In the CNC Machining of threads, how to determine the cutting parameters of threads is probably chosen by many frontline operators based on experience. It is undeniable that practitioners can gradually explore and find cutting parameters that are in line with the actual production of enterprises through careful observation over time. However, for most practitioners, it is necessary to further master some empirical formulas of thread cutting in order to quickly grasp the precautions in thread cutting processing.
Think about it, in the entire CNC machining process, thread machining is the most complex and involves the most formulas. For example, what is the width of the slot cutting tool to be selected for the machining of the thread's cutting groove? How to calculate the major diameter, minor diameter, and pitch diameter in external threads? How many internal thread boreholes have been drilled? What is the spindle speed of the thread to be taken? How should left-hand and multi thread threads be machined? How many times is the thread fed, and what is the radial feed rate for each tool?
For some practitioners, they may be very familiar, but for beginners, do they find it complicated? Does it also exist that it is only processed based on the experience of the master teacher? The purpose of writing this article is for the latter. I will list and summarize the relevant knowledge points about ordinary triangular external threads in CNC machining.
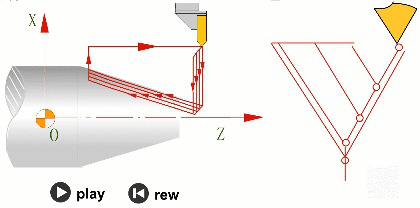
Thread processing
From the graph, it can be seen that the thread cutter has walked a total of 4 times, and the radial feed rate is gradually decreasing. How much does it decrease each time? If the thread cutter needs to run 3 times, 5 times, etc., how much radial feed should be taken for each run? This is an important topic for discussion today!
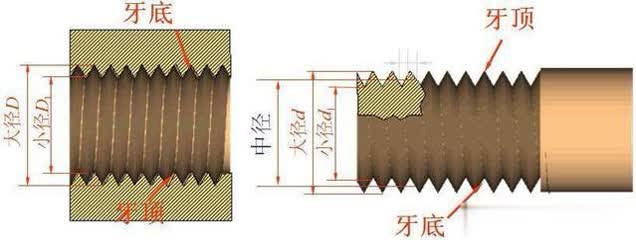
Basic parameters of threads
In actual machining, the outer diameter d of each actual cutting thread is different. For plastic materials, d=d-0.1p; minor diameter d2=d-2H=d-2X0.65 (0.54) P, where 0.65 represents the empirical coefficient; The maximum speed n of the threaded spindle is 1200, n1200/p-80, and 80 is the safety factor, which is also an empirical formula; The feed rate F is f=p for single thread and f=S for multiple threads. The above are the most basic, but I will focus on explaining the number of passes and feed rate for each thread.
In thread machining, when the feed rate is continuously decreasing, there is also a calculation formula for the feed rate of each cutting path, as follows
Ax represents the radial feed rate each time, n represents the number of tool passes, and j represents the number of tool passes per pass. The first pass is 0.3, followed by 1, 2, 3..., depending on the number of cuts completed.
For example, for external threads with a pitch of 1.5mm, a total thread depth ap of 0.94mm, and 6 tool passes, the feed rate for each pass is calculated as follows
First cutting: a1=0.94/50.3=0.23mm;
The second cutting: a2=0.94/51=0.42mm, with a feed rate of 0.42-0.23=0.19mm;
The third cutting: a3=0.94/52=0.59mm, with a feed rate of 0.59-0.42=0.17mm;
The fourth cutting: a4=0.94/53=0.73mm, with a feed rate of 0.73-0.59=0.14mm;
The fifth cutting: a5=0.94/54=0.84mm, with a feed rate of 0.84-0.73=0.11mm;
The sixth cutting: a6=0.94/55=0.94mm, with a feed rate of 0.94-0.84=0.10mm;
For professionals who frequently involve thread processing, it is recommended to master the above formulas.