Sheet Metal Processing factories mainly design and process according to design drawings, and the processing technology will also vary depending on the design drawings. Each link of the technology can be used as a part processing process, and now the most commonly used is sheet metal processing for industrial machinery.
1、 The main purpose of carrying out step-by-step process operations based on drawings, or drawing part drawings of sheet metal parts based on the physical appearance provided by customers, is to present the parts to be processed according to the drawings.
2、 According to the requirements and materials of sheet metal parts, different cutting methods can be selected, usually including cutting machine cutting, punching machine cutting, CNC cutting, and laser cutting machine cutting. Because many sheet metal parts require high precision and quality for laser cutting, the method used is to use a laser cutting machine for cutting, in order to ensure quality and improve work efficiency.

3、 Bending is the process of processing flat parts into three-dimensional parts, which requires a folding machine and corresponding bending molds to complete the operation. It also has a certain bending sequence, and the principle is to fold the next one that does not interfere first, and fold the one that will interfere later. Currently, the main method used is CNC bending processing, which not only improves efficiency but also reduces labor commission, ensuring quality improvement.
4、 Welding is the process of assembling multiple parts together to achieve the purpose of machining or welding the edges of individual parts to increase their strength. One of the crucial steps in welding is that good welding points will not produce welding slag or leave marks on the surface of sheet metal objects, and can be tested for water leakage. Nowadays, gas shielded welding, argon arc welding, spot welding, robot welding, etc. are widely used. 
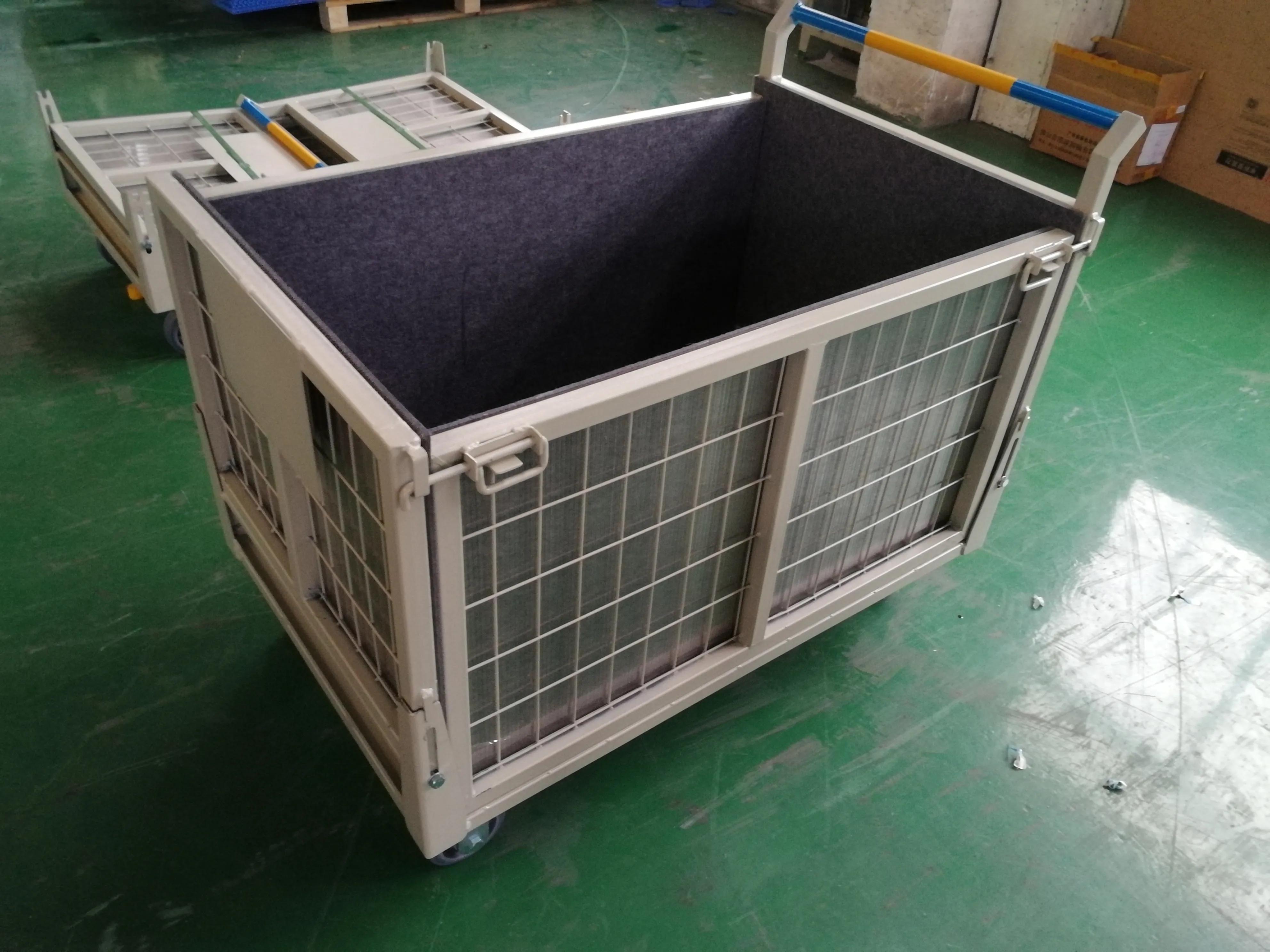
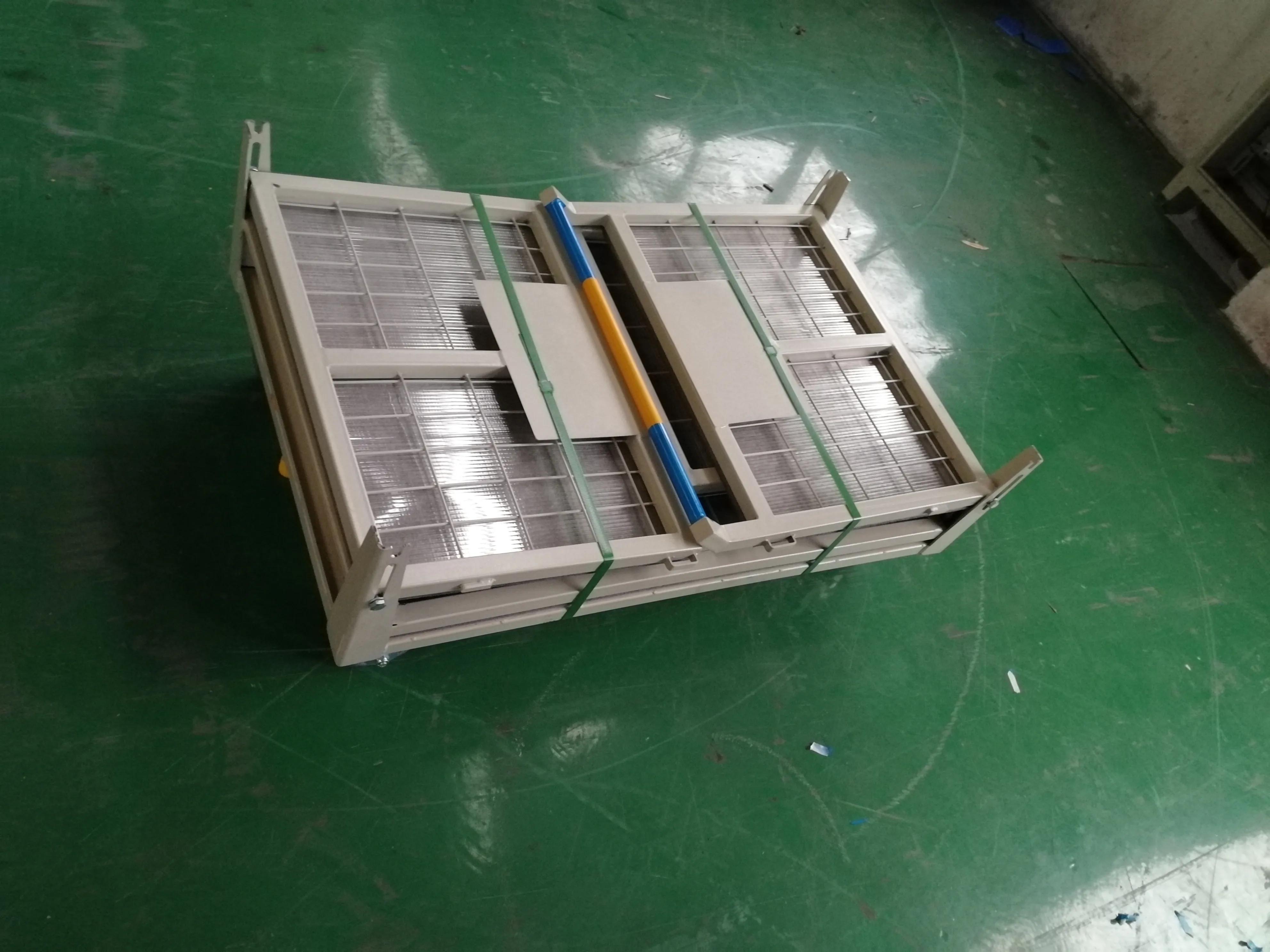
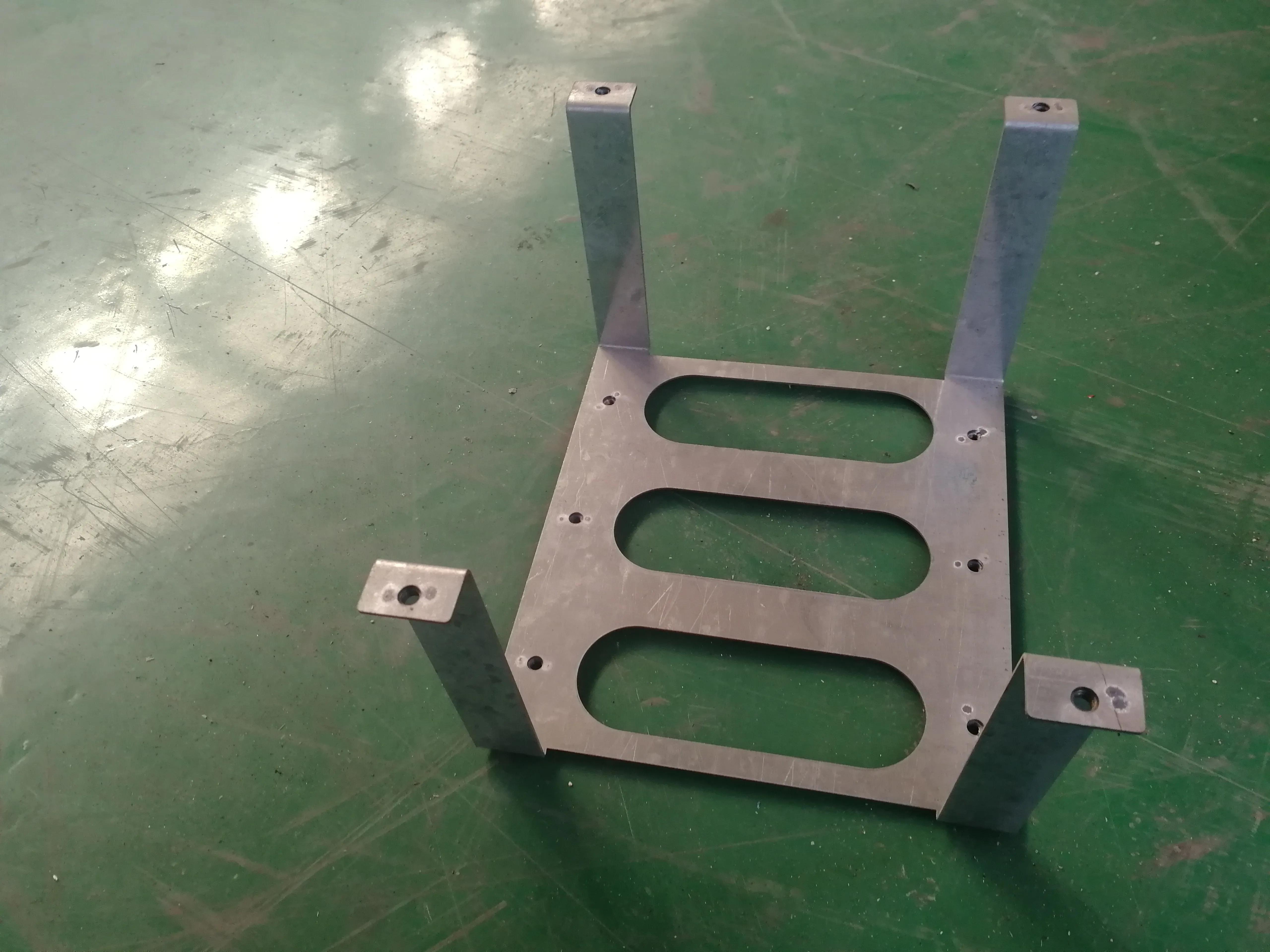
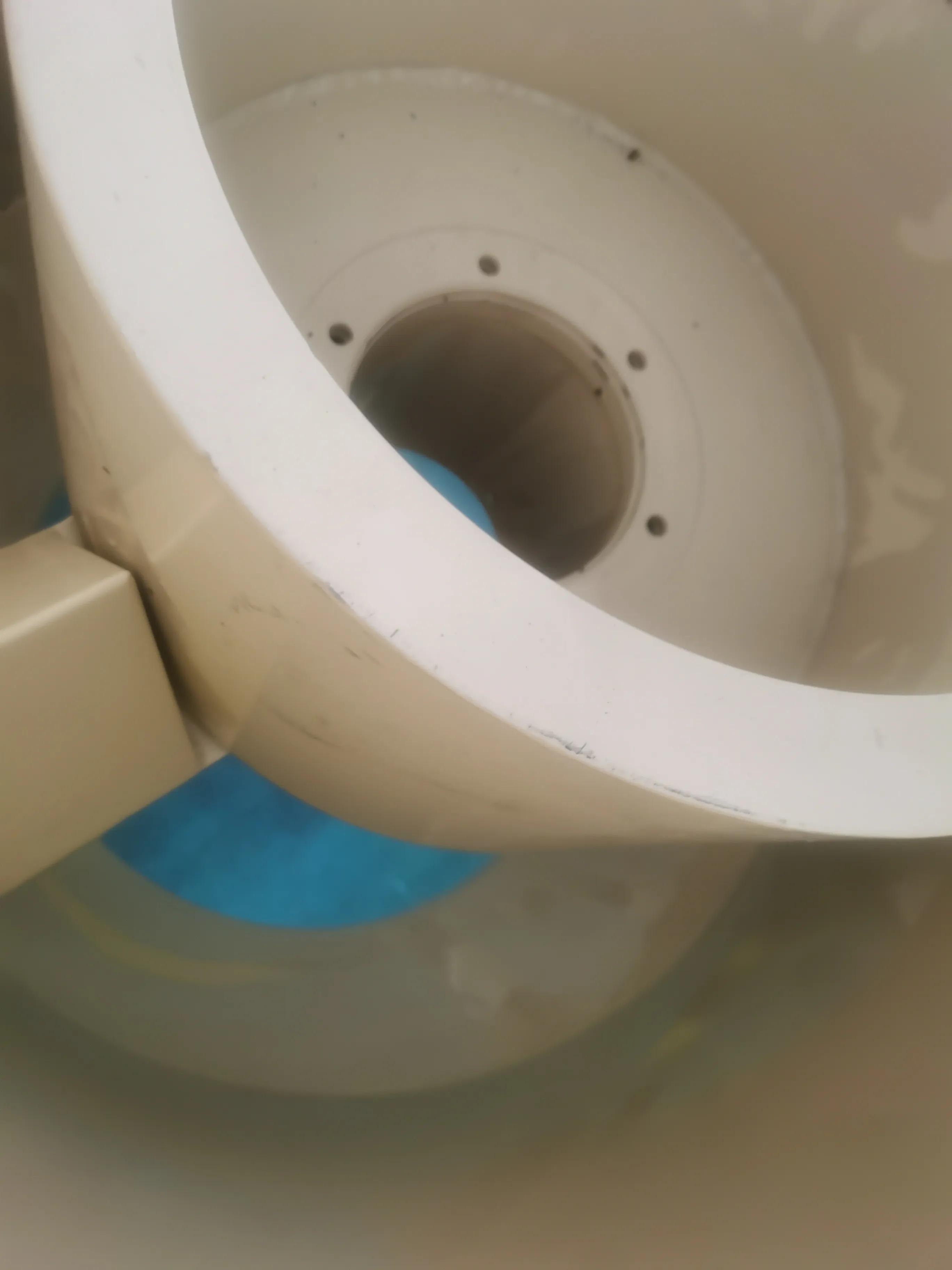
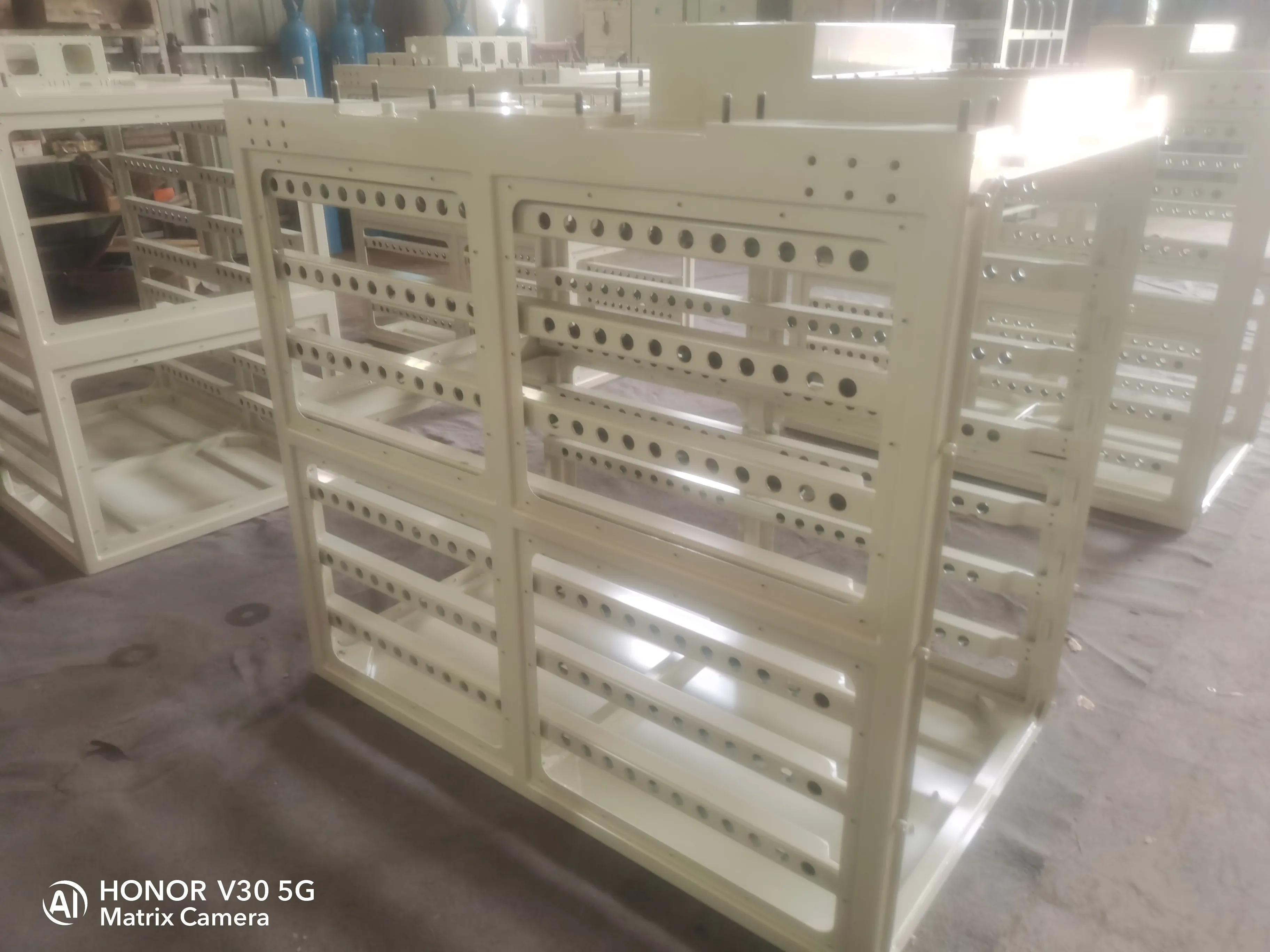
1. Laser cutting series: Processing according to customer's drawings. 2. Mechanical shell series: large mechanical sheet metal structural components such as injection molding machines, automation, packaging, printing, ceramics, elevators, etc. 3. Box series: indoor and outdoor floor standing chassis, automatic ticket vending machine chassis, LED electronic display screen shell, etc. 4. Electrical cabinet chassis series: network communication cabinet, distribution cabinet, switch cabinet, junction box, control box, etc. 5. Medical equipment series: equipment cabinets, operating tables, medical beds, medical purification equipment, etc. 6. Decoration Engineering Series: Aluminum Ceiling, Aluminum Curtain Wall, Aluminum Profile, Stainless Steel Decoration Engineering, etc. 7. Office supplies series: filing cabinets. 8. Public utility series: automatic water vending machine casing, ATM teller casing, bus waiting hall, intelligent garbage sorting and recycling bin. 9. Manufacturing of power electronic components; Manufacturing of industrial automatic control system devices; Manufacturing of hardware products; Manufacturing of communication equipment; Sales of metal products