Emma Technology Co., Ltd. is one of the leading professional manufacturers of precision metal parts in China, established in 2006. It mainly undertakes business such as CNC Machining parts, metal stamping parts, and sheet metal processing.
1. Stamping processing is a production technology that utilizes the power of conventional or specialized stamping equipment to directly subject the sheet metal to deformation forces and deformations in the mold, thereby obtaining product parts with a certain shape, size, and performance. Sheet metal, molds, and equipment are the three elements of stamping processing.
Stamping processing can be referred to as a process in sheet metal processing. For example, mass production of chimney elbows using scissors to cut each piece will result in low efficiency. If the sheet material is directly processed using a stamping die on a punching machine, the processing rate will be very high.
3. Sheet metal processing is the processing of metal plates. For example, using sheet metal to make chimneys, iron drums, oil tanks and kettles, ventilation pipes, elbow sizes, sky gardens, funnel-shaped structures, etc., the main processes include cutting, bending, edge fastening, bending forming, welding, riveting, etc.
According to the temperature during stamping, there are two methods: cold stamping and hot stamping. This depends on the strength, plasticity, thickness, degree of deformation, and equipment capability of the material, while considering its original heat treatment state and final usage conditions.
5. Sheet metal is a comprehensive cold working process for metal sheets (usually below 6 millimeters), including cutting, stamping/cutting/composite, folding, welding, riveting, splicing, forming (such as automotive body), etc. Its notable feature is that the thickness of the same part is consistent. Generally speaking, basic equipment includes shearing machines, CNC punching machines, plasma, water jet cutting machines, laminating machines, bending machines, and various auxiliary equipment, such as uncoilers, leveling machines, deburring machines, spot welding machines, etc.
Stamping processes can be roughly divided into two categories: separation processes and forming processes (divided into bending, deep drawing, and forming).
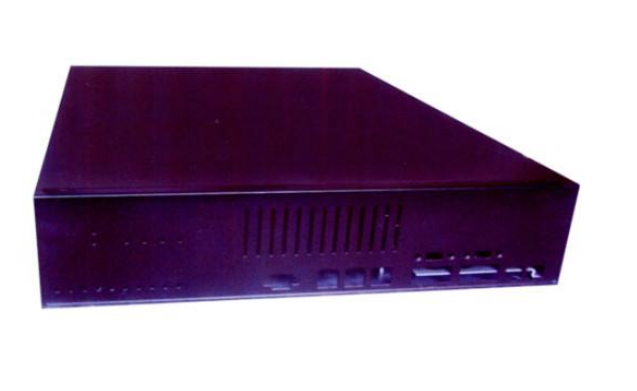