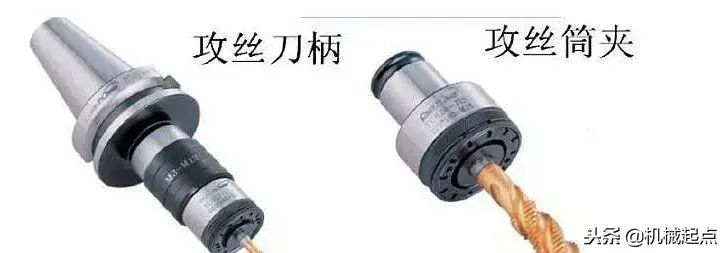
main points
1) The hole opening of the threaded bottom hole on the workpiece should be chamfered, and both ends of the through-hole thread should be chamfered.
2) The position of the workpiece clamp should be correct, and the centerline of the threaded hole should be placed in a horizontal or vertical position as much as possible, making it easy to determine whether the tap axis is perpendicular to the plane of the workpiece during tapping.
3) At the beginning of tapping, try to align the tap as much as possible, then apply pressure to the tap and rotate the wrench. When cutting 1-2 turns, carefully check and calibrate the position of the tap. When cutting into 3-4 threads, the position of the tap should be correct and error free. In the future, only the twisting hand needs to be turned, and no more pressure should be applied to the tap, otherwise the thread shape will be damaged.
4) When tapping, for every 1/2-1 turn of the wrench, it should be reversed about 1/2 turn to make it easier to discharge the broken chips and reduce the phenomenon of the cutting edge being stuck by the tap due to chip sticking.
5) When encountering a screw hole that cannot be penetrated, the tap should be frequently withdrawn to remove chips from the hole.
6) When attacking the screw holes of plastic materials, lubricating coolant should be added. For steel materials, engine oil or high concentration emulsions are generally used, and vegetable oil or molybdenum disulfide can be used for higher requirements. For stainless steel, 30 # engine oil or sulfurized oil can be used.
7) When replacing the last tap during the tapping process, it is necessary to manually screw it into the already tapped thread until it can no longer be screwed in, and then use a wrench to turn it. When exiting after the final cone attack, it is also necessary to avoid rapid rotation of the twisting hand, and it is best to manually rotate it out to ensure that the quality of the already drilled thread is not affected.
8) During machine tapping, the tap and screw hole should maintain coaxiality.
9) During machine tapping, the calibration part of the tap cannot be fully pointed out, otherwise it will produce messy teeth when reversing and exiting the tap.
10) The cutting speed during machine attack is generally 6-15 meters per minute for steel materials; Quenched and tempered steel or harder steel is 5-10 meters per minute; Stainless steel is 2-7 meters per minute; Cast iron is 8-10 meters per minute. When using the same material, a smaller tap diameter is taken as the higher value, and a larger tap diameter is taken as the lower value.
Rigid tapping
Also known as "synchronous feed tapping". The rigid tapping cycle synchronizes spindle rotation with feed to match specific thread pitch requirements. Due to the synchronous feed into the hole, theoretically, it is not possible to use an integral tap clamp with any tension compression.
However, the problem in actual production is that the machine tool cannot accurately match the specific pitch of the tap being used. There is always a slight difference between the threads processed by the machine tool and the actual pitch of the tap. If an integral tap clamp is used, this difference has a decisive impact on the lifespan of the tap and the quality of the thread, as additional axial forces are applied on the tap.
If a tension compression floating tap clamp is used, the tap life and thread quality will be greatly improved because these additional axial forces on the tap are eliminated. The problem with traditional tension compression tap clamps is that they can cause significant changes in tapping depth. As the tap becomes blunt, the pressure required to start the tap into the hole increases, and the compression stroke used in the tap driver is greater before the tap starts cutting. The result is a shallow tapping depth.
One of the main advantages of rigid tapping is that it allows for precise depth control in blind hole machining. In order to process workpieces accurately and consistently, it is necessary to use tap clamps with sufficient compensation to achieve a higher tap life without causing any changes in depth control.
Professional lubricants are also required in tapping processing, which can effectively reduce the friction between the workpiece and the wire tap, reduce wear, have a strong and tough oil film, prevent surface scratches and wrinkles of the workpiece, and effectively improve work quality and efficiency. Simultaneously suppressing temperature rise, reducing the occurrence of sintering and jamming, prolonging the service life of molds, protecting tools, suppressing the production of black sludge, and not corroding workpieces; The cooling effect is remarkable.
It is important to choose a suitable lubricant in tapping. In situations where cleaning is not required, self-cleaning tapping lubricants should be used. For difficult to machine workpieces, pure oil-based tapping oil should be used.