Alloy steel with a chromium content of over 12% or an nickel content of over 8% is commonly referred to as stainless steel. This type of steel has constant corrosion resistance in air or corrosive media, and exhibits high strength at high temperatures (> 450C).
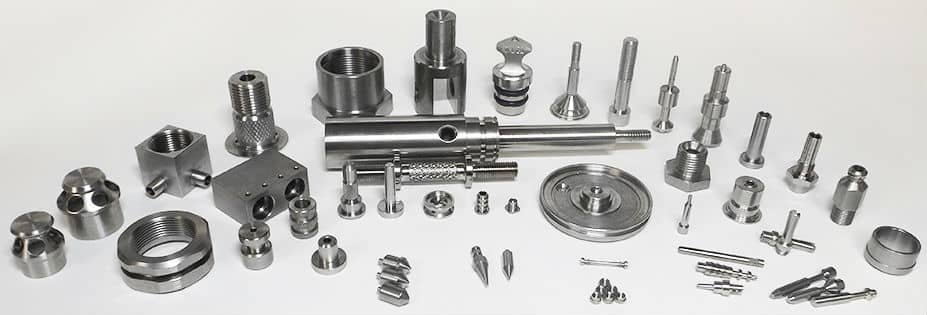
features
Stainless steel has characteristics such as corrosion resistance, scaling resistance, acid resistance, impact resistance, and toughness over a wide temperature range. Based on the environment, we can provide various grades and surface finishes, making these parts an ideal choice for many applications. Chromium in steel can form a rough, invisible, and corrosion-resistant chromium oxide film on the surface of the steel. If the material is mechanically or chemically damaged, the film will repair itself (assuming the presence of oxygen). In addition, its 100% recyclability provides a new way for stainless steel to be used as an environmentally friendly material. Therefore, it is widely used in heavy industry, light industry, daily necessities industry, and building decoration industry.
Stainless steel
Stainless steel is usually divided into five different categories. Each element is identified by alloy elements that affect its microstructure and named accordingly. It is austenite,
austenitic stainless steel
Austenitic stainless steel is the most commonly used type of stainless steel and is non-magnetic. The most common austenitic alloy is iron chromium nickel steel, commonly referred to as the 300 series. Mainly adding chromium (about 18% -30%) and nickel (about 6% -20%). Due to its high chromium and nickel content, austenitic stainless steel is the most corrosion-resistant among stainless steel groups. It has excellent mechanical properties because it can maintain strength even at high temperatures, is easy to maintain, and has good formability. They can be cold processed, but not heat treated. It is commonly used for manufacturing shafts, valves, bolts, bushings, nuts, aircraft accessories, brewing equipment, and low-temperature containers.
Low carbon level (L level)
"L" level is used to improve the corrosion resistance after welding. The letter "L" after the stainless steel grade indicates low-carbon (such as 304L). The carbon content should be kept below 0.03% to prevent carbide precipitation. Due to the temperature encountered during the welding process (which may cause carbon deposition), an "L" grade is usually used. Generally speaking, stainless steel rolling mills can provide dual certification for these stainless steel grades, such as 304/304L or 316/316L.
High carbon level (H-level)
The minimum carbon content of stainless steel grade "H" is 0.04%, and the maximum carbon content is 0.10%. Higher carbon helps maintain strength at extreme temperatures. The letter "H" after the stainless steel grade indicates these grades. When the final use involves extreme temperature environments, use this grade.
304 type
A commonly used (austenitic) stainless steel grade with a basic composition of 18/8 (18% chromium, 8% nickel) and a maximum carbon content of 0.07%, also known as A2 stainless steel.
It has excellent corrosion resistance, is easy to process, and has excellent formability after CNC Machining. The 304/304L model has excellent formability and excellent welding performance, making it an ideal choice for various household and commercial applications.
Due to its high chromium and nickel content, it is very suitable for manufacturing processing equipment used in the chemical (mild chemistry), food/dairy, and beverage industries.
309 type
The higher chromium and nickel content enhances corrosion resistance and high-temperature fouling resistance, making it suitable for high-temperature applications up to 1900F. Strong corrosion resistance. 309 can be cold processed, but not heat treated. It is weldable and relatively easy to process.
This alloy is commonly used for furnace components, thermocouple sleeves, boiler pipe hangers in power plants, generators, paper mills, refineries, brazing fixtures, bolts, refractory brackets, and furnace linings.
316 type
It is the second most widely used steel after 304, containing 16% to 18% chromium, 11% to 14% nickel, and at least 2% molybdenum. These combined can improve corrosion resistance. Especially, molybdenum is used to help control corrosion pitting. This level can withstand stains at temperatures up to 1600F.
Used in chemical processing, pulp and paper industry, food and beverage, surgical equipment, processing and distribution, and corrosive environments. It is also used in the marine industry because it is more resistant to chloride corrosion than 304. SS316 is commonly used in nuclear fuel recovery equipment. 18/10 grade stainless steel typically meets this application level.
317 type
If the molybdenum content is higher than 316, the molybdenum content of that grade should be higher than 3%. This alloy is weldable, easy to process, and can be processed both cold and hot. However, it cannot undergo heat treatment.
Commonly used in highly corrosive environments and in air pollution control scrubber systems. It is an ideal material for manufacturing generators, absorption towers, boilers, condenser tubes, heat exchanger tubes, pressure vessels, chimney fittings, and valves.
The 317L model limits the maximum carbon content to 0.030%. The silicon content can reach up to 0.75% to increase corrosion resistance.
321 type
The titanium content is at least five times higher than the carbon content. This is done to reduce or eliminate chromium carbide precipitation caused by welding or exposure to high temperatures.
Suitable for environments with temperatures up to 1500 degrees Fahrenheit. Easy to cause creep and fracture, with high resistance to elongation and vibration fatigue. Mainly used for manufacturing aircraft exhaust pipes and manifolds, jet engine parts, boiler casings, heaters, etc.
348 type
The combination of niobium and tantalum content with carbon helps to prevent chromium carbide precipitation during the welding process. It has excellent corrosion resistance when exposed to temperatures of 800-1500F.
Martensite
Martensitic stainless steel grades are a group of stainless steel alloys that are corrosion-resistant and hardenable (using heat treatment). The martensitic grade is pure chromium steel without nickel. They have magnetism, can be hardened by heat treatment, and are not as corrosion-resistant as austenitic stainless steel. Martensite grades are mainly used in areas where hardness, strength, and wear resistance are required.
It is commonly used to manufacture pump shafts, bolts and screws, valves, liners, rivets, coal cans, cutlery, jet engine parts, aircraft parts, mining equipment, rifle barrels, and fire extinguisher inserts. Common levels include 410, 414, 416, 420, 431, and 440.
410 type
The basic martensitic grade has the lowest alloy content among the three basic stainless steels (304, 430, and 410). Low cost, universal, heat-treatable stainless steel. Stainless steel 410 contains at least 1.5% chromium, making it particularly resistant to the erosion of many chemicals and acids. Widely used in areas with less severe corrosion (air, water, certain chemicals, food acids). The application of this product may include components that require a combination of strength and corrosion resistance, such as fasteners.
Compared with the 410 type, the carbon content of 410S is lower, making it easier to weld, but its hardenability is poor. 410S type is a universal corrosion-resistant and heat-resistant chromium steel, recommended for corrosion-resistant applications.
414 type
Add nickel (2%) to improve corrosion resistance. Applications include bolts and nuts, pressure plates, valve components, surgical instruments, and refineries. Typical applications include springs and tableware.
416 type
The added phosphorus and sulfur are special variants of 410, which can improve cutting performance and undergo heat treatment. Typical applications include threaded machine parts.
420 type
Add carbon to improve mechanical properties. It can be heat treated to a Brinell hardness of approximately 500 and has maximum corrosion resistance after complete hardening. Suitable for various precision machinery, bearings, appliances, equipment, measuring tools, instruments, transportation vehicles, household appliances, etc. Mainly used for manufacturing parts that are resistant to air, water vapor, water, and oxidative acid corrosion.
Type 431
The nickel content is 1.252%, and the chromium content increases. The corrosion resistance and mechanical properties are high, and the corrosion resistance is better than 410 and 430 steel. It has the highest corrosion resistance in hardenable martensitic stainless steel. It undergoes hot or cold work and hardens to 40HRC. Typical applications include valves, pumps, aircraft components, propeller shafts, and ship equipment.
440 type
There are three common models of 440 stainless steel B: 440A, 440B, 440C, and 440F (more suitable for machine types). Further increasing the content of chromium and carbon can improve the toughness and corrosion resistance of this type. The hardness can reach 58HRC, making it one of the hardest stainless steels. Typical applications include surgical instruments such as surgical knives, scissors, nozzles, and bearings.
Ferrite
Like martensitic steel, ferritic stainless steel is a pure chromium steel without nickel, which has corrosion resistance and oxidation resistance, while still resisting stress and cracking. These steels have magnetism, but cannot be hardened through heat treatment. They are cold processed and can be softened through annealing. They have higher corrosion resistance than martensitic grades, but are usually not as good as austenitic grades. Commonly used for decorative strips, sinks, and certain automotive applications, such as exhaust systems. Common levels include 405, 409, 430, 434, 436, 442, and 446.
405 type
Contains 12% chromium with added aluminum. After cooling from high temperature, this chemical composition helps prevent hardening. Very suitable for welding applications. Advanced shape, easy to process. Typical applications include heat exchangers, turbine materials, hardened parts, etc.
409 type
The content of chromium is 11%, which is the lowest in all stainless steels. This is the least amount of passivation surface facial mask that forms the corrosion resistance of stainless steel. It is one of the cheapest stainless steel grades.
This type can only be used for internal or external parts in non severely corrosive environments. Typical applications include silencers.
409 alloy has better corrosion resistance than carbon steel and can be used as a substitute for carbon steel in less corrosive environments. Due to its high corrosion resistance and high-temperature oxidation resistance, it has advantages.
430 type
430 stainless steel is a general-purpose steel with excellent corrosion resistance. It has better thermal conductivity than austenite, smaller coefficient of thermal expansion than austenite, resistance to thermal fatigue, added stable element titanium, and excellent mechanical properties in welds. 430 stainless steel is used for building decoration, fuel burner parts, appliances, and appliance parts.
430F is a type of steel that adds easy cutting performance to 430 steel. Mainly used for automatic lathes, bolts, and nuts. Adding Ti or Nb to 430 steel for 430LX to reduce C content and improve treatment and welding performance. Mainly used in hot water tanks, water supply systems, bathroom appliances, durable household appliances, bicycle flywheels, etc.
Type 434
It contains 12% to 30% chromium and molybdenum is added to improve corrosion resistance. Its corrosion resistance, toughness, and weldability increase with the increase of chromium content, and its ability to resist chloride stress corrosion is superior to other types of stainless steel. 434 is an improved grade of 430 steel, which is more salt resistant than 430 steel and is commonly used in automotive decorative parts and fasteners.
Type 436
436 stainless steel is an improved steel grade of 434. Niobium has been added to this brand to improve corrosion resistance and heat resistance. Can be used for deep drawing parts, gas burners, dishwashers, range hoods, steam irons, frying pans, etc.
442 type
Due to its high chromium content, excellent heat resistance and scale resistance, it has excellent corrosion resistance. However, due to the inability to heat treat, it is difficult to process. Applications include furnaces and combustion components, zinc die-casting machines, nitrogen fixation components, and nitric acid storage tanks.
Type 446
High chromium content (27%) can further improve corrosion resistance and oxidation resistance at high temperatures. The combustion chamber is resistant to high temperature and corrosion, and has no peeling oxide skin below 1082 ℃.
Precipitation hardening (PH) grade
Like martensite, precipitation hardened stainless steel can also be strengthened and hardened through heat treatment. Its strength, hardness, and corrosion resistance are superior to martensitic chromium stainless steel. It is usually stronger and at higher temperatures than austenitic stainless steel. It can retain most of its power. Commonly referred to as PH stainless steel, both contain high chromium content and are used in the manufacturing of military equipment and aerospace structural components. Common levels include 17-7PH PH15-7Mo、17-4PH、15-5PH。
Type 17-7
After solid solution treatment, 17-7PH stainless steel forms an unstable austenite structure with good ductility and processability. After quenching and tempering, the composition of austenite precipitates and carbides changes. After martensitic transformation treatment, most of the microstructure transforms into a more ductile low-carbon tempered martensite. This state is the usage state of steel, which has good mechanical properties at moderate temperatures. The corrosion resistance of 17-7PH is better than that of ordinary martensitic stainless steel.
PH15-7 molybdenum
This is a steel grade developed using 2% molybdenum instead of 2% chromium in 0Cr17Ni7Al steel. The basic performance is similar to 17-7PH steel, but the overall performance is better. In its austenitic state, it can withstand various cold forming and welding processes. After heat treatment, achieve the highest strength. Excellent high-temperature strength below 550 ℃. Used for manufacturing aircraft thin-walled structural components, various containers, pipelines, springs, valve membranes, ship shafts, compressor discs, reactor parts, various chemical equipment and other structural components.
Type 17-4
Alloy 17-4 is a chromium copper precipitation hardened stainless steel with excellent oxidation resistance and corrosion resistance. Heat treatment can optimize mechanical properties such as strength, ductility, and oxidation resistance. This brand can undergo heat treatment at various temperatures. Generate a wide range of finished product characteristics. This level should not be used at temperatures above 300C or very low.
Type 15-5
This is a variant of the older 17-4 chromium nickel copper precipitation hardened martensitic stainless steel. The toughness of 15-5 alloy is higher than that of 17-4. Compared to other similar martensitic stainless steels, it is used for applications that require better corrosion resistance and lateral performance.
Dual phase (ferrite austenite) grade
Dual phase stainless steel is a modern stainless steel that combines austenite and ferrite materials. Known for its extremely high strength and resistance to stress corrosion cracking. The strength of these grades is approximately twice that of austenitic and ferritic grades. It has better toughness and ductility than ferritic steel, but it cannot reach the level of austenitic steel. Heat treatment is easy, but cold forming is difficult. It is usually used to manufacture chemical processing equipment, pressure vessels, and heat exchanger components.
Duplex stainless steel is divided into four categories:
The first type is a low alloy steel representing the UNSS32304 (23Cr-4Ni-0.1N) grade, which does not contain molybdenum and has a PREN value of 24-25. It can replace AISI304 or 316 in terms of stress corrosion resistance.
The second type is medium alloy type, represented by the grade UNSS31803 (22Cr-5Ni-3Mo-0.15N), with a PREN value of 32-33, and corrosion resistance between AISI316L and 6% Mo+N austenitic stainless steel.
The third type is high alloy type, which generally contains 25% Cr, as well as molybdenum and nitrogen, and some also contain copper and tungsten. The standard grade is UNSS32550 (25Cr-6Ni-3Mo-2Cu-0.2N), with a PREN value of 38-39. The corrosion resistance of this type of steel is higher than that of 22% Cr duplex stainless steel.
The fourth type belongs to the super duplex stainless steel type with high molybdenum and high nitrogen content, standard grade UNSS32750 (25Cr-7Ni-3.7Mo-0.3N), and some also contain tungsten and copper. Under harsh moderate conditions, the PREN value exceeds 40, exhibiting excellent corrosion resistance and overall mechanical properties comparable to super austenitic stainless steel.
Processing characteristics
In the long-term practice of processing stainless steel parts, SANS has concluded that stainless steel has the following characteristics in the CNC cutting process.
Severe work hardening:
Stainless steel has high plasticity, and its performance undergoes distortion during plastic deformation, resulting in a high strengthening coefficient. However, austenite is not stable enough, and under the action of cutting stress, some austenite transforms into martensite. Due to the effect of composite cutting heat, impurities are easily decomposed and dispersed, forming a hardened layer during the cutting process. The work hardening caused by the previous feed or process can seriously affect the smooth progress of the next process.
High cutting force:
Stainless steel undergoes significant plastic deformation and cutting resistance during the cutting process. Stainless steel has a high degree of work hardening and thermal strength, resulting in greater cutting resistance and less susceptibility to chip curling and fracture.
High cutting temperature:
During cutting, plastic deformation and high friction with the cutting tool generate a large amount of cutting heat. A large amount of cutting heat is concentrated in the cutting area and the interface between the tool and the chip, resulting in poor heat dissipation.
Chips are prone to breakage and cannot be assembled.
Stainless steel has good plasticity and toughness. During CNC machining, the chips are continuous, which not only affects the smooth operation but also crushes the machining surface. Stainless steel has a high affinity with other metals under high temperature and pressure, which can easily adhere and form tumors. This not only exacerbates tool wear, but also tears and damages the machining surface.
Tools are prone to wear and tear.
The affinity during stainless steel cutting causes the bonding and diffusion between the tool and the blade, resulting in tool bonding wear and diffusion wear, thereby forming crescent shaped crescent pits on the front cutting surface of the tool. Formed. In addition to the cutting edge, the hardness of stainless steel carbide particles (such as TiC) is very high. During the cutting process, direct contact and friction with the cutting tool can cause tool scratches and increase tool wear due to work hardening.
High coefficient of linear expansion:
The coefficient of linear expansion of stainless steel is about 1.5 times that of carbon steel. Under the influence of cutting temperature, the workpiece is prone to thermal deformation and dimensional accuracy is difficult to control.
Due to its unique properties, stainless steel is increasingly used in industries such as power, aviation, aerospace, petroleum, and food. The characteristics of stainless steel cutting are high thermal strength, large plastic deformation, severe work hardening, excessive cutting heat, and difficulty in heat dissipation. We can ensure the quality of processing. And handling methods.
Advantages of stainless steel machined parts
Stainless steel parts have excellent corrosion resistance even when buried underground due to the thin and dense chromium rich oxide film on the surface of stainless steel. They have excellent corrosion resistance in all water quality, including soft water.
Stainless steel can be safely used for a long time at temperatures ranging from -270 ℃ to 400 ℃, with no harmful substances precipitated at high or low temperatures, and its material properties are very stable.
Stainless steel material is safe, non-toxic, non corrosive, non leaching, non odorous, and non turbid, and does not cause secondary pollution to water quality. Maintain pure and hygienic water quality, and ensure adequate hygiene and safety.
Stainless steel has the characteristics of corrosion resistance, increased strength, less deformation and fracture of steel, environmental protection, less rusting, good ductility and toughness. Suitable for harsh environments (indoor and outdoor environments such as humidity, acidity, and alkalinity).
Application of stainless steel machined parts
1. Medical industry
There are too many stainless steel needles, stainless steel surgical knives, stainless steel wheelchairs, stainless steel infusion frames, and stainless steel medical forceps. It may be essential every day, especially in orthopedic use.
The excellent comprehensive performance, more mature manufacturing process, and lower price of stainless steel make its application in the medical field increasingly widespread. The application of stainless steel in the medical field has become a major development trend.
2. Electronics and Home Furnishings Industry
The properties of stainless steel make it widely used in other electronic fields. For example, today's water heaters are made of surgical stainless steel, and the heating pipes of coffee machines are made of stainless steel. There are others, but you may know them in your daily life.
3. The automotive industry
The penetration rate of stainless steel in the automotive industry is almost the highest. The automotive industry is currently the fastest-growing application area for stainless steel. Today, the most important manufacturing material for automobiles is basically stainless steel. Mainly used for vehicle body, exhaust system, fuel tank, frame, stainless steel parts, and automotive decoration. Due to the high demand for stainless steel in automobiles, the automotive industry is basically one of the main forces driving the development of stainless steel.
Stainless steel can also be used in some high-end mechanical fields, such as food industry, chemical industry, medical equipment, aircraft exhaust pipes, etc. Stainless steel is widely used in industries such as heavy industry, light industry, daily necessities industry, and building decoration.