Understanding the quality of Metal Stamping parts is crucial for all industries. But how should we measure it? Please delve deeper and find a comprehensive answer.
The method of measuring the quality of metal stamping parts is to check the accuracy of the stamping parts, the consistency of each batch, and whether there are defects such as burrs or misalignment.
Although the above content provides a quick answer, there is still much to understand the complexity of the quality of metal stamping parts. Let's delve deeper into it.
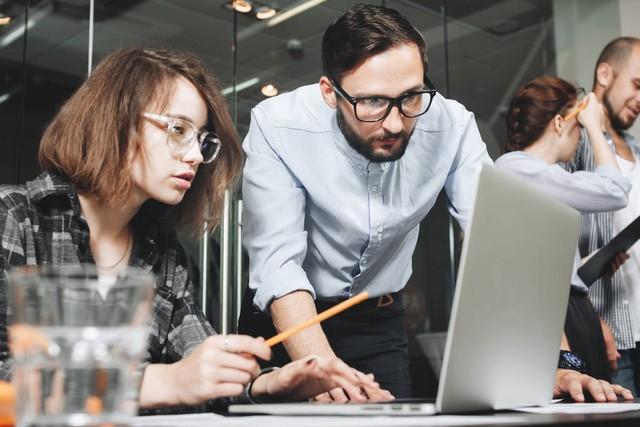
The core of understanding metal stamping is the manufacturing process of converting flat metal plates into specific shapes. This is achieved through the use of specialized tools and molds that apply high pressure to deform and cut the metal plate according to the desired design.
According to the operations involved, this process can be divided into various types, such as punching, cutting, extrusion, bending, tongue cutting, rib pressing, and material dropping. Each operation has its unique purpose, from punching holes in metal plates to raising them to create raised patterns (ribs).
Metal stamping is of great significance in various industries. It is the cornerstone of industries such as automotive, electronics, aerospace, and healthcare. The reason why metal stamping is widely used is that it can accurately, quickly, and economically produce a large number of complex parts. Whether it's car body panels, connectors in electronic devices, or components in household appliances, metal stamping plays a crucial role in turning design into reality.
Essentially, metal stamping is not only a process, but also an art that combines engineering precision with material science to produce parts that power our daily lives.
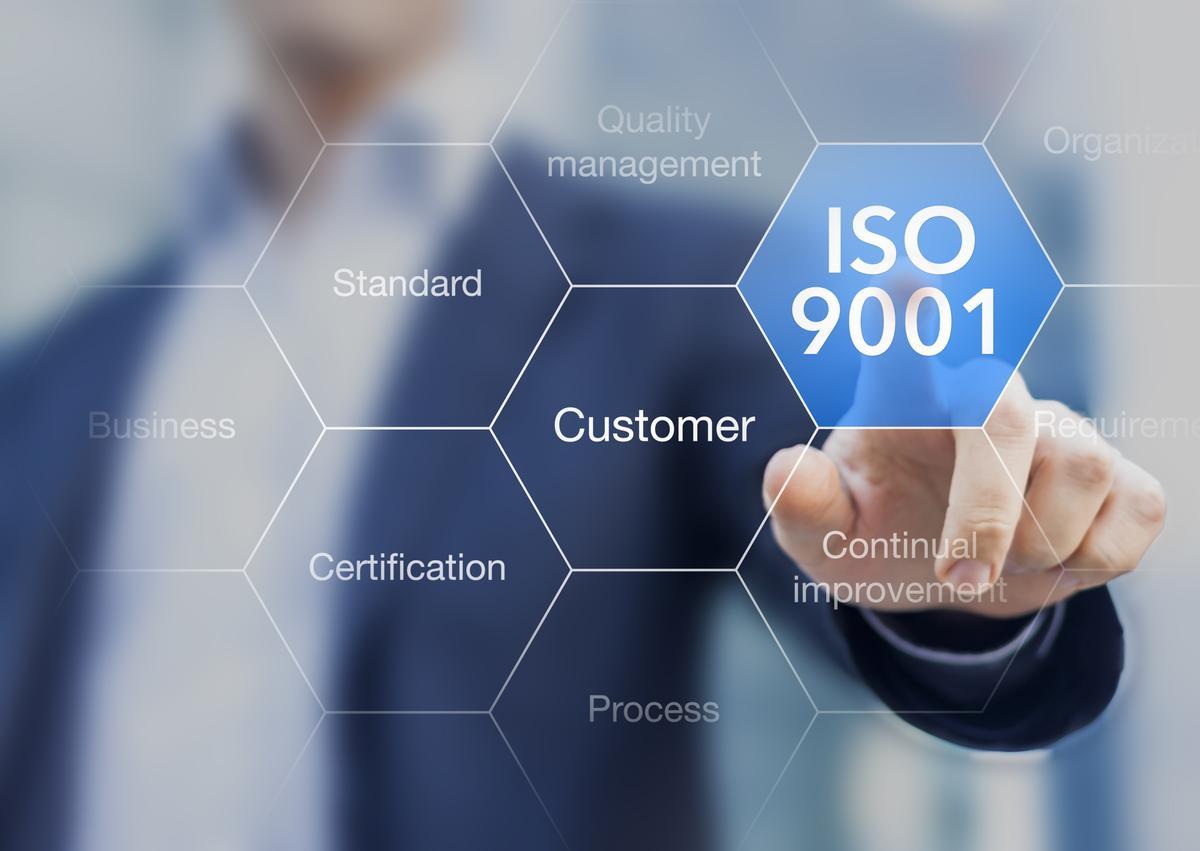
The key indicator of metal stamping quality is the quality assurance of metal stamping, which can ensure that the final product meets the expected specifications and performs the expected functions. The following are some of the main indicators that professionals are concerned about when evaluating the quality of metal stamping parts:
Accuracy of stamping parts
Accuracy is the cornerstone of the quality of metal stamping parts. Accurate and error free stamped parts mean that every part produced fully complies with design specifications. Whether it is a component in a machine or a part in a large assembly, this precision ensures that the part fits perfectly with the expected application. Any deviation, even a small one, can lead to malfunctions, reduced efficiency, and even safety hazards. Therefore, various industries invest heavily in advanced machines and skilled operators to achieve the highest level of accuracy.
Batch consistency
Although individual precision parts are commendable, achieving consistency in mass production is the true quality assurance. Consistency ensures that every part, from the first to the last in the production process, maintains the same high standards. This consistency is crucial, especially in industries such as automotive or electronics that require thousands of identical parts. Inconsistent batches can lead to increased losses, rising costs, and potential product recalls, therefore consistency is an important quality indicator.
No defects
Defects in metal stamping parts, such as burrs, misalignment, or uneven surfaces, are obvious signs of errors in the production process.
Burrs are unwanted rough edges or protrusions, usually caused by cutting operations. They can hinder the assembly process and even pose safety risks. Misalignment refers to the mismatch between parts and design intent, resulting in improper assembly. Surface unevenness may be caused by improper material handling or problems during the stamping process. The absence of these defects is a clear indicator of quality. It signifies a meticulous attention to detail, strict quality control measures, and the use of state-of-the-art machines.
In short, these key indicators are closely monitored to ensure that the parts produced by the metal stamping process are not only fully functional, but also reliable and safe, suitable for their expected applications.
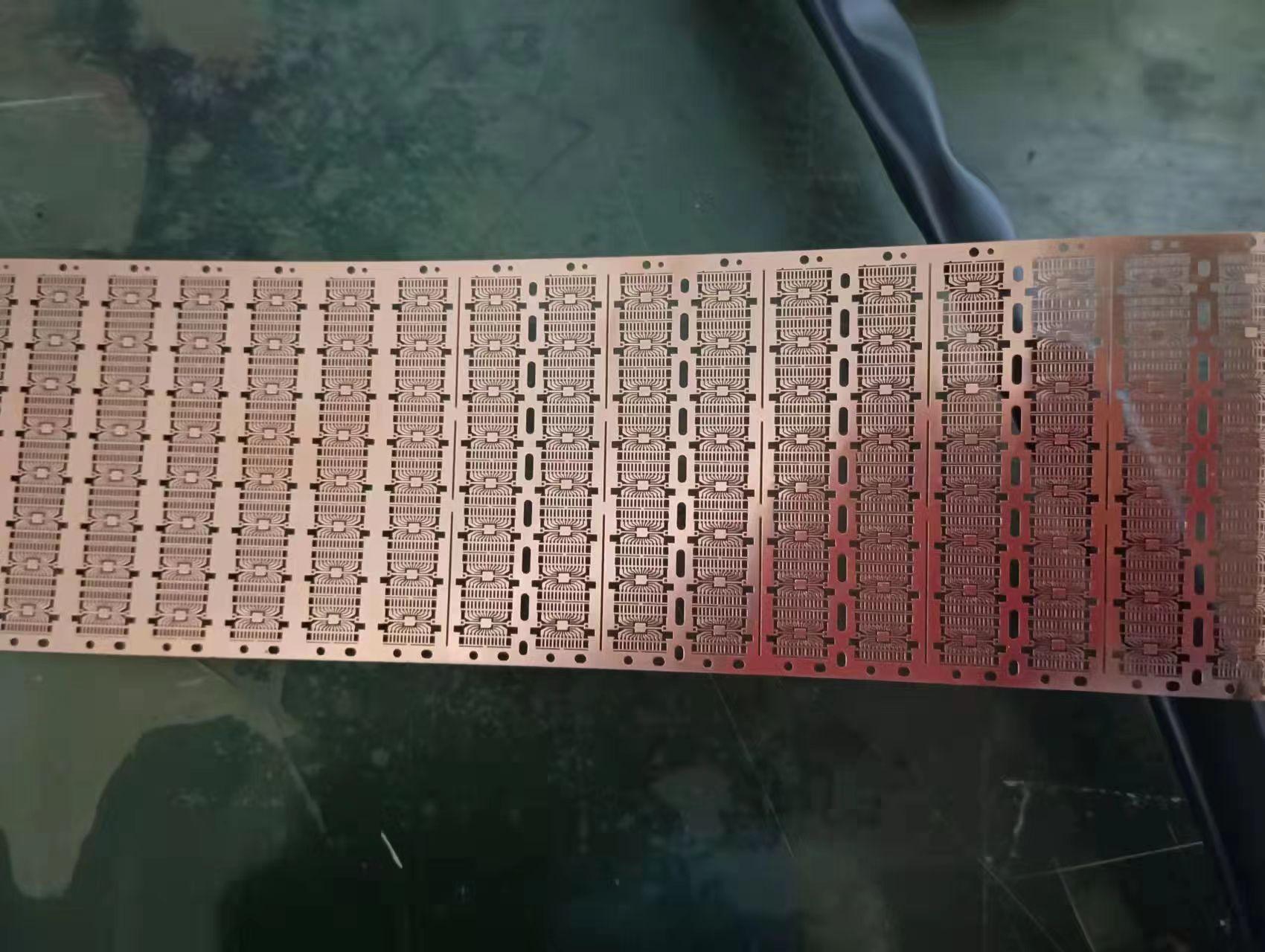
The tools and techniques for measuring quality ensure that the quality of metal stamping parts is not only related to the final product, but also to the processes and tools used to achieve the product. To maintain the highest standards of metal stamping, it is necessary to combine advanced tools with powerful quality control technology.
Testing tools
Calipers: Calipers are one of the most widely used tools for measuring the distance between two opposing surfaces of an object. There are various types of calipers, including vernier calipers, dial calipers, and digital calipers, each with a different level of accuracy. Micrometer: Compared to calipers, micrometers have higher accuracy and are used to measure small sizes. The micrometer uses a screw device to measure dimensions of one thousandth of an inch or even smaller. Gauge: These are specialized tools designed for specific measurement tasks. For example, "; Normal/Abnormal "; The gauge checks the workpiece according to the allowable tolerance to ensure that the workpiece is not too large or too small. Other types of measuring tools, such as depth gauges or ring gauges, are used for specific measurement purposes. Quality Control Technology
Statistical Process Control (SPC): This method uses statistical techniques to monitor the production process. By analyzing sample data, SPC can identify deviations from standard procedures for timely correction. This is an active method to ensure stable quality. Visual inspection: Sometimes, the human eye is the best tool. Trained inspectors will visually inspect parts for defects such as burrs, discoloration, or misalignment. Although this method may seem simple, it is often effective, especially when combined with other technologies. Automatic quality inspection: With the advancement of technology, automated systems equipped with cameras and sensors can now detect parts at high speeds. These systems can quickly identify defects, ensuring that only high-quality parts can enter the next stage of production. By using these tools and techniques in the metal stamping process, it can be ensured that each part meets the expected quality standards, thereby reducing losses, saving costs, and ensuring customer satisfaction.
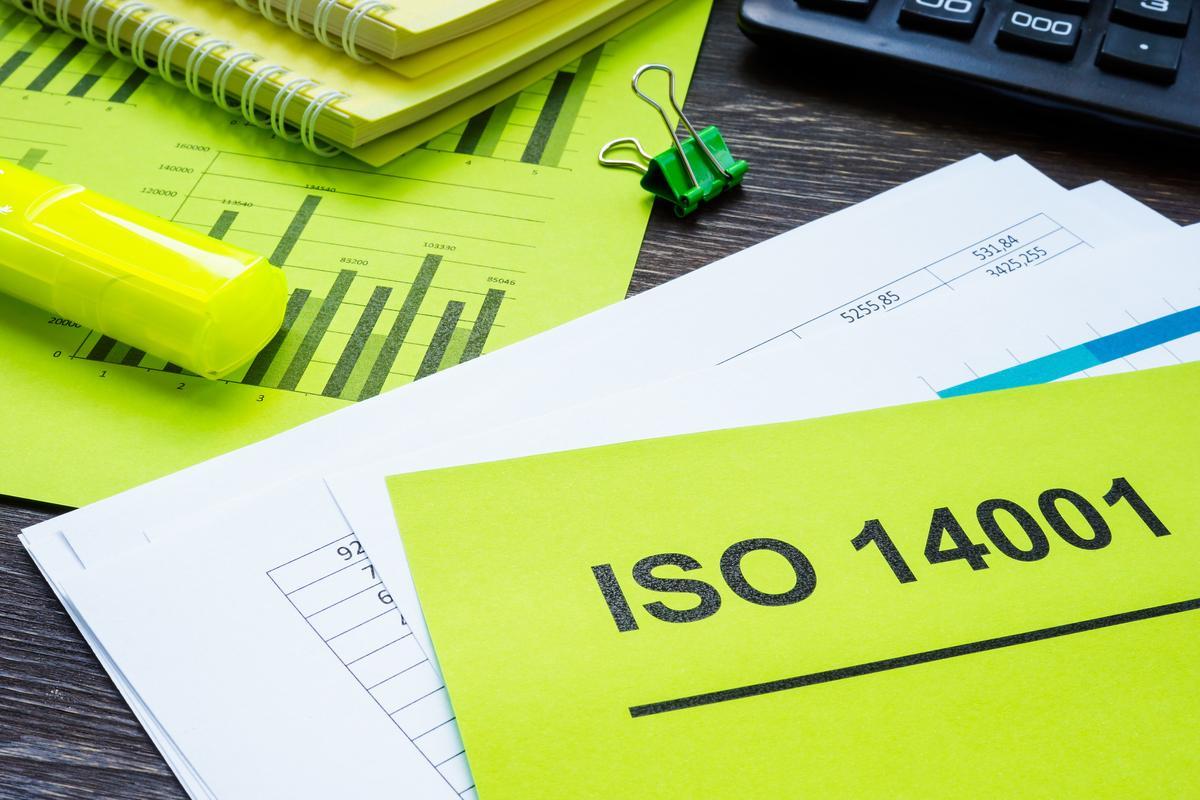
The impact of quality on the final product: The quality of metal stamping parts is not only an indicator, but also a commitment to reliability, functionality, and service life. When manufacturers prioritize quality, the final product benefits in multiple ways, directly affecting the user experience and the entire lifecycle of the product. The following is the impact of ensuring the quality of metal stamping on the final product:
Durability: High quality metal stamping ensures that each part is manufactured to the highest standards, using the correct materials and processes. The parts produced in this way can withstand wear, environmental factors, and mechanical stress. For example, precision stamped metal parts in the machine will fit perfectly, reducing undue stress on adjacent components and extending the product's lifespan.
Functionality: The main purpose of any product is to achieve the expected functionality. The quality assurance of metal stamping ensures that each component can accurately and precisely perform its designated function. For example, precisely stamped connectors in electronic devices can ensure optimal conductivity, allowing the device to operate perfectly.
Aesthetics: Although the main focus of hardware stamping may be functionality and durability, aesthetics also plays a crucial role, especially in consumer facing products. High quality stamping technology ensures that product lines are simple, perfectly fitted, and as smooth as new. For example, a well stamped metal casing for a smartphone not only protects the device but also enhances its visual appeal.
Cost effectiveness: Investing in quality may seem to increase expenses, but in the long run it saves costs. High quality stamped parts can reduce the need for replacement, repair, and recall. This not only saves direct costs, but also protects brand reputation, thereby maintaining customer trust and loyalty.
Safety: In industries such as automotive or aerospace, the quality of metal stamping parts is directly related to safety. A defect in a component can lead to catastrophic failure. Ensuring quality means ensuring the safety of end users.
Environmental impact: Quality is also related to the environment. High quality products have a longer lifespan and reduce the need for frequent replacement. This means less waste, less resource consumption, and a smaller carbon footprint.
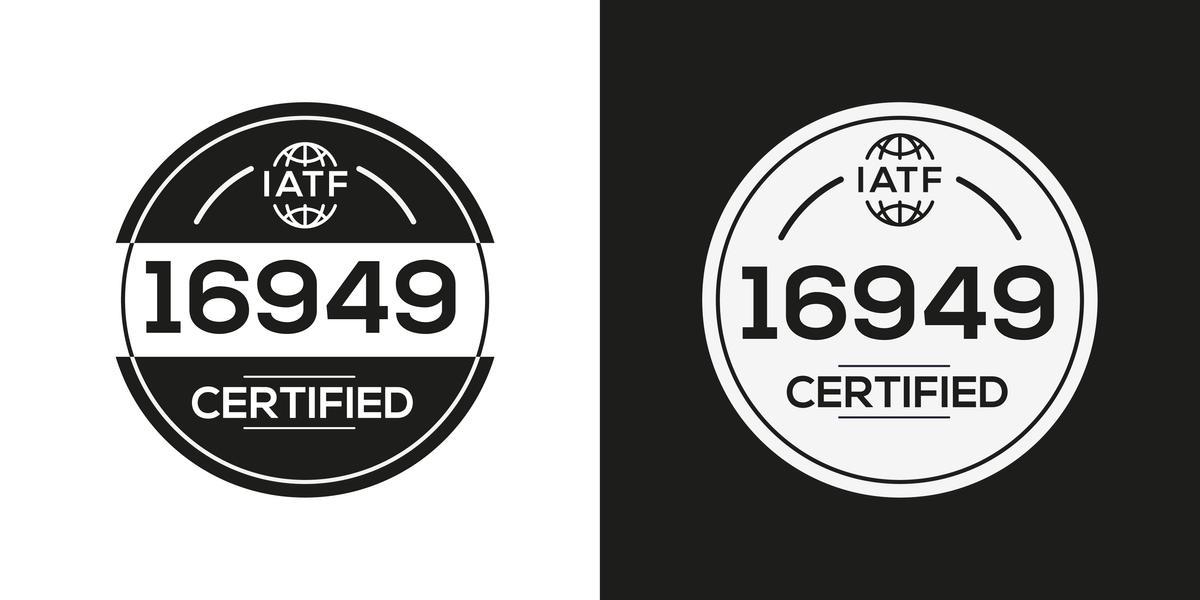
Conclusion: Metal stamping is the cornerstone of manufacturing and plays a crucial role in producing the components required for countless products we use in our daily lives. The accuracy, durability, and functionality of these components are directly affected by the quality of the stamping process. As we have discussed, measuring and ensuring quality is not just a compliance issue, but a commitment to excellence, safety, and sustainable development.
From the use of precision inspection tools such as calipers and micrometers to advanced quality control technologies such as statistical process control and automatic inspection, the industry has adopted numerous methods to adhere to the highest standards. These efforts not only ensure the optimal performance of the final product, but also improve its lifespan, aesthetics, and safety.
In addition, the chain reaction of the quality of metal stamping parts is not limited to direct products. It can save costs, reduce environmental impact, and earn the continued trust of consumers and stakeholders.
Essentially, the pursuit of quality in the metal stamping industry proves its commitment to providing the best products. This is a process of continuous improvement, innovation, and firm commitment to ensure that the products we rely on, from cars to small tools, can perform at their best.
Understanding the quality of metal stamping parts is crucial for all industries. But how should we measure it? Please delve deeper and find a comprehensive answer.
The method of measuring the quality of metal stamping parts is to check the accuracy of the stamping parts, the consistency of each batch, and whether there are defects such as burrs or misalignment.
Although the above content provides a quick answer, there is still much to understand the complexity of the quality of metal stamping parts. Let's delve deeper into it.
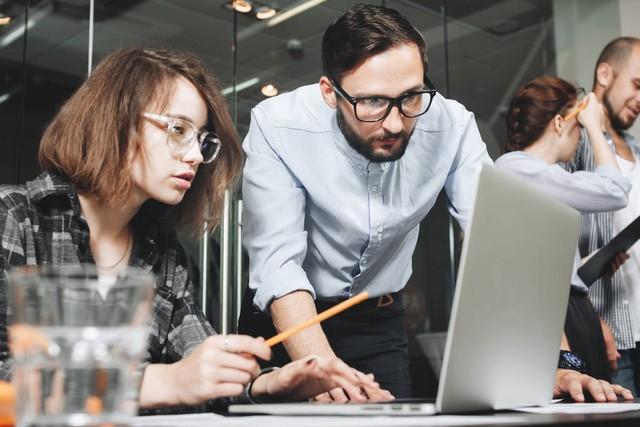
The core of understanding metal stamping is the manufacturing process of converting flat metal plates into specific shapes. This is achieved through the use of specialized tools and molds that apply high pressure to deform and cut the metal plate according to the desired design.
According to the operations involved, this process can be divided into various types, such as punching, cutting, extrusion, bending, tongue cutting, rib pressing, and material dropping. Each operation has its unique purpose, from punching holes in metal plates to raising them to create raised patterns (ribs).
Metal stamping is of great significance in various industries. It is the cornerstone of industries such as automotive, electronics, aerospace, and healthcare. The reason why metal stamping is widely used is that it can accurately, quickly, and economically produce a large number of complex parts. Whether it's car body panels, connectors in electronic devices, or components in household appliances, metal stamping plays a crucial role in turning design into reality.
Essentially, metal stamping is not only a process, but also an art that combines engineering precision with material science to produce parts that power our daily lives.
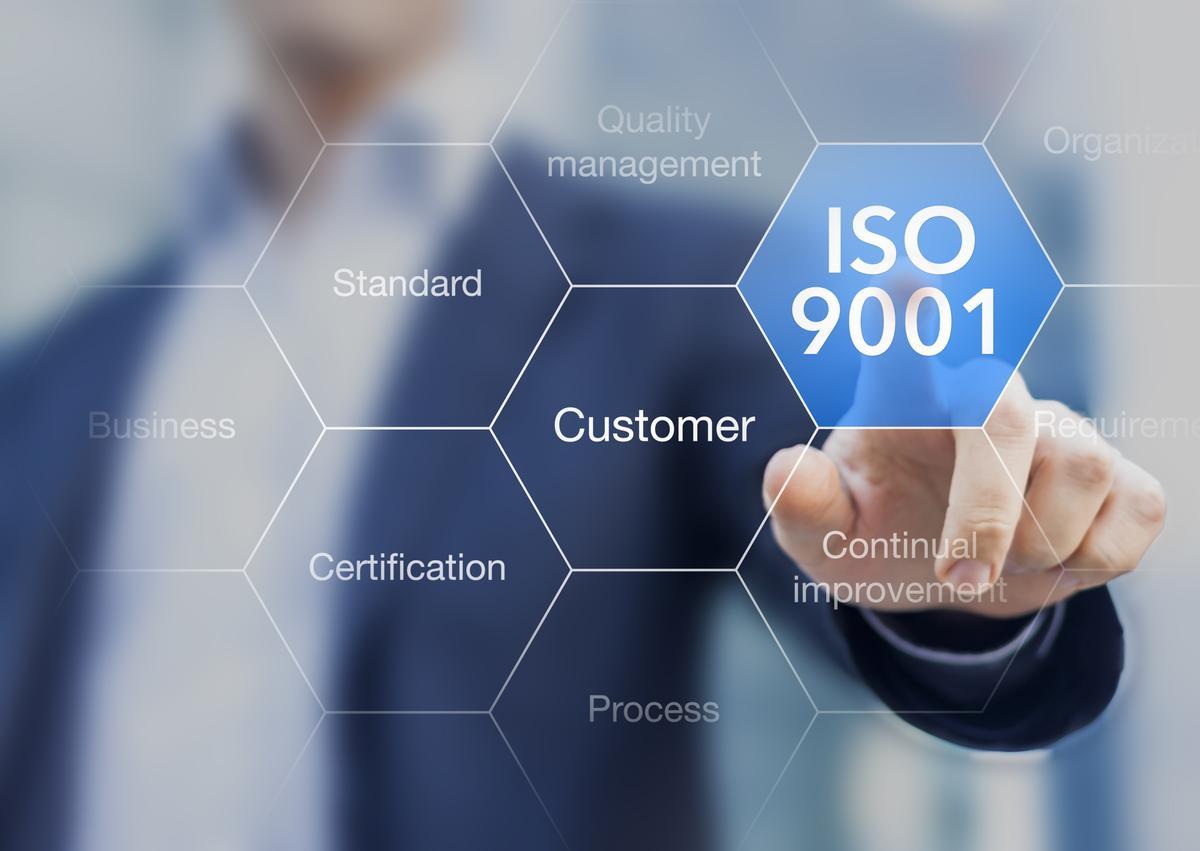
The key indicator of metal stamping quality is the quality assurance of metal stamping, which can ensure that the final product meets the expected specifications and performs the expected functions. The following are some of the main indicators that professionals are concerned about when evaluating the quality of metal stamping parts:
Accuracy of stamping parts
Accuracy is the cornerstone of the quality of metal stamping parts. Accurate and error free stamped parts mean that every part produced fully complies with design specifications. Whether it is a component in a machine or a part in a large assembly, this precision ensures that the part fits perfectly with the expected application. Any deviation, even a small one, can lead to malfunctions, reduced efficiency, and even safety hazards. Therefore, various industries invest heavily in advanced machines and skilled operators to achieve the highest level of accuracy.
Batch consistency
Although individual precision parts are commendable, achieving consistency in mass production is the true quality assurance. Consistency ensures that every part, from the first to the last in the production process, maintains the same high standards. This consistency is crucial, especially in industries such as automotive or electronics that require thousands of identical parts. Inconsistent batches can lead to increased losses, rising costs, and potential product recalls, therefore consistency is an important quality indicator.
No defects
Defects in metal stamping parts, such as burrs, misalignment, or uneven surfaces, are obvious signs of errors in the production process.
Burrs are unwanted rough edges or protrusions, usually caused by cutting operations. They can hinder the assembly process and even pose safety risks. Misalignment refers to the mismatch between parts and design intent, resulting in improper assembly. Surface unevenness may be caused by improper material handling or problems during the stamping process. The absence of these defects is a clear indicator of quality. It signifies a meticulous attention to detail, strict quality control measures, and the use of state-of-the-art machines.
In short, these key indicators are closely monitored to ensure that the parts produced by the metal stamping process are not only fully functional, but also reliable and safe, suitable for their expected applications.
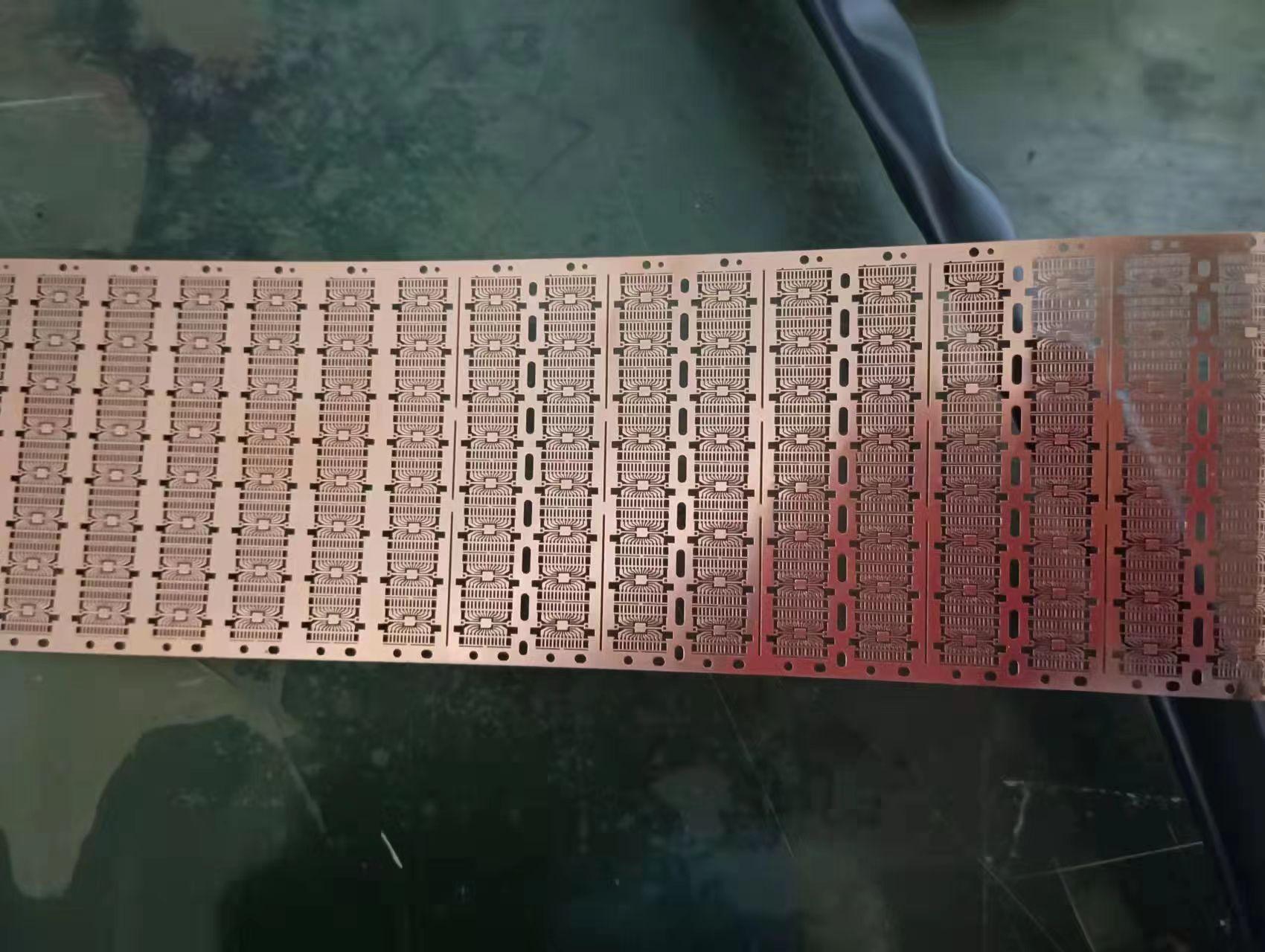
The tools and techniques for measuring quality ensure that the quality of metal stamping parts is not only related to the final product, but also to the processes and tools used to achieve the product. To maintain the highest standards of metal stamping, it is necessary to combine advanced tools with powerful quality control technology.
Testing tools
Calipers: Calipers are one of the most widely used tools for measuring the distance between two opposing surfaces of an object. There are various types of calipers, including vernier calipers, dial calipers, and digital calipers, each with a different level of accuracy. Micrometer: Compared to calipers, micrometers have higher accuracy and are used to measure small sizes. The micrometer uses a screw device to measure dimensions of one thousandth of an inch or even smaller. Gauge: These are specialized tools designed for specific measurement tasks. For example, "; Normal/Abnormal "; The gauge checks the workpiece according to the allowable tolerance to ensure that the workpiece is not too large or too small. Other types of measuring tools, such as depth gauges or ring gauges, are used for specific measurement purposes. Quality Control Technology
Statistical Process Control (SPC): This method uses statistical techniques to monitor the production process. By analyzing sample data, SPC can identify deviations from standard procedures for timely correction. This is an active method to ensure stable quality. Visual inspection: Sometimes, the human eye is the best tool. Trained inspectors will visually inspect parts for defects such as burrs, discoloration, or misalignment. Although this method may seem simple, it is often effective, especially when combined with other technologies. Automatic quality inspection: With the advancement of technology, automated systems equipped with cameras and sensors can now detect parts at high speeds. These systems can quickly identify defects, ensuring that only high-quality parts can enter the next stage of production. By using these tools and techniques in the metal stamping process, it can be ensured that each part meets the expected quality standards, thereby reducing losses, saving costs, and ensuring customer satisfaction.
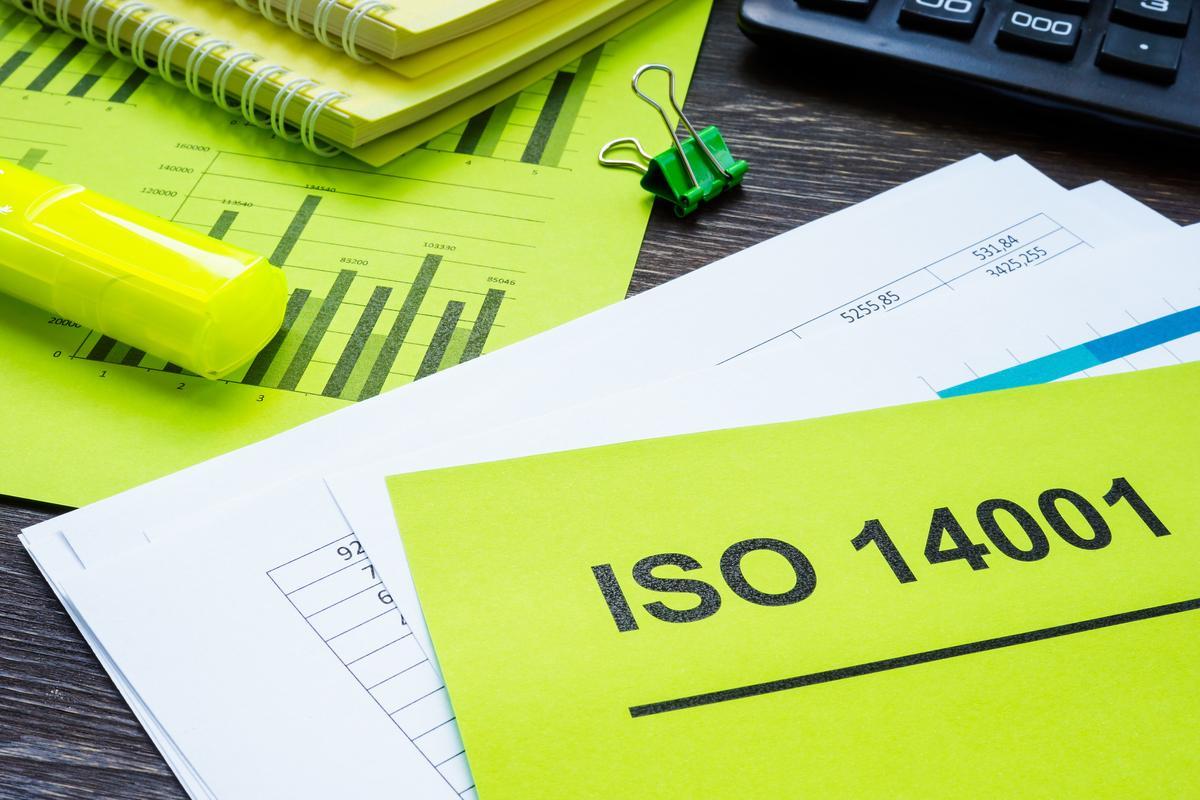
The impact of quality on the final product: The quality of metal stamping parts is not only an indicator, but also a commitment to reliability, functionality, and service life. When manufacturers prioritize quality, the final product benefits in multiple ways, directly affecting the user experience and the entire lifecycle of the product. The following is the impact of ensuring the quality of metal stamping on the final product:
Durability: High quality metal stamping ensures that each part is manufactured to the highest standards, using the correct materials and processes. The parts produced in this way can withstand wear, environmental factors, and mechanical stress. For example, precision stamped metal parts in the machine will fit perfectly, reducing undue stress on adjacent components and extending the product's lifespan.
Functionality: The main purpose of any product is to achieve the expected functionality. The quality assurance of metal stamping ensures that each component can accurately and precisely perform its designated function. For example, precisely stamped connectors in electronic devices can ensure optimal conductivity, allowing the device to operate perfectly.
Aesthetics: Although the main focus of hardware stamping may be functionality and durability, aesthetics also plays a crucial role, especially in consumer facing products. High quality stamping technology ensures that product lines are simple, perfectly fitted, and as smooth as new. For example, a well stamped metal casing for a smartphone not only protects the device but also enhances its visual appeal.
Cost effectiveness: Investing in quality may seem to increase expenses, but in the long run it saves costs. High quality stamped parts can reduce the need for replacement, repair, and recall. This not only saves direct costs, but also protects brand reputation, thereby maintaining customer trust and loyalty.
Safety: In industries such as automotive or aerospace, the quality of metal stamping parts is directly related to safety. A defect in a component can lead to catastrophic failure. Ensuring quality means ensuring the safety of end users.
Environmental impact: Quality is also related to the environment. High quality products have a longer lifespan and reduce the need for frequent replacement. This means less waste, less resource consumption, and a smaller carbon footprint.
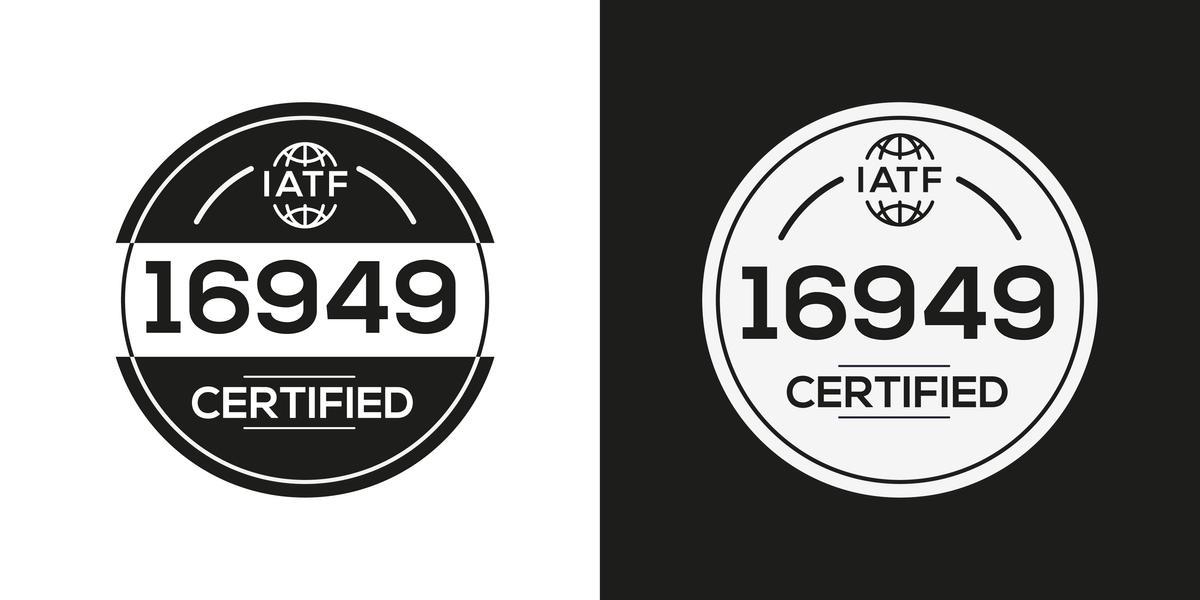
Conclusion: Metal stamping is the cornerstone of manufacturing and plays a crucial role in producing the components required for countless products we use in our daily lives. The accuracy, durability, and functionality of these components are directly affected by the quality of the stamping process. As we have discussed, measuring and ensuring quality is not just a compliance issue, but a commitment to excellence, safety, and sustainable development.
From the use of precision inspection tools such as calipers and micrometers to advanced quality control technologies such as statistical process control and automatic inspection, the industry has adopted numerous methods to adhere to the highest standards. These efforts not only ensure the optimal performance of the final product, but also improve its lifespan, aesthetics, and safety.
In addition, the chain reaction of the quality of metal stamping parts is not limited to direct products. It can save costs, reduce environmental impact, and earn the continued trust of consumers and stakeholders.
Essentially, the pursuit of quality in the metal stamping industry proves its commitment to providing the best products. This is a process of continuous improvement, innovation, and firm commitment to ensure that the products we rely on, from cars to small tools, can perform at their best.