khi phần còn lại của khuôn lồi sẽ làm biến dạng kéo dài vật liệu cùng một lúc, tạo thành hình dạng nhấp nhô của một bên mở.
Cấu trúc điển hình của rèm xem hình dưới đây
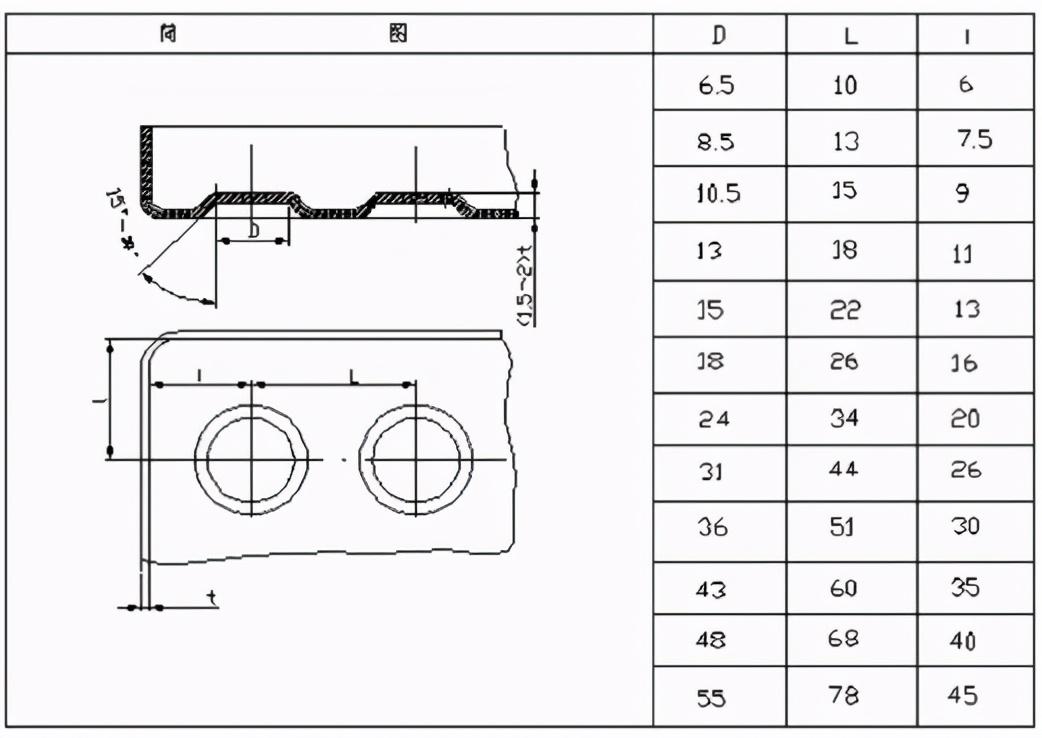
Yêu cầu kích thước rèm: a4t; b6t;h5t;L24t;r0.5t。
3. 3 lỗ vát (lỗ kéo dài)
Hình thức gấp lỗ tương đối nhiều, thông thường là phải gia công gấp lỗ bên trong.
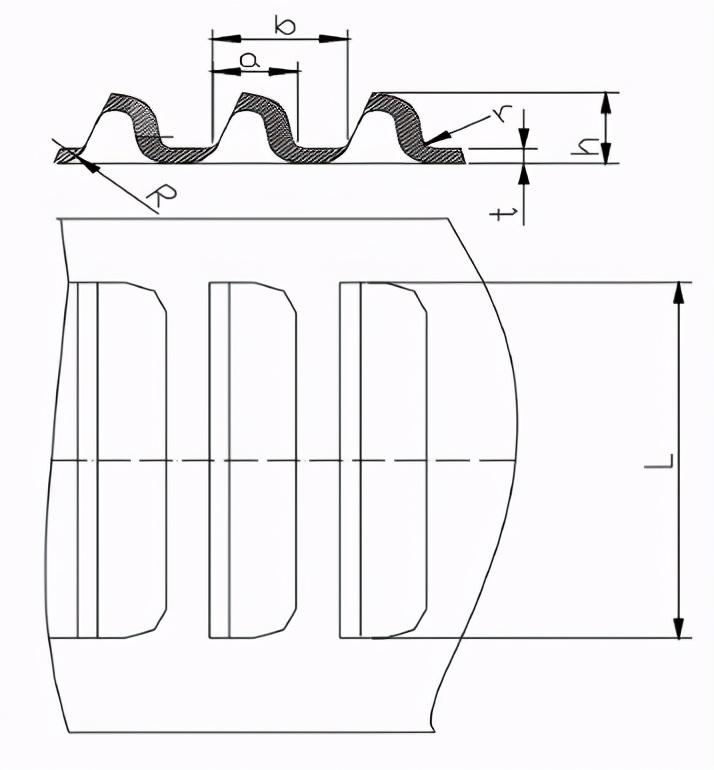
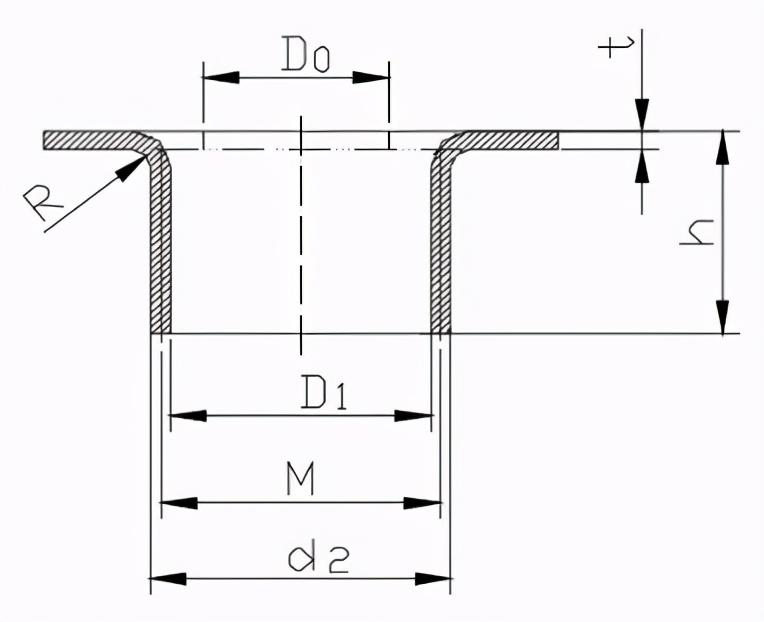
Quá trình gia công kim loại tấm - tán đinh của các phụ kiện trên kim loại tấm gia công khác, chẳng hạn như đai ốc tán đinh, đinh tán đinh tán, đinh hướng đinh tán, v.v.
2. Tấn công răng của lỗ ren trên tấm kim loại.
Tấm kim loại dày t< 1,5 giờ, áp dụng công nha phiên biên. Khi tấm kim loại dày t1.5, răng tấn công trực tiếp có thể được sử dụng.
Quá trình gia công kim loại tấm - hàn trong thiết kế cấu trúc hàn kim loại tấm, nên thực hiện "đối xứng sắp xếp các mối hàn, mối hàn, và tránh giao thoa, tập hợp, chồng chéo, mối hàn nhỏ, mối hàn có thể bị gián đoạn, mối hàn chính, mối hàn nên được kết nối."
Trong kim loại tấm thường được hàn với hàn hồ quang, hàn điện trở, v.v.
Giữa các tấm kim loại hàn hồ quang phải có đủ không gian hàn, khoảng cách hàn tối đa phải là 0,5~0,8mm, mối hàn phải đồng đều và phẳng.
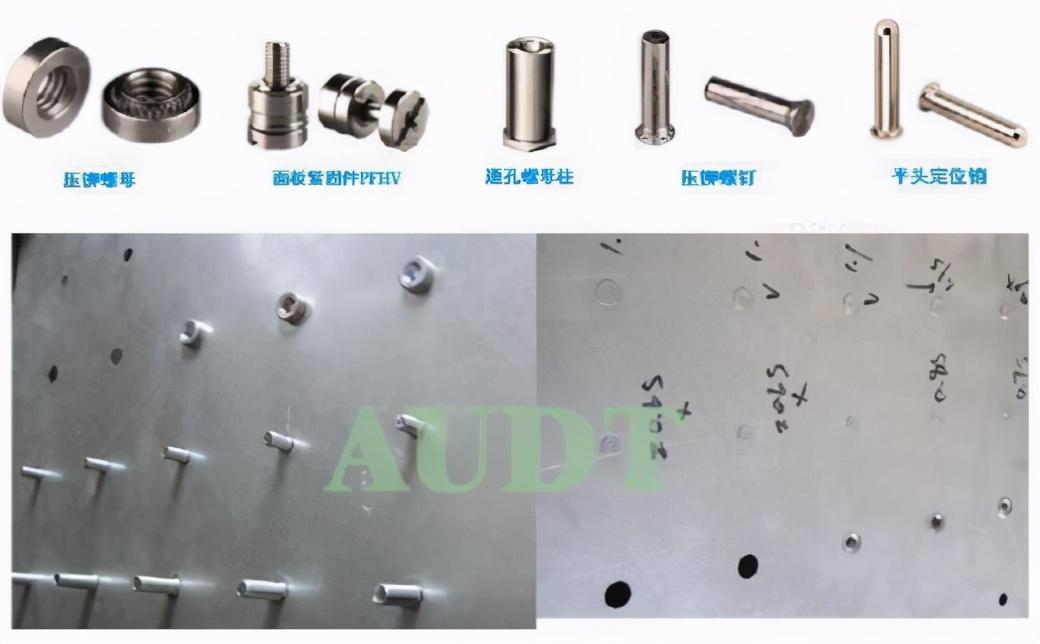
2. Bề mặt hàn điện trở yêu cầu phải phẳng, không nhăn, bật lại, v.v.
Kích thước của hàn kháng như sau:
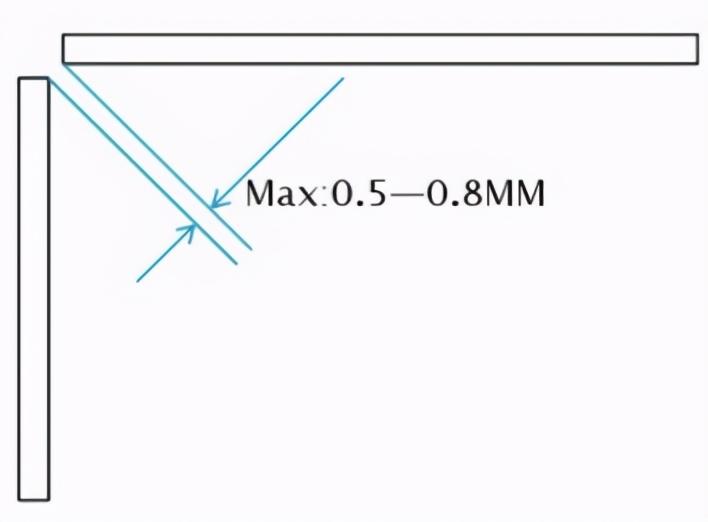
Khoảng cách điểm hàn kháng
Trong ứng dụng thực tế, dữ liệu bảng dưới đây có thể được tham khảo khi hàn các bộ phận nhỏ.
Khi hàn các bộ phận kích thước lớn, khoảng cách điểm có thể được tăng lên một cách thích hợp, thường không nhỏ hơn 40-50mm, các bộ phận không chịu lực, khoảng cách giữa các điểm hàn có thể được mở rộng đến 70-80mm.
Độ dày tấm t, đường kính điểm hàn d, đường kính điểm hàn tối thiểu dmin, khoảng cách tối thiểu giữa các điểm hàn e, nếu tấm là sự kết hợp độ dày khác nhau, hãy chọn tấm mỏng nhất.
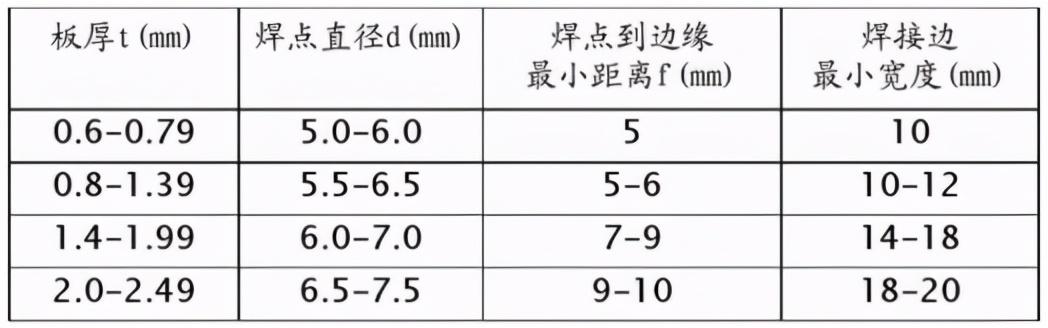
Số lớp hàn kháng và tỷ lệ độ dày vật liệu
Tấm hàn điểm điện trở thường là 2 lớp, tối đa 3 lớp, tỷ lệ độ dày tấm của mỗi lớp đầu hàn nên nằm trong khoảng 1/3~3.
Nếu thực sự cần hàn tấm 3 lớp, trước tiên bạn nên kiểm tra tỷ lệ độ dày vật liệu, nếu hợp lý có thể hàn, nếu không hợp lý, bạn nên xem xét mở lỗ quá trình hoặc lỗ quá trình, hàn 2 lớp, điểm hàn xen kẽ.
Quá trình gia công kim loại tấm - chế độ kết nối Ở đây chủ yếu giới thiệu cách kết nối kim loại tấm trong quá trình chế biến, chủ yếu là tán đinh, hàn (như đã đề cập ở trên), tán đinh bơm, tán đinh TOX.
Đinh tán tán: Loại đinh tán này thường được gọi là đinh tán, hai tấm được tán bằng đinh tán tán lại với nhau gọi là đinh tán tán, hình dạng tán tán phổ biến như hình ảnh:
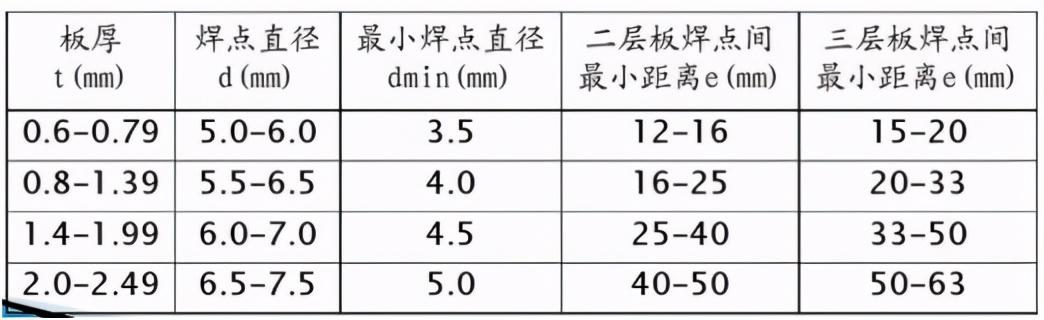
2. Hàn (như đã đề cập trước đó) 3. Bơm tán đinh: trong đó một số không là lỗ bơm và một số không là lỗ chìm, làm cho nó trở thành một kết nối không thể tháo rời bằng cách chạm vào tán đinh.
Tính ưu việt: Bản thân lỗ hút phối hợp với lỗ chìm có chức năng định vị. Cường độ tán hợp cao, thông qua khuôn tán hợp hiệu quả cũng tương đối cao.
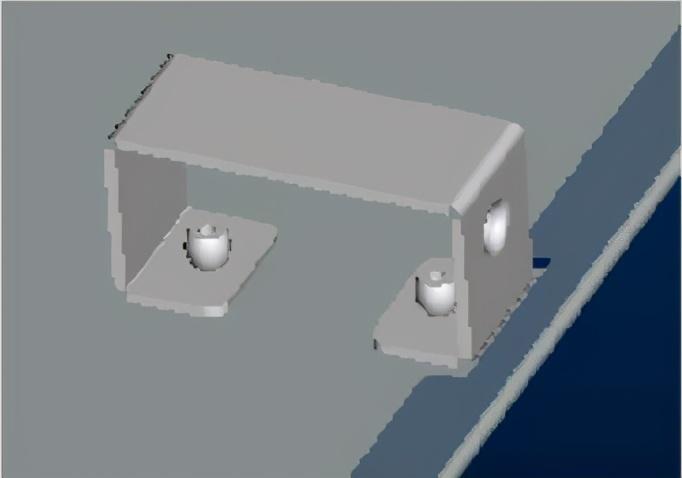
4. TOX tán đinh: thông qua một khuôn lồi đơn giản sẽ được ép vào khuôn lõm bởi các mảnh ghép. Dưới tác động của áp lực hơn nữa, đó là vật liệu bên trong khuôn lõm "chảy" ra bên ngoài. Kết quả là tạo ra một điểm kết nối tròn không có góc cạnh và không có gờ, và sẽ không ảnh hưởng đến khả năng chống ăn mòn của nó, ngay cả khi bề mặt có lớp phủ hoặc lớp sơn của tấm cũng có thể giữ lại các đặc tính chống ăn mòn ban đầu, bởi vì lớp mạ và lớp sơn và tấm cũng có thể giữ lại các đặc tính chống ăn mòn ban đầu, bởi vì lớp phủ và lớp sơn cũng biến dạng với nhau. Vật liệu được ép sang cả hai bên và được ép vào các miếng dựa vào mặt lõm của khuôn, do đó tạo thành các chấm kết nối TOX. Như hình dưới đây cho thấy:
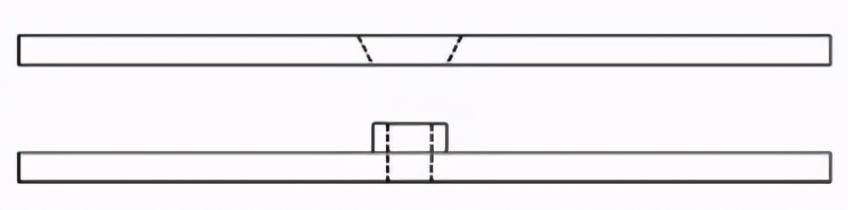
Quá trình gia công kim loại tấm - xử lý bề mặt để xử lý bề mặt kim loại tấm có thể đóng vai trò bảo vệ chống ăn mòn và trang trí. Xử lý bề mặt phổ biến cho kim loại tấm là: phun bột, mạ kẽm điện, kẽm nhúng nóng, oxy hóa bề mặt, vẽ bề mặt, in lụa, v.v.
Bề mặt kim loại tấm nên được loại bỏ dầu bẩn, rỉ sét, hàn xỉ và vân vân trước khi xử lý bề mặt.
Phun bột: Bề mặt kim loại tấm được phun bằng chất lỏng và sơn bột, chúng tôi thường sử dụng sơn bột. Thông qua phun bột, hấp phụ tĩnh điện, nướng nhiệt độ cao và các phương pháp khác, phun một lớp sơn màu khác nhau trên bề mặt kim loại tấm để làm đẹp bề ngoài và có thể tăng khả năng chống ăn mòn của vật liệu. Là phương thức xử lý bề mặt thường dùng.
Lưu ý: các nhà sản xuất khác nhau phun ra bao nhiêu màu sắc sẽ có một sự khác biệt màu sắc nhất định, vì vậy cùng một thiết bị của cùng một màu kim loại tấm nên được phun càng nhiều càng tốt trong cùng một nhà sản xuất.
2. Mạ kẽm điện, mạ kẽm bề mặt của kim loại tấm kẽm nhúng nóng là phương pháp xử lý chống ăn mòn bề mặt thường được sử dụng, và nó có thể đóng một vai trò làm đẹp nhất định. Mạ kẽm có thể được chia thành mạ kẽm điện và mạ kẽm nhúng nóng.
Bề ngoài của mạ kẽm điện tương đối sáng và bằng phẳng, lớp mạ kẽm mỏng hơn, thường được sử dụng hơn.
Mạ kẽm nhúng nóng dày hơn và có thể tạo ra một lớp hợp kim sắt-kẽm, khả năng chống ăn mòn mạnh hơn mạ kẽm điện.
3. oxy hóa bề mặt: ở đây chủ yếu giới thiệu về anodizing bề mặt của nhôm và hợp kim nhôm.
Anodizing bề mặt của nhôm và hợp kim nhôm có thể được oxy hóa thành nhiều màu sắc khác nhau, đóng vai trò bảo vệ và có tác dụng trang trí tốt. Đồng thời, nó có thể tạo ra màng anodized trên bề mặt của vật liệu, màng anodized có độ cứng và khả năng chống mài mòn cao hơn, nhưng cũng có cách điện tốt và cách nhiệt.
4. Vẽ bề mặt: Đặt vật liệu giữa các bánh xe lăn trên và dưới của máy vẽ dây, có một vành đai mài mòn gắn liền với bánh xe lăn, được điều khiển bởi động cơ, để vật liệu đi qua vành đai mài mòn trên và dưới, kéo ra từng dấu vết trên bề mặt vật liệu, theo sự khác biệt của vành đai mài mòn, kích thước dấu vết cũng không giống nhau, vai trò chính là làm đẹp vẻ ngoài. Thông thường đều là vật liệu nhôm mới xem xét phương thức xử lý bề mặt bằng sợi.
5. In lụa trên bề mặt vật liệu in lụa trên quá trình đánh dấu khác nhau, nói chung có hai cách in lụa phẳng và in pad, màn hình lụa phẳng chủ yếu được sử dụng trên mặt phẳng chung, nhưng nếu gặp phải nơi có hố sâu hơn, cần phải sử dụng in pad.
Tơ tằm phải có tơ tằm.
Phụ kiện tham khảo cho độ chính xác gia công kim loại tấm:
GBT1914-2002 Bộ phận dập Dung sai kích thước
GBT1915-2002-T Dung sai góc cho các bộ phận dập
GB-T15005-2007 Bộ phận dập Không dung sai Độ lệch giới hạn
GB-T 13916-2002 Bộ phận dập Hình dạng và vị trí Không khoan dung
Khả năng của thiết bị gia công kim loại tấm phổ biến Phạm vi gia công thiết bị kim loại tấm phổ biến
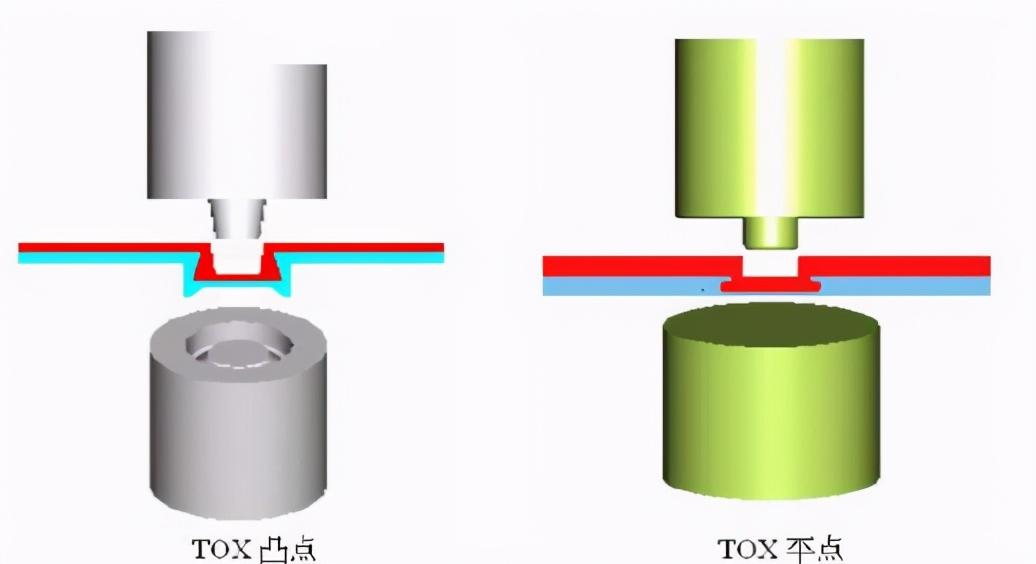
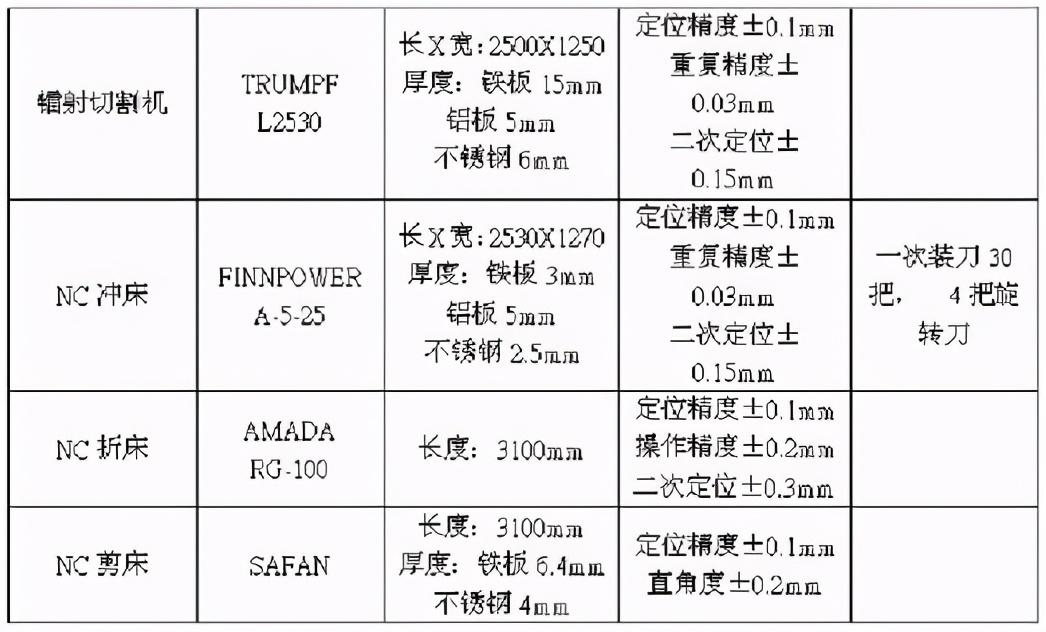