The cost composition of stamping parts is generally divided into the following parts: 1 Material cost 2 Standard parts cost 3 Process processing fee 4 Packaging fee 5 Transportation fee 6. Management fee 7 profit
Let's take a closer look at the composition of these expenses below
Analysis of cost composition of stamping parts
1、 Material costs
Material cost refers to the net material cost according to the drawing requirements=material volume * material density * material unit price.
2、 Standard parts cost
The standard component cost required by the drawing.
3、 Process processing fee
The processing cost required for each process of processing into a product. The composition of each process is detailed in the Cost Accounting Format and the Cost Composition Table for Each Process. Here are the main process cost components for explanation:
1. CNC material dropping
Its cost composition=equipment depreciation and amortization+labor cost+auxiliary materials
Equipment depreciation and amortization:
Equipment depreciation is calculated on a 5-year basis, with 12 months per year, 22 days per month, and 8 hours per day.
For example, for a device worth 2 million yuan, the hourly equipment depreciation is 200 * 10000/5/12/22/8=189.4 yuan/hour
Labor cost:
Each CNC requires 3 technicians to operate, and the average monthly salary for each technician is 1800 yuan. They work 22 days a month and 8 hours a day, which means the hourly cost is 1800 * 3/22/8=31 yuan/hour
Auxiliary material cost:
Refers to auxiliary production materials such as lubricants and volatile liquids required for equipment operation. Each equipment costs approximately 1000 yuan per month, calculated based on 22 days per month and 8 hours per day. The hourly cost is 1000/22/8=5.68 yuan/hour
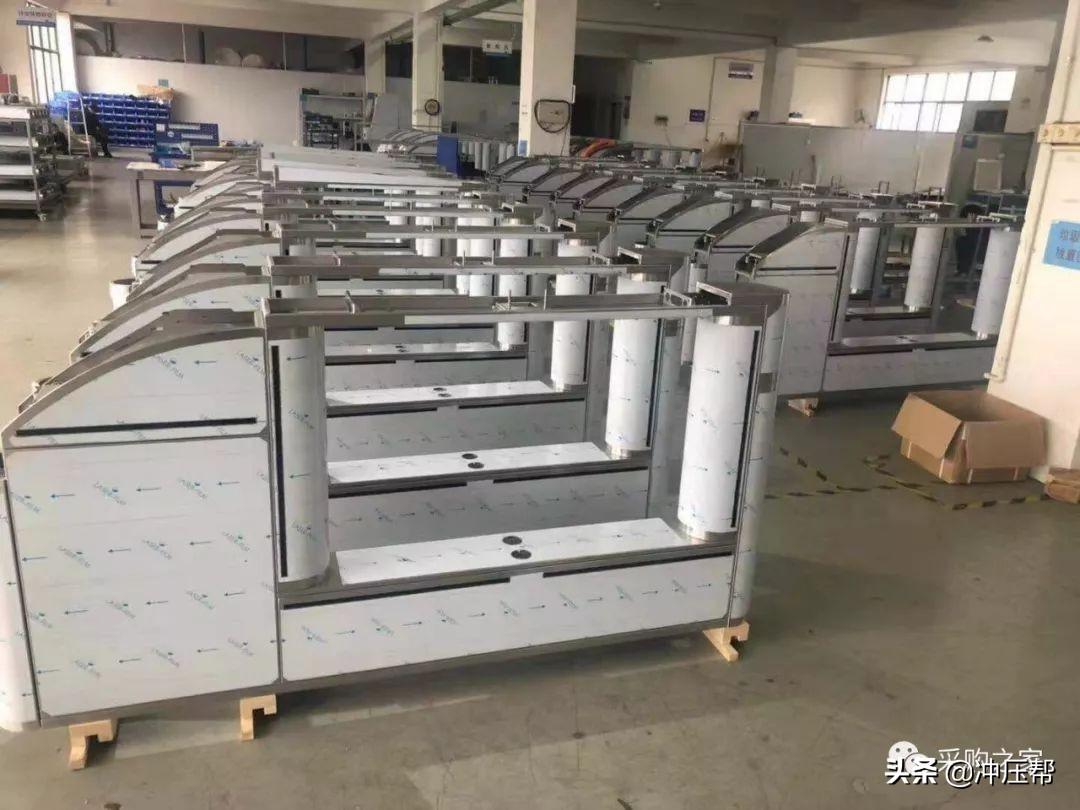
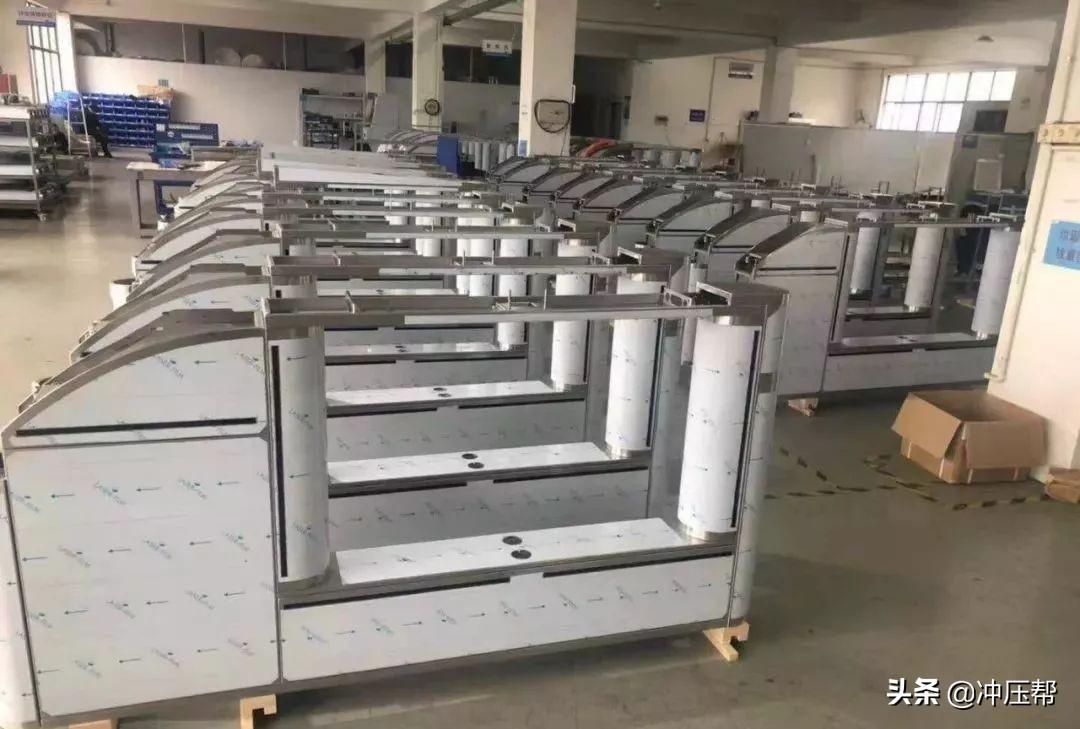
2. Bending
Its cost composition=equipment depreciation and amortization+labor cost+auxiliary materials
Equipment depreciation and amortization:
Equipment depreciation is calculated on a 5-year basis, with 12 months per year, 22 days per month, and 8 hours per day.
For example, for equipment worth 500000 yuan, the depreciation per minute is 50 * 10000/5/12/22/8/60=0.79 yuan/minute
It usually takes 10 to 100 seconds to make a bend, so the depreciation of each bending equipment is 0.13-1.3 yuan per bend.
Labor cost:
Each device requires one technician to operate, with an average monthly salary of 1800 yuan. Each technician works 22 days a month and 8 hours a day, which means the cost per minute is 1800/22/8/60=0.17 yuan/minute. On average, 1-2 bends can be made per minute. Therefore, the labor cost per bend is 0.08-0.17 yuan/track
Auxiliary material cost:
The cost of auxiliary materials used for each bending machine per month is 600 yuan. Based on 22 days per month and 8 hours per day, the hourly cost is 600/22/8/60=0.06 yuan/track
3. Surface treatment
Outsourced based on purchase price (such as electroplating, oxidation)
Composition of spraying costs:
Spray coating cost=powder material cost+labor cost+auxiliary material cost+equipment depreciation
Powder material cost: The calculation method is generally based on square meters, and the price per kilogram of powder ranges from 25 to 60 yuan (mainly related to customer requirements). Generally, 4-5 square meters can be sprayed per kilogram of powder.
Powder material cost=6-15 yuan/square meter
Labor cost: There are a total of 15 people on the spraying line, each person is charged 1200 yuan/month, with 22 days per month and 8 hours per day. Each hour can spray 30 square meters.
Labor cost=15 * 1200/22/8/30=3.4 yuan/square meter
Auxiliary material cost: mainly refers to the fuel cost used for pre-treatment liquid and curing furnace, which is 50000 yuan per month. It is 22 days per month, 8 hours per day, and 30 square meters per hour.
Auxiliary material cost=9.47 yuan/square meter
Equipment depreciation: The spraying line has an investment of 1 million yuan and is depreciated for 5 years. It operates in December each year, 22 days a month, 8 hours a day, and sprays 30 square meters per hour.
Equipment depreciation cost=100 * 10000/5/12/22/8/30=3.16 yuan/square meter
Total spraying cost=22-32 yuan/square meter
If partial protection spraying is required, the cost will be higher.
4、 Packaging fee
According to different products, packaging requirements and prices vary, usually ranging from 20 to 30 yuan/cubic meter.
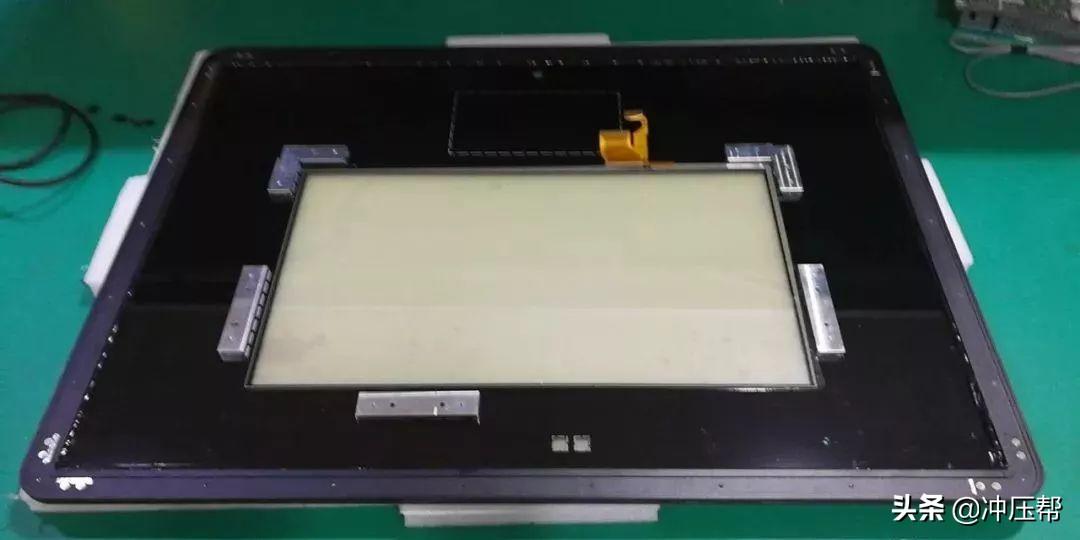
5、 Transportation management fee
The transportation cost is amortized into the product.
6、 Management expenses
There are two parts to management expenses: factory rent, water and electricity, and financial expenses
Factory rental water and electricity:
The monthly rental water and electricity cost is 150000 yuan, and the monthly output value is calculated at 4 million yuan. The proportion of rental water and electricity to the output value is 15/400=3.75%
Financial expenses:
Due to mismatched accounts receivable and payable cycles (we purchase materials in cash and customers settle 60 days per month), we need to hold down funds for at least 3 months at a bank interest rate of 1.25-1.5%.
Therefore, management expenses should account for about 5% of the total sales price.
7、 Profit
Considering the long-term development of the company and better customer service, set a reasonable profit point, such as 10% -15%.
The above 7 points are the main costs that constitute the product and are for reference only.
Calculation method for stamping quotation
The manufacturing price of sheet metal is calculated based on the operating time:
Laser cutting for 8RMB/Min, calculated at 1RMB per small hole
CNC pricing of 5RMB/Min
CNC bending pricing is 1 RMB per side, double for the larger side
Cold work welding calculation is 70RMB per day, with 50KG per working day as the benchmark
The above calculation methods require a high level of comprehensive quality and a strong understanding of industry trends, but they are difficult to operate.
The following sheet metal calculations are empirical formulas that do not consider manufacturing processes:
Material price=unfolded weight of material dropped x market material price
Processing fee calculation: without considering process, tax, management fees, and shipping costs
Benchmark calculation: 3200RMB/T cold-rolled steel plate t=2.0 1804-m Grade 7 IT7
Cold work processing cost: 8.0-8.4RMB/KG, with workers producing 50KG or more per work.
Cold work includes the following: grinding wheel machine cutting, old style shearing machines, old style bending machines, flame piercing, old welding, and outsourcing prices ranging from 7.2 to 7.5 RMB/KG.
The above processing coefficient base is set to 1.

The outsourcing costs for CNC cutting, CNC punching, CNC bending, and CO2 shielded welding are calculated with a coefficient of 2.5-3.5, and the coefficients are taken into account based on the number of processes and complexity.
Laser cutting is twice the impact:
When the board is not equal to 2, the processing cost is calculated as equal to 2
When the plate size is less than 1.2, the processing cost is multiplied by 2.5 to 3.5
When the market price of materials fluctuates, the processing cost base remains unchanged.
If the sheet metal production is fully assembled without welding, the counting coefficient is multiplied by 0.75 to 0.85, usually taking the larger value;
When the tolerance level is increased to 1804-f, the counting coefficient is multiplied by 1.5-2;
For batch deburring and blunting, multiply the counting coefficient by 1.1 to 1.5;
The surface spray price is 20-30 RMB/m2;
The price for surface three degree paint processing is 15-20RMB/m2;
For those with special requirements and difficulties in manufacturing and processing, it is necessary to consider the yield and multiply the yield coefficient;
The above pricing is the standard pricing, which means that if the scrap rate is within 3%, the profit is approximately 28% to 35%. After deducting taxes, the profit is around 18% to 23%. If there is a requirement for profit, the corresponding multiplication coefficient should not be less than 1.75 when pricing.
The cost composition of stamping parts is generally divided into the following parts: 1 Material cost 2 Standard parts cost 3 Process processing fee 4 Packaging fee 5 Transportation fee 6. Management fee 7 profit
Let's take a closer look at the composition of these expenses below
Analysis of cost composition of stamping parts
1、 Material costs
Material cost refers to the net material cost according to the drawing requirements=material volume * material density * material unit price.
2、 Standard parts cost
The standard component cost required by the drawing.
3、 Process processing fee
The processing cost required for each process of processing into a product. The composition of each process is detailed in the Cost Accounting Format and the Cost Composition Table for Each Process. Here are the main process cost components for explanation:
1. CNC material dropping
Its cost composition=equipment depreciation and amortization+labor cost+auxiliary materials
Equipment depreciation and amortization:
Equipment depreciation is calculated on a 5-year basis, with 12 months per year, 22 days per month, and 8 hours per day.
For example, for a device worth 2 million yuan, the hourly equipment depreciation is 200 * 10000/5/12/22/8=189.4 yuan/hour
Labor cost:
Each CNC requires 3 technicians to operate, and the average monthly salary for each technician is 1800 yuan. They work 22 days a month and 8 hours a day, which means the hourly cost is 1800 * 3/22/8=31 yuan/hour
Auxiliary material cost:
Refers to auxiliary production materials such as lubricants and volatile liquids required for equipment operation. Each equipment costs approximately 1000 yuan per month, calculated based on 22 days per month and 8 hours per day. The hourly cost is 1000/22/8=5.68 yuan/hour
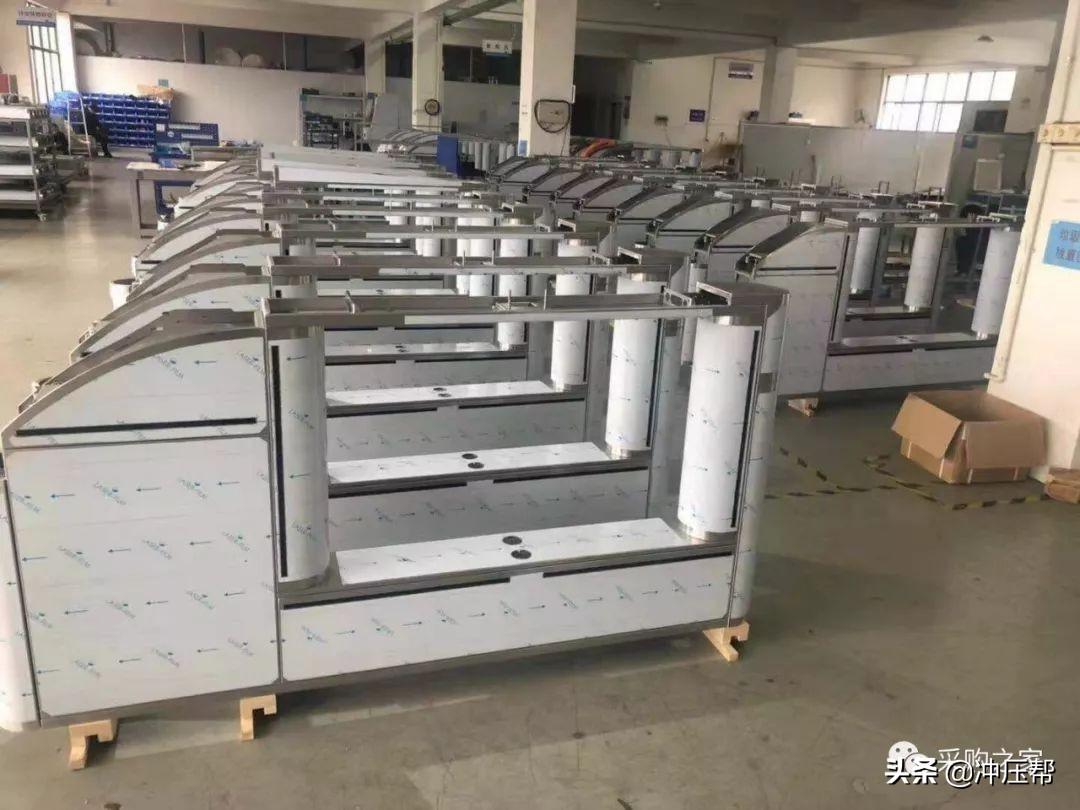
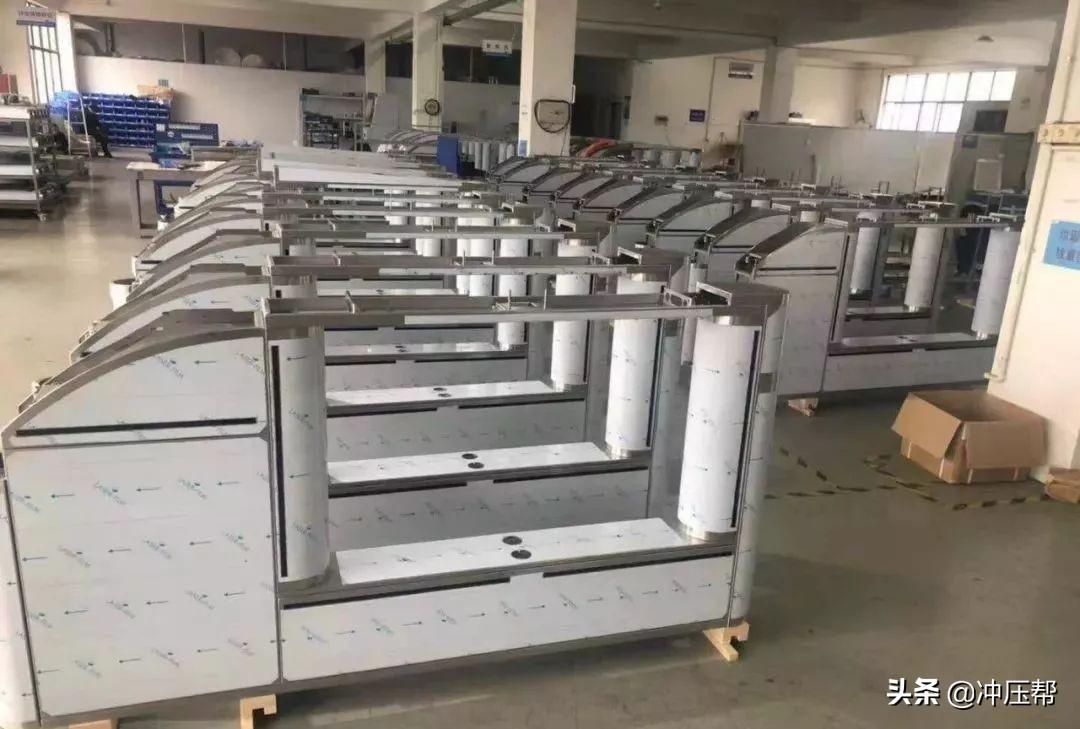
2. Bending
Its cost composition=equipment depreciation and amortization+labor cost+auxiliary materials
Equipment depreciation and amortization:
Equipment depreciation is calculated on a 5-year basis, with 12 months per year, 22 days per month, and 8 hours per day.
For example, for equipment worth 500000 yuan, the depreciation per minute is 50 * 10000/5/12/22/8/60=0.79 yuan/minute
It usually takes 10 to 100 seconds to make a bend, so the depreciation of each bending equipment is 0.13-1.3 yuan per bend.
Labor cost:
Each device requires one technician to operate, with an average monthly salary of 1800 yuan. Each technician works 22 days a month and 8 hours a day, which means the cost per minute is 1800/22/8/60=0.17 yuan/minute. On average, 1-2 bends can be made per minute. Therefore, the labor cost per bend is 0.08-0.17 yuan/track
Auxiliary material cost:
The cost of auxiliary materials used for each bending machine per month is 600 yuan. Based on 22 days per month and 8 hours per day, the hourly cost is 600/22/8/60=0.06 yuan/track
3. Surface treatment
Outsourced based on purchase price (such as electroplating, oxidation)
Composition of spraying costs:
Spray coating cost=powder material cost+labor cost+auxiliary material cost+equipment depreciation
Powder material cost: The calculation method is generally based on square meters, and the price per kilogram of powder ranges from 25 to 60 yuan (mainly related to customer requirements). Generally, 4-5 square meters can be sprayed per kilogram of powder.
Powder material cost=6-15 yuan/square meter
Labor cost: There are a total of 15 people on the spraying line, each person is charged 1200 yuan/month, with 22 days per month and 8 hours per day. Each hour can spray 30 square meters.
Labor cost=15 * 1200/22/8/30=3.4 yuan/square meter
Auxiliary material cost: mainly refers to the fuel cost used for pre-treatment liquid and curing furnace, which is 50000 yuan per month. It is 22 days per month, 8 hours per day, and 30 square meters per hour.
Auxiliary material cost=9.47 yuan/square meter
Equipment depreciation: The spraying line has an investment of 1 million yuan and is depreciated for 5 years. It operates in December each year, 22 days a month, 8 hours a day, and sprays 30 square meters per hour.
Equipment depreciation cost=100 * 10000/5/12/22/8/30=3.16 yuan/square meter
Total spraying cost=22-32 yuan/square meter
If partial protection spraying is required, the cost will be higher.
4、 Packaging fee
According to different products, packaging requirements and prices vary, usually ranging from 20 to 30 yuan/cubic meter.
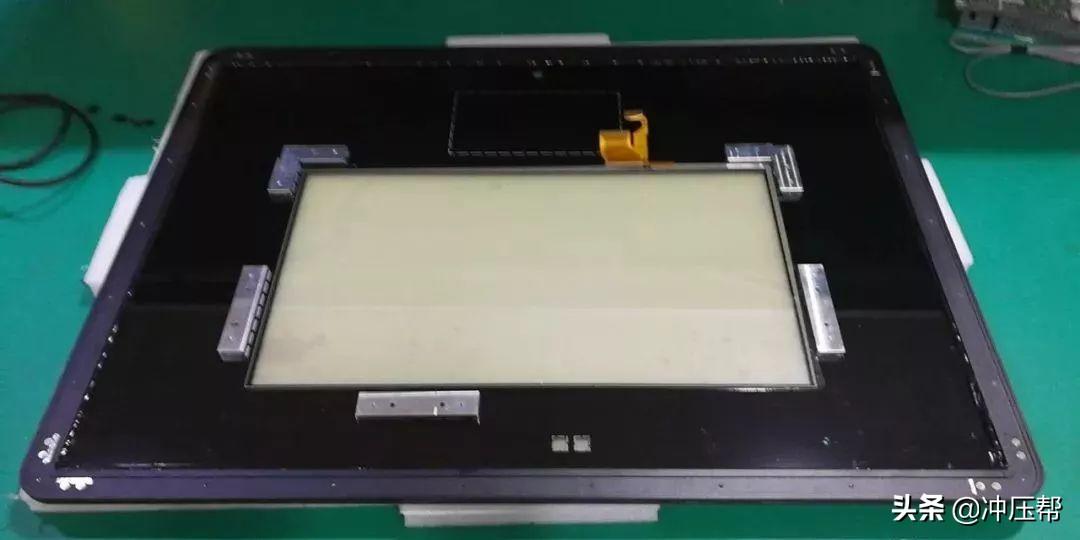
5、 Transportation management fee
The transportation cost is amortized into the product.
6、 Management expenses
There are two parts to management expenses: factory rent, water and electricity, and financial expenses
Factory rental water and electricity:
The monthly rental water and electricity cost is 150000 yuan, and the monthly output value is calculated at 4 million yuan. The proportion of rental water and electricity to the output value is 15/400=3.75%
Financial expenses:
Due to mismatched accounts receivable and payable cycles (we purchase materials in cash and customers settle 60 days per month), we need to hold down funds for at least 3 months at a bank interest rate of 1.25-1.5%.
Therefore, management expenses should account for about 5% of the total sales price.
7、 Profit
Considering the long-term development of the company and better customer service, set a reasonable profit point, such as 10% -15%.
The above 7 points are the main costs that constitute the product and are for reference only.
Calculation method for stamping quotation
The manufacturing price of sheet metal is calculated based on the operating time:
Laser cutting for 8RMB/Min, calculated at 1RMB per small hole
CNC pricing of 5RMB/Min
CNC bending pricing is 1 RMB per side, double for the larger side
Cold work welding calculation is 70RMB per day, with 50KG per working day as the benchmark
The above calculation methods require a high level of comprehensive quality and a strong understanding of industry trends, but they are difficult to operate.
The following sheet metal calculations are empirical formulas that do not consider manufacturing processes:
Material price=unfolded weight of material dropped x market material price
Processing fee calculation: without considering process, tax, management fees, and shipping costs
Benchmark calculation: 3200RMB/T cold-rolled steel plate t=2.0 1804-m Grade 7 IT7
Cold work processing cost: 8.0-8.4RMB/KG, with workers producing 50KG or more per work.
Cold work includes the following: grinding wheel machine cutting, old style shearing machines, old style bending machines, flame piercing, old welding, and outsourcing prices ranging from 7.2 to 7.5 RMB/KG.
The above processing coefficient base is set to 1.

The outsourcing costs for CNC cutting, CNC punching, CNC bending, and CO2 shielded welding are calculated with a coefficient of 2.5-3.5, and the coefficients are taken into account based on the number of processes and complexity.
Laser cutting is twice the impact:
When the board is not equal to 2, the processing cost is calculated as equal to 2
When the plate size is less than 1.2, the processing cost is multiplied by 2.5 to 3.5
When the market price of materials fluctuates, the processing cost base remains unchanged.
If the sheet metal production is fully assembled without welding, the counting coefficient is multiplied by 0.75 to 0.85, usually taking the larger value;
When the tolerance level is increased to 1804-f, the counting coefficient is multiplied by 1.5-2;
For batch deburring and blunting, multiply the counting coefficient by 1.1 to 1.5;
The surface spray price is 20-30 RMB/m2;
The price for surface three degree paint processing is 15-20RMB/m2;
For those with special requirements and difficulties in manufacturing and processing, it is necessary to consider the yield and multiply the yield coefficient;
The above pricing is the standard pricing, which means that if the scrap rate is within 3%, the profit is approximately 28% to 35%. After deducting taxes, the profit is around 18% to 23%. If there is a requirement for profit, the corresponding multiplication coefficient should not be less than 1.75 when pricing.
The cost composition of stamping parts is generally divided into the following parts: 1 Material cost 2 Standard parts cost 3 Process processing fee 4 Packaging fee 5 Transportation fee 6. Management fee 7 profit
Let's take a closer look at the composition of these expenses below
Analysis of cost composition of stamping parts
1、 Material costs
Material cost refers to the net material cost according to the drawing requirements=material volume * material density * material unit price.
2、 Standard parts cost
The standard component cost required by the drawing.
3、 Process processing fee
The processing cost required for each process of processing into a product. The composition of each process is detailed in the Cost Accounting Format and the Cost Composition Table for Each Process. Here are the main process cost components for explanation:
1. CNC material dropping
Its cost composition=equipment depreciation and amortization+labor cost+auxiliary materials
Equipment depreciation and amortization:
Equipment depreciation is calculated on a 5-year basis, with 12 months per year, 22 days per month, and 8 hours per day.
For example, for a device worth 2 million yuan, the hourly equipment depreciation is 200 * 10000/5/12/22/8=189.4 yuan/hour
Labor cost:
Each CNC requires 3 technicians to operate, and the average monthly salary for each technician is 1800 yuan. They work 22 days a month and 8 hours a day, which means the hourly cost is 1800 * 3/22/8=31 yuan/hour
Auxiliary material cost:
Refers to auxiliary production materials such as lubricants and volatile liquids required for equipment operation. Each equipment costs approximately 1000 yuan per month, calculated based on 22 days per month and 8 hours per day. The hourly cost is 1000/22/8=5.68 yuan/hour
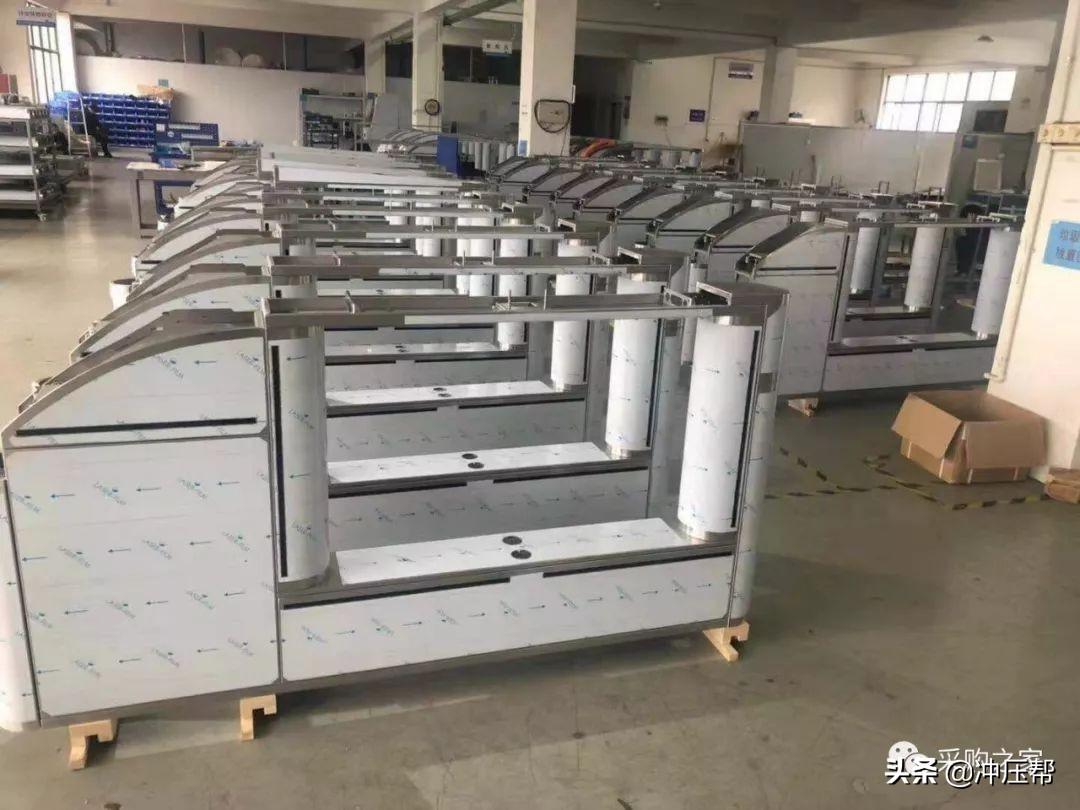
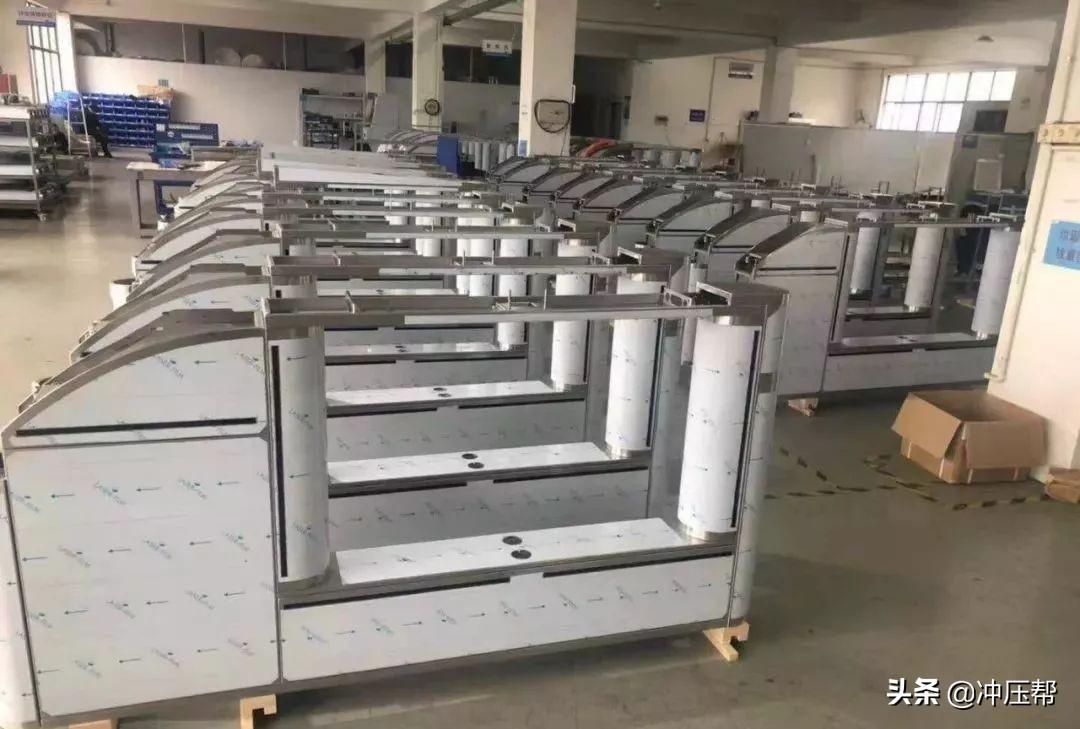
2. Bending
Its cost composition=equipment depreciation and amortization+labor cost+auxiliary materials
Equipment depreciation and amortization:
Equipment depreciation is calculated on a 5-year basis, with 12 months per year, 22 days per month, and 8 hours per day.
For example, for equipment worth 500000 yuan, the depreciation per minute is 50 * 10000/5/12/22/8/60=0.79 yuan/minute
It usually takes 10 to 100 seconds to make a bend, so the depreciation of each bending equipment is 0.13-1.3 yuan per bend.
Labor cost:
Each device requires one technician to operate, with an average monthly salary of 1800 yuan. Each technician works 22 days a month and 8 hours a day, which means the cost per minute is 1800/22/8/60=0.17 yuan/minute. On average, 1-2 bends can be made per minute. Therefore, the labor cost per bend is 0.08-0.17 yuan/track
Auxiliary material cost:
The cost of auxiliary materials used for each bending machine per month is 600 yuan. Based on 22 days per month and 8 hours per day, the hourly cost is 600/22/8/60=0.06 yuan/track
3. Surface treatment
Outsourced based on purchase price (such as electroplating, oxidation)
Composition of spraying costs:
Spray coating cost=powder material cost+labor cost+auxiliary material cost+equipment depreciation
Powder material cost: The calculation method is generally based on square meters, and the price per kilogram of powder ranges from 25 to 60 yuan (mainly related to customer requirements). Generally, 4-5 square meters can be sprayed per kilogram of powder.
Powder material cost=6-15 yuan/square meter
Labor cost: There are a total of 15 people on the spraying line, each person is charged 1200 yuan/month, with 22 days per month and 8 hours per day. Each hour can spray 30 square meters.
Labor cost=15 * 1200/22/8/30=3.4 yuan/square meter
Auxiliary material cost: mainly refers to the fuel cost used for pre-treatment liquid and curing furnace, which is 50000 yuan per month. It is 22 days per month, 8 hours per day, and 30 square meters per hour.
Auxiliary material cost=9.47 yuan/square meter
Equipment depreciation: The spraying line has an investment of 1 million yuan and is depreciated for 5 years. It operates in December each year, 22 days a month, 8 hours a day, and sprays 30 square meters per hour.
Equipment depreciation cost=100 * 10000/5/12/22/8/30=3.16 yuan/square meter
Total spraying cost=22-32 yuan/square meter
If partial protection spraying is required, the cost will be higher.
4、 Packaging fee
According to different products, packaging requirements and prices vary, usually ranging from 20 to 30 yuan/cubic meter.
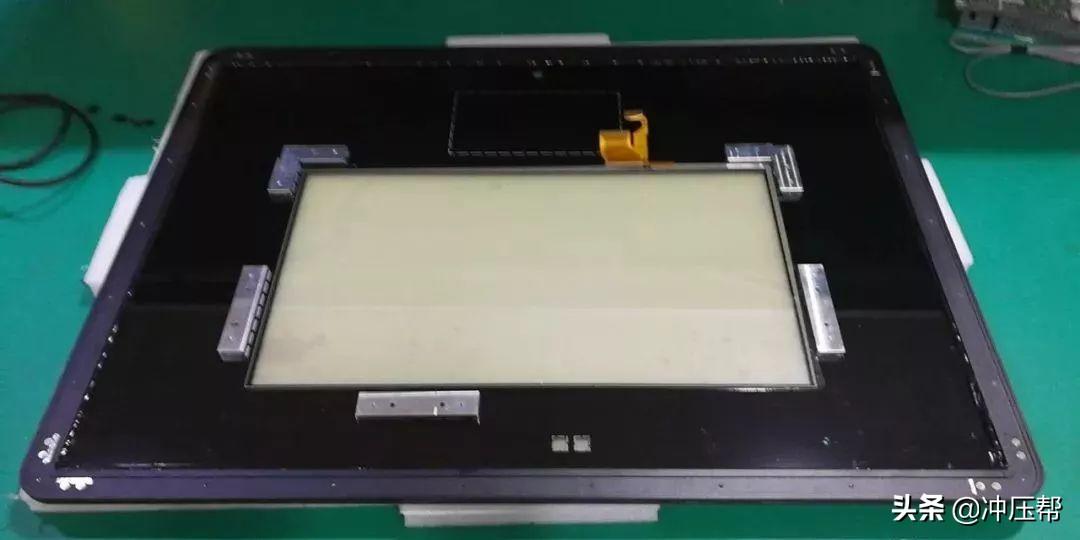
5、 Transportation management fee
The transportation cost is amortized into the product.
6、 Management expenses
There are two parts to management expenses: factory rent, water and electricity, and financial expenses
Factory rental water and electricity:
The monthly rental water and electricity cost is 150000 yuan, and the monthly output value is calculated at 4 million yuan. The proportion of rental water and electricity to the output value is 15/400=3.75%
Financial expenses:
Due to mismatched accounts receivable and payable cycles (we purchase materials in cash and customers settle 60 days per month), we need to hold down funds for at least 3 months at a bank interest rate of 1.25-1.5%.
Therefore, management expenses should account for about 5% of the total sales price.
7、 Profit
Considering the long-term development of the company and better customer service, set a reasonable profit point, such as 10% -15%.
The above 7 points are the main costs that constitute the product and are for reference only.
Calculation method for stamping quotation
The manufacturing price of sheet metal is calculated based on the operating time:
Laser cutting for 8RMB/Min, calculated at 1RMB per small hole
CNC pricing of 5RMB/Min
CNC bending pricing is 1 RMB per side, double for the larger side
Cold work welding calculation is 70RMB per day, with 50KG per working day as the benchmark
The above calculation methods require a high level of comprehensive quality and a strong understanding of industry trends, but they are difficult to operate.
The following sheet metal calculations are empirical formulas that do not consider manufacturing processes:
Material price=unfolded weight of material dropped x market material price
Processing fee calculation: without considering process, tax, management fees, and shipping costs
Benchmark calculation: 3200RMB/T cold-rolled steel plate t=2.0 1804-m Grade 7 IT7
Cold work processing cost: 8.0-8.4RMB/KG, with workers producing 50KG or more per work.
Cold work includes the following: grinding wheel machine cutting, old style shearing machines, old style bending machines, flame piercing, old welding, and outsourcing prices ranging from 7.2 to 7.5 RMB/KG.
The above processing coefficient base is set to 1.

The outsourcing costs for CNC cutting, CNC punching, CNC bending, and CO2 shielded welding are calculated with a coefficient of 2.5-3.5, and the coefficients are taken into account based on the number of processes and complexity.
Laser cutting is twice the impact:
When the board is not equal to 2, the processing cost is calculated as equal to 2
When the plate size is less than 1.2, the processing cost is multiplied by 2.5 to 3.5
When the market price of materials fluctuates, the processing cost base remains unchanged.
If the sheet metal production is fully assembled without welding, the counting coefficient is multiplied by 0.75 to 0.85, usually taking the larger value;
When the tolerance level is increased to 1804-f, the counting coefficient is multiplied by 1.5-2;
For batch deburring and blunting, multiply the counting coefficient by 1.1 to 1.5;
The surface spray price is 20-30 RMB/m2;
The price for surface three degree paint processing is 15-20RMB/m2;
For those with special requirements and difficulties in manufacturing and processing, it is necessary to consider the yield and multiply the yield coefficient;
The above pricing is the standard pricing, which means that if the scrap rate is within 3%, the profit is approximately 28% to 35%. After deducting taxes, the profit is around 18% to 23%. If there is a requirement for profit, the corresponding multiplication coefficient should not be less than 1.75 when pricing.
The cost composition of stamping parts is generally divided into the following parts: 1 Material cost 2 Standard parts cost 3 Process processing fee 4 Packaging fee 5 Transportation fee 6. Management fee 7 profit
Let's take a closer look at the composition of these expenses below
Analysis of cost composition of stamping parts
1、 Material costs
Material cost refers to the net material cost according to the drawing requirements=material volume * material density * material unit price.
2、 Standard parts cost
The standard component cost required by the drawing.
3、 Process processing fee
The processing cost required for each process of processing into a product. The composition of each process is detailed in the Cost Accounting Format and the Cost Composition Table for Each Process. Here are the main process cost components for explanation:
1. CNC material dropping
Its cost composition=equipment depreciation and amortization+labor cost+auxiliary materials
Equipment depreciation and amortization:
Equipment depreciation is calculated on a 5-year basis, with 12 months per year, 22 days per month, and 8 hours per day.
For example, for a device worth 2 million yuan, the hourly equipment depreciation is 200 * 10000/5/12/22/8=189.4 yuan/hour
Labor cost:
Each CNC requires 3 technicians to operate, and the average monthly salary for each technician is 1800 yuan. They work 22 days a month and 8 hours a day, which means the hourly cost is 1800 * 3/22/8=31 yuan/hour
Auxiliary material cost:
Refers to auxiliary production materials such as lubricants and volatile liquids required for equipment operation. Each equipment costs approximately 1000 yuan per month, calculated based on 22 days per month and 8 hours per day. The hourly cost is 1000/22/8=5.68 yuan/hour
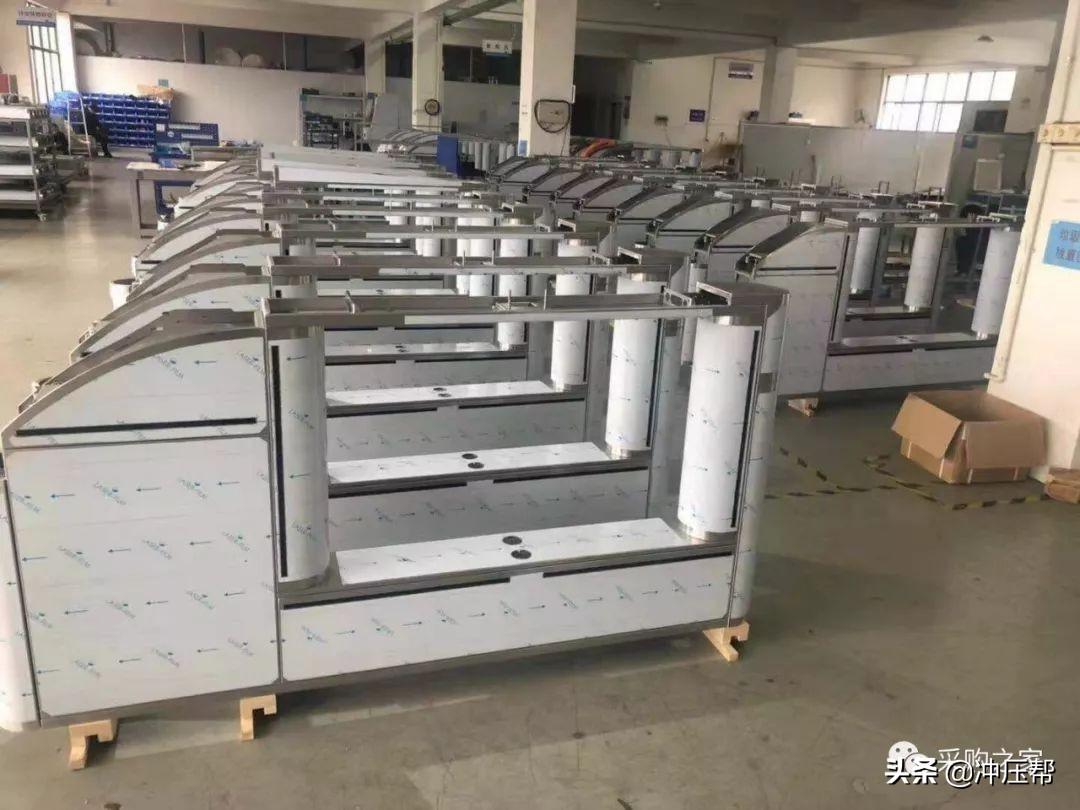
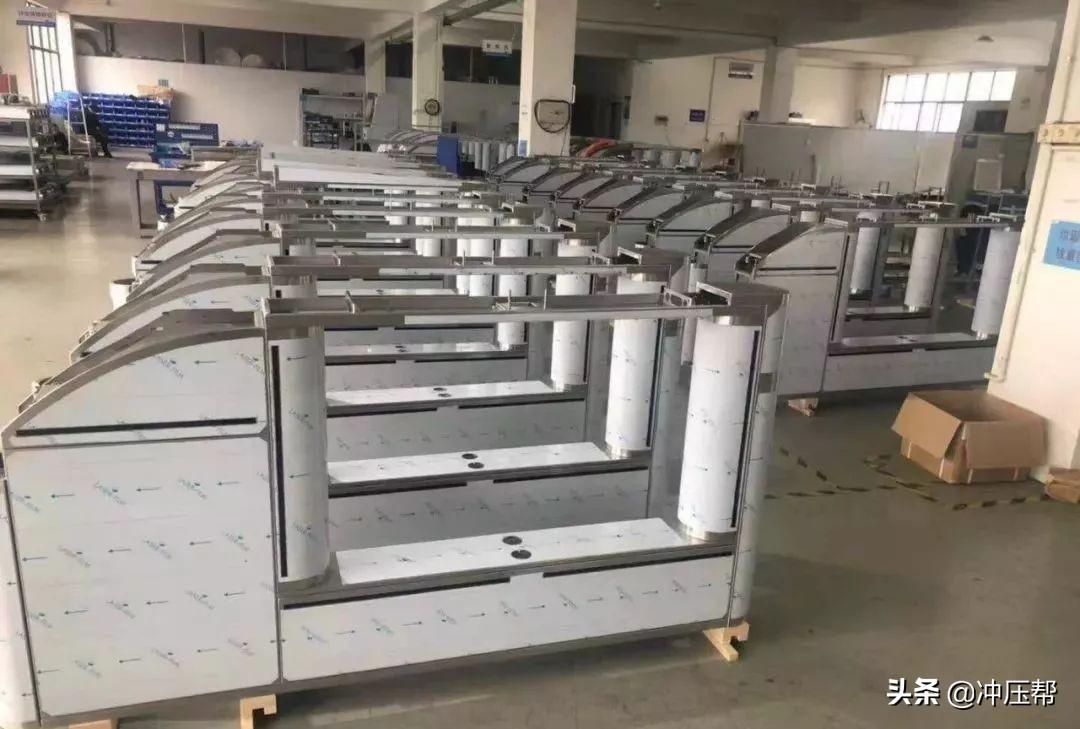
2. Bending
Its cost composition=equipment depreciation and amortization+labor cost+auxiliary materials
Equipment depreciation and amortization:
Equipment depreciation is calculated on a 5-year basis, with 12 months per year, 22 days per month, and 8 hours per day.
For example, for equipment worth 500000 yuan, the depreciation per minute is 50 * 10000/5/12/22/8/60=0.79 yuan/minute
It usually takes 10 to 100 seconds to make a bend, so the depreciation of each bending equipment is 0.13-1.3 yuan per bend.
Labor cost:
Each device requires one technician to operate, with an average monthly salary of 1800 yuan. Each technician works 22 days a month and 8 hours a day, which means the cost per minute is 1800/22/8/60=0.17 yuan/minute. On average, 1-2 bends can be made per minute. Therefore, the labor cost per bend is 0.08-0.17 yuan/track
Auxiliary material cost:
The cost of auxiliary materials used for each bending machine per month is 600 yuan. Based on 22 days per month and 8 hours per day, the hourly cost is 600/22/8/60=0.06 yuan/track
3. Surface treatment
Outsourced based on purchase price (such as electroplating, oxidation)
Composition of spraying costs:
Spray coating cost=powder material cost+labor cost+auxiliary material cost+equipment depreciation
Powder material cost: The calculation method is generally based on square meters, and the price per kilogram of powder ranges from 25 to 60 yuan (mainly related to customer requirements). Generally, 4-5 square meters can be sprayed per kilogram of powder.
Powder material cost=6-15 yuan/square meter
Labor cost: There are a total of 15 people on the spraying line, each person is charged 1200 yuan/month, with 22 days per month and 8 hours per day. Each hour can spray 30 square meters.
Labor cost=15 * 1200/22/8/30=3.4 yuan/square meter
Auxiliary material cost: mainly refers to the fuel cost used for pre-treatment liquid and curing furnace, which is 50000 yuan per month. It is 22 days per month, 8 hours per day, and 30 square meters per hour.
Auxiliary material cost=9.47 yuan/square meter
Equipment depreciation: The spraying line has an investment of 1 million yuan and is depreciated for 5 years. It operates in December each year, 22 days a month, 8 hours a day, and sprays 30 square meters per hour.
Equipment depreciation cost=100 * 10000/5/12/22/8/30=3.16 yuan/square meter
Total spraying cost=22-32 yuan/square meter
If partial protection spraying is required, the cost will be higher.
4、 Packaging fee
According to different products, packaging requirements and prices vary, usually ranging from 20 to 30 yuan/cubic meter.
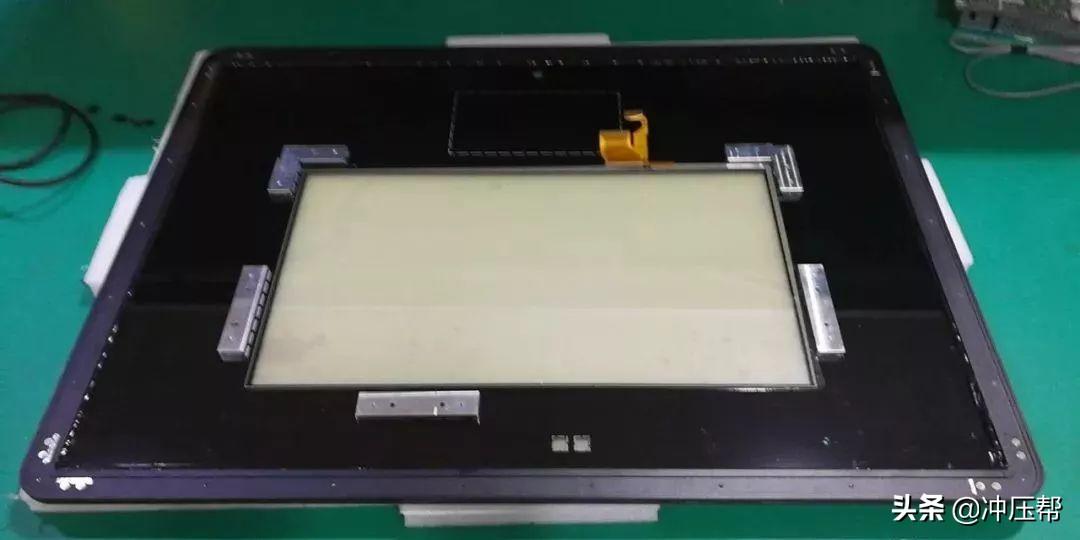
5、 Transportation management fee
The transportation cost is amortized into the product.
6、 Management expenses
There are two parts to management expenses: factory rent, water and electricity, and financial expenses
Factory rental water and electricity:
The monthly rental water and electricity cost is 150000 yuan, and the monthly output value is calculated at 4 million yuan. The proportion of rental water and electricity to the output value is 15/400=3.75%
Financial expenses:
Due to mismatched accounts receivable and payable cycles (we purchase materials in cash and customers settle 60 days per month), we need to hold down funds for at least 3 months at a bank interest rate of 1.25-1.5%.
Therefore, management expenses should account for about 5% of the total sales price.
7、 Profit
Considering the long-term development of the company and better customer service, set a reasonable profit point, such as 10% -15%.
The above 7 points are the main costs that constitute the product and are for reference only.
Calculation method for stamping quotation
The manufacturing price of sheet metal is calculated based on the operating time:
Laser cutting for 8RMB/Min, calculated at 1RMB per small hole
CNC pricing of 5RMB/Min
CNC bending pricing is 1 RMB per side, double for the larger side
Cold work welding calculation is 70RMB per day, with 50KG per working day as the benchmark
The above calculation methods require a high level of comprehensive quality and a strong understanding of industry trends, but they are difficult to operate.
The following sheet metal calculations are empirical formulas that do not consider manufacturing processes:
Material price=unfolded weight of material dropped x market material price
Processing fee calculation: without considering process, tax, management fees, and shipping costs
Benchmark calculation: 3200RMB/T cold-rolled steel plate t=2.0 1804-m Grade 7 IT7
Cold work processing cost: 8.0-8.4RMB/KG, with workers producing 50KG or more per work.
Cold work includes the following: grinding wheel machine cutting, old style shearing machines, old style bending machines, flame piercing, old welding, and outsourcing prices ranging from 7.2 to 7.5 RMB/KG.
The above processing coefficient base is set to 1.

The outsourcing costs for CNC cutting, CNC punching, CNC bending, and CO2 shielded welding are calculated with a coefficient of 2.5-3.5, and the coefficients are taken into account based on the number of processes and complexity.
Laser cutting is twice the impact:
When the board is not equal to 2, the processing cost is calculated as equal to 2
When the plate size is less than 1.2, the processing cost is multiplied by 2.5 to 3.5
When the market price of materials fluctuates, the processing cost base remains unchanged.
If the sheet metal production is fully assembled without welding, the counting coefficient is multiplied by 0.75 to 0.85, usually taking the larger value;
When the tolerance level is increased to 1804-f, the counting coefficient is multiplied by 1.5-2;
For batch deburring and blunting, multiply the counting coefficient by 1.1 to 1.5;
The surface spray price is 20-30 RMB/m2;
The price for surface three degree paint processing is 15-20RMB/m2;
For those with special requirements and difficulties in manufacturing and processing, it is necessary to consider the yield and multiply the yield coefficient;
The above pricing is the standard pricing, which means that if the scrap rate is within 3%, the profit is approximately 28% to 35%. After deducting taxes, the profit is around 18% to 23%. If there is a requirement for profit, the corresponding multiplication coefficient should not be less than 1.75 when pricing.
The cost composition of stamping parts is generally divided into the following parts: 1 Material cost 2 Standard parts cost 3 Process processing fee 4 Packaging fee 5 Transportation fee 6. Management fee 7 profit
Let's take a closer look at the composition of these expenses below
Analysis of cost composition of stamping parts
1、 Material costs
Material cost refers to the net material cost according to the drawing requirements=material volume * material density * material unit price.
2、 Standard parts cost
The standard component cost required by the drawing.
3、 Process processing fee
The processing cost required for each process of processing into a product. The composition of each process is detailed in the Cost Accounting Format and the Cost Composition Table for Each Process. Here are the main process cost components for explanation:
1. CNC material dropping
Its cost composition=equipment depreciation and amortization+labor cost+auxiliary materials
Equipment depreciation and amortization:
Equipment depreciation is calculated on a 5-year basis, with 12 months per year, 22 days per month, and 8 hours per day.
For example, for a device worth 2 million yuan, the hourly equipment depreciation is 200 * 10000/5/12/22/8=189.4 yuan/hour
Labor cost:
Each CNC requires 3 technicians to operate, and the average monthly salary for each technician is 1800 yuan. They work 22 days a month and 8 hours a day, which means the hourly cost is 1800 * 3/22/8=31 yuan/hour
Auxiliary material cost:
Refers to auxiliary production materials such as lubricants and volatile liquids required for equipment operation. Each equipment costs approximately 1000 yuan per month, calculated based on 22 days per month and 8 hours per day. The hourly cost is 1000/22/8=5.68 yuan/hour
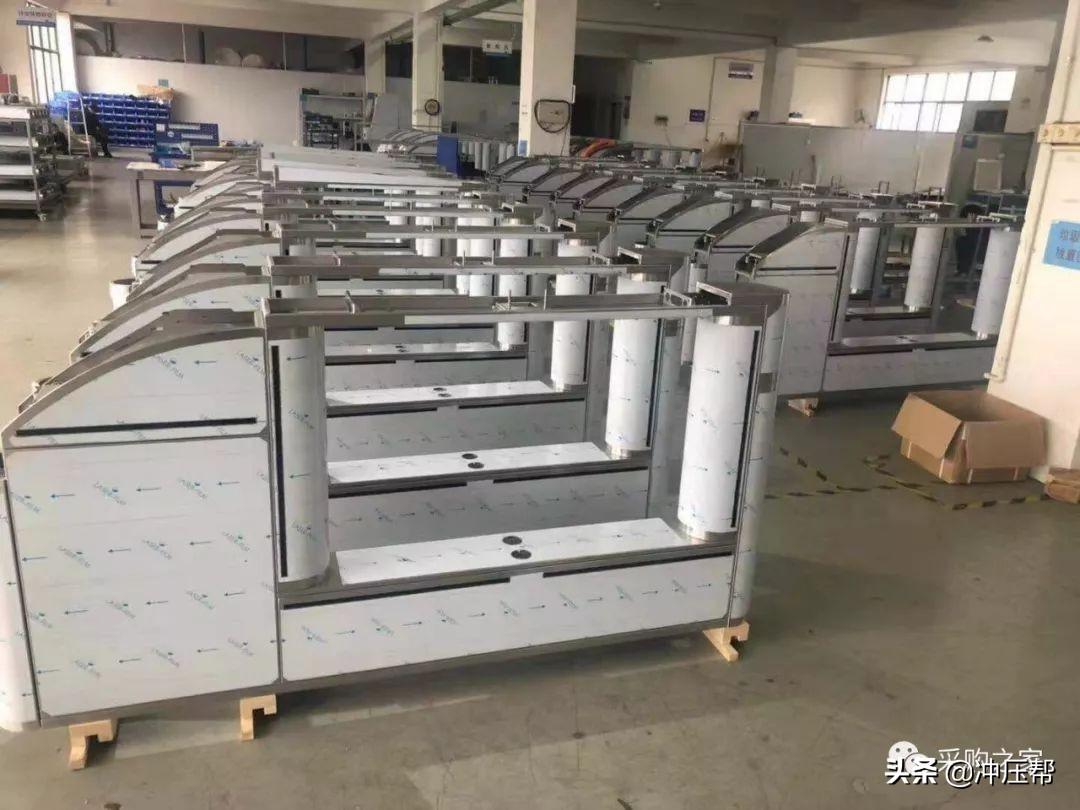
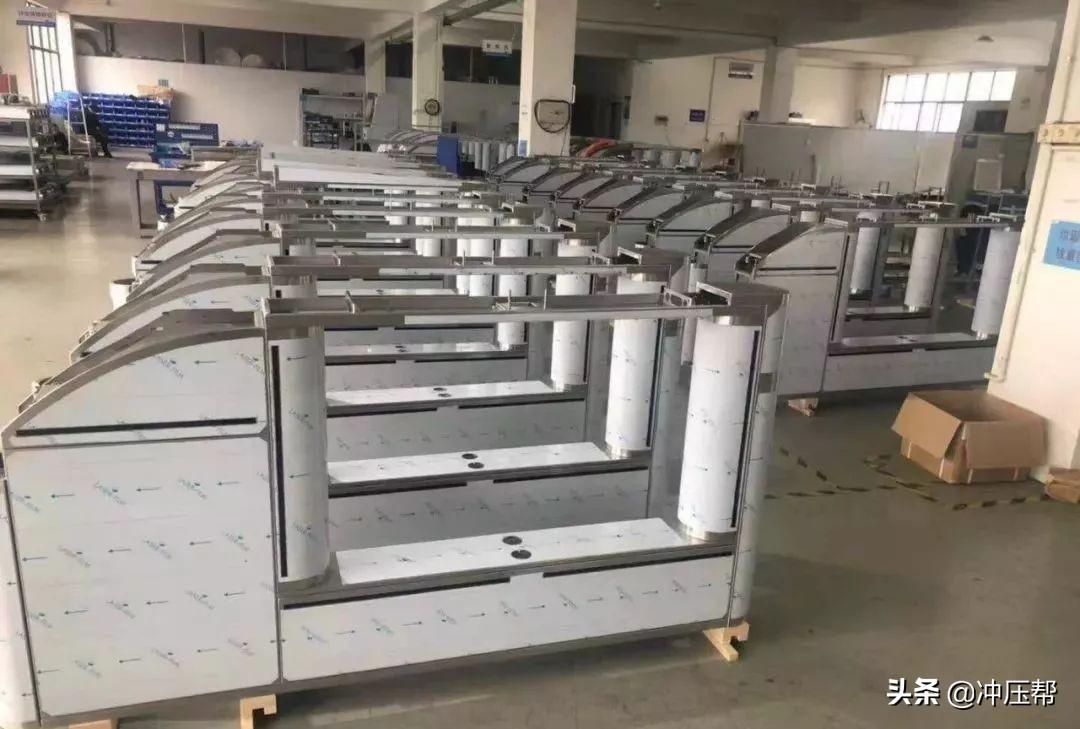
2. Bending
Its cost composition=equipment depreciation and amortization+labor cost+auxiliary materials
Equipment depreciation and amortization:
Equipment depreciation is calculated on a 5-year basis, with 12 months per year, 22 days per month, and 8 hours per day.
For example, for equipment worth 500000 yuan, the depreciation per minute is 50 * 10000/5/12/22/8/60=0.79 yuan/minute
It usually takes 10 to 100 seconds to make a bend, so the depreciation of each bending equipment is 0.13-1.3 yuan per bend.
Labor cost:
Each device requires one technician to operate, with an average monthly salary of 1800 yuan. Each technician works 22 days a month and 8 hours a day, which means the cost per minute is 1800/22/8/60=0.17 yuan/minute. On average, 1-2 bends can be made per minute. Therefore, the labor cost per bend is 0.08-0.17 yuan/track
Auxiliary material cost:
The cost of auxiliary materials used for each bending machine per month is 600 yuan. Based on 22 days per month and 8 hours per day, the hourly cost is 600/22/8/60=0.06 yuan/track
3. Surface treatment
Outsourced based on purchase price (such as electroplating, oxidation)
Composition of spraying costs:
Spray coating cost=powder material cost+labor cost+auxiliary material cost+equipment depreciation
Powder material cost: The calculation method is generally based on square meters, and the price per kilogram of powder ranges from 25 to 60 yuan (mainly related to customer requirements). Generally, 4-5 square meters can be sprayed per kilogram of powder.
Powder material cost=6-15 yuan/square meter
Labor cost: There are a total of 15 people on the spraying line, each person is charged 1200 yuan/month, with 22 days per month and 8 hours per day. Each hour can spray 30 square meters.
Labor cost=15 * 1200/22/8/30=3.4 yuan/square meter
Auxiliary material cost: mainly refers to the fuel cost used for pre-treatment liquid and curing furnace, which is 50000 yuan per month. It is 22 days per month, 8 hours per day, and 30 square meters per hour.
Auxiliary material cost=9.47 yuan/square meter
Equipment depreciation: The spraying line has an investment of 1 million yuan and is depreciated for 5 years. It operates in December each year, 22 days a month, 8 hours a day, and sprays 30 square meters per hour.
Equipment depreciation cost=100 * 10000/5/12/22/8/30=3.16 yuan/square meter
Total spraying cost=22-32 yuan/square meter
If partial protection spraying is required, the cost will be higher.
4、 Packaging fee
According to different products, packaging requirements and prices vary, usually ranging from 20 to 30 yuan/cubic meter.
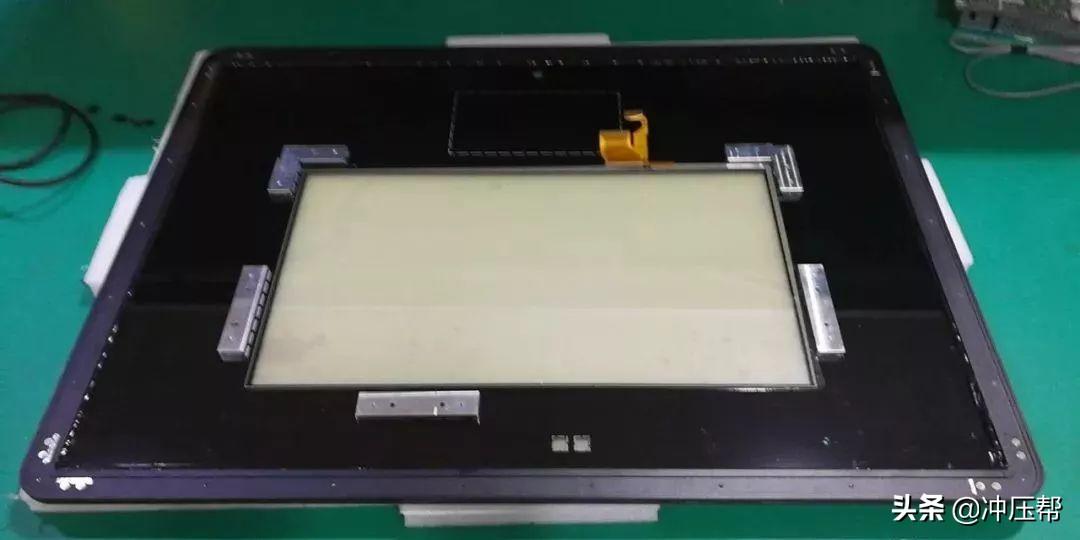
5、 Transportation management fee
The transportation cost is amortized into the product.
6、 Management expenses
There are two parts to management expenses: factory rent, water and electricity, and financial expenses
Factory rental water and electricity:
The monthly rental water and electricity cost is 150000 yuan, and the monthly output value is calculated at 4 million yuan. The proportion of rental water and electricity to the output value is 15/400=3.75%
Financial expenses:
Due to mismatched accounts receivable and payable cycles (we purchase materials in cash and customers settle 60 days per month), we need to hold down funds for at least 3 months at a bank interest rate of 1.25-1.5%.
Therefore, management expenses should account for about 5% of the total sales price.
7、 Profit
Considering the long-term development of the company and better customer service, set a reasonable profit point, such as 10% -15%.
The above 7 points are the main costs that constitute the product and are for reference only.
Calculation method for stamping quotation
The manufacturing price of sheet metal is calculated based on the operating time:
Laser cutting for 8RMB/Min, calculated at 1RMB per small hole
CNC pricing of 5RMB/Min
CNC bending pricing is 1 RMB per side, double for the larger side
Cold work welding calculation is 70RMB per day, with 50KG per working day as the benchmark
The above calculation methods require a high level of comprehensive quality and a strong understanding of industry trends, but they are difficult to operate.
The following sheet metal calculations are empirical formulas that do not consider manufacturing processes:
Material price=unfolded weight of material dropped x market material price
Processing fee calculation: without considering process, tax, management fees, and shipping costs
Benchmark calculation: 3200RMB/T cold-rolled steel plate t=2.0 1804-m Grade 7 IT7
Cold work processing cost: 8.0-8.4RMB/KG, with workers producing 50KG or more per work.
Cold work includes the following: grinding wheel machine cutting, old style shearing machines, old style bending machines, flame piercing, old welding, and outsourcing prices ranging from 7.2 to 7.5 RMB/KG.
The above processing coefficient base is set to 1.

The outsourcing costs for CNC cutting, CNC punching, CNC bending, and CO2 shielded welding are calculated with a coefficient of 2.5-3.5, and the coefficients are taken into account based on the number of processes and complexity.
Laser cutting is twice the impact:
When the board is not equal to 2, the processing cost is calculated as equal to 2
When the plate size is less than 1.2, the processing cost is multiplied by 2.5 to 3.5
When the market price of materials fluctuates, the processing cost base remains unchanged.
If the sheet metal production is fully assembled without welding, the counting coefficient is multiplied by 0.75 to 0.85, usually taking the larger value;
When the tolerance level is increased to 1804-f, the counting coefficient is multiplied by 1.5-2;
For batch deburring and blunting, multiply the counting coefficient by 1.1 to 1.5;
The surface spray price is 20-30 RMB/m2;
The price for surface three degree paint processing is 15-20RMB/m2;
For those with special requirements and difficulties in manufacturing and processing, it is necessary to consider the yield and multiply the yield coefficient;
The above pricing is the standard pricing, which means that if the scrap rate is within 3%, the profit is approximately 28% to 35%. After deducting taxes, the profit is around 18% to 23%. If there is a requirement for profit, the corresponding multiplication coefficient should not be less than 1.75 when pricing.