Trong quá trình cắt kim loại tấm bằng máy cắt laser Thẩm Dương, các vấn đề khác nhau thường gặp phải. Để đảm bảo chất lượng cắt, sau đây là một số vấn đề phổ biến và giải pháp thông thường:
1. Kỹ thuật cắt lỗ:
Bất kỳ kỹ thuật cắt nhiệt nào, ngoại trừ một số trường hợp có thể bắt đầu từ cạnh của tấm, thường phải mặc một lỗ nhỏ trên tấm. Trước đây trên máy ép laser là dùng đấm trước tiên lao ra một lỗ, sau đó lại dùng laser bắt đầu cắt từ lỗ nhỏ. Có hai phương pháp cơ bản để đục lỗ cho máy cắt laser không có thiết bị dập:
Nổ thủng - Vật liệu tạo thành một lỗ trong lõi sau khi được chiếu xạ bằng tia laser liên tục, sau đó nhanh chóng loại bỏ vật liệu nóng chảy bằng dòng oxy đồng trục với chùm tia laser để tạo thành một lỗ. Kích thước của lỗ thông thường có liên quan đến độ dày của tấm, đường kính trung bình của lỗ thủng nổ là một nửa độ dày của tấm, do đó, lỗ thủng nổ trên tấm dày hơn lớn hơn và không tròn, không nên được sử dụng trên các bộ phận có yêu cầu độ chính xác xử lý cao hơn, chỉ có thể được sử dụng trên phế liệu. Ngoài ra, do áp suất oxy được sử dụng để đục lỗ giống như khi cắt, nên vết văng khá lớn.
Pulsed Piercing - Sử dụng công suất cao nhất xung laser để làm cho một lượng nhỏ vật liệu tan chảy hoặc bốc hơi, không khí hoặc nitơ thường được sử dụng làm khí phụ trợ để giảm lỗ mở rộng do quá trình oxy hóa tỏa nhiệt, áp suất khí nhỏ hơn áp suất oxy khi cắt. Mỗi xung laser chỉ tạo ra các tia nhỏ, dần dần sâu hơn, vì vậy thời gian thủng tấm dày mất vài giây. Ngay sau khi lỗ thủng hoàn tất, khí phụ được thay thế bằng oxy để cắt. Đường kính lỗ thủng như vậy nhỏ hơn và chất lượng lỗ thủng của nó tốt hơn so với lỗ thủng nổ. Laser được sử dụng cho mục đích này không chỉ phải có công suất đầu ra cao; Quan trọng hơn là các đặc tính thời gian và không gian của chùm tia, vì vậy laser CO2 dòng chảy ngang nói chung không thể thích ứng với yêu cầu cắt laser. Ngoài ra, thủng xung cũng cần có một hệ thống điều khiển đường dẫn khí đáng tin cậy hơn để đạt được loại khí, chuyển đổi áp suất khí và kiểm soát thời gian thủng.
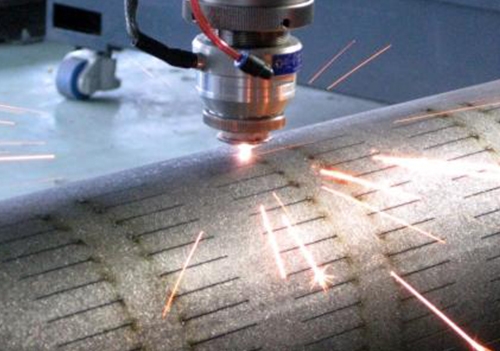
Trong trường hợp thủng xung được thông qua, để có được vết cắt chất lượng cao, cần chú ý đến công nghệ chuyển tiếp từ thủng xung khi phôi đứng yên đến cắt liên tục với tốc độ bằng nhau của phôi. Về mặt lý thuyết, nó thường có thể thay đổi các điều kiện cắt của phần tăng tốc, chẳng hạn như tiêu cự, vị trí vòi phun, áp suất khí, v.v., nhưng trên thực tế, không có khả năng thay đổi các điều kiện trên vì thời gian quá ngắn. Trong sản xuất công nghiệp chủ yếu sử dụng phương pháp thay đổi công suất trung bình của laser là tương đối thực tế, phương pháp cụ thể là thay đổi chiều rộng xung; Thay đổi tần số xung; Thay đổi chiều rộng và tần số xung cùng một lúc. Kết quả thực tế cho thấy loại thứ ba sẽ hoạt động tốt.
2. Phân tích tình trạng biến dạng của lỗ nhỏ gia công cắt (đường kính nhỏ so với độ dày tấm):
Điều này là do máy công cụ (chỉ dành cho máy cắt laser công suất cao) khi xử lý các lỗ nhỏ thay vì áp dụng phương pháp nổ thủng, mà bằng cách đục lỗ xung (đâm mềm), làm cho năng lượng laser quá tập trung trong một khu vực rất nhỏ, đốt cháy cả khu vực không xử lý, gây biến dạng lỗ, ảnh hưởng đến chất lượng xử lý. Tại thời điểm này, chúng ta nên thay đổi cách thủng xung (đâm mềm) thành cách thủng nổ (đâm thông thường) trong quy trình xử lý để giải quyết. Và đối với máy cắt laser công suất nhỏ hơn thì ngược lại, trong quá trình xử lý lỗ nhỏ nên áp dụng phương pháp đục lỗ xung để đạt được độ hoàn thiện bề mặt tốt hơn.
Nội dung bài viết bắt nguồn từ mạng internet, nếu có vấn đề xin liên hệ với tôi xóa bỏ!