Sheet metal parts are products processed by sheet metal technology, and we cannot live without sheet metal parts everywhere. Sheet metal parts are made through filament power winding, laser cutting, heavy-duty processing, metal bonding, metal drawing, plasma cutting, precision welding, roll forming, metal sheet bending, forging, water jet cutting, and precision welding.
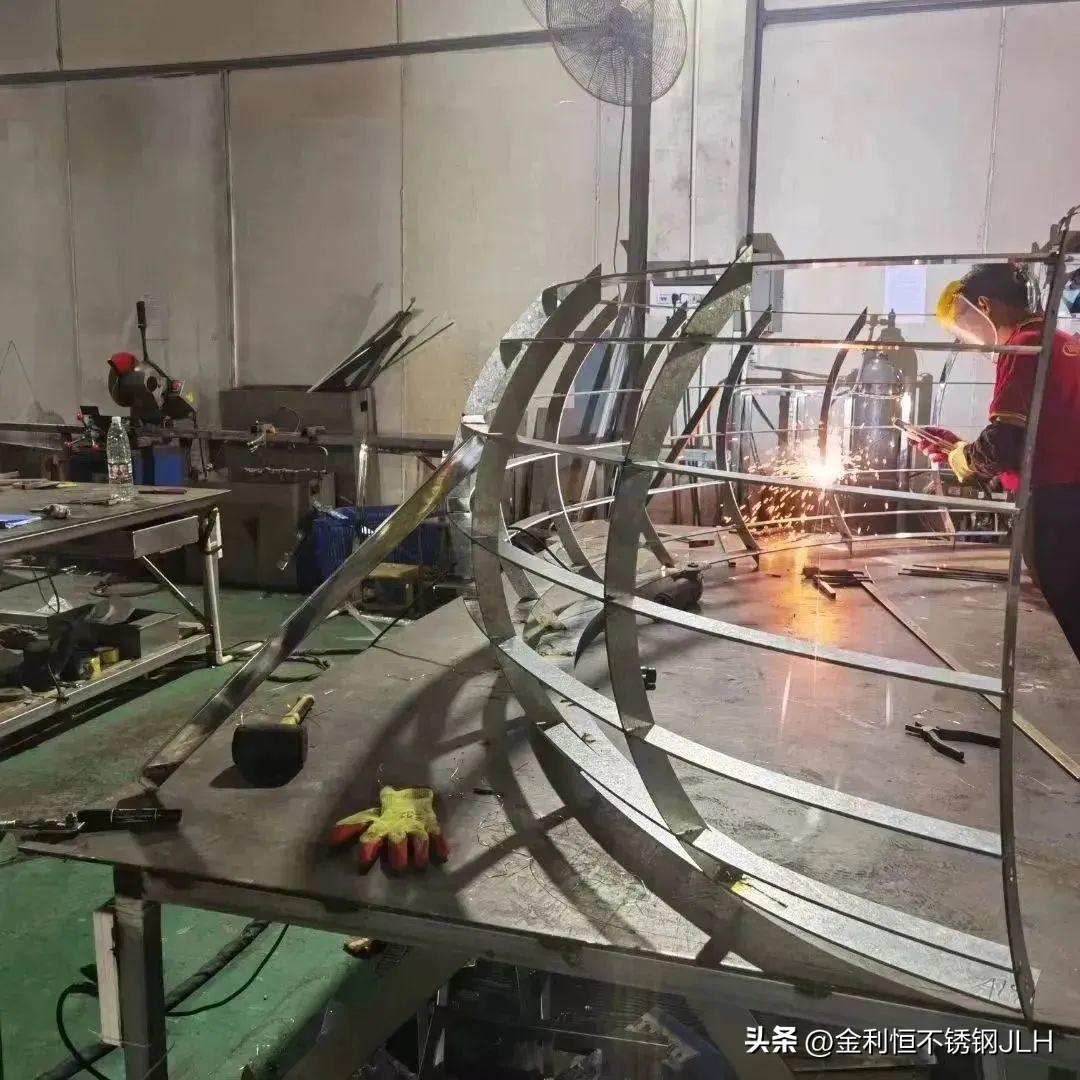
Stainless steel sheet metal processing manufacturer
In sheet metal processing, there are some necessary rules and regulations that we must abide by. Therefore, since it is important, Jin Liheng will provide a specific explanation of this content below, so that everyone can learn, understand and grasp it clearly, so as to better understand sheet metal processing and delve into this field, making their knowledge more extensive and knowledge more diverse.
For some rules in sheet metal, they have a certain scope of application, mainly including: the thickness of the material being cut, its basic size should be 0.5-6mm, and its maximum width range should be 2500mm.
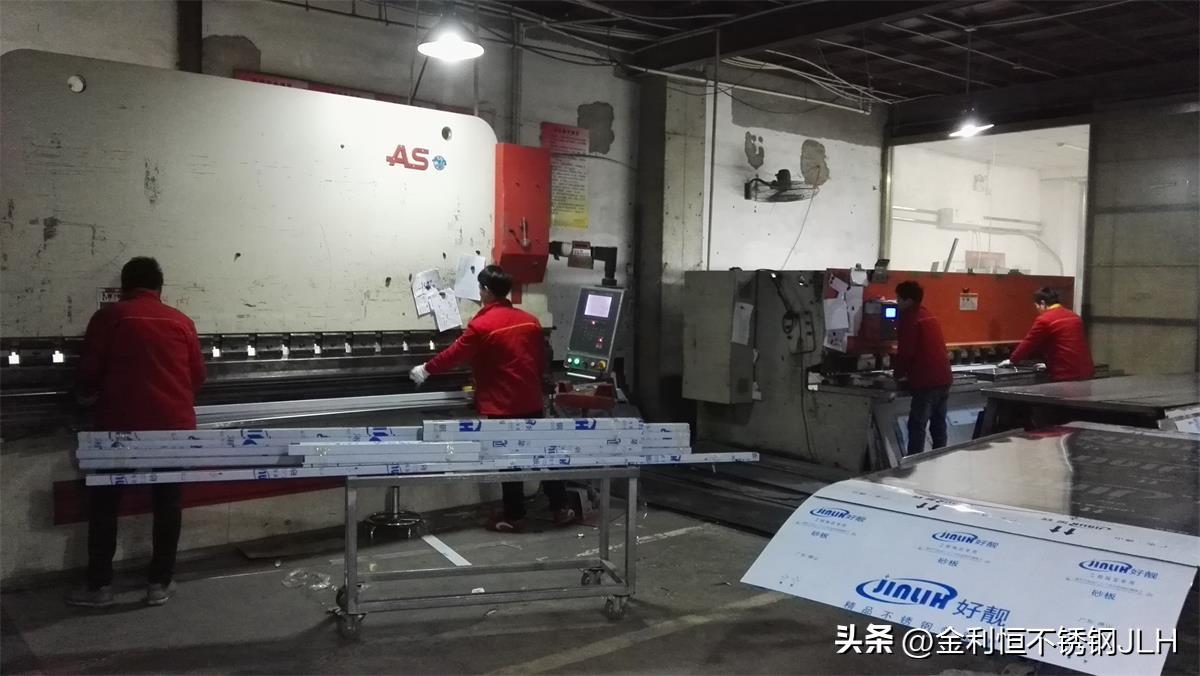
Stainless steel sheet metal processing manufacturer
1. In terms of materials
(1) The materials used should meet the technical requirements, otherwise they cannot be used.
(2) If cold-rolled steel plates are used, their surface must not have scratches, scratches, rust spots, or impurities, which means there must be no defects.
(3) The equipment needs to be prepared, as well as the tools needed, such as vernier calipers, micrometers, steel tapes, and scribes.
2. Preparation in terms of craftsmanship
(1) Be very familiar and familiar with its related drawings, process requirements, and size requirements.
(2) To check if the material meets the process requirements and if necessary lubrication work is carried out on the equipment to ensure its normal operation.
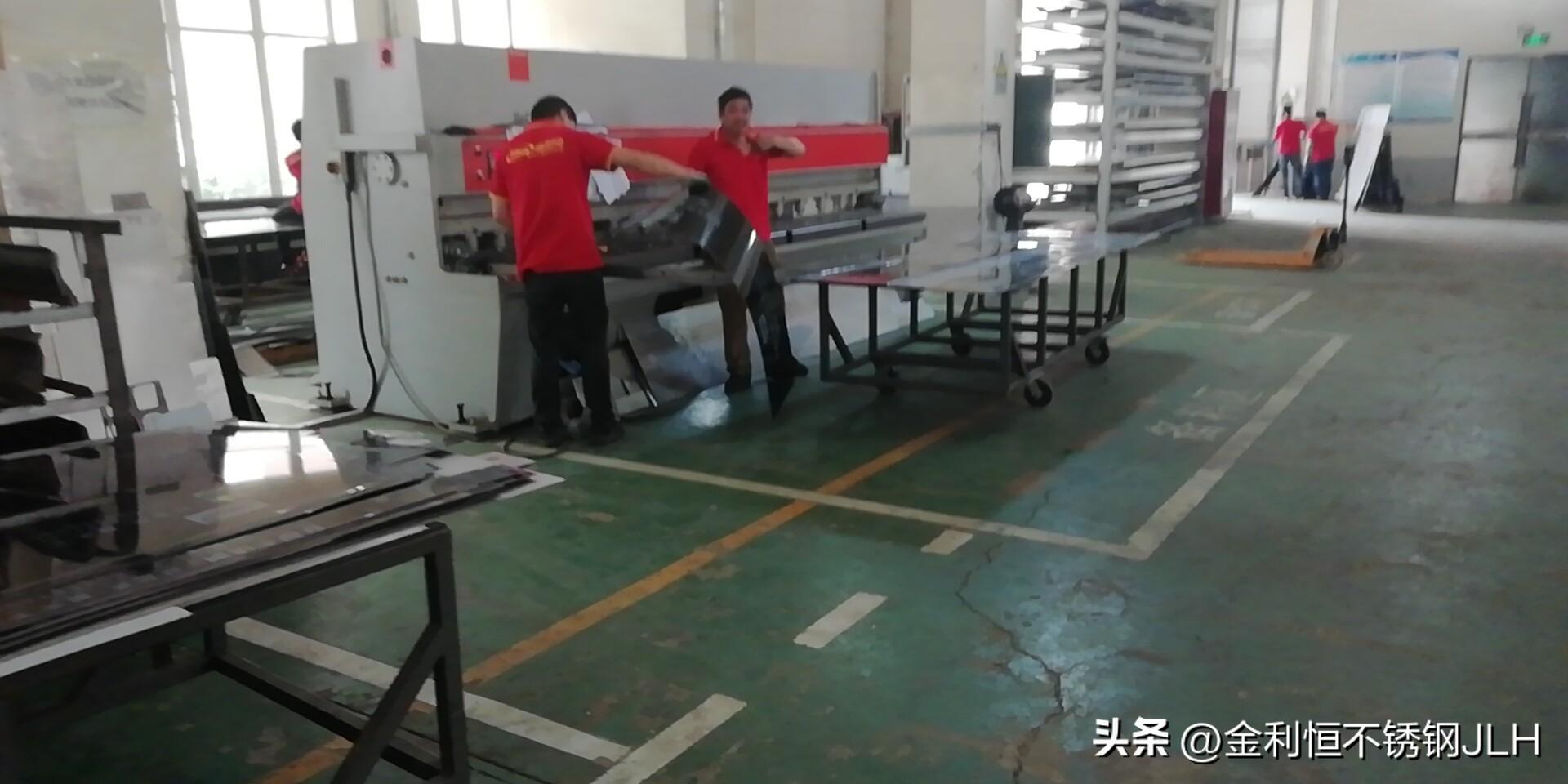
Stainless steel sheet metal processing manufacturer
The processed parts of the finished product are welded or plated according to different requirements, and finally sent to the customer's hands. With the continuous development of production and technological progress, the vast majority of forming processes are completed on machines. Manual methods are often used as supplementary processing or finishing work. However, in the case of single piece production or some parts with complex shapes, manual operation and processing are still indispensable. Manual forming is mainly completed using some simple tire shapes, molds, and various fixtures.
Emma Technology Co., Ltd. is one of the leading professional manufacturers of precision metal parts in China, established in 2006. It mainly undertakes business such as CNC Machining parts, metal stamping parts, and sheet metal processing.