Stamping is a commonly used processing technique in metal processing. With the increasing demand for product accuracy, the application of CNC spinning machining is gradually becoming more and more widespread. Both processes can process sheet materials into shape, but compared to stamping, CNC spinning has significant differences and advantages.
1. Principle difference
CNC spinning processing is controlled by the path of the rotary wheel (cutting wheel) to control the flow and deformation of the billet, while stretching and stamping forming is controlled by the combination of upper and lower convex and concave molds to control the flow of the material and ultimately form.
2. Mold differences
To produce the same hardware molding product, CNC spinning only requires the production of one core mold, while stretching and stamping require the production of two convex and concave molds. The manufacturing cost of the molds is usually 3-6 times that of CNC spinning. Moreover, the manufacturing cycle of spinning molds is shorter than that of stretching and stamping molds, and the dimensions are also easier to modify.
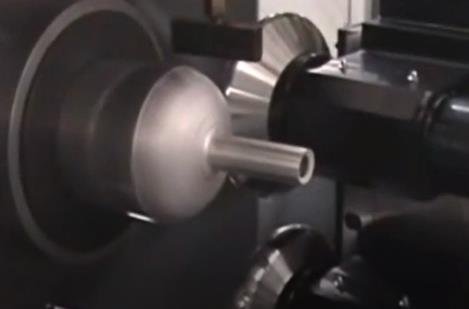
Shangxi shrink tube spinning
3. Differences in material costs
The thinning rate of raw materials in spinning processing is usually about 30%, while the thinning rate in stretching and stamping processing is about 10%. The thinning rate in CNC spinning processing is relatively higher. At present, the minimum thickness of metal materials that can be processed by CNC spinning is 0.5mm, while stretching and stamping require about 5-10mm of edge pressing material, which requires a high material cost.
4. Differences in processing procedures
Even for simple hardware formed products, stretching and stamping still need to go through basic processes such as cutting, forming, and trimming. Some products require multiple stretching processes for forming, which are complex but have relatively faster processing speeds; The forming and cutting of CNC spinning can be completed simultaneously on a CNC spinning machine, but the processing speed of individual parts will be slow. In addition, for some products with long or irregular stretching heights, stretching and stamping forming may cause product cracking, while spinning processing is easier to complete product forming.
5 Product Differences
From the surface of the product, spinning processed products have spinning patterns distributed in a circular pattern, while stamping processed products have drawing patterns distributed vertically on the surface; In terms of product strength, due to the metal being spun, the internal arrangement of molecules becomes tighter and the density increases. Therefore, the strength of spun products is much higher than that of tensile stamping.
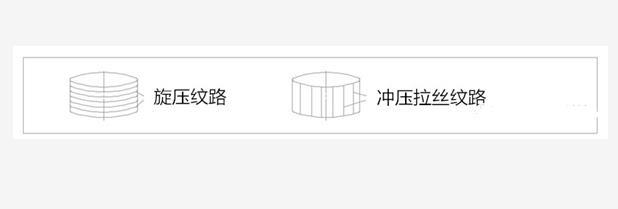
The difference in texture between spinning and stamping
Due to these advantages of CNC spinning, it is also widely used in aerospace, military, hydropower and other fields, especially in aerospace manufacturing products such as aircraft nose covers and auxiliary fuel tanks with large dimensions, high precision and strength requirements. Traditional stamping processing is no longer able to meet the requirements. Therefore, CNC spinning processing has also been increasingly widely used.