The quotation does not include transportation costs and profits (determined by the market based on MOQ), which are not included in the cost.
The profit value is adjusted based on MOQ:
MOQ< 5PCS Profit=Cost X60%
MOQ< 20PCS Profit=Cost X50%
MOQ< 100PCS Profit=Cost X40%
MOQ< 200PCS Profit=Cost X30%
200< MOQ< 500 Profit=Cost X25%
MOQ> 500PCS Profit=Cost X20%
Profit=(material cost+table processing fee+purchased parts fee+material loss fee+processing fee+transportation fee) X profit parameter
Profit parameter=depends on MOQ (20% -60%)
Final quotation of the product=material cost+surface processing fee+external procurement fee+loss fee+processing fee+transportation fee+profit
Plate material cost (steel plate, etc.)=part volume x specific gravity x unit price=length x width x plate thickness x density x loss rate x unit price
Note: (Density: Mass per unit volume, Specific gravity: Weight per unit volume.) Actually, it's basically the same, but later in 1984, the term weight was removed from the national unit of measurement, so specific gravity became a thing of the past. Nowadays, what we verbally call specific gravity is actually density.
Loss rate: Cabinet/rack=115% Chassis/rack=122% Box=130%
Actual material length of the profile=length of the profile on the drawing+10mm
Net weight=cross-sectional area of aluminum profile x actual material length (drawing profile length+10mm)/10x1000000 x quantity x density (2.75g/m ³)
Gross weight=net weight x loss coefficient (cabinet 115%, plug-in 122%, box module 130%)
Profile material cost=unit price x gross weight
Material loss cost=(material cost+surface processing fee+external parts cost) X0.03 (0.03 is the loss rate)
Actual material used for sheet metal parts=longer edge of the unfolded surface x shorter edge of the unfolded surface x loss coefficient
S loss coefficient formula=actual processing area/developed area of the part
1. When S< At 0.05m ², the loss coefficient is 1.38%
When 0.05m ²< The loss coefficient at S< 0.1m ² is 1.23%
3. When 0.1m ²< The loss coefficient at S< 0.25m ² is 1.17%
4. When 0.25m ²< The loss coefficient at S< 0.6m ² is 1.12%
5. When S> The loss coefficient at 0.6m ² is 1.06%
When MOQ< At 100PCS, the cost of preparing the computer bed equipment is required. Formula=(30-50) X Number of sheet metal parts/MOQ
Carton type (each box cannot exceed 20kg)
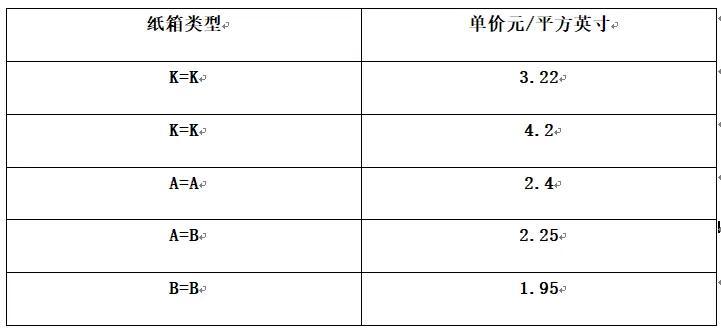
Carton algorithm: [(length+width+2) x (width+height+2)]/500x unit price, i.e. square inches/500x unit price
Paper/flat card algorithm: (length+1 inch flash) x (width+1 inch flash)/1000x unit price
Plastic bag algorithm: 0.08x length (m) x width (m) x 1.84x unit price (anti-static 16 yuan/kg, regular PE 15 yuan/kg)
Common wooden board specifications: 800X600X140, standard 5T vehicle can accommodate 36 wooden boards, and the height cannot exceed 1.5M
Specification of extended wooden board: 2000X800X140 (each board cannot exceed 400Kg)
Standard vehicle 5 tons=L9MxW2.4MxH2.5M (volume=54m ³)
Freight including tax=500/Total quantity loaded x 1.17
Total quantity of loading=(length of wooden board/length of cardboard box) x (width of wooden board/width of cardboard box) x (1500/height of cardboard box) Unit: mm
For example: Carton size: 9 (1/2) x9x7 (1/2) 2PCS per box
Length 9 (1/2) x 25.4=241.3 800/241.3.=3.319 (take integer)
Width 9x25.4=228.6 600/228.6=2.62 (taking whole numbers)
High 7 (1/2) x25.4=190.5 1500/190.5=7.87 (rounded to whole number)
Total number of loaded vehicles=3x2x7x2x36=3024
Card usage=freight including tax x 36/500 or=1/total number of cards per card
The assembly time should be reasonable, and below 2U, it cannot exceed 1.5 yuan
Screw assembly/riveting time: 1U=25S, 2U=35S, cabinet/rack/chassis=45S
The standard assembly time for cardboard boxes is 40 seconds
Processing costs for each section
Cutting=2 yuan/minute
Shuchong=3.35 yuan/minute
Laser=4.47 yuan/minute
Bending L< 600mm=0.36 yuan/knife L< 1200mm=0.55 yuan/knife L ≥ 1200mm=0.8 yuan/knife
Polishing/polishing=0.45 yuan/minute
Drilling/chamfering/sinking/tapping=0.08 yuan/hole
Wire drawing=19 yuan/M ² oxidation=20.5 yuan/M ²
Electric welding=0.97 yuan/minute (full welding 1cm=15S, spot welding one point=12S)
Calibration/machining=1 yuan/minute, collision welding=0.12 yuan/point
Seed mother/column=0.12 yuan/PCS
Artificial punching machine: 45T=0.13 yuan/time 60T=0.16 yuan/time 80T=0.2 yuan/time
110T=0.25 yuan/time 160T=0.29 yuan/time 200T=0.33 yuan/time
M250T=0.35 yuan/time, 400T oil pressure=0.49 yuan/time
Screen printing: 0.65 yuan/time
Assembly: 0.5 yuan/minute (locking screws 0.1 yuan/pcs, rivets 0.05 yuan/pcs, rivets 0.08 yuan/pcs)
Back glue=100 yuan/M ²
Spray coating: G127/G150=21.8 yuan/M ² G129/G107=20.1 yuan/²
G108=25.9 yuan/M ² G139=43.7 yuan/M ²
G133=44.4 yuan/m ²
Stainless steel passivation (G011)=5.98 yuan/kg
Nickel plating=8.12 yuan/kg
T001=6 yuan/M ²
G002=25.64 yuan/M ²
Tin plating=273.05 yuan/M ² Silver plating=99.27 yuan/M ²
All unit prices here do not include taxes
Calculation of tonnage of manual punching machine: P=TxCxMX1.3/1000 tons
T=material thickness C=punching perimeter M=shear strength 1.3=sum of unloading force+pushing force+top material force
Film 18 yuan/sheet (A4), film algorithm (not A4)=length x width x 0.08 minimum (20cm x 30cm) x 0.08=48 yuan
Standard working hour statistics table
Laser cutting hours (T=0.5-1.5)
The working hours for loading/unloading a single workpiece=1 minute/1. The number of pieces that can be cut from the entire piece of material
The number of pieces of the entire material=[2500 (our standard plate length/workpiece length)] x [1220 (our standard plate width/workpiece width)]
Laser cutting working hours (T=2.0-2.5)
Laser cutting hours=number of cutting holes x average cutting speed+cutting edge length x average cutting edge speed
The loading/unloading time for a single workpiece is 1.5 minutes per piece of material that can be cut
The number of pieces that can be cut from the entire piece of material=[2500 (effective length after removing excess material/length of workpiece)] x [1220 (effective width after removing excess material)/width of workpiece]
Relaxation rate:
1. Line changing is generally 5% (cutting a small number of workpieces)
The time required for X-axis movement is generally relaxed by 3% -5%
3. The time required for Y-axis movement is generally relaxed by 1% -3%
Laser (T3.0-3.5) as above
Laser (T4.0)
Cutting working hours=loading/unloading time+number of cutting holes x average cutting speed+cutting edge length x average cutting speed
The loading/unloading time for a single workpiece is 1.5 minutes per piece of material that can be cut
The number of pieces that can be cut from the entire piece of material=[2500 (effective length after removing excess material/length of workpiece)] x [1220 (effective width after removing excess material/width of workpiece)]
1. Cutting bed working hours=(material handling CT+cutting CT) x number of people=total CT time x number of people
2. The material handling operation takes 10 minutes (2 minutes to push the cart to the raw material warehouse+4 minutes to load the cart+4 minutes to push the loaded cart to the cutting bed), with a maximum of 20 pieces per cart. The formula is 10 minutes/the number of workpieces that can be cut per piece of material/the maximum number of materials per cart is 20 pieces
3. CT time=(homework time+homework time) x relaxation rate
4. Relaxation rate includes: 1. Physiological relaxation of 5% -10%, such as drinking water or using the toilet
2. Relax fatigue by 2% -8%, such as resting or waiting for work
3. Relax efforts by 1% -5%
Number of punching hours=loading and unloading time+punching time+tool changing time
Please note that there are no powders in stock or products with special color palettes in the quotation,
When the powder is not available, it will be distributed into the product at a rate of 100KG, with a unit price of 25 yuan/KG
About 2500 yuan will be allocated to MOQ as purchased parts
Special powder spraying algorithm=25 * 100/MOQ
Take similar sand and orange grain codes for manual codes in the quotation template
Mold cost allocation:
For example, in 20230328, if the demand for this code is 10000 sets and the mold cost is 10000, 50% of the order (i.e. 5000 sets) will be allocated to these 5000 sets. If the customer requests to allocate it to these 5000 sets, the mold cost allocated to the product will be 10000/5000=2 yuan. If it exceeds 5000 sets, the price will need to be lowered again (the mold cost is no longer included in the excess part)
MOQ< 3000, same mold processing cost, same CNC processing cost, minimum MOQ ≥ 2500
For example: Mold fee of 16000 yuan, MOQ=4000PCS
After sharing the cost of a single mold=16000/4000=4 yuan
The cost of purchasing external parts and processing according to the mold is 10 yuan
So the actual cost is 10+4=14 yuan
Actual market reported expenses to customers=cost x profit
When MOQ< 3000PCS customers do not agree to mold opening. If the CNC of the parts can meet the processing requirements, the mold will not be opened.