The selection of cutting tools and tools is one of the important contents in CNC Machining technology, which not only affects the machining efficiency of the machine tool, but also directly affects the machining quality. Compared with traditional machining methods, CNC machining has higher requirements for cutting tools and tools. Not only does it require high precision, good rigidity, and durability, but it also requires stable size and convenient installation and adjustment.
CNC machining tool materials 1. High speed steel
High speed steel, also known as front steel or white steel. It is an alloy steel containing elements such as tungsten (W), molybdenum (Mo), chromium (Cr), vanadium (V), cobalt (Co), etc. It is divided into two major series of tungsten and molybdenum and is a traditional tool material. Its room temperature hardness is 62-65HRC, and its thermal hardness can be increased to 500-600 ℃. After quenching, the deformation is small, easy to sharpen, and can be forged and cut. It can not only be used to manufacture drill bits and milling cutters, but also to manufacture complex cutting tools such as gear cutters and forming milling cutters. However, due to its low allowable cutting speed (50m/min), it is mostly used for low-speed machining on CNC machines. Ordinary high-speed steel is represented by W18Cr4V.
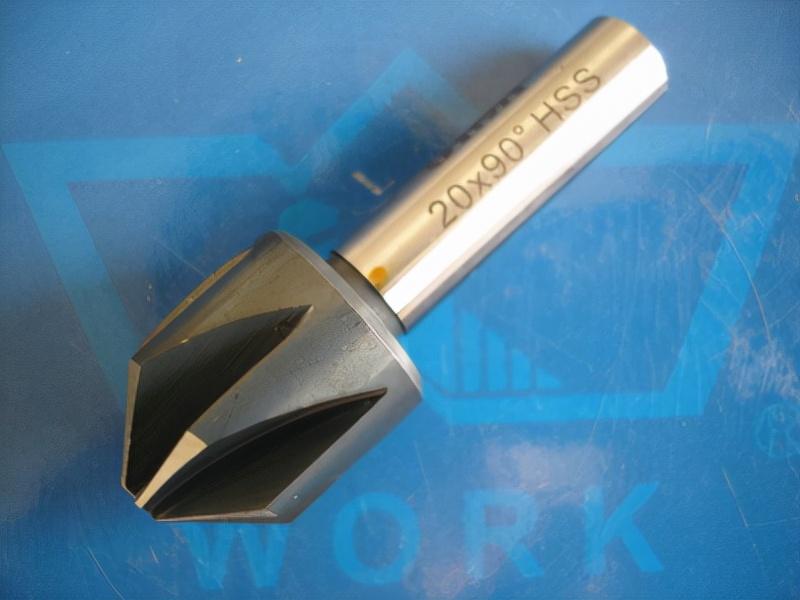
2. Hard alloy
Hard alloy is a powder metallurgy product made from carbides (WC, TiC, TaC, NbC, etc.) with high hardness and melting point, using Co, Mo, Ni as binders. Its room temperature hardness can reach 74-82HRC and can withstand high temperatures ranging from 800 ℃ to 1000 ℃. Due to its low production cost, it can exhibit excellent cutting performance in medium speed (150m/min) and high feed cutting, making it the most widely used tool material in CNC machining. But its impact toughness and bending strength are much lower than those of high-speed steel, so it is rarely made into integral cutting tools. In practical use, hard alloy cutting blocks are generally fixed on the cutting body by welding or mechanical clamping. The commonly used hard alloys include tungsten cobalt (YG) alloys (YG8, YG6, YG3), tungsten titanium (YT) alloys (YT5, YT15, YT30), and tungsten titanium tantalum (niobium) (YW) (YW1, YW2) alloys.
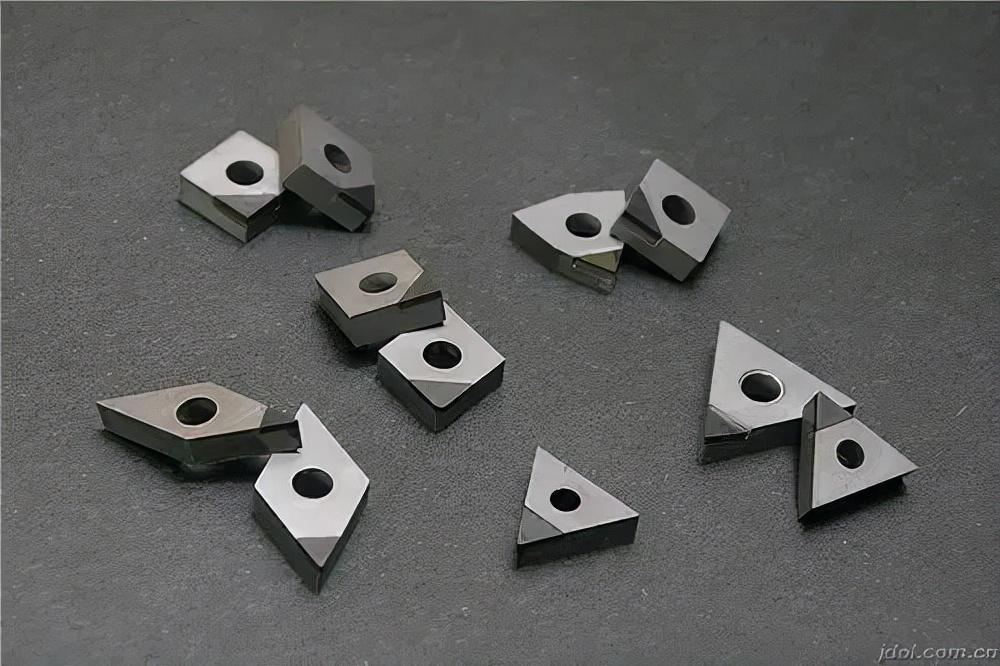
3. Coated hard alloy
Coated hard alloy tools are made by coating one or more layers of wear-resistant TiN, TiCN, TiAlN, and Al2O3 on hard alloy tools with good toughness. The thickness of the coating ranges from 2 µ m to 18 µ m. Coatings usually have two functions: on the one hand, they have a much lower thermal conductivity coefficient than the tool substrate and workpiece material, weakening the thermal effect of the tool substrate; On the other hand, it can effectively improve the friction and adhesion during the cutting process, reducing the generation of cutting heat. TiN has low friction characteristics, which can reduce the loss of coating tissue. TiCN can reduce the wear of the rear cutting surface. The TiCN coating has a higher hardness. Al2O3 coating has excellent thermal insulation effect. Compared with hard alloy cutting tools, coated hard alloy cutting tools have greatly improved in terms of strength, hardness, and wear resistance. For cutting workpieces with a hardness of 45-55HRC, low-cost coated hard alloys can achieve high-speed cutting. In recent years, some manufacturers have relied on improving the coating materials and proportions, which has greatly improved the properties of coated cutting tools.
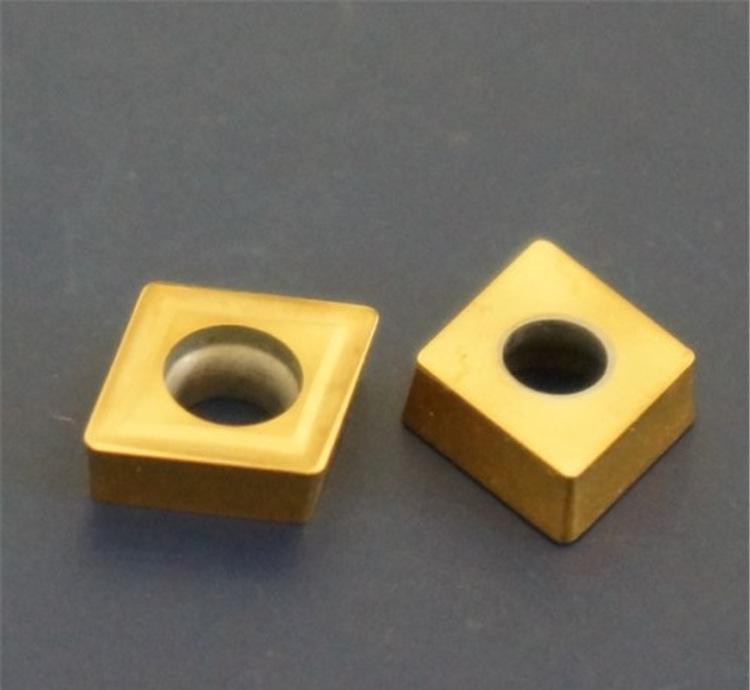
4. Ceramic materials
Ceramic is one of the cutting tool materials that has developed rapidly and has become increasingly widely used in the past 20 years. In the near future, ceramics may lead to a third revolution in cutting machining, following high-speed steel and hard alloys.
Ceramic cutting tools have advantages such as high hardness (91-95HRA), high strength (bending strength of 750MPa~1000MPa), good wear resistance, good chemical stability, good adhesive resistance, low friction coefficient, and low cost. Not only that, ceramic cutting tools also have high high-temperature hardness, reaching 80HRA at 1200 ℃. When used normally, ceramic cutting tools have an extremely long lifespan, and the cutting speed can be increased by 2-5 times compared to hard alloy cutting tools. They are particularly suitable for processing high hardness materials, precision machining, and high-speed machining. They can process various types of quenched steel and hardened cast iron with a hardness of up to 60HRC. Commonly used include alumina based ceramics, silicon nitride based ceramics, and metal ceramics. Alumina based ceramic cutting tools have higher thermal hardening than hard alloys. Under high-speed cutting conditions, the cutting edge generally does not undergo plastic deformation, but its strength and toughness are lower. In addition to high thermal hardness, silicon nitride based ceramics also have good toughness. Compared with silicon oxide based ceramics, its disadvantage is that it is prone to high-temperature diffusion during steel processing, which intensifies tool wear. Silicon nitride based ceramic tools are mainly used for intermittent turning and milling of gray cast iron. Cermet metal is a tool material based on carbides, similar to hard alloys, but with lower affinity, good friction, and better wear resistance. It can withstand higher cutting temperatures than conventional hard alloys, but lacks the impact resistance, toughness during heavy machining, and strength at low speeds and high feed rates of hard alloys. In recent years, through extensive research, improvement, and adoption of new manufacturing processes, the bending strength and toughness of ceramic materials have been greatly improved. For example, the new metal ceramic NX2525 developed by Mitsubishi Metal Company in Japan and the CT series of metal ceramic blades and the coated metal ceramic blade series developed by Sandvik Company in Sweden have significantly higher bending strength and wear resistance than ordinary metal ceramics, greatly expanding the application range of ceramic materials.
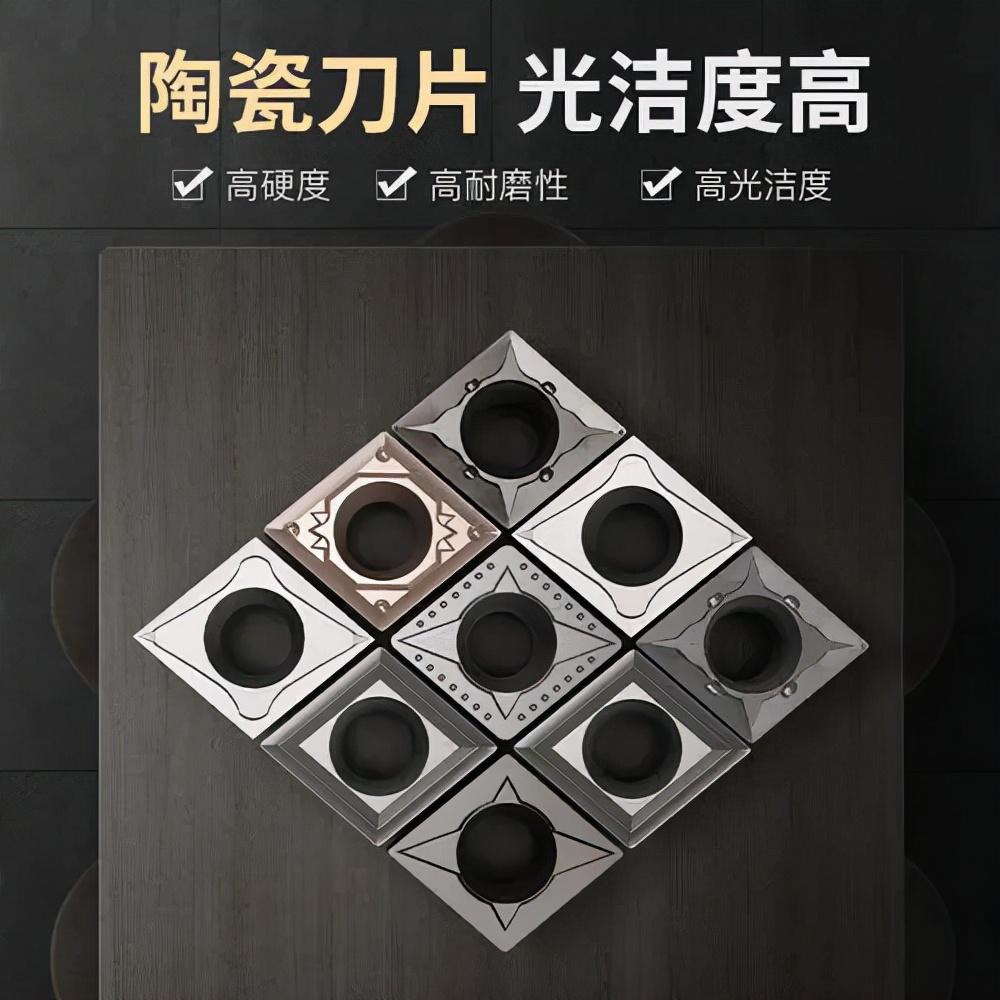
5. Cubic boron nitride (CBN)
CBN is a artificially synthesized high hardness material, with a hardness of up to 7300-9000HV. Its hardness and wear resistance are second only to diamond, and it has excellent high-temperature hardness. Compared with ceramic cutting tools, its heat resistance and chemical stability are slightly worse, but its impact toughness and anti crushing performance are better.
It is widely used for cutting hardened steel (above 50HRC), pearlite gray cast iron, chilled cast iron, and high-temperature alloys. Compared with hard alloy cutting tools, its cutting speed can be increased by an order of magnitude. PCBN (polycrystalline cubic boron nitride) cutting tools with high CBN content have high hardness, good wear resistance, high compressive strength, and good impact toughness. However, their disadvantages are poor thermal stability and low chemical inertness, making them suitable for cutting heat-resistant alloys, cast iron, and iron based sintered metals. The CBN particle content in composite PCBN cutting tools is relatively low, and ceramics are used as binders, resulting in lower hardness. However, this compensates for the poor thermal stability and low chemical inertness of PCBN with high CBN content, making it suitable for cutting hardened steel. In the application field of cutting gray cast iron and quenched steel, ceramic cutting tools and CBN cutting tools are available for simultaneous selection. When dry cutting hardened steel, the cost of using Al2O3 ceramics is lower than that of PCBN materials, because ceramic cutting tools have good thermal and chemical stability, but they are not as tough and hard as PCBN cutting tools. Ceramic cutting tools are a better choice when cutting workpieces with a hardness below 60HRC and small feed rates. PCBN cutting tools are suitable for situations where the workpiece hardness is higher than 60HRC, especially for automated and high-precision machining.
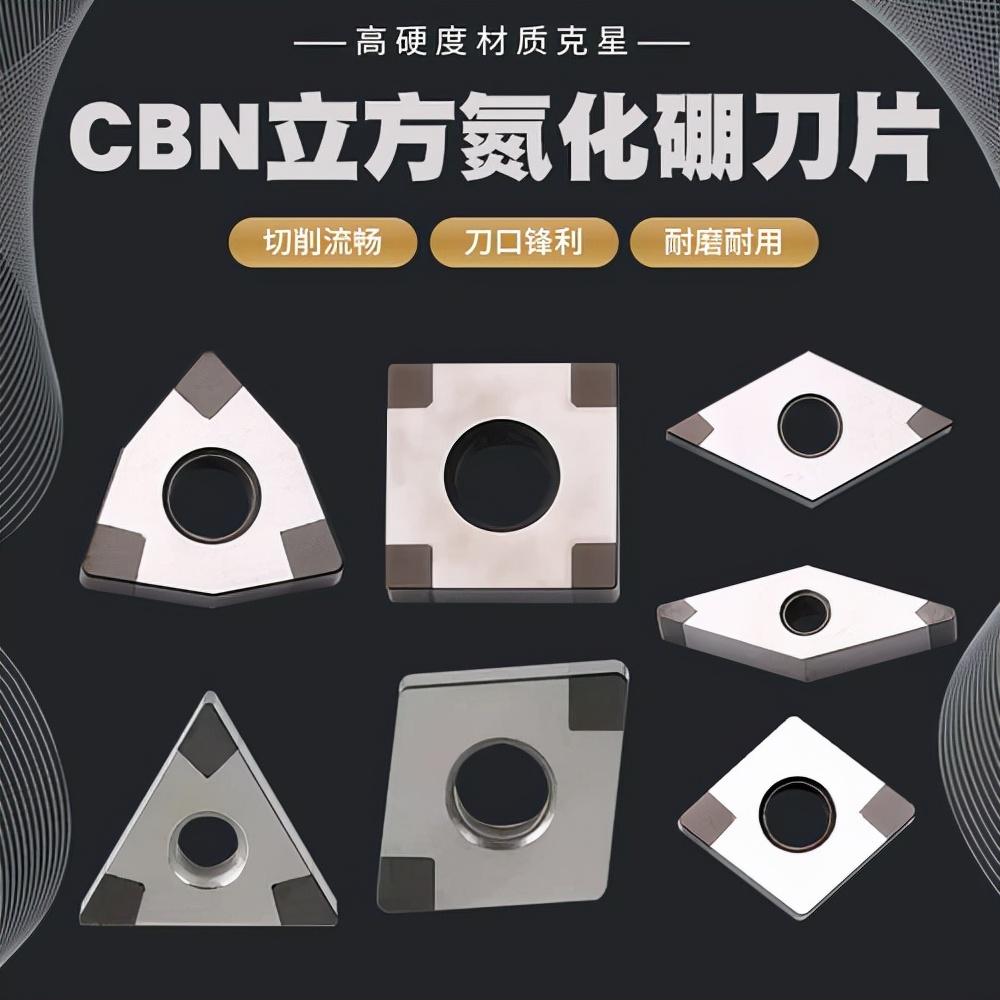
6. Polycrystalline Diamond (PCD)
As the hardest cutting tool material, PCD has a hardness of up to 10000HV and the best wear resistance. It can process soft non-ferrous metal materials with high speed (1000m/min) and precision. However, it is sensitive to impact, easy to break, and has a strong affinity for iron in ferrous metals, which can easily trigger chemical reactions. Generally, it can only be used to process non-ferrous parts, such as non-ferrous metals and their alloys, glass fibers, engineering ceramics, and hard alloys, which are extremely hard materials.
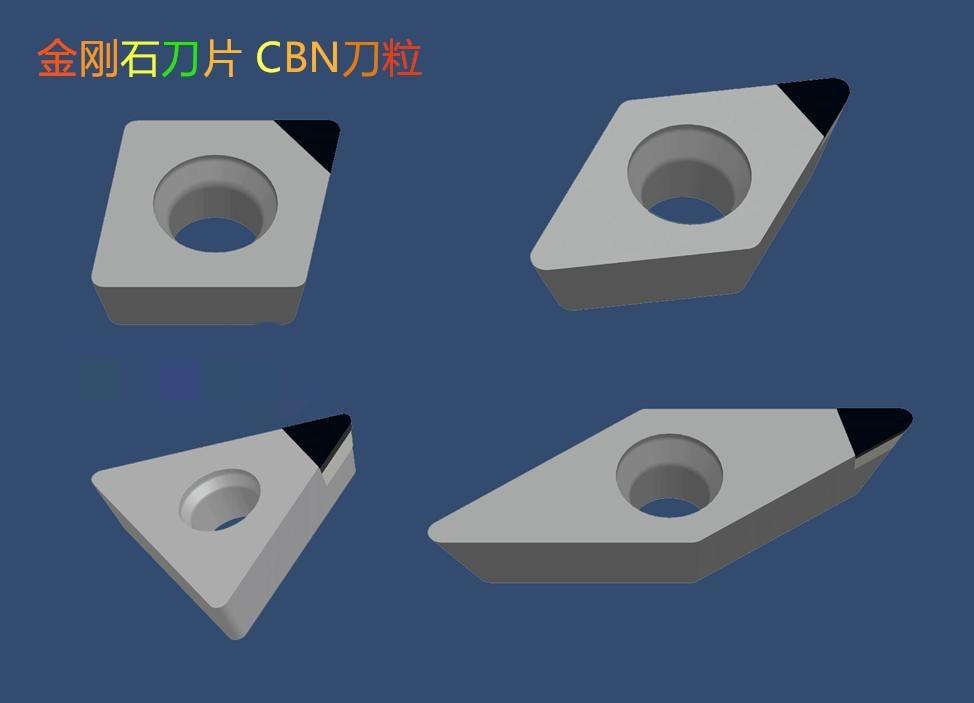